TimeMass filaments are 70% water.
Yes, really. Ask ChatGPT how’s that even possible.
We make our own polymerized alcohols in-house, our materials are unique, not your dishwasher’s PVA.
Still skeptical? Good.
Our 7 patents, our partnership with Nestle, or our crowdfunding campaign could light up our tech’s value, yet having our filaments in your hands is the ultimate skepticism’s antidote.
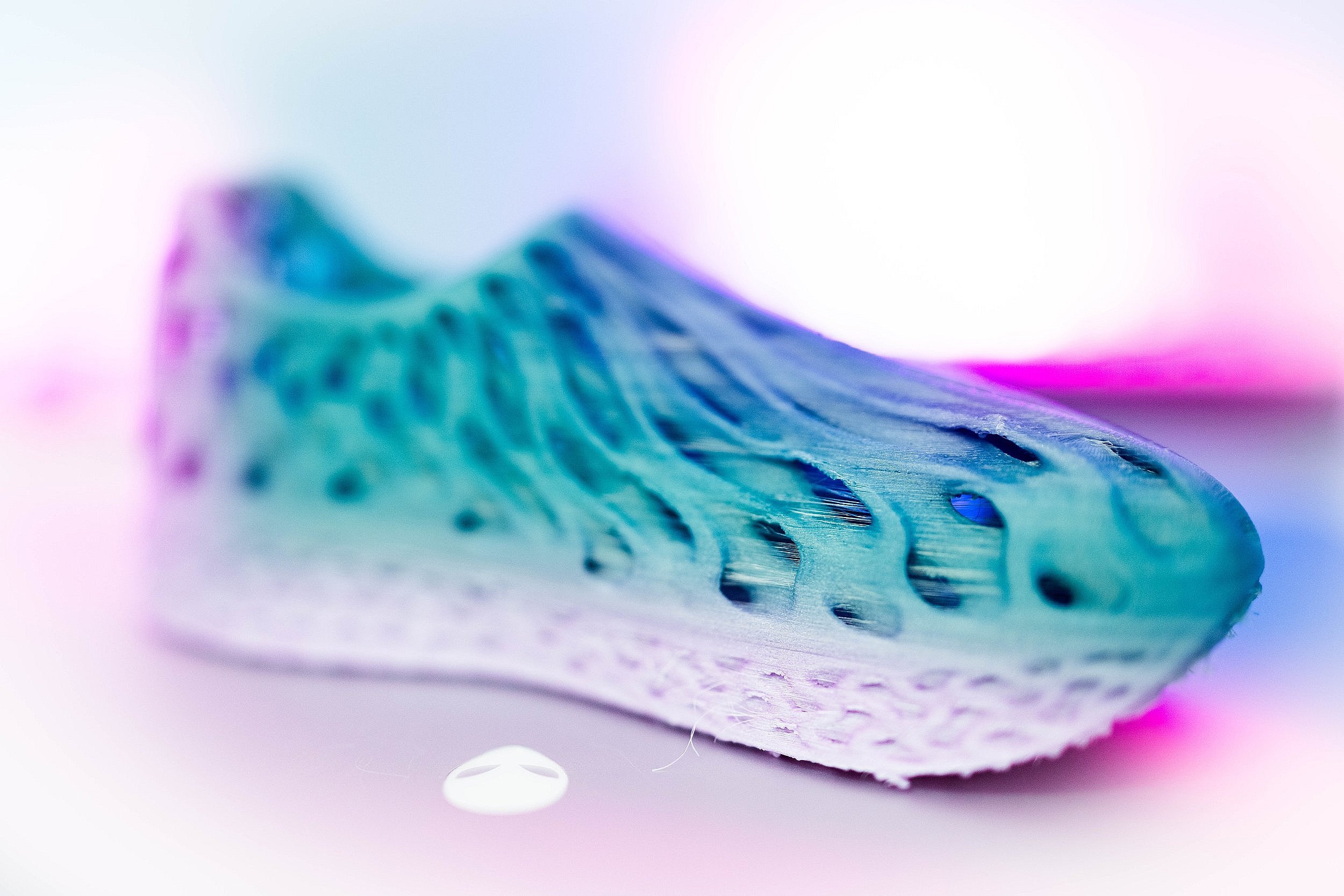
What is
TimeMass?
