Experimental Use Disclaimer (Must Read)
TimeMass filaments are 70% water.
Yes, really. Ask ChatGPT how’s that even possible.
We make our own polymerized alcohols in-house, our materials are unique, not your dishwasher’s PVA.
Still skeptical? Good.
Our 7 patents, our partnership with Nestle, or our crowdfunding campaign could enlighten you, however nothing will replace having our filaments in your hands.
Best Selling Filaments
Soap - Gen 4
3D print usable soaps!
-
TimeMass Soap Gen 4 – Now With Bubbles. You're Welcome.
TimeMass Soap Gen 4 is the world’s first truly 3D-printable soap that not only cleans like a lab-engineered miracle—it actually foams. Yes. You read that right. We finally cracked the code.
Built from water, calcium carbonate, in-house polymerized alcohols, olive oil, essential oils, and a balanced mix of surfactants and emulsifiers (Coco-Glucoside and Glyceryl Stearate), this filament is part soap, part science experiment, part victory lap.
With Gen 4, we stabilized the chemistry to unleash full surfactant performance without compromising printability. The result: a bar of soap that prints like butter, foams like a show-off, and still lasts 10x longer than whatever you're buying in a box store.
What’s Inside:
Water + Alcohol – Gives it print flexibility, then hardens post-print like it means business.
Calcium Carbonate – For that gentle grit you didn’t know you loved (also in toothpaste).
Surfactants & Emulsifiers – Now optimized to actually lather, not just clean in silence.
Olive Oil – Moisturizing, luxurious, Mediterranean-approved.
Essential Oils – Fragrance, antimicrobial power, and optional spa vibes.
New in Gen 4: Bubbles. Real Ones.
After years of foam denial, we said, “Fine, let’s give the people what they want.”
And now? Lather. Suds. Foamy satisfaction.
It’s still smart. Still efficient. Still weird. Just now... it’s bubbly too.Use It Like a Mad Soap Alchemist:
Print your own soaps. Pause mid-print to inject oils, moisturizers, exfoliants—or secrets.
Embed capsules or time-release additives.
Sculpt messages into your soap. (Post-apocalyptic love notes, maybe?)
Why It Rules:
Cleans with actual foam (finally).
Printable on any basic 3D printer.
Reusable, regenerative, long-lasting.
Customizable with whatever wild scent profile you dream up.
Electrostatically attracts and removes dirt and grease like a polite molecular hitman.
TimeMass Soap Gen 4:
For people who love soap science, hate waste, and secretly always wanted a 3D printer that could make bath products. We did what the skeptics said was impossible.Now go print something that lathers.
Safety tip: Don’t go wild with undiluted essential oils. They’re called “concentrated” for a reason. Use responsibly.
-
Click here to access our specialized TimeMass GPT Assistant. Just tell it your printer model and the TimeMass filament you're using—it will instantly recommend the exact parameters you need to start printing successfully.
Using a Bambu Lab printer?
Click here to download our updated Bambu Lab profile. All printing parameters are fully optimized and tested—just load the file and start printing.1. Introduction
These parameters are designed to help avoid printing issues; however, temperatures and speed timings can be adjusted based on your specific goals. For example, if you prefer a less rigid result, we recommend using a lower temperature. This section outlines a complete slicing and printing profile for TimeMass Soap, tailored for printers with a 0.8 mm nozzle. If the print is not being successful, please lower the nozzle temperature by 10°C and start over until an optimal print is achieved. While these examples were printed with a 0.8 mm nozzle, TimeMass can be used with any nozzle size. Please check the manual for printing parameters with all the other nozzle sizes.2. Temperature Settings
2.aNozzle Temperature: 240°C — Optimal for flowability while avoiding decomposition (which begins around 250°C).
2.bBed Temperature: 95°C — Ensures strong first-layer adhesion and prevents moisture bubbling.
2.cNozzle Temperature Range: 230–245°C — Timeplast melts around 165°C but prints best at 240°C for precise viscosity control.3. Cooling Settings
3.aNo Cooling for First Layers: 3 layers — Prevents shrinkage due to rapid cooling of moisture-rich filament.
3.bFan Minimum Speed: 0% for the first 100 seconds — Allows heat retention during early layers.
3.cFan Maximum Speed: 15% starting at 8 seconds — Avoids overcooling that can lead to warping.
3.dKeep Fan Always On: OFF — Allows vapor to escape and avoids internal fogging.
3.eSlow Down for Cooling: ON — Improves surface finish with controlled cooling.
3.fForce Cooling for Overhangs: OFF — Overcooling can deform bridges in Timeplast.
3.gFan for Overhangs: 15% — Only for essential cooling in complex areas.
3.hPre-Start Fan Time: 2 seconds — Minimizes pressure differential during the first layer.4. Volumetric Flow
4.aMax Volumetric Speed: 12 mm³/s — Based on a melt flow index of ~15 g/10min, allows high-speed printing.
4.bRamming Speed: 3 mm³/s — Prevents bubbles or popping from pressure spikes.5. Retraction and Flow
5.aRetraction Distance: 0.4 mm — Minimal retraction required for soft filaments to avoid stringing.
5.bRetraction Speed: 15 mm/s — Slow enough to avoid pulling molten plastic.
5.cPressure Advance: 0.05 — Compensates for nozzle lag at high flow rates.
5.dFlow Ratio: 92% — Slight under-extrusion avoids swelling and surface artifacts.6. Precision Settings
6.aGap Closing Radius: 0.1 mm — Tolerant of gaps in thicker walls.
6.bArc Fitting: ON — Reduces G-code size and smooths curve transitions.
6.cElephant Foot Compensation: 0.1 mm — Offsets squishing in the first layer caused by large bead sizes.7. Walls and Shells
7.aWall Loops: 2 — Minimum for strength when using a 0.8 mm nozzle.
7.bDetect Thin Walls: ON — Ensures tight geometries aren’t skipped.
7.cTop/Bottom Shell Layers: 3 — Provides good coverage; increase if watertightness is needed.
7.dTop/Bottom Thickness: 1.2 mm — Equals 1.5x the nozzle size for solid strength.
7.eTop/Bottom Pattern: Monotonic — Distributes tension evenly and improves surface finish.8. Geometry and Movement
8.aWall Order: Inner before Outer — Creates cleaner outer surfaces.
8.bInfill First: OFF — Maintains precise outer dimensions.
8.cSmooth Speed Transition: ON — Prevents ringing caused by abrupt speed changes.
8.dSmooth Coefficient: 80 — Ideal damping for soft materials.
8.eAvoid Crossing Wall: ON — Minimizes stringing across part walls.
8.fMax Detour for Crossing: 10 mm or 5% — Balances time with print cleanliness.9. Layer and Width Settings
9.aLayer Height: 0.3 mm — Optimal for strength and resolution using a 0.8 mm nozzle.
9.bInitial Layer Height: 0.35 mm — Slightly higher to improve adhesion.
9.cLine Widths (all): 0.8 mm — Matches nozzle diameter for consistent extrusion.10. Seam Settings
10.aSeam Position: Aligned or Back — Use aligned for mechanical consistency, back for visual appeal.
10.bSmart Scarf Seam: ON — Automatically adjusts seam location to reduce visual impact.
10.cSeam Angle: 155° — Standard seam angle for clean transitions.
10.dSeam Steps: 10 — Smooths seam path and improves visual finish.11. Infill Settings
11.aWall/Infill Overlap: 10% — Prevents infill from deforming soft exterior walls.
11.bInfill Combination: ON — Consolidates paths for efficiency.
11.cDetect Floating Shells: ON — Ensures unsupported vertical structures are printed reliably.
11.dSparse Infill Density: 20–25% — Balanced rigidity vs. material use.
11.eSparse Pattern: Grid — Stable and efficient for flexible geometries.12. Speed Settings
12.aTravel: 160 mm/s — Fast but safe against backlash.
12.bInitial Layer: 15 mm/s — Prevents nozzle from skimming and ensures bed adhesion.
12.cOuter Wall: 60 mm/s — Controlled speed for surface quality.
12.dInner Wall: 90 mm/s — Slightly faster without compromising control.
12.eSmall Perimeter: 35 mm/s — Reduced speed for detailed geometry.
12.fTop Surface: 40 mm/s — Improves finish on topmost layers.
12.gInfill: 100–120 mm/s — Takes advantage of high flowability.13. Acceleration Settings
13.aNormal Print: 2000 mm/s² — Prevents ringing in soft filaments.
13.bTravel: 4000 mm/s² — Enables fast movement without harsh transitions.
13.cInitial Layer: 300 mm/s² — Gentle movement prevents lifting from the bed.
13.dOuter Wall: 1500 mm/s² — Improves outer surface clarity.
13.eInner Wall: 2000 mm/s² — Balanced for structural components.
13.fTop Surface: 1500 mm/s² — Ensures smooth detailing.14. Adhesion and Brims
14.aSkirt Loops: 2 — Helps prime nozzle and start cleanly.
14.bBrim Width: 6 mm — Helps hold soft materials down.
14.cBrim Gap: 0.15 mm — Allows for easy removal without tearing.15. Prime Tower and Flush Settings
15.aPrime Tower: ON — Purges moisture and early flow inconsistencies.
15.bTower Width: 40 mm — Prevents collapse due to heat.
15.cBrim Width (Tower): 4 mm — Adds stability to the purge base.
15.dFlush Into Support: ON — Discards unwanted early flow safely.16. G-Code Start Script
M900 K0.05 ; Pressure Advance M106 S0 ; Fan off G92 E0 G1 E15 F300 ; purge line G92 E0
17. Additional Notes
17.aDry filament at 100°C for 2 hours before use.
17.bStore with desiccant.
17.cKeep extruder door open to allow vapor to escape.
17.dAvoid long dwell times at high temperatures.If you need print settings for other nozzle sizes, feel free to reach out to us at timeplast@timeplast.com — we’ll be happy to help.
Free U.S. standard shipping on orders of 5+ spools!
Custom colors for 5+ same-type spools’ orders
Fire - Gen 2
Burnable 3D filament
-
TimeMass Fire Gen 2 is a burnable 3D printing filament made of water, wood, calcium carbonate, vinegar, in-house made and patented polymerized alcohol.
It prints fast, melts smooth, burns clean, and yes—it’s designed to ignite on purpose. Unlike traditional filaments that either melt like sad spaghetti or combust like a campfire mistake, this one burns right.
Want to print candles? Fire sculptures? Ritual objects for your post-plastic utopia? Go wild. You can even design your prints to control how they burn—fast, slow, flashy, or dramatic.
Pro tip: treat your print like a wick. Too thick? It’ll choke. Too thin? It’ll vanish. Just right? Beautiful combustion.
Need Ideas? Here You Go:
Spiral Towers – fire climbs up like it’s doing performance art.
Geometric Lanterns – pretty shapes + oxygen = dramatic collapse.
Flame Trees – fast-burning branches, slow-burning trunks.
Fire Flowers – petals curl and vanish while the stem holds the line.
Maze Prints – fire snakes through like it’s solving a puzzle.
Starbursts – spikes ignite like a slow-motion explosion.
Wavy Sculptures – dynamic flames that ripple as they burn.
You can even pause the print to drop in oils or other additives. TimeMass Fire holds them, absorbs them, and releases them mid-burn. Yes, your candle can smell like bergamot and existential closure.
Why It Matters:
Burns efficiently with minimal residue.
Prints on standard 3D printers.
Customizable burn rates.
Cleaner alternative to paraffin wax and plastic trash.
Absorbs oils and additives mid-print.
Supports sustainability without sacrificing creativity.
Basically, it’s a burnable, sculptable, programmable piece of environmental art.
Welcome to the future of fire. No paraffin. No guilt. Just combustion, on your terms. -
Click here to access our specialized TimeMass GPT Assistant. Just tell it your printer model and the TimeMass filament you're using—it will instantly recommend the exact parameters you need to start printing successfully.