A must watch video made by our team.
Unlock the 4th dimension in your 3D printer.
3D Printing with Zero Toxic Fumes.
Print 4-Dimensional objects by integrating the dimension of Time, such as Bloominite.
All filaments are water-soluble.
Compatible with any filament-based 3D printer.
Packaged in plastic-free, 100% recycled cardboard.
Made in the USA.
3D printed ball before stone powder treatment
3D printed ball after stone powder treatment
100% Money-Back Guarantee: If you're not satisfied, we'll refund your purchase—no questions asked.
Free U.S. standard shipping on orders of 5+ spools!
Meet the Solution
-
Certified 100% Water Soluble
ASTM E 1148
-
Certified 100% PFAs-free
ASTM D7979-19
-
70% water, 30% sugar, vinegar, proprietary in-house Polyethenol and Calcium components
-
Patented Pabyss - The Plastic Abyss
A “Molecular Disintegrator” bottomless trashcan.
Metal Surface
The non-metal, metal filament
This demonstration proves that TimeMass Metal Surface isn’t just a filament—it’s an innovative functional material capable of creating lightweight, realistic metallic objects that can even attract magnets! By simply dipping and powder-coating with iron filings, you get a stunning, durable metal effect without complex post-processing.
Fire
A Burning 3D printing filament
Sound on! Listen to the built-in crackling noise
In the video: A TimeMass Fire Benchy boat burning at a slower, more controlled pace. Check the difference in the flame’s color.
Combustible Polymer Matrix: A water-soluble polymer that burns cleanly. This matrix forms the main body of the filament.
Water-Embedded Microstructure: Tiny microcapsules containing water distributed throughout the filament.
Fiber Reinforcement: Thin, slow-burning fibers running through the filament, mimicking the wick structure in traditional candles.
Water Vapor Release: As the filament burns, the embedded water slowly evaporates. This vapor acts as a heat sink, regulating the burn rate and temperature, much like how a candle wick regulates the flame.
Localized Cooling: The release of water vapor creates localized cooling zones, preventing rapid combustion and ensuring a steady, controlled flame height.
Fiber-Wick Effect: The embedded fibers function similarly to a candle wick, channeling the flame and maintaining a consistent burn path. This guides the flame through the filament, layer by layer, in a predictable manner.
We believe TimeMass Fire will burn significantly cleaner than conventional filaments due to its 70% water-based composition. However, we have not yet tested all potential combustion byproducts. For safety, please use this filament only in a well-ventilated area.
In the video a PLA benchy boat burning.
PLA (Polylactic Acid) is not designed for burning and presents several disadvantages compared to Time-Mass - Fire:
Uncontrolled Combustion: PLA burns unpredictably, often resulting in irregular flames, soot production, and unpleasant odors.
Toxic Fumes: Burning PLA can release potentially harmful chemicals, making it unsuitable for controlled applications like candles.
Rapid Burn Rate: PLA lacks any inherent mechanism to regulate the burn rate, leading to fast and uneven combustion.
Light
The illumination filament
Experience the future of light with TimeMass Light, our cutting-edge illumination filament. Designed to efficiently transport and diffuse light, this revolutionary material opens new possibilities for 3D-printed lighting solutions.
Watch our videos to see how TimeMass Light seamlessly channels and disperses light, bringing your creations to life with stunning visual effects.
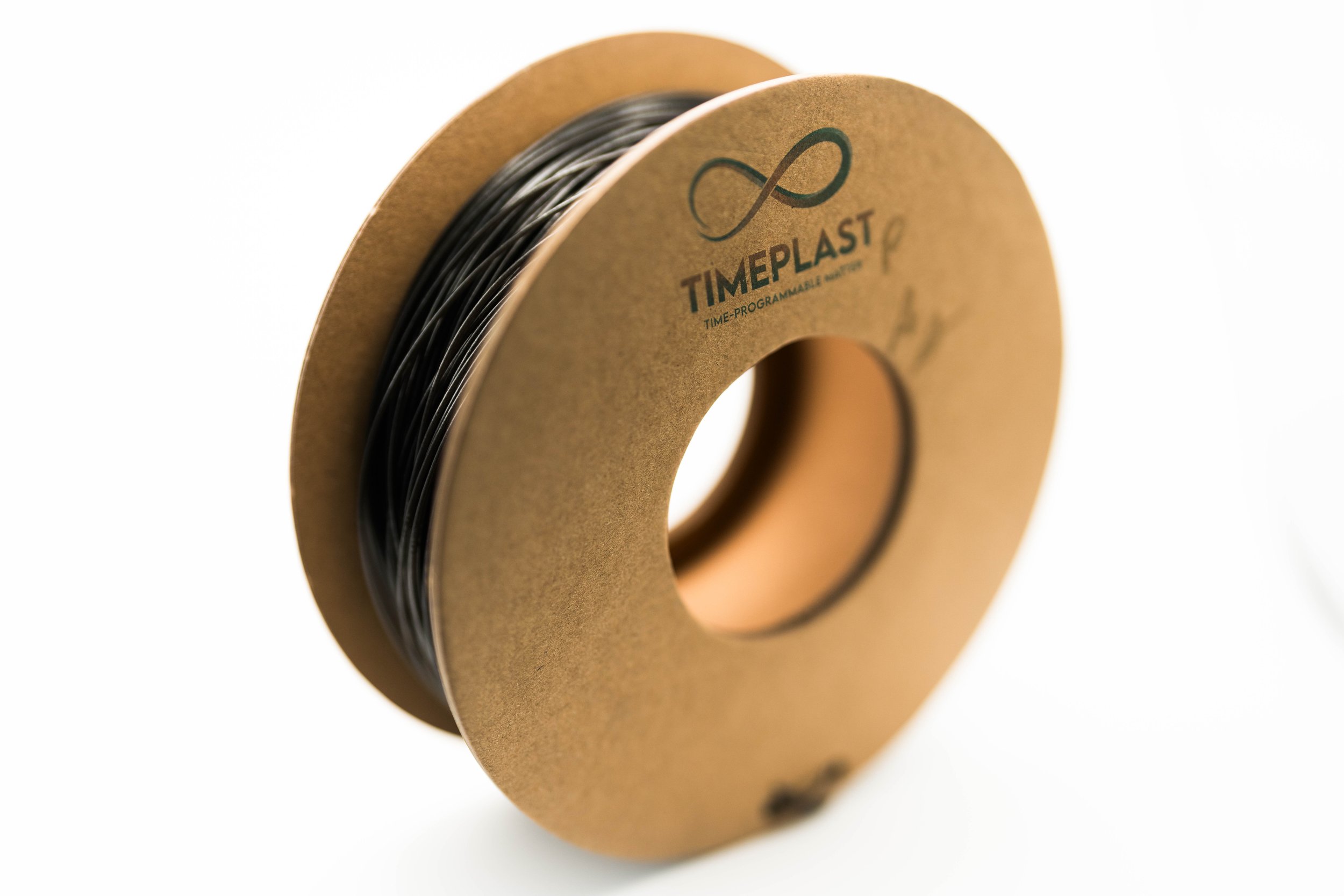
The possibilities are endless
Time-programmed wearables: Like artistic shoes, with incredible designs and at a very low cost of production.
Self-Eroding Marine Structures: Ocean-based supports that provide habitats for marine life and dissolve over time to release beneficial minerals, enriching marine ecosystems naturally.
Automated Farming Components: Timed-dissolving planters that release nutrients and water at key stages of plant growth, optimizing crop health and reducing artificial fertilizers.
Self-destructive Construction Scaffolding: Temporary, self-dissolving scaffolding for construction projects, removing the need for disassembly and minimizing post-construction waste.
Temporary Floating Platforms for Aquatic Events: Modular, dissolvable platforms for water-based events that disappear afterward, leaving the environment undisturbed.
Self-Deconstructing Medical Implants: Medical implants that dissolve once healing is complete, reducing the need for follow-up surgeries and minimizing infection risks.
Slow-Releasing Pesticide Capsules: Agricultural capsules that dissolve over time to release nutrients and pesticides sequentially, optimizing crop protection and reducing chemical waste.
Programmable Packaging Solutions: Water-soluble packaging for single-use items or perishables that disappears after disposal, reducing plastic waste effectively.
Zero-waste Temporary Art Installations: Timed art pieces designed to dissolve over time, creating ephemeral installations that leave no environmental impact, with increased art appreciation due to its ephemeral nature.