Using a Bambu Lab printer?
Click here to download our updated Bambu Lab profile. All printing parameters are fully optimized and tested—just load the file and start printing.1. Introduction
These parameters are designed to help avoid printing issues; however, temperatures and speed timings can be adjusted based on your specific goals. For example, if you prefer a less rigid result, we recommend using a lower temperature. This section outlines a complete slicing and printing profile for TimeMass Fire, tailored for printers with a 0.8 mm nozzle. If the print is not being successful, please lower the nozzle temperature by 10°C and start over until an optimal print is achieved. While these examples were printed with a 0.8 mm nozzle, TimeMass can be used with any nozzle size. Please check the manual for printing parameters with all the other nozzle sizes.2. Temperature Settings
2.aNozzle Temperature: 240°C — Optimal for flowability while avoiding decomposition (which begins around 250°C).
2.bBed Temperature: 95°C — Ensures strong first-layer adhesion and prevents moisture bubbling.
2.cNozzle Temperature Range: 230–245°C — Timeplast melts around 165°C but prints best at 240°C for precise viscosity control.3. Cooling Settings
3.aNo Cooling for First Layers: 3 layers — Prevents shrinkage due to rapid cooling of moisture-rich filament.
3.bFan Minimum Speed: 0% for the first 100 seconds — Allows heat retention during early layers.
3.cFan Maximum Speed: 15% starting at 8 seconds — Avoids overcooling that can lead to warping.
3.dKeep Fan Always On: OFF — Allows vapor to escape and avoids internal fogging.
3.eSlow Down for Cooling: ON — Improves surface finish with controlled cooling.
3.fForce Cooling for Overhangs: OFF — Overcooling can deform bridges in Timeplast.
3.gFan for Overhangs: 15% — Only for essential cooling in complex areas.
3.hPre-Start Fan Time: 2 seconds — Minimizes pressure differential during the first layer.4. Volumetric Flow
4.aMax Volumetric Speed: 12 mm³/s — Based on a melt flow index of ~15 g/10min, allows high-speed printing.
4.bRamming Speed: 3 mm³/s — Prevents bubbles or popping from pressure spikes.5. Retraction and Flow
5.aRetraction Distance: 0.4 mm — Minimal retraction required for soft filaments to avoid stringing.
5.bRetraction Speed: 15 mm/s — Slow enough to avoid pulling molten plastic.
5.cPressure Advance: 0.05 — Compensates for nozzle lag at high flow rates.
5.dFlow Ratio: 92% — Slight under-extrusion avoids swelling and surface artifacts.6. Precision Settings
6.aGap Closing Radius: 0.1 mm — Tolerant of gaps in thicker walls.
6.bArc Fitting: ON — Reduces G-code size and smooths curve transitions.
6.cElephant Foot Compensation: 0.1 mm — Offsets squishing in the first layer caused by large bead sizes.7. Walls and Shells
7.aWall Loops: 2 — Minimum for strength when using a 0.8 mm nozzle.
7.bDetect Thin Walls: ON — Ensures tight geometries aren’t skipped.
7.cTop/Bottom Shell Layers: 3 — Provides good coverage; increase if watertightness is needed.
7.dTop/Bottom Thickness: 1.2 mm — Equals 1.5x the nozzle size for solid strength.
7.eTop/Bottom Pattern: Monotonic — Distributes tension evenly and improves surface finish.8. Geometry and Movement
8.aWall Order: Inner before Outer — Creates cleaner outer surfaces.
8.bInfill First: OFF — Maintains precise outer dimensions.
8.cSmooth Speed Transition: ON — Prevents ringing caused by abrupt speed changes.
8.dSmooth Coefficient: 80 — Ideal damping for soft materials.
8.eAvoid Crossing Wall: ON — Minimizes stringing across part walls.
8.fMax Detour for Crossing: 10 mm or 5% — Balances time with print cleanliness.9. Layer and Width Settings
9.aLayer Height: 0.3 mm — Optimal for strength and resolution using a 0.8 mm nozzle.
9.bInitial Layer Height: 0.35 mm — Slightly higher to improve adhesion.
9.cLine Widths (all): 0.8 mm — Matches nozzle diameter for consistent extrusion.10. Seam Settings
10.aSeam Position: Aligned or Back — Use aligned for mechanical consistency, back for visual appeal.
10.bSmart Scarf Seam: ON — Automatically adjusts seam location to reduce visual impact.
10.cSeam Angle: 155° — Standard seam angle for clean transitions.
10.dSeam Steps: 10 — Smooths seam path and improves visual finish.11. Infill Settings
11.aWall/Infill Overlap: 10% — Prevents infill from deforming soft exterior walls.
11.bInfill Combination: ON — Consolidates paths for efficiency.
11.cDetect Floating Shells: ON — Ensures unsupported vertical structures are printed reliably.
11.dSparse Infill Density: 20–25% — Balanced rigidity vs. material use.
11.eSparse Pattern: Grid — Stable and efficient for flexible geometries.12. Speed Settings
12.aTravel: 160 mm/s — Fast but safe against backlash.
12.bInitial Layer: 15 mm/s — Prevents nozzle from skimming and ensures bed adhesion.
12.cOuter Wall: 60 mm/s — Controlled speed for surface quality.
12.dInner Wall: 90 mm/s — Slightly faster without compromising control.
12.eSmall Perimeter: 35 mm/s — Reduced speed for detailed geometry.
12.fTop Surface: 40 mm/s — Improves finish on topmost layers.
12.gInfill: 100–120 mm/s — Takes advantage of high flowability.13. Acceleration Settings
13.aNormal Print: 2000 mm/s² — Prevents ringing in soft filaments.
13.bTravel: 4000 mm/s² — Enables fast movement without harsh transitions.
13.cInitial Layer: 300 mm/s² — Gentle movement prevents lifting from the bed.
13.dOuter Wall: 1500 mm/s² — Improves outer surface clarity.
13.eInner Wall: 2000 mm/s² — Balanced for structural components.
13.fTop Surface: 1500 mm/s² — Ensures smooth detailing.14. Adhesion and Brims
14.aSkirt Loops: 2 — Helps prime nozzle and start cleanly.
14.bBrim Width: 6 mm — Helps hold soft materials down.
14.cBrim Gap: 0.15 mm — Allows for easy removal without tearing.15. Prime Tower and Flush Settings
15.aPrime Tower: ON — Purges moisture and early flow inconsistencies.
15.bTower Width: 40 mm — Prevents collapse due to heat.
15.cBrim Width (Tower): 4 mm — Adds stability to the purge base.
15.dFlush Into Support: ON — Discards unwanted early flow safely.16. G-Code Start Script
M900 K0.05 ; Pressure Advance M106 S0 ; Fan off G92 E0 G1 E15 F300 ; purge line G92 E0
17. Additional Notes
17.aDry filament at 100°C for 2 hours before use.
17.bStore with desiccant.
17.cKeep extruder door open to allow vapor to escape.
17.dAvoid long dwell times at high temperatures.If you need print settings for other nozzle sizes, feel free to reach out to us at timeplast@timeplast.com — we’ll be happy to help.
Free U.S. standard shipping on orders of 5+ spools!
Custom colors for 5+ same-type spools’ orders
Light - Gen 2
The Illumination 3D filament
-
TimeMass Light - Make It Glow Without Wiring a Small City
TimeMass Light works like optical fiber… if optical fiber decided to chill out and light up everything, not just one boring line. Instead of shooting light straight through like a laser pointer at a PowerPoint, this filament scatters and diffuses it across its entire body. Translation? The whole thing glows like it knows it’s being admired.
Here’s how the magic works (without the wand):
• Microstructured diffusion:
We pack the filament with microscopic voids, sneaky shifts in refractive index, and nanoparticles that scatter light like it owes them money.
• Selective diffraction:
Unlike transparent materials that pretend to be cool and just let light pass through, TimeMass Light stays interesting—spreading the glow evenly instead of making one pixel overheat with existential pressure.
• Smart light entry:
Want it to glow properly? Cut or sand the base flat. The smoother it is, the easier it is for your LED, flashlight, or candle (yes, we make those too) to pump light inside and let it party.
Polishing the entry point isn’t extra credit—it’s how you avoid “tiny flashlight trapped in plastic cube” vibes. The flatter and cleaner the surface, the better the filament does its thing: glowing like it was born to.
⸻
Stuff You Can Do With It (That Looks Cooler in the Dark):
• Low-energy lighting: Glowing structures that don’t need 47 LEDs and a power grid.
• Wearables: Print accessories that light up your outfit and make you visible to cars and confused party guests.
• Art & signage: Want a glowing logo with no wires? Done. Just don’t spell your name wrong.
• Emergency lighting: Self-lit exit signs for power outages, low-key apocalypses, or overly dramatic basements.
• Sci-fi layering experiments: Create semi-transparent, light-diffusing structures that make it look like you’re up to something.
-
Click here to access our specialized TimeMass GPT Assistant. Just tell it your printer model and the TimeMass filament you're using—it will instantly recommend the exact parameters you need to start printing successfully.
Using a Bambu Lab printer?
Click here to download our updated Bambu Lab profile. All printing parameters are fully optimized and tested—just load the file and start printing.1. Introduction
These parameters are designed to help avoid printing issues; however, temperatures and speed timings can be adjusted based on your specific goals. For example, if you prefer a less rigid result, we recommend using a lower temperature. This section outlines a complete slicing and printing profile for TimeMass Light, tailored for printers with a 0.8 mm nozzle. If the print is not being successful, please lower the nozzle temperature by 10°C and start over until an optimal print is achieved. While these examples were printed with a 0.8 mm nozzle, TimeMass can be used with any nozzle size. Please check the manual for printing parameters with all the other nozzle sizes.2. Temperature Settings
2.aNozzle Temperature: 240°C — Optimal for flowability while avoiding decomposition (which begins around 250°C).
2.bBed Temperature: 95°C — Ensures strong first-layer adhesion and prevents moisture bubbling.
2.cNozzle Temperature Range: 230–245°C — Timeplast melts around 165°C but prints best at 240°C for precise viscosity control.3. Cooling Settings
3.aNo Cooling for First Layers: 3 layers — Prevents shrinkage due to rapid cooling of moisture-rich filament.
3.bFan Minimum Speed: 0% for the first 100 seconds — Allows heat retention during early layers.
3.cFan Maximum Speed: 15% starting at 8 seconds — Avoids overcooling that can lead to warping.
3.dKeep Fan Always On: OFF — Allows vapor to escape and avoids internal fogging.
3.eSlow Down for Cooling: ON — Improves surface finish with controlled cooling.
3.fForce Cooling for Overhangs: OFF — Overcooling can deform bridges in Timeplast.
3.gFan for Overhangs: 15% — Only for essential cooling in complex areas.
3.hPre-Start Fan Time: 2 seconds — Minimizes pressure differential during the first layer.4. Volumetric Flow
4.aMax Volumetric Speed: 12 mm³/s — Based on a melt flow index of ~15 g/10min, allows high-speed printing.
4.bRamming Speed: 3 mm³/s — Prevents bubbles or popping from pressure spikes.5. Retraction and Flow
5.aRetraction Distance: 0.4 mm — Minimal retraction required for soft filaments to avoid stringing.
5.bRetraction Speed: 15 mm/s — Slow enough to avoid pulling molten plastic.
5.cPressure Advance: 0.05 — Compensates for nozzle lag at high flow rates.
5.dFlow Ratio: 92% — Slight under-extrusion avoids swelling and surface artifacts.6. Precision Settings
6.aGap Closing Radius: 0.1 mm — Tolerant of gaps in thicker walls.
6.bArc Fitting: ON — Reduces G-code size and smooths curve transitions.
6.cElephant Foot Compensation: 0.1 mm — Offsets squishing in the first layer caused by large bead sizes.7. Walls and Shells
7.aWall Loops: 2 — Minimum for strength when using a 0.8 mm nozzle.