Ocean Buoys for Wildlife Monitoring: Timed-dissolving buoys that monitor marine life and disappear after their mission, preventing marine debris.
Personalized Fitness and Wellness Devices: Disposable fitness trackers that dissolve after use, releasing beneficial compounds, offering convenience with no waste.
Smart Infrastructure with Automated Deconstruction: Self-dissolving infrastructure for temporary construction needs, saving on cleanup costs and reducing waste when no longer needed.
Fiber
Sacrificial Polymer Technology for soft 3D printed fabrics
In the image: Our 1.75mm Fiber filament.
What is TimeMass Fiber?
It’s a version of our filaments which is made of a composite Timeplast material, consisting of:
Core or Microfibers as Structural Component: These are durable, flexible strands embedded within the filament. They act as the final "yarn" or fabric structure.
Matrix or Outer Material as the Sacrificial Polymer: Surrounding the structural fibers, the sacrificial polymer serves as a temporary binding material, holding the microfibers in a specific shape during the 3D printing process.
This dual-material design within a single filament eliminates the need for a separate support material, simplifying the printing process and making it possible to achieve very thin fibers
In the image: The same fiber filament shown previously, but after 24 hours of exposure to water, the fibers begin to emerge.
When you print with this filament:
Layer Formation: The filament is deposited in layers, with the sacrificial polymer temporarily binding the fibers to maintain the desired geometry and tension until post-processing.
During printing, the sacrificial polymer:
Supports intricate designs and fine fiber orientation, acting as scaffolding during the build process.
Provides enough structural integrity to enable overhangs or complex shapes without collapsing.
In the image: A close-up view of the fibers themselves.
After printing, the object undergoes a sacrificial polymer removal process:
The sacrificial polymer is engineered to dissolve or disintegrate when exposed to room-temperature water.
As the sacrificial polymer dissolves, it leaves behind only the structural fibers, which are now loosely interwoven or patterned to create a fabric-like material.
The final printed object has to be dried out (for example in a food dehydrator) up until it achieves the desired final texture.
The remaining structure:
Retains flexibility and softness because the fibers were embedded in a precise pattern, mimicking woven or knitted textiles.
Has microvoids and interconnected fiber networks where the sacrificial material was removed, enhancing breathability and softness.
In the image: The before-and-after.
The final product achieves fabric-like properties because:
Fiber Orientation: The structural fibers remain in a pattern that mimics traditional fabric weaving, providing flexibility and drapability.
Tunable Thickness and Texture: By adjusting the sacrificial polymer-to-design ratio and the printing pattern, the properties of the resulting fabric can be tailored for softness, elasticity, or even stretchability.
Porosity: The dissolution of the sacrificial polymer creates spaces between the fibers, allowing the fabric to feel light and breathable.
Applications:
Fashion: Soft, customizable 3D-printed fabrics for garments with intricate patterns and dynamic properties (e.g., shape memory or thermal adaptability).
Medical: Biocompatible fabrics for bandages, surgical meshes, or wearable sensors.
Soft Robotics: Lightweight, flexible materials for artificial skins or soft robotic components.
Eco-Friendly Textiles: Fully recyclable or biodegradable fabrics due to the innovative polymer chemistry of Timeplast.