7.bDetect Thin Walls: ON — Ensures tight geometries aren’t skipped.
7.cTop/Bottom Shell Layers: 3 — Provides good coverage; increase if watertightness is needed.
7.dTop/Bottom Thickness: 1.2 mm — Equals 1.5x the nozzle size for solid strength.
7.eTop/Bottom Pattern: Monotonic — Distributes tension evenly and improves surface finish.8. Geometry and Movement
8.aWall Order: Inner before Outer — Creates cleaner outer surfaces.
8.bInfill First: OFF — Maintains precise outer dimensions.
8.cSmooth Speed Transition: ON — Prevents ringing caused by abrupt speed changes.
8.dSmooth Coefficient: 80 — Ideal damping for soft materials.
8.eAvoid Crossing Wall: ON — Minimizes stringing across part walls.
8.fMax Detour for Crossing: 10 mm or 5% — Balances time with print cleanliness.9. Layer and Width Settings
9.aLayer Height: 0.3 mm — Optimal for strength and resolution using a 0.8 mm nozzle.
9.bInitial Layer Height: 0.35 mm — Slightly higher to improve adhesion.
9.cLine Widths (all): 0.8 mm — Matches nozzle diameter for consistent extrusion.10. Seam Settings
10.aSeam Position: Aligned or Back — Use aligned for mechanical consistency, back for visual appeal.
10.bSmart Scarf Seam: ON — Automatically adjusts seam location to reduce visual impact.
10.cSeam Angle: 155° — Standard seam angle for clean transitions.
10.dSeam Steps: 10 — Smooths seam path and improves visual finish.11. Infill Settings
11.aWall/Infill Overlap: 10% — Prevents infill from deforming soft exterior walls.
11.bInfill Combination: ON — Consolidates paths for efficiency.
11.cDetect Floating Shells: ON — Ensures unsupported vertical structures are printed reliably.
11.dSparse Infill Density: 20–25% — Balanced rigidity vs. material use.
11.eSparse Pattern: Grid — Stable and efficient for flexible geometries.12. Speed Settings
12.aTravel: 160 mm/s — Fast but safe against backlash.
12.bInitial Layer: 15 mm/s — Prevents nozzle from skimming and ensures bed adhesion.
12.cOuter Wall: 60 mm/s — Controlled speed for surface quality.
12.dInner Wall: 90 mm/s — Slightly faster without compromising control.
12.eSmall Perimeter: 35 mm/s — Reduced speed for detailed geometry.
12.fTop Surface: 40 mm/s — Improves finish on topmost layers.
12.gInfill: 100–120 mm/s — Takes advantage of high flowability.13. Acceleration Settings
13.aNormal Print: 2000 mm/s² — Prevents ringing in soft filaments.
13.bTravel: 4000 mm/s² — Enables fast movement without harsh transitions.
13.cInitial Layer: 300 mm/s² — Gentle movement prevents lifting from the bed.
13.dOuter Wall: 1500 mm/s² — Improves outer surface clarity.
13.eInner Wall: 2000 mm/s² — Balanced for structural components.
13.fTop Surface: 1500 mm/s² — Ensures smooth detailing.14. Adhesion and Brims
14.aSkirt Loops: 2 — Helps prime nozzle and start cleanly.
14.bBrim Width: 6 mm — Helps hold soft materials down.
14.cBrim Gap: 0.15 mm — Allows for easy removal without tearing.15. Prime Tower and Flush Settings
15.aPrime Tower: ON — Purges moisture and early flow inconsistencies.
15.bTower Width: 40 mm — Prevents collapse due to heat.
15.cBrim Width (Tower): 4 mm — Adds stability to the purge base.
15.dFlush Into Support: ON — Discards unwanted early flow safely.16. G-Code Start Script
M900 K0.05 ; Pressure Advance M106 S0 ; Fan off G92 E0 G1 E15 F300 ; purge line G92 E0
17. Additional Notes
17.aDry filament at 100°C for 2 hours before use.
17.bStore with desiccant.
17.cKeep extruder door open to allow vapor to escape.
17.dAvoid long dwell times at high temperatures.If you need print settings for other nozzle sizes, feel free to reach out to us at timeplast@timeplast.com — we’ll be happy to help.
Free U.S. standard shipping on orders of 5+ spools!
Custom colors for 5+ same-type spools’ orders
Plant Vitamin - Gen 2
Growth, Layer by Layer
-
TimeMass Plant Vitamin is a water-retaining, nutrient-loaded filament engineered for slow-release fertilization right from the print bed. Built with carbon, nitrogen, phosphorus, and sulfur—plus structured water and calcium carbonate—it lets you 3D print objects that nourish plants over time.
No runoff. No burst-release. Just sustained growth, powered by smart material design.
How it works:
Hydrophilic matrix absorbs moisture and dissolves slowly, releasing nutrients in sync with plant needs.
Water = trigger – Pods can be printed to behave like analog biological computers, using moisture to time and deliver nutrient output.
No batteries. No sensors. Just physics.
Full Nutrient Breakdown (per 350g spool):
Nitrogen (N): 10.8 g – Chlorophyll production & leaf growth
Phosphate (P₂O₅): 8.4 g – Root development & flowering
Potash (K₂O): 6.8 g – Disease resistance & overall health
Calcium (Ca): 2.4 g – Cell wall structure & nutrient absorption
Magnesium (Mg): 0.8 g – Photosynthesis & enzyme function
Core Material:
Structured Water: 70% – Boosts solubility and uptake
Calcium Carbonate: 20% – Strengthens the filament and feeds the soil
Sustained Release Design:
Nutrients are embedded within the Timeplast Plus matrix for gradual delivery
Structured water ensures efficient solubility
No leaching = no waste
Stability & Vitamin Integrity (Because Growers Actually Care):
Microencapsulation – Heat-resistant shells (sol-gel silica, melamine, urea-formaldehyde, etc.) prevent degradation during extrusion.
Vitamin Derivatives – Stable precursors like ascorbyl palmitate reactivate in soil through pH, enzymes, or hydration.
Multi-phase Composite – Core-shell architecture keeps active components cool during print.
Low-shear, thermally controlled extrusion – Custom nozzles and low-friction channels reduce heat spikes.
Water-based integration – Vitamins are solvent-bound into low-temp meltable additives, preserving potency.
Where to use it:
Urban gardening & hydroponics – Print self-feeding seed pods, planters, or nutrient spikes
Precision agriculture – Design root-zone diffusers to boost yield without runoff
Reforestation – Print biodegradable seed capsules with long-term nutrient support
Irrigation aids & smart pots – Combine watering and feeding in one functional print
The result?
Printed structures that actually feed the soil. No over-fertilizing. No chemical waste. Just controlled, water-powered nutrient delivery—designed by you.Need Ideas? Here You Go:
Self-fertilizing plant pots and holders, eliminating the need for chemical fertilizers.
Water-dispersible nutrient discs that can be buried in soil for controlled nutrient release.
Eco-friendly seedling trays that break down naturally, enriching the soil.
Hydroponic nutrient carriers, improving plant growth in water-based systems.
Custom garden markers, serving both as labels and soil enhancers.
-
Click here to access our specialized TimeMass GPT Assistant. Just tell it your printer model and the TimeMass filament you're using—it will instantly recommend the exact parameters you need to start printing successfully.
Using a Bambu Lab printer?
Click here to download our updated Bambu Lab profile. All printing parameters are fully optimized and tested—just load the file and start printing.1. Introduction
These parameters are designed to help avoid printing issues; however, temperatures and speed timings can be adjusted based on your specific goals. For example, if you prefer a less rigid result, we recommend using a lower temperature. This section outlines a complete slicing and printing profile for TimeMass Plant Vitamin, tailored for printers with a 0.8 mm nozzle. If the print is not being successful, please lower the nozzle temperature by 10°C and start over until an optimal print is achieved. While these examples were printed with a 0.8 mm nozzle, TimeMass can be used with any nozzle size. Please check the manual for printing parameters with all the other nozzle sizes.2. Temperature Settings
2.aNozzle Temperature: 240°C — Optimal for flowability while avoiding decomposition (which begins around 250°C).
2.bBed Temperature: 95°C — Ensures strong first-layer adhesion and prevents moisture bubbling.
2.cNozzle Temperature Range: 230–245°C — Timeplast melts around 165°C but prints best at 240°C for precise viscosity control.3. Cooling Settings
3.aNo Cooling for First Layers: 3 layers — Prevents shrinkage due to rapid cooling of moisture-rich filament.
3.bFan Minimum Speed: 0% for the first 100 seconds — Allows heat retention during early layers.
3.cFan Maximum Speed: 15% starting at 8 seconds — Avoids overcooling that can lead to warping.
3.dKeep Fan Always On: OFF — Allows vapor to escape and avoids internal fogging.
3.eSlow Down for Cooling: ON — Improves surface finish with controlled cooling.
3.fForce Cooling for Overhangs: OFF — Overcooling can deform bridges in Timeplast.
3.gFan for Overhangs: 15% — Only for essential cooling in complex areas.
3.hPre-Start Fan Time: 2 seconds — Minimizes pressure differential during the first layer.4. Volumetric Flow
4.aMax Volumetric Speed: 12 mm³/s — Based on a melt flow index of ~15 g/10min, allows high-speed printing.
4.bRamming Speed: 3 mm³/s — Prevents bubbles or popping from pressure spikes.5. Retraction and Flow
5.aRetraction Distance: 0.4 mm — Minimal retraction required for soft filaments to avoid stringing.
5.bRetraction Speed: 15 mm/s — Slow enough to avoid pulling molten plastic.
5.cPressure Advance: 0.05 — Compensates for nozzle lag at high flow rates.
5.dFlow Ratio: 92% — Slight under-extrusion avoids swelling and surface artifacts.6. Precision Settings
6.aGap Closing Radius: 0.1 mm — Tolerant of gaps in thicker walls.
6.bArc Fitting: ON — Reduces G-code size and smooths curve transitions.
6.cElephant Foot Compensation: 0.1 mm — Offsets squishing in the first layer caused by large bead sizes.7. Walls and Shells
7.aWall Loops: 2 — Minimum for strength when using a 0.8 mm nozzle.
7.bDetect Thin Walls: ON — Ensures tight geometries aren’t skipped.
7.cTop/Bottom Shell Layers: 3 — Provides good coverage; increase if watertightness is needed.
7.dTop/Bottom Thickness: 1.2 mm — Equals 1.5x the nozzle size for solid strength.
7.eTop/Bottom Pattern: Monotonic — Distributes tension evenly and improves surface finish.8. Geometry and Movement
8.aWall Order: Inner before Outer — Creates cleaner outer surfaces.
8.bInfill First: OFF — Maintains precise outer dimensions.
8.cSmooth Speed Transition: ON — Prevents ringing caused by abrupt speed changes.
8.dSmooth Coefficient: 80 — Ideal damping for soft materials.
8.eAvoid Crossing Wall: ON — Minimizes stringing across part walls.
8.fMax Detour for Crossing: 10 mm or 5% — Balances time with print cleanliness.9. Layer and Width Settings
9.aLayer Height: 0.3 mm — Optimal for strength and resolution using a 0.8 mm nozzle.
9.bInitial Layer Height: 0.35 mm — Slightly higher to improve adhesion.
9.cLine Widths (all): 0.8 mm — Matches nozzle diameter for consistent extrusion.10. Seam Settings
10.aSeam Position: Aligned or Back — Use aligned for mechanical consistency, back for visual appeal.
10.bSmart Scarf Seam: ON — Automatically adjusts seam location to reduce visual impact.
10.cSeam Angle: 155° — Standard seam angle for clean transitions.
10.dSeam Steps: 10 — Smooths seam path and improves visual finish.11. Infill Settings
11.aWall/Infill Overlap: 10% — Prevents infill from deforming soft exterior walls.
11.bInfill Combination: ON — Consolidates paths for efficiency.