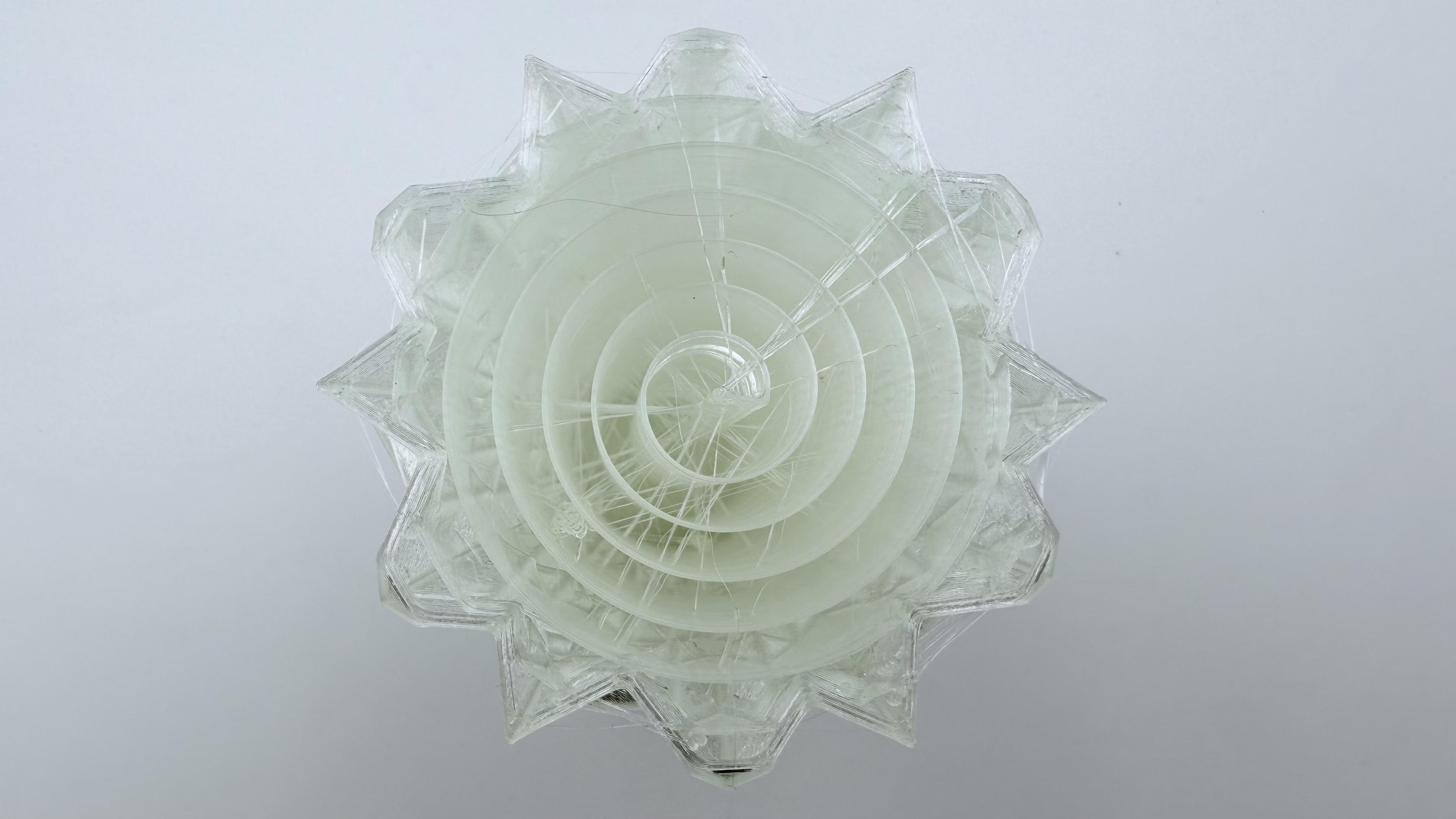
The best
Support filament in the 3D printing world period.
When we say TimeMass is the best support filament, it’s because we genuinely believe it to be true based on our testing and experience.
TimeMass stands out due to its exceptionally high molecular weight—the highest of any support filament we’ve tested at Timeplast. Combined with the non-toxic nature of our proprietary materials, you can print all day without worrying about releasing harmful chemicals into the air.
Additionally, TimeMass is an elastomer, which means it offers a unique combination of flexibility and water solubility. This allows supports to detach in a single stroke, making post-processing easier and cleaner. The high molecular weight also contributes to high-definition prints, setting a new standard for support filaments.
While materials like BVOH, PEG, and HIPS have been used for scientific purposes at much higher price points and are derived from conventional non-polar polymer chains, Time-Mass delivers a superior balance of affordability, safety, and functionality. We believe these factors make it an ideal choice for the average 3D printing enthusiast looking for a reliable and high-performing support filament.
Check the flexibility:
Active.
Delayed.
Passive.
Simulate 1000 years in one minute - Or Unleash your artistic side with organic deformations for your otherwise perfect prints with.
TimeMass Microwave
Printed figure before microwave treatment.
Printed figure after microwave treatment.
TPU on the left, TimeMass on the right.
Same flexibility, much higher potential.
Clean all strings with a quick dip in water instead of using toxic solvents.