11.cDetect Floating Shells: ON — Ensures unsupported vertical structures are printed reliably.
11.dSparse Infill Density: 20–25% — Balanced rigidity vs. material use.
11.eSparse Pattern: Grid — Stable and efficient for flexible geometries.12. Speed Settings
12.aTravel: 160 mm/s — Fast but safe against backlash.
12.bInitial Layer: 15 mm/s — Prevents nozzle from skimming and ensures bed adhesion.
12.cOuter Wall: 60 mm/s — Controlled speed for surface quality.
12.dInner Wall: 90 mm/s — Slightly faster without compromising control.
12.eSmall Perimeter: 35 mm/s — Reduced speed for detailed geometry.
12.fTop Surface: 40 mm/s — Improves finish on topmost layers.
12.gInfill: 100–120 mm/s — Takes advantage of high flowability.13. Acceleration Settings
13.aNormal Print: 2000 mm/s² — Prevents ringing in soft filaments.
13.bTravel: 4000 mm/s² — Enables fast movement without harsh transitions.
13.cInitial Layer: 300 mm/s² — Gentle movement prevents lifting from the bed.
13.dOuter Wall: 1500 mm/s² — Improves outer surface clarity.
13.eInner Wall: 2000 mm/s² — Balanced for structural components.
13.fTop Surface: 1500 mm/s² — Ensures smooth detailing.14. Adhesion and Brims
14.aSkirt Loops: 2 — Helps prime nozzle and start cleanly.
14.bBrim Width: 6 mm — Helps hold soft materials down.
14.cBrim Gap: 0.15 mm — Allows for easy removal without tearing.15. Prime Tower and Flush Settings
15.aPrime Tower: ON — Purges moisture and early flow inconsistencies.
15.bTower Width: 40 mm — Prevents collapse due to heat.
15.cBrim Width (Tower): 4 mm — Adds stability to the purge base.
15.dFlush Into Support: ON — Discards unwanted early flow safely.16. G-Code Start Script
M900 K0.05 ; Pressure Advance M106 S0 ; Fan off G92 E0 G1 E15 F300 ; purge line G92 E0
17. Additional Notes
17.aDry filament at 100°C for 2 hours before use.
17.bStore with desiccant.
17.cKeep extruder door open to allow vapor to escape.
17.dAvoid long dwell times at high temperatures.If you need print settings for other nozzle sizes, feel free to reach out to us at timeplast@timeplast.com — we’ll be happy to help.
Free U.S. standard shipping on orders of 5+ spools!
Custom colors for 5+ same-type spools’ orders
We Accept:
Time-Programming Filaments
Active
Quick timed 4D filament
-
TimeMass Active by Timeplast is an advanced 3D printing filament designed to introduce 4D printing capabilities, where objects can transform over time due to their material composition. Unlike traditional filaments, TimeMass Active embeds time-sensitive water dissolution properties, allowing printed objects to change, dissolve, or degrade in a controlled manner when exposed to specific environmental triggers like water.
This revolutionary material aligns with sustainability goals, offering a potential solution for reducing plastic waste by ensuring objects don't persist indefinitely. It's a step beyond conventional biodegradable materials, as it can be precisely engineered for degradation timelines and environmental impact.
Need Ideas? Here You Go:
Active opens the door to a variety of cutting-edge applications, especially in industries that benefit from controlled degradation, temporary functionality, or sustainable disposal. Here are some key applications that can be manufactured with it:
1. Sustainable Packaging & Containers
Single-use packaging that dissolves in water or degrades after a set time.
Medical and pharmaceutical blister packs that disappear after use.
E-commerce mailers or shipping materials that break down naturally.
2. Medical & dissolvable Implants
Dissolvable medical devices (e.g., temporary surgical supports or drug-delivery capsules).
Dissolvable splints and casts for temporary use.
Eco-friendly sutures or wound dressings that dissolve safely in the body.
3. Fishing & Marine Applications
Water-soluble fishing line that reduces ocean waste.
Dissolvable bait holders for sustainable fishing practices.
Temporary aquatic structures that degrade naturally over time.
4. Construction & Temporary Structures
Scaffolding that disappears when exposed to rain or UV light.
Dissolvable moldings and supports for temporary installations.
Formwork for concrete that dissolves after the structure sets.
5. Smart Consumer Goods
Eco-friendly toys or festival products that disappear after use.
Single-use utensils or dishware that self-destruct in water.
Event wristbands and passes that vanish after an event ends.
6. Electronics & Smart Materials
Dissolvable circuits or casings for electronics.
Temporary RFID tags or security seals that disappear after use.
Eco-friendly wearable tech components designed for planned obsolescence.
7. Aerospace & Military
Time-sensitive drones or surveillance devices that degrade after deployment.
Dissolvable camouflage materials for stealth operations.
Temporary shelters that degrade in extreme environments.
8. Art & Design
Interactive sculptures or installations that disappear over time.
Water-soluble fashion pieces that change with rain or humidity.
Degradable 3D-printed decor for temporary displays.
Active has a huge potential for industries looking to reduce waste, enhance sustainability, and introduce functional degradation into 3D printed products.
-
Click here to access our specialized TimeMass GPT Assistant. Just tell it your printer model and the TimeMass filament you're using—it will instantly recommend the exact parameters you need to start printing successfully.
Using a Bambu Lab printer?
Click here to download our updated Bambu Lab profile. All printing parameters are fully optimized and tested—just load the file and start printing.1. Introduction
These parameters are designed to help avoid printing issues; however, temperatures and speed timings can be adjusted based on your specific goals. For example, if you prefer a less rigid result, we recommend using a lower temperature. This section outlines a complete slicing and printing profile for TimeMass Active, tailored for printers with a 0.8 mm nozzle. If the print is not being successful, please lower the nozzle temperature by 10°C and start over until an optimal print is achieved.While these examples were printed with a 0.8 mm nozzle, TimeMass can be used with any nozzle size. Please check the manual for printing parameters with all the other nozzle sizes.2. Temperature Settings
2.aNozzle Temperature: 240°C — Optimal for flowability while avoiding decomposition (which begins around 250°C).
2.bBed Temperature: 95°C — Ensures strong first-layer adhesion and prevents moisture bubbling.
2.cNozzle Temperature Range: 230–245°C — Timeplast melts around 165°C but prints best at 240°C for precise viscosity control.3. Cooling Settings
3.aNo Cooling for First Layers: 3 layers — Prevents shrinkage due to rapid cooling of moisture-rich filament.
3.bFan Minimum Speed: 0% for the first 100 seconds — Allows heat retention during early layers.
3.cFan Maximum Speed: 15% starting at 8 seconds — Avoids overcooling that can lead to warping.
3.dKeep Fan Always On: OFF — Allows vapor to escape and avoids internal fogging.
3.eSlow Down for Cooling: ON — Improves surface finish with controlled cooling.
3.fForce Cooling for Overhangs: OFF — Overcooling can deform bridges in Timeplast.
3.gFan for Overhangs: 15% — Only for essential cooling in complex areas.
3.hPre-Start Fan Time: 2 seconds — Minimizes pressure differential during the first layer.4. Volumetric Flow
4.aMax Volumetric Speed: 12 mm³/s — Based on a melt flow index of ~15 g/10min, allows high-speed printing.
4.bRamming Speed: 3 mm³/s — Prevents bubbles or popping from pressure spikes.5. Retraction and Flow
5.aRetraction Distance: 0.4 mm — Minimal retraction required for soft filaments to avoid stringing.
5.bRetraction Speed: 15 mm/s — Slow enough to avoid pulling molten plastic.
5.cPressure Advance: 0.05 — Compensates for nozzle lag at high flow rates.
5.dFlow Ratio: 92% — Slight under-extrusion avoids swelling and surface artifacts.6. Precision Settings
6.aGap Closing Radius: 0.1 mm — Tolerant of gaps in thicker walls.
6.bArc Fitting: ON — Reduces G-code size and smooths curve transitions.
6.cElephant Foot Compensation: 0.1 mm — Offsets squishing in the first layer caused by large bead sizes.7. Walls and Shells
7.aWall Loops: 2 — Minimum for strength when using a 0.8 mm nozzle.
7.bDetect Thin Walls: ON — Ensures tight geometries aren’t skipped.
7.cTop/Bottom Shell Layers: 3 — Provides good coverage; increase if watertightness is needed.
7.dTop/Bottom Thickness: 1.2 mm — Equals 1.5x the nozzle size for solid strength.
7.eTop/Bottom Pattern: Monotonic — Distributes tension evenly and improves surface finish.8. Geometry and Movement
8.aWall Order: Inner before Outer — Creates cleaner outer surfaces.
8.bInfill First: OFF — Maintains precise outer dimensions.
8.cSmooth Speed Transition: ON — Prevents ringing caused by abrupt speed changes.
8.dSmooth Coefficient: 80 — Ideal damping for soft materials.
8.eAvoid Crossing Wall: ON — Minimizes stringing across part walls.
8.fMax Detour for Crossing: 10 mm or 5% — Balances time with print cleanliness.9. Layer and Width Settings
9.aLayer Height: 0.3 mm — Optimal for strength and resolution using a 0.8 mm nozzle.
9.bInitial Layer Height: 0.35 mm — Slightly higher to improve adhesion.
9.cLine Widths (all): 0.8 mm — Matches nozzle diameter for consistent extrusion.10. Seam Settings
10.aSeam Position: Aligned or Back — Use aligned for mechanical consistency, back for visual appeal.
10.bSmart Scarf Seam: ON — Automatically adjusts seam location to reduce visual impact.
10.cSeam Angle: 155° — Standard seam angle for clean transitions.
10.dSeam Steps: 10 — Smooths seam path and improves visual finish.11. Infill Settings
11.aWall/Infill Overlap: 10% — Prevents infill from deforming soft exterior walls.
11.bInfill Combination: ON — Consolidates paths for efficiency.
11.cDetect Floating Shells: ON — Ensures unsupported vertical structures are printed reliably.
11.dSparse Infill Density: 20–25% — Balanced rigidity vs. material use.
11.eSparse Pattern: Grid — Stable and efficient for flexible geometries.12. Speed Settings
12.aTravel: 160 mm/s — Fast but safe against backlash.
12.bInitial Layer: 15 mm/s — Prevents nozzle from skimming and ensures bed adhesion.
12.cOuter Wall: 60 mm/s — Controlled speed for surface quality.
12.dInner Wall: 90 mm/s — Slightly faster without compromising control.
12.eSmall Perimeter: 35 mm/s — Reduced speed for detailed geometry.
12.fTop Surface: 40 mm/s — Improves finish on topmost layers.
12.gInfill: 100–120 mm/s — Takes advantage of high flowability.13. Acceleration Settings
13.aNormal Print: 2000 mm/s² — Prevents ringing in soft filaments.
13.bTravel: 4000 mm/s² — Enables fast movement without harsh transitions.
13.cInitial Layer: 300 mm/s² — Gentle movement prevents lifting from the bed.
13.dOuter Wall: 1500 mm/s² — Improves outer surface clarity.
13.eInner Wall: 2000 mm/s² — Balanced for structural components.
13.fTop Surface: 1500 mm/s² — Ensures smooth detailing.14. Adhesion and Brims
14.aSkirt Loops: 2 — Helps prime nozzle and start cleanly.
14.bBrim Width: 6 mm — Helps hold soft materials down.
14.cBrim Gap: 0.15 mm — Allows for easy removal without tearing.15. Prime Tower and Flush Settings
15.aPrime Tower: ON — Purges moisture and early flow inconsistencies.
15.bTower Width: 40 mm — Prevents collapse due to heat.
15.cBrim Width (Tower): 4 mm — Adds stability to the purge base.
15.dFlush Into Support: ON — Discards unwanted early flow safely.16. G-Code Start Script
M900 K0.05 ; Pressure Advance M106 S0 ; Fan off G92 E0 G1 E15 F300 ; purge line G92 E0
17. Additional Notes
17.aDry filament at 100°C for 2 hours before use.