Unlock the
4th dimension in
your 3D printer
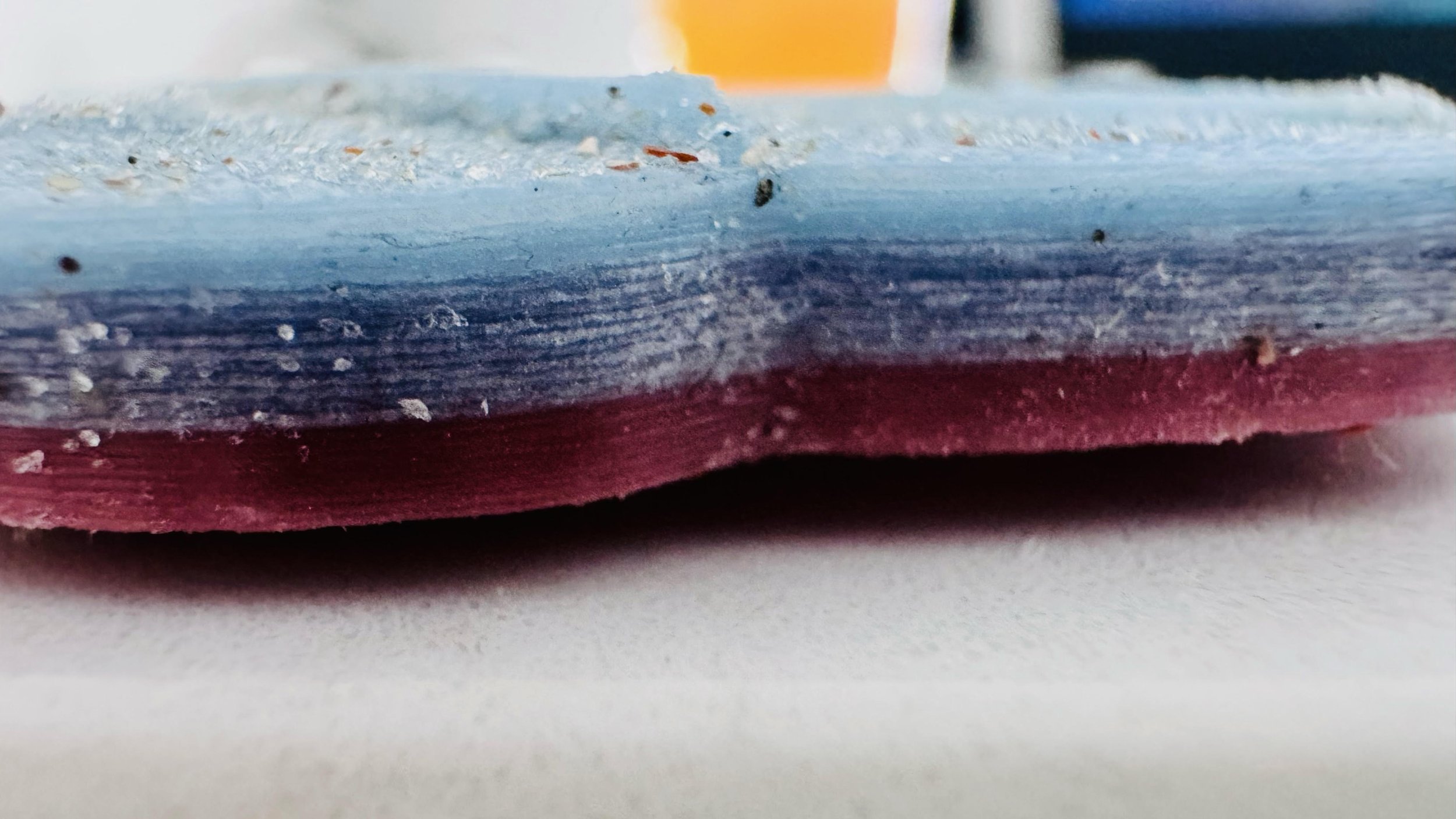
Timed
Dissolution Times
• ACTIVE: Dissolves quickly.
• EXTENDED/DELAYED: Dissolves slower than active.
• PASSIVE: Dissolves slowly
Watch 3 benchies with 3 different disolution times.