17.bStore with desiccant.
17.cKeep extruder door open to allow vapor to escape.
17.dAvoid long dwell times at high temperatures.If you need print settings for other nozzle sizes, feel free to reach out to us at timeplast@timeplast.com — we’ll be happy to help.
Free U.S. standard shipping on orders of 5+ spools!
Custom colors for 5+ same-type spools’ orders
Extended
Medium timed 4D filament
-
TimeMass Extended by Timeplast is a versatile 3D printing filament designed to offer a controlled mid-point between short-term dissolution and long-term durability. Positioned between TimeMass Active and TimeMass Passive, it maintains structural integrity for extended periods before gradually dissolving in water. This makes it ideal for applications that require temporary functionality with a longer lifecycle.
Key Features:
- Extended Dissolution Timeline – Designed to last months or years before dissolving.
- Environmentally Responsive – Begins degradation only under specific moisture exposure.
- Sustainable Alternative – Fully dissolves without leaving microplastics behind.
- Functional Durability – Suitable for semi-permanent tools, fixtures, and packaging.Ideal Uses:
Outdoor tools or fixtures that naturally disappear over seasons.
Medical models or trays intended for medium-term use.
Temporary signage, displays, or installations.
Educational kits with limited lifespan needs.
TimeMass Extended offers the perfect balance for users needing a filament that’s neither too fleeting nor permanently persistent—just right for sustainability and functionality.
-
Click here to access our specialized TimeMass GPT Assistant. Just tell it your printer model and the TimeMass filament you're using—it will instantly recommend the exact parameters you need to start printing successfully.
Using a Bambu Lab printer?
Click here to download our updated Bambu Lab profile. All printing parameters are fully optimized and tested—just load the file and start printing.1. Introduction
These parameters are designed to help avoid printing issues; however, temperatures and speed timings can be adjusted based on your specific goals. For example, if you prefer a less rigid result, we recommend using a lower temperature. This section outlines a complete slicing and printing profile for TimeMass Extended, tailored for printers with a 0.8 mm nozzle. If the print is not being successful, please lower the nozzle temperature by 10°C and start over until an optimal print is achieved.While these examples were printed with a 0.8 mm nozzle, TimeMass can be used with any nozzle size. Please check the manual for printing parameters with all the other nozzle sizes.2. Temperature Settings
2.aNozzle Temperature: 240°C — Optimal for flowability while avoiding decomposition (which begins around 250°C).
2.bBed Temperature: 95°C — Ensures strong first-layer adhesion and prevents moisture bubbling.
2.cNozzle Temperature Range: 230–245°C — Timeplast melts around 165°C but prints best at 240°C for precise viscosity control.3. Cooling Settings
3.aNo Cooling for First Layers: 3 layers — Prevents shrinkage due to rapid cooling of moisture-rich filament.
3.bFan Minimum Speed: 0% for the first 100 seconds — Allows heat retention during early layers.
3.cFan Maximum Speed: 15% starting at 8 seconds — Avoids overcooling that can lead to warping.
3.dKeep Fan Always On: OFF — Allows vapor to escape and avoids internal fogging.
3.eSlow Down for Cooling: ON — Improves surface finish with controlled cooling.
3.fForce Cooling for Overhangs: OFF — Overcooling can deform bridges in Timeplast.
3.gFan for Overhangs: 15% — Only for essential cooling in complex areas.
3.hPre-Start Fan Time: 2 seconds — Minimizes pressure differential during the first layer.4. Volumetric Flow
4.aMax Volumetric Speed: 12 mm³/s — Based on a melt flow index of ~15 g/10min, allows high-speed printing.
4.bRamming Speed: 3 mm³/s — Prevents bubbles or popping from pressure spikes.5. Retraction and Flow
5.aRetraction Distance: 0.4 mm — Minimal retraction required for soft filaments to avoid stringing.
5.bRetraction Speed: 15 mm/s — Slow enough to avoid pulling molten plastic.
5.cPressure Advance: 0.05 — Compensates for nozzle lag at high flow rates.
5.dFlow Ratio: 92% — Slight under-extrusion avoids swelling and surface artifacts.6. Precision Settings
6.aGap Closing Radius: 0.1 mm — Tolerant of gaps in thicker walls.
6.bArc Fitting: ON — Reduces G-code size and smooths curve transitions.
6.cElephant Foot Compensation: 0.1 mm — Offsets squishing in the first layer caused by large bead sizes.7. Walls and Shells
7.aWall Loops: 2 — Minimum for strength when using a 0.8 mm nozzle.
7.bDetect Thin Walls: ON — Ensures tight geometries aren’t skipped.
7.cTop/Bottom Shell Layers: 3 — Provides good coverage; increase if watertightness is needed.
7.dTop/Bottom Thickness: 1.2 mm — Equals 1.5x the nozzle size for solid strength.
7.eTop/Bottom Pattern: Monotonic — Distributes tension evenly and improves surface finish.8. Geometry and Movement
8.aWall Order: Inner before Outer — Creates cleaner outer surfaces.
8.bInfill First: OFF — Maintains precise outer dimensions.
8.cSmooth Speed Transition: ON — Prevents ringing caused by abrupt speed changes.
8.dSmooth Coefficient: 80 — Ideal damping for soft materials.
8.eAvoid Crossing Wall: ON — Minimizes stringing across part walls.
8.fMax Detour for Crossing: 10 mm or 5% — Balances time with print cleanliness.9. Layer and Width Settings
9.aLayer Height: 0.3 mm — Optimal for strength and resolution using a 0.8 mm nozzle.
9.bInitial Layer Height: 0.35 mm — Slightly higher to improve adhesion.
9.cLine Widths (all): 0.8 mm — Matches nozzle diameter for consistent extrusion.10. Seam Settings
10.aSeam Position: Aligned or Back — Use aligned for mechanical consistency, back for visual appeal.
10.bSmart Scarf Seam: ON — Automatically adjusts seam location to reduce visual impact.
10.cSeam Angle: 155° — Standard seam angle for clean transitions.
10.dSeam Steps: 10 — Smooths seam path and improves visual finish.11. Infill Settings
11.aWall/Infill Overlap: 10% — Prevents infill from deforming soft exterior walls.
11.bInfill Combination: ON — Consolidates paths for efficiency.
11.cDetect Floating Shells: ON — Ensures unsupported vertical structures are printed reliably.
11.dSparse Infill Density: 20–25% — Balanced rigidity vs. material use.
11.eSparse Pattern: Grid — Stable and efficient for flexible geometries.12. Speed Settings
12.aTravel: 160 mm/s — Fast but safe against backlash.
12.bInitial Layer: 15 mm/s — Prevents nozzle from skimming and ensures bed adhesion.
12.cOuter Wall: 60 mm/s — Controlled speed for surface quality.
12.dInner Wall: 90 mm/s — Slightly faster without compromising control.
12.eSmall Perimeter: 35 mm/s — Reduced speed for detailed geometry.
12.fTop Surface: 40 mm/s — Improves finish on topmost layers.
12.gInfill: 100–120 mm/s — Takes advantage of high flowability.13. Acceleration Settings
13.aNormal Print: 2000 mm/s² — Prevents ringing in soft filaments.
13.bTravel: 4000 mm/s² — Enables fast movement without harsh transitions.
13.cInitial Layer: 300 mm/s² — Gentle movement prevents lifting from the bed.
13.dOuter Wall: 1500 mm/s² — Improves outer surface clarity.
13.eInner Wall: 2000 mm/s² — Balanced for structural components.
13.fTop Surface: 1500 mm/s² — Ensures smooth detailing.14. Adhesion and Brims
14.aSkirt Loops: 2 — Helps prime nozzle and start cleanly.
14.bBrim Width: 6 mm — Helps hold soft materials down.
14.cBrim Gap: 0.15 mm — Allows for easy removal without tearing.15. Prime Tower and Flush Settings
15.aPrime Tower: ON — Purges moisture and early flow inconsistencies.
15.bTower Width: 40 mm — Prevents collapse due to heat.
15.cBrim Width (Tower): 4 mm — Adds stability to the purge base.
15.dFlush Into Support: ON — Discards unwanted early flow safely.16. G-Code Start Script
M900 K0.05 ; Pressure Advance M106 S0 ; Fan off G92 E0 G1 E15 F300 ; purge line G92 E0
17. Additional Notes
17.aDry filament at 100°C for 2 hours before use.
17.bStore with desiccant.
17.cKeep extruder door open to allow vapor to escape.
17.dAvoid long dwell times at high temperatures.If you need print settings for other nozzle sizes, feel free to reach out to us at timeplast@timeplast.com — we’ll be happy to help.
Free U.S. standard shipping on orders of 5+ spools!
Custom colors for 5+ same-type spools’ orders
Passive
Slow timed 4D filament
-
TimeMass Passive by Timeplast is a specialized 3D printing filament designed to be highly durable, stable, and resistant to external environmental factors. Unlike Time-Mass Active (which degrades over time) or TimeMass Fire (which is designed to burn), TimeMass Passive is engineered for long-term structural integrity, making it ideal for applications that require strength, longevity, and resistance to wear.
Key Features of TimeMass Passive:
Highly Durable – Designed to last for extended periods without significant degradation.
Resistant to Environmental Factors – Protects against moisture, UV exposure, and oxidation.
Structurally Strong – Can be used in applications requiring mechanical stability.
Sustainable & Non-Toxic – Developed with eco-friendly material science principles.
Dimensional Stability – Maintains its form and function over time without warping or breaking down.
Why TimeMass Passive?
Timeplast designed TimeMass Passive as a material solution for industries and consumers needing durability without excessive waste. While many materials either degrade too quickly or persist indefinitely as pollutants, TimeMass Passive offers a balance—lasting as long as needed while remaining eco-conscious.
Need Ideas? Here You Go:
1. Long-Lasting Consumer Goods
Durable home decor and furniture components.
Weather-resistant outdoor accessories.
Sustainable, long-term-use kitchenware.
2. Industrial & Engineering Applications
Structural parts for 3D-printed machinery or tools.
Corrosion-resistant components for marine or aerospace applications.
Long-lasting prototypes for product development.
3. Infrastructure & Construction
3D-printed building materials that withstand the elements.
Durable interlocking tiles or modular structures.
Architectural elements requiring longevity.
4. Medical & Safety Equipment
Hygienic and long-lasting prosthetic components.
Non-degradable medical tools or diagnostic equipment.
Protective casings for sensitive instruments.
5. Automotive & Aerospace Applications
Heat and pressure-resistant vehicle components.
Protective covers for electronic and mechanical systems.
Long-term-use parts for sustainable transport solutions.
-
Click here to access our specialized TimeMass GPT Assistant.Just tell it your printer model and the TimeMass filament you're using—it will instantly recommend the exact parameters you need to start printing successfully.
Using a Bambu Lab printer?
Click here to download our updated Bambu Lab profile. All printing parameters are fully optimized and tested—just load the file and start printing.1. Introduction
This is the printing guide for TimeMass Passive filament as tested on the Bambu Labs A1. This filament features extremely low moisture exchange, high structural stiffness, and requires higher thermal energy for optimal melt and flow.Because TimeMass Passive releases minimal vapor but has high melt resistance and moderate elasticity, these profiles focus on thermal force management, mechanical flow stability, and precise extrusion tuning.
If the print is not being successful, please lower the nozzle temperature by 10°C and start over until an optimal print is achieved.2. Temperature Settings (All Nozzles)
2.a 0.2 mm Nozzle — Nozzle Temp: 235°C | Bed Temp: 70°C — High energy needed to soften the matrix
2.b 0.4 mm Nozzle — Nozzle Temp: 245°C | Bed Temp: 70°C — Better melt performance through standard nozzle size
2.c 0.6 mm Nozzle — Nozzle Temp: 250°C | Bed Temp: 70°C — Elevated flow demand for thick lines
2.d 0.8 mm Nozzle — Nozzle Temp: 255°C | Bed Temp: 70°C — Necessary thermal energy to prevent partial fusion at large diameterNote: Heatsink fans must remain consistent. Bed adhesion improves with light glue stick.
3. Cooling Settings (All Nozzles)
3.a No Cooling for First Layers: 2 — Less needed due to stiffer filament body
3.b Fan Minimum Speed: 20% at 50 seconds — Starts cooling sooner to shape rigid geometry
3.c Fan Maximum Speed: 25% — Supports layer definition without cracking
3.d Keep Fan Always On: ON — Essential for shaping passive structure
3.e Force Cooling Overhangs: ON — Encourages clean bridges for long spans
3.f Fan for Overhangs: 25–35% — Passive holds angles well, supports sharper fan controlNote: Timeplast Passive benefits from continuous airflow and structured cooling logic.
4. Max Volumetric Flow
4.a 0.2 mm Nozzle — Max Flow: 2 mm³/s — High-viscosity structure needs conservative flow
4.b 0.4 mm Nozzle — Max Flow: 5 mm³/s — Standard flow, safe and precise for rigid plastic
4.c 0.6 mm Nozzle — Max Flow: 9 mm³/s — Accommodates increased demand for high-mass lines
4.d 0.8 mm Nozzle — Max Flow: 13 mm³/s — Delivers clean, full-fused thick walls5. Retraction & Pressure Advance
5.a 0.2 mm Nozzle — Retraction: 1.0 mm @ 25 mm/s | Pressure Advance: 0.03
5.b 0.4 mm Nozzle — Retraction: 0.8 mm @ 20 mm/s | Pressure Advance: 0.04
5.c 0.6 mm Nozzle — Retraction: 0.6 mm @ 18 mm/s | Pressure Advance: 0.045
5.d 0.8 mm Nozzle — Retraction: 0.5 mm @ 15 mm/s | Pressure Advance: 0.05Note: Low moisture = less stringing, but retraction is still key for clean transitions.
6. Layer Height and Line Width
6.a 0.2 mm — Layer Height: 0.12 mm | Initial: 0.18 mm | Line Width: 0.25 mm
6.b 0.4 mm — Layer Height: 0.2 mm | Initial: 0.22 mm | Line Width: 0.42 mm
6.c 0.6 mm — Layer Height: 0.3 mm | Initial: 0.32 mm | Line Width: 0.6 mm
6.d 0.8 mm — Layer Height: 0.3 mm | Initial: 0.35 mm | Line Width: 0.8 mmNote: Clean lines support Timeplast Passive’s structural stiffness.
7. Wall, Shell & Infill Settings
7.a Wall Loops — 0.2 mm: 3 | 0.4 mm: 2–3 | 0.6 mm: 2 | 0.8 mm: 2
7.b Top/Bottom Shells — 0.2 mm & 0.4 mm: 4 | 0.6 mm & 0.8 mm: 3
7.c Top/Bottom Thickness — All: 1.2 mm (except 0.2 mm at 1 mm)
7.d Sparse Infill Density — 0.2 mm: 25% | 0.4 mm: 20–25% | 0.6 & 0.8 mm: 15–20%Note: Strong shells help support high stiffness and dimensional precision.
8. Speed & Acceleration
8.a Travel Speed — 0.2 mm: 120 mm/s | 0.4 mm: 140 mm/s | 0.6 mm: 150 mm/s | 0.8 mm: 160 mm/s
8.b Outer Wall Speed — 35 / 45 / 55 / 65 mm/s (increasing by nozzle size)
8.c Infill Speed — 70 / 100 / 120 / 130 mm/s
8.d Acceleration (Print) — 1200 / 1800 / 2200 / 2400 mm/s²
8.e Acceleration (Travel) — 3000 / 3500 / 4000 / 4500 mm/s²Note: Passive resists flex — high-speed print motion is safe and reliable.
9. Adhesion & Brims
9.a Skirt Loops: 1–2 — Clears dense first-line flow
9.b Brim Width: 5 mm — Secures stiffer corners to plate
9.c Brim Gap: 0.15 mm — Moderate release force to match rigidity10. Flush, Prime & G-code
10.a Prime Tower: Optional — Low moisture means less need for purging10.b Start G-code:
M900 K[PA] ; Pressure Advance M106 S0 ; Fan off G92 E0 G1 E15 F300 ; purge line G92 E0
Replace [PA] with the appropriate pressure advance value for your nozzle size.
11. Parameters That Stay Consistent Across All Nozzles
11.a Bed temperature: 70°C
11.b Seam logic and arc fitting: ON
11.c Retraction smoothing: Enabled
11.d Cooling delay: 2–3 layers
11.e Compatible with all standard Bambu Lab slicer toolsIf you need print settings for other nozzle sizes or any other assistance, feel free to reach out to us anytime at timeplast@timeplast.com — we’ll be happy to help.
Free U.S. standard shipping on orders of 5+ spools!
Custom colors for 5+ same-type spools’ orders
Fishing Kit
Fish Food
-
A protein-rich, interactive filament made from shrimp meal, fish meal, earthworm powder, and spirulina. This is more than food—it's enrichment. Print mini prey-like structures your fish will explore and nibble on over time.
Feed. Play. Repeat.
How it works:
Bioavailable proteins and marine vitamins are embedded within a low-leach matrix that softens underwater, triggering interest and gradual release.
It’s enrichment disguised as nutrition.
Nutrient Composition (per 350g spool):
Fish & Shrimp Meal: 20 g – Rich in omega-3s
Spirulina & Earthworms: 15 g – For immunity and digestion
Vitamin Mix: 5 g – A, D3, B-complex
Where to use it:
Aquarium toys – Print fish- or squid-shaped items for slow feeding
Breeder tanks – Enrichment for bettas, cichlids, and other active fish
Decorative feeders – Combine style and sustenance
Education kits – Demonstrate animal behavior and nutrition in action.
-
Click here to access our specialized TimeMass GPT Assistant. Just tell it your printer model and the TimeMass filament you're using—it will instantly recommend the exact parameters you need to start printing successfully.
Using a Bambu Lab printer?
Click here to download our updated Bambu Lab profile. All printing parameters are fully optimized and tested—just load the file and start printing.1. Introduction
These parameters are designed to help avoid printing issues; however, temperatures and speed timings can be adjusted based on your specific goals. For example, if you prefer a less rigid result, we recommend using a lower temperature. This section outlines a complete slicing and printing profile for TimeMass Fish Food, tailored for printers with a 0.8 mm nozzle. If the print is not being successful, please lower the nozzle temperature by 10°C and start over until an optimal print is achieved. While these examples were printed with a 0.8 mm nozzle, TimeMass can be used with any nozzle size. Please check the manual for printing parameters with all the other nozzle sizes.2. Temperature Settings
2.aNozzle Temperature: 240°C — Optimal for flowability while avoiding decomposition (which begins around 250°C).
2.bBed Temperature: 95°C — Ensures strong first-layer adhesion and prevents moisture bubbling.
2.cNozzle Temperature Range: 230–245°C — Timeplast melts around 165°C but prints best at 240°C for precise viscosity control.3. Cooling Settings
3.aNo Cooling for First Layers: 3 layers — Prevents shrinkage due to rapid cooling of moisture-rich filament.
3.bFan Minimum Speed: 0% for the first 100 seconds — Allows heat retention during early layers.
3.cFan Maximum Speed: 15% starting at 8 seconds — Avoids overcooling that can lead to warping.
3.dKeep Fan Always On: OFF — Allows vapor to escape and avoids internal fogging.
3.eSlow Down for Cooling: ON — Improves surface finish with controlled cooling.
3.fForce Cooling for Overhangs: OFF — Overcooling can deform bridges in Timeplast.
3.gFan for Overhangs: 15% — Only for essential cooling in complex areas.
3.hPre-Start Fan Time: 2 seconds — Minimizes pressure differential during the first layer.4. Volumetric Flow
4.aMax Volumetric Speed: 12 mm³/s — Based on a melt flow index of ~15 g/10min, allows high-speed printing.
4.bRamming Speed: 3 mm³/s — Prevents bubbles or popping from pressure spikes.5. Retraction and Flow
5.aRetraction Distance: 0.4 mm — Minimal retraction required for soft filaments to avoid stringing.
5.bRetraction Speed: 15 mm/s — Slow enough to avoid pulling molten plastic.
5.cPressure Advance: 0.05 — Compensates for nozzle lag at high flow rates.
5.dFlow Ratio: 92% — Slight under-extrusion avoids swelling and surface artifacts.6. Precision Settings
6.aGap Closing Radius: 0.1 mm — Tolerant of gaps in thicker walls.
6.bArc Fitting: ON — Reduces G-code size and smooths curve transitions.
6.cElephant Foot Compensation: 0.1 mm — Offsets squishing in the first layer caused by large bead sizes.7. Walls and Shells
7.aWall Loops: 2 — Minimum for strength when using a 0.8 mm nozzle.
7.bDetect Thin Walls: ON — Ensures tight geometries aren’t skipped.
7.cTop/Bottom Shell Layers: 3 — Provides good coverage; increase if watertightness is needed.
7.dTop/Bottom Thickness: 1.2 mm — Equals 1.5x the nozzle size for solid strength.
7.eTop/Bottom Pattern: Monotonic — Distributes tension evenly and improves surface finish.8. Geometry and Movement
8.aWall Order: Inner before Outer — Creates cleaner outer surfaces.
8.bInfill First: OFF — Maintains precise outer dimensions.
8.cSmooth Speed Transition: ON — Prevents ringing caused by abrupt speed changes.
8.dSmooth Coefficient: 80 — Ideal damping for soft materials.
8.eAvoid Crossing Wall: ON — Minimizes stringing across part walls.
8.fMax Detour for Crossing: 10 mm or 5% — Balances time with print cleanliness.9. Layer and Width Settings
9.aLayer Height: 0.3 mm — Optimal for strength and resolution using a 0.8 mm nozzle.
9.bInitial Layer Height: 0.35 mm — Slightly higher to improve adhesion.
9.cLine Widths (all): 0.8 mm — Matches nozzle diameter for consistent extrusion.10. Seam Settings
10.aSeam Position: Aligned or Back — Use aligned for mechanical consistency, back for visual appeal.
10.bSmart Scarf Seam: ON — Automatically adjusts seam location to reduce visual impact.
10.cSeam Angle: 155° — Standard seam angle for clean transitions.
10.dSeam Steps: 10 — Smooths seam path and improves visual finish.11. Infill Settings
11.aWall/Infill Overlap: 10% — Prevents infill from deforming soft exterior walls.
11.bInfill Combination: ON — Consolidates paths for efficiency.
11.cDetect Floating Shells: ON — Ensures unsupported vertical structures are printed reliably.
11.dSparse Infill Density: 20–25% — Balanced rigidity vs. material use.
11.eSparse Pattern: Grid — Stable and efficient for flexible geometries.12. Speed Settings
12.aTravel: 160 mm/s — Fast but safe against backlash.
12.bInitial Layer: 15 mm/s — Prevents nozzle from skimming and ensures bed adhesion.
12.cOuter Wall: 60 mm/s — Controlled speed for surface quality.
12.dInner Wall: 90 mm/s — Slightly faster without compromising control.
12.eSmall Perimeter: 35 mm/s — Reduced speed for detailed geometry.
12.fTop Surface: 40 mm/s — Improves finish on topmost layers.
12.gInfill: 100–120 mm/s — Takes advantage of high flowability.13. Acceleration Settings
13.aNormal Print: 2000 mm/s² — Prevents ringing in soft filaments.
13.bTravel: 4000 mm/s² — Enables fast movement without harsh transitions.
13.cInitial Layer: 300 mm/s² — Gentle movement prevents lifting from the bed.
13.dOuter Wall: 1500 mm/s² — Improves outer surface clarity.