TimeMass Support:
Elevating 3D Printing Beyond PVA
Advantages Compared to Other Supports
Higher molecular weight, resulting in significantly better printing resolution and reliability.
Flexibility similar to TPU, making it much easier to remove support structures in complex prints.
More cost-effective than PEG, BVOH, and other premium water-soluble supports.
Works with multifilament systems that pull, but it doesn’t work in systems that push. Pausing and changing filaments is an easy fix.
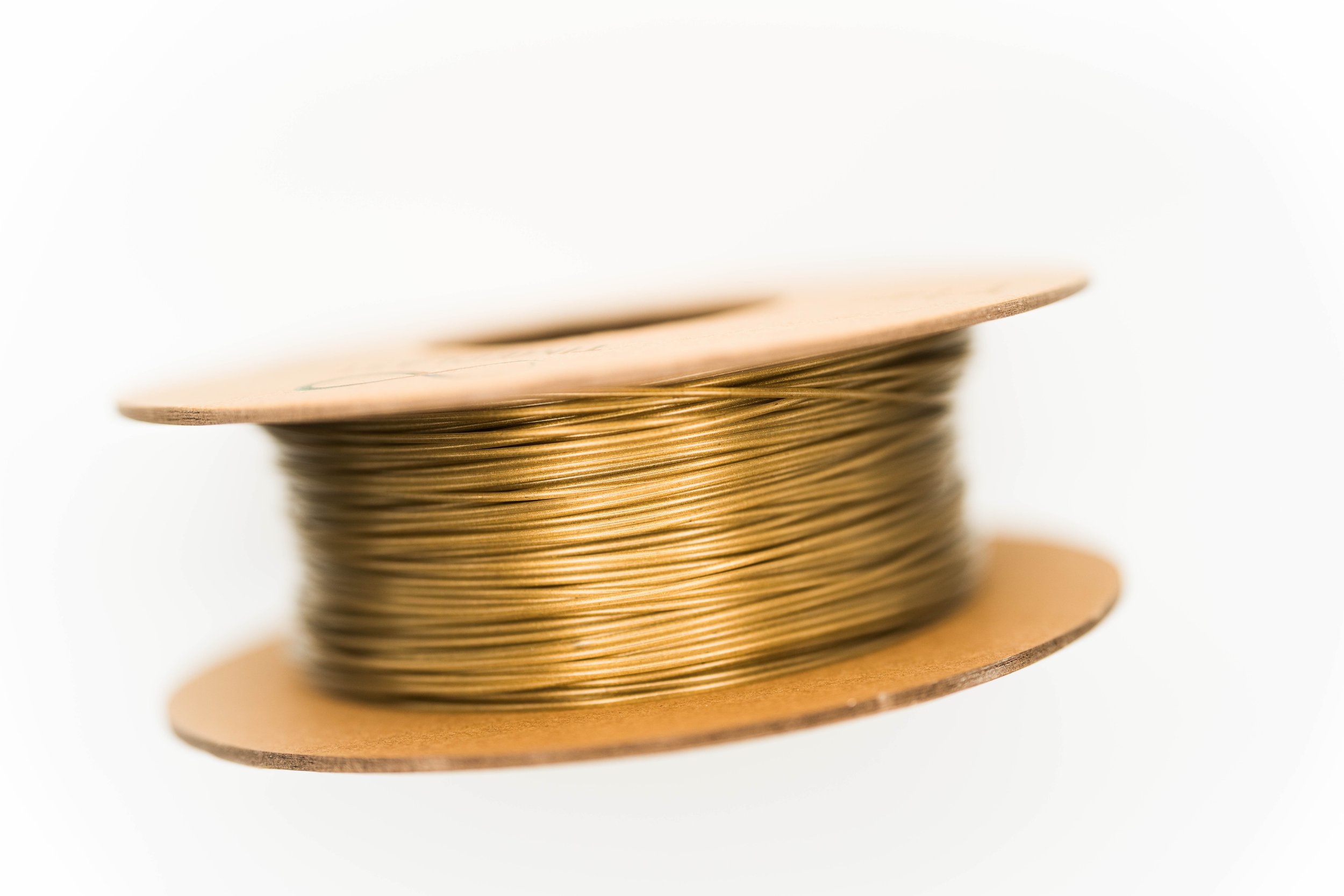