13.eInner Wall: 2000 mm/s² — Balanced for structural components.
13.fTop Surface: 1500 mm/s² — Ensures smooth detailing.14. Adhesion and Brims
14.aSkirt Loops: 2 — Helps prime nozzle and start cleanly.
14.bBrim Width: 6 mm — Helps hold soft materials down.
14.cBrim Gap: 0.15 mm — Allows for easy removal without tearing.15. Prime Tower and Flush Settings
15.aPrime Tower: ON — Purges moisture and early flow inconsistencies.
15.bTower Width: 40 mm — Prevents collapse due to heat.
15.cBrim Width (Tower): 4 mm — Adds stability to the purge base.
15.dFlush Into Support: ON — Discards unwanted early flow safely.16. G-Code Start Script
M900 K0.05 ; Pressure Advance M106 S0 ; Fan off G92 E0 G1 E15 F300 ; purge line G92 E0
17. Additional Notes
17.aDry filament at 100°C for 2 hours before use.
17.bStore with desiccant.
17.cKeep extruder door open to allow vapor to escape.
17.dAvoid long dwell times at high temperatures.If you need print settings for other nozzle sizes, feel free to reach out to us at timeplast@timeplast.com — we’ll be happy to help.
You can also get instant support through our dedicated ChatGPT assistant here:https://chatgpt.com/g/g-6823924241cc8191bbabcf0bc6523e3f-timemass-4d-printing🚀
Free U.S. standard shipping on orders of 5+ spools!
Custom colors for 5+ same-type spools’ orders
Coral Food
-
Crafted for reef-building organisms, this filament contains a precise blend of phytoplankton, zooplankton, and organic matter—formulated to release slowly in marine systems without overwhelming your tank chemistry.
3D-printed nourishment for vibrant corals.
How it works:
Timeplast’s gentle encapsulation process protects thermally sensitive ingredients, ensuring coral-friendly nutrients survive extrusion and dissolve on cue.
Stable. Targeted. Coral-safe.
Food Matrix Includes:
Phytoplankton: 22 g – Stimulates soft coral growth
Zooplankton: 16 g – Provides protein for hard corals
Organic marine matter: 8 g – Feeds filter feeders and boosts biodiversity
Where to use it:
Reef aquariums – Print food-releasing rocks or domes
Coral nurseries – Support growth with minimal water impact
Research labs – Controlled delivery of coral diets
DIY enthusiasts – Make coral feeders with specific profiles
-
Click here to access our specialized TimeMass GPT Assistant. Just tell it your printer model and the TimeMass filament you're using—it will instantly recommend the exact parameters you need to start printing successfully.
Using a Bambu Lab printer?
Click here to download our updated Bambu Lab profile. All printing parameters are fully optimized and tested—just load the file and start printing.1. Introduction
These parameters are designed to help avoid printing issues; however, temperatures and speed timings can be adjusted based on your specific goals. For example, if you prefer a less rigid result, we recommend using a lower temperature. This section outlines a complete slicing and printing profile for TimeMass Coral Food, tailored for printers with a 0.8 mm nozzle. If the print is not being successful, please lower the nozzle temperature by 10°C and start over until an optimal print is achieved. While these examples were printed with a 0.8 mm nozzle, TimeMass can be used with any nozzle size. Please check the manual for printing parameters with all the other nozzle sizes.2. Temperature Settings
2.aNozzle Temperature: 240°C — Optimal for flowability while avoiding decomposition (which begins around 250°C).
2.bBed Temperature: 95°C — Ensures strong first-layer adhesion and prevents moisture bubbling.
2.cNozzle Temperature Range: 230–245°C — Timeplast melts around 165°C but prints best at 240°C for precise viscosity control.3. Cooling Settings
3.aNo Cooling for First Layers: 3 layers — Prevents shrinkage due to rapid cooling of moisture-rich filament.
3.bFan Minimum Speed: 0% for the first 100 seconds — Allows heat retention during early layers.
3.cFan Maximum Speed: 15% starting at 8 seconds — Avoids overcooling that can lead to warping.
3.dKeep Fan Always On: OFF — Allows vapor to escape and avoids internal fogging.
3.eSlow Down for Cooling: ON — Improves surface finish with controlled cooling.
3.fForce Cooling for Overhangs: OFF — Overcooling can deform bridges in Timeplast.
3.gFan for Overhangs: 15% — Only for essential cooling in complex areas.
3.hPre-Start Fan Time: 2 seconds — Minimizes pressure differential during the first layer.4. Volumetric Flow
4.aMax Volumetric Speed: 12 mm³/s — Based on a melt flow index of ~15 g/10min, allows high-speed printing.
4.bRamming Speed: 3 mm³/s — Prevents bubbles or popping from pressure spikes.5. Retraction and Flow
5.aRetraction Distance: 0.4 mm — Minimal retraction required for soft filaments to avoid stringing.
5.bRetraction Speed: 15 mm/s — Slow enough to avoid pulling molten plastic.
5.cPressure Advance: 0.05 — Compensates for nozzle lag at high flow rates.
5.dFlow Ratio: 92% — Slight under-extrusion avoids swelling and surface artifacts.6. Precision Settings
6.aGap Closing Radius: 0.1 mm — Tolerant of gaps in thicker walls.
6.bArc Fitting: ON — Reduces G-code size and smooths curve transitions.
6.cElephant Foot Compensation: 0.1 mm — Offsets squishing in the first layer caused by large bead sizes.7. Walls and Shells
7.aWall Loops: 2 — Minimum for strength when using a 0.8 mm nozzle.
7.bDetect Thin Walls: ON — Ensures tight geometries aren’t skipped.
7.cTop/Bottom Shell Layers: 3 — Provides good coverage; increase if watertightness is needed.
7.dTop/Bottom Thickness: 1.2 mm — Equals 1.5x the nozzle size for solid strength.
7.eTop/Bottom Pattern: Monotonic — Distributes tension evenly and improves surface finish.8. Geometry and Movement
8.aWall Order: Inner before Outer — Creates cleaner outer surfaces.
8.bInfill First: OFF — Maintains precise outer dimensions.
8.cSmooth Speed Transition: ON — Prevents ringing caused by abrupt speed changes.
8.dSmooth Coefficient: 80 — Ideal damping for soft materials.
8.eAvoid Crossing Wall: ON — Minimizes stringing across part walls.
8.fMax Detour for Crossing: 10 mm or 5% — Balances time with print cleanliness.9. Layer and Width Settings
9.aLayer Height: 0.3 mm — Optimal for strength and resolution using a 0.8 mm nozzle.
9.bInitial Layer Height: 0.35 mm — Slightly higher to improve adhesion.
9.cLine Widths (all): 0.8 mm — Matches nozzle diameter for consistent extrusion.10. Seam Settings
10.aSeam Position: Aligned or Back — Use aligned for mechanical consistency, back for visual appeal.
10.bSmart Scarf Seam: ON — Automatically adjusts seam location to reduce visual impact.
10.cSeam Angle: 155° — Standard seam angle for clean transitions.
10.dSeam Steps: 10 — Smooths seam path and improves visual finish.11. Infill Settings
11.aWall/Infill Overlap: 10% — Prevents infill from deforming soft exterior walls.
11.bInfill Combination: ON — Consolidates paths for efficiency.
11.cDetect Floating Shells: ON — Ensures unsupported vertical structures are printed reliably.
11.dSparse Infill Density: 20–25% — Balanced rigidity vs. material use.
11.eSparse Pattern: Grid — Stable and efficient for flexible geometries.12. Speed Settings
12.aTravel: 160 mm/s — Fast but safe against backlash.
12.bInitial Layer: 15 mm/s — Prevents nozzle from skimming and ensures bed adhesion.
12.cOuter Wall: 60 mm/s — Controlled speed for surface quality.
12.dInner Wall: 90 mm/s — Slightly faster without compromising control.
12.eSmall Perimeter: 35 mm/s — Reduced speed for detailed geometry.
12.fTop Surface: 40 mm/s — Improves finish on topmost layers.
12.gInfill: 100–120 mm/s — Takes advantage of high flowability.13. Acceleration Settings
13.aNormal Print: 2000 mm/s² — Prevents ringing in soft filaments.
13.bTravel: 4000 mm/s² — Enables fast movement without harsh transitions.
13.cInitial Layer: 300 mm/s² — Gentle movement prevents lifting from the bed.
13.dOuter Wall: 1500 mm/s² — Improves outer surface clarity.
13.eInner Wall: 2000 mm/s² — Balanced for structural components.
13.fTop Surface: 1500 mm/s² — Ensures smooth detailing.14. Adhesion and Brims
14.aSkirt Loops: 2 — Helps prime nozzle and start cleanly.
14.bBrim Width: 6 mm — Helps hold soft materials down.
14.cBrim Gap: 0.15 mm — Allows for easy removal without tearing.15. Prime Tower and Flush Settings
15.aPrime Tower: ON — Purges moisture and early flow inconsistencies.
15.bTower Width: 40 mm — Prevents collapse due to heat.
15.cBrim Width (Tower): 4 mm — Adds stability to the purge base.
15.dFlush Into Support: ON — Discards unwanted early flow safely.16. G-Code Start Script
M900 K0.05 ; Pressure Advance M106 S0 ; Fan off G92 E0 G1 E15 F300 ; purge line G92 E0
17. Additional Notes
17.aDry filament at 100°C for 2 hours before use.
17.bStore with desiccant.
17.cKeep extruder door open to allow vapor to escape.
17.dAvoid long dwell times at high temperatures.If you need print settings for other nozzle sizes, feel free to reach out to us at timeplast@timeplast.com — we’ll be happy to help.
Free U.S. standard shipping on orders of 5+ spools!
Custom colors for 5+ same-type spools’ orders
Fish Bait
-
Water soluble, fish-attracting filament built to dissolve after one hour in water. Packed with worm, shrimp, squid, and fish meal, it tempts fish while reducing waste in the water. Ideal for recreational fishing or custom bait design.
Print. Cast. Catch. No mess left behind.
How it works:
Water exposure activates flavor molecules and starts softening the bait. Time-controlled dissolution ensures no environmental-impact disposal.
Bait it your way.
Core Ingredients:
Fish + Shrimp Meal: 15 g
Squid Powder + Worm Extract: 3 g
Marine-safe Binder: 25 g
Where to use it:
Fishing bait prototypes – Shape-specific lures
Retail baits – Sell your own 3D-printed bait line
Sustainable fishing – No plastic trash in rivers or lakes
-
Click here to access our specialized TimeMass GPT Assistant. Just tell it your printer model and the TimeMass filament you're using—it will instantly recommend the exact parameters you need to start printing successfully.
Using a Bambu Lab printer?
Click here to download our updated Bambu Lab profile. All printing parameters are fully optimized and tested—just load the file and start printing.1. Introduction
These parameters are designed to help avoid printing issues; however, temperatures and speed timings can be adjusted based on your specific goals. For example, if you prefer a less rigid result, we recommend using a lower temperature. This section outlines a complete slicing and printing profile for TimeMass Fish Bait, tailored for printers with a 0.8 mm nozzle. If the print is not being successful, please lower the nozzle temperature by 10°C and start over until an optimal print is achieved. While these examples were printed with a 0.8 mm nozzle, TimeMass can be used with any nozzle size. Please check the manual for printing parameters with all the other nozzle sizes.2. Temperature Settings
2.aNozzle Temperature: 240°C — Optimal for flowability while avoiding decomposition (which begins around 250°C).
2.bBed Temperature: 95°C — Ensures strong first-layer adhesion and prevents moisture bubbling.
2.cNozzle Temperature Range: 230–245°C — Timeplast melts around 165°C but prints best at 240°C for precise viscosity control.3. Cooling Settings
3.aNo Cooling for First Layers: 3 layers — Prevents shrinkage due to rapid cooling of moisture-rich filament.
3.bFan Minimum Speed: 0% for the first 100 seconds — Allows heat retention during early layers.
3.cFan Maximum Speed: 15% starting at 8 seconds — Avoids overcooling that can lead to warping.
3.dKeep Fan Always On: OFF — Allows vapor to escape and avoids internal fogging.
3.eSlow Down for Cooling: ON — Improves surface finish with controlled cooling.
3.fForce Cooling for Overhangs: OFF — Overcooling can deform bridges in Timeplast.
3.gFan for Overhangs: 15% — Only for essential cooling in complex areas.
3.hPre-Start Fan Time: 2 seconds — Minimizes pressure differential during the first layer.4. Volumetric Flow
4.aMax Volumetric Speed: 12 mm³/s — Based on a melt flow index of ~15 g/10min, allows high-speed printing.
4.bRamming Speed: 3 mm³/s — Prevents bubbles or popping from pressure spikes.5. Retraction and Flow
5.aRetraction Distance: 0.4 mm — Minimal retraction required for soft filaments to avoid stringing.
5.bRetraction Speed: 15 mm/s — Slow enough to avoid pulling molten plastic.
5.cPressure Advance: 0.05 — Compensates for nozzle lag at high flow rates.
5.dFlow Ratio: 92% — Slight under-extrusion avoids swelling and surface artifacts.6. Precision Settings
6.aGap Closing Radius: 0.1 mm — Tolerant of gaps in thicker walls.
6.bArc Fitting: ON — Reduces G-code size and smooths curve transitions.
6.cElephant Foot Compensation: 0.1 mm — Offsets squishing in the first layer caused by large bead sizes.7. Walls and Shells
7.aWall Loops: 2 — Minimum for strength when using a 0.8 mm nozzle.
7.bDetect Thin Walls: ON — Ensures tight geometries aren’t skipped.
7.cTop/Bottom Shell Layers: 3 — Provides good coverage; increase if watertightness is needed.
7.dTop/Bottom Thickness: 1.2 mm — Equals 1.5x the nozzle size for solid strength.
7.eTop/Bottom Pattern: Monotonic — Distributes tension evenly and improves surface finish.8. Geometry and Movement
8.aWall Order: Inner before Outer — Creates cleaner outer surfaces.
8.bInfill First: OFF — Maintains precise outer dimensions.
8.cSmooth Speed Transition: ON — Prevents ringing caused by abrupt speed changes.
8.dSmooth Coefficient: 80 — Ideal damping for soft materials.
8.eAvoid Crossing Wall: ON — Minimizes stringing across part walls.
8.fMax Detour for Crossing: 10 mm or 5% — Balances time with print cleanliness.9. Layer and Width Settings
9.aLayer Height: 0.3 mm — Optimal for strength and resolution using a 0.8 mm nozzle.
9.bInitial Layer Height: 0.35 mm — Slightly higher to improve adhesion.
9.cLine Widths (all): 0.8 mm — Matches nozzle diameter for consistent extrusion.10. Seam Settings
10.aSeam Position: Aligned or Back — Use aligned for mechanical consistency, back for visual appeal.
10.bSmart Scarf Seam: ON — Automatically adjusts seam location to reduce visual impact.
10.cSeam Angle: 155° — Standard seam angle for clean transitions.
10.dSeam Steps: 10 — Smooths seam path and improves visual finish.11. Infill Settings
11.aWall/Infill Overlap: 10% — Prevents infill from deforming soft exterior walls.
11.bInfill Combination: ON — Consolidates paths for efficiency.
11.cDetect Floating Shells: ON — Ensures unsupported vertical structures are printed reliably.
11.dSparse Infill Density: 20–25% — Balanced rigidity vs. material use.
11.eSparse Pattern: Grid — Stable and efficient for flexible geometries.12. Speed Settings
12.aTravel: 160 mm/s — Fast but safe against backlash.
12.bInitial Layer: 15 mm/s — Prevents nozzle from skimming and ensures bed adhesion.
12.cOuter Wall: 60 mm/s — Controlled speed for surface quality.
12.dInner Wall: 90 mm/s — Slightly faster without compromising control.
12.eSmall Perimeter: 35 mm/s — Reduced speed for detailed geometry.
12.fTop Surface: 40 mm/s — Improves finish on topmost layers.
12.gInfill: 100–120 mm/s — Takes advantage of high flowability.13. Acceleration Settings
13.aNormal Print: 2000 mm/s² — Prevents ringing in soft filaments.
13.bTravel: 4000 mm/s² — Enables fast movement without harsh transitions.
13.cInitial Layer: 300 mm/s² — Gentle movement prevents lifting from the bed.
13.dOuter Wall: 1500 mm/s² — Improves outer surface clarity.
13.eInner Wall: 2000 mm/s² — Balanced for structural components.
13.fTop Surface: 1500 mm/s² — Ensures smooth detailing.14. Adhesion and Brims
14.aSkirt Loops: 2 — Helps prime nozzle and start cleanly.
14.bBrim Width: 6 mm — Helps hold soft materials down.
14.cBrim Gap: 0.15 mm — Allows for easy removal without tearing.15. Prime Tower and Flush Settings
15.aPrime Tower: ON — Purges moisture and early flow inconsistencies.
15.bTower Width: 40 mm — Prevents collapse due to heat.
15.cBrim Width (Tower): 4 mm — Adds stability to the purge base.
15.dFlush Into Support: ON — Discards unwanted early flow safely.16. G-Code Start Script
M900 K0.05 ; Pressure Advance M106 S0 ; Fan off G92 E0 G1 E15 F300 ; purge line G92 E0
17. Additional Notes
17.aDry filament at 100°C for 2 hours before use.
17.bStore with desiccant.
17.cKeep extruder door open to allow vapor to escape.
17.dAvoid long dwell times at high temperatures.If you need print settings for other nozzle sizes, feel free to reach out to us at timeplast@timeplast.com — we’ll be happy to help.
Free U.S. standard shipping on orders of 5+ spools!
Custom colors for 5+ same-type spools’ orders
Outdoor
Flex
-
TimeMass Flex is a TPU-like flexible filament developed by Timeplast that is also water-soluble. This unique combination allows for applications where maximum flexibility is needed, followed by controlled dissolution in water.
-
Click here to access our specialized TimeMass GPT Assistant. Just tell it your printer model and the TimeMass filament you're using—it will instantly recommend the exact parameters you need to start printing successfully.
Using a Bambu Lab printer?
Click here to download our updated Bambu Lab profile. All printing parameters are fully optimized and tested—just load the file and start printing.1. Introduction
These parameters are designed to help avoid printing issues; however, temperatures and speed timings can be adjusted based on your specific goals. For example, if you prefer a less rigid result, we recommend using a lower temperature. This section outlines a complete slicing and printing profile for TimeMass Flex, tailored for printers with a 0.8 mm nozzle. If the print is not being successful, please lower the nozzle temperature by 10°C and start over until an optimal print is achieved. While these examples were printed with a 0.8 mm nozzle, TimeMass can be used with any nozzle size. Please check the manual for printing parameters with all the other nozzle sizes.2. Temperature Settings
2.aNozzle Temperature: 240°C — Optimal for flowability while avoiding decomposition (which begins around 250°C).
2.bBed Temperature: 95°C — Ensures strong first-layer adhesion and prevents moisture bubbling.
2.cNozzle Temperature Range: 230–245°C — Timeplast melts around 165°C but prints best at 240°C for precise viscosity control.3. Cooling Settings
3.aNo Cooling for First Layers: 3 layers — Prevents shrinkage due to rapid cooling of moisture-rich filament.
3.bFan Minimum Speed: 0% for the first 100 seconds — Allows heat retention during early layers.
3.cFan Maximum Speed: 15% starting at 8 seconds — Avoids overcooling that can lead to warping.
3.dKeep Fan Always On: OFF — Allows vapor to escape and avoids internal fogging.
3.eSlow Down for Cooling: ON — Improves surface finish with controlled cooling.
3.fForce Cooling for Overhangs: OFF — Overcooling can deform bridges in Timeplast.
3.gFan for Overhangs: 15% — Only for essential cooling in complex areas.
3.hPre-Start Fan Time: 2 seconds — Minimizes pressure differential during the first layer.4. Volumetric Flow
4.aMax Volumetric Speed: 12 mm³/s — Based on a melt flow index of ~15 g/10min, allows high-speed printing.
4.bRamming Speed: 3 mm³/s — Prevents bubbles or popping from pressure spikes.5. Retraction and Flow
5.aRetraction Distance: 0.4 mm — Minimal retraction required for soft filaments to avoid stringing.
5.bRetraction Speed: 15 mm/s — Slow enough to avoid pulling molten plastic.
5.cPressure Advance: 0.05 — Compensates for nozzle lag at high flow rates.
5.dFlow Ratio: 92% — Slight under-extrusion avoids swelling and surface artifacts.6. Precision Settings
6.aGap Closing Radius: 0.1 mm — Tolerant of gaps in thicker walls.
6.bArc Fitting: ON — Reduces G-code size and smooths curve transitions.
6.cElephant Foot Compensation: 0.1 mm — Offsets squishing in the first layer caused by large bead sizes.7. Walls and Shells
7.aWall Loops: 2 — Minimum for strength when using a 0.8 mm nozzle.
7.bDetect Thin Walls: ON — Ensures tight geometries aren’t skipped.
7.cTop/Bottom Shell Layers: 3 — Provides good coverage; increase if watertightness is needed.
7.dTop/Bottom Thickness: 1.2 mm — Equals 1.5x the nozzle size for solid strength.
7.eTop/Bottom Pattern: Monotonic — Distributes tension evenly and improves surface finish.8. Geometry and Movement
8.aWall Order: Inner before Outer — Creates cleaner outer surfaces.
8.bInfill First: OFF — Maintains precise outer dimensions.
8.cSmooth Speed Transition: ON — Prevents ringing caused by abrupt speed changes.
8.dSmooth Coefficient: 80 — Ideal damping for soft materials.
8.eAvoid Crossing Wall: ON — Minimizes stringing across part walls.
8.fMax Detour for Crossing: 10 mm or 5% — Balances time with print cleanliness.9. Layer and Width Settings
9.aLayer Height: 0.3 mm — Optimal for strength and resolution using a 0.8 mm nozzle.
9.bInitial Layer Height: 0.35 mm — Slightly higher to improve adhesion.
9.cLine Widths (all): 0.8 mm — Matches nozzle diameter for consistent extrusion.10. Seam Settings
10.aSeam Position: Aligned or Back — Use aligned for mechanical consistency, back for visual appeal.
10.bSmart Scarf Seam: ON — Automatically adjusts seam location to reduce visual impact.
10.cSeam Angle: 155° — Standard seam angle for clean transitions.
10.dSeam Steps: 10 — Smooths seam path and improves visual finish.11. Infill Settings
11.aWall/Infill Overlap: 10% — Prevents infill from deforming soft exterior walls.
11.bInfill Combination: ON — Consolidates paths for efficiency.
11.cDetect Floating Shells: ON — Ensures unsupported vertical structures are printed reliably.
11.dSparse Infill Density: 20–25% — Balanced rigidity vs. material use.
11.eSparse Pattern: Grid — Stable and efficient for flexible geometries.12. Speed Settings
12.aTravel: 160 mm/s — Fast but safe against backlash.
12.bInitial Layer: 15 mm/s — Prevents nozzle from skimming and ensures bed adhesion.
12.cOuter Wall: 60 mm/s — Controlled speed for surface quality.
12.dInner Wall: 90 mm/s — Slightly faster without compromising control.
12.eSmall Perimeter: 35 mm/s — Reduced speed for detailed geometry.
12.fTop Surface: 40 mm/s — Improves finish on topmost layers.
12.gInfill: 100–120 mm/s — Takes advantage of high flowability.13. Acceleration Settings
13.aNormal Print: 2000 mm/s² — Prevents ringing in soft filaments.
13.bTravel: 4000 mm/s² — Enables fast movement without harsh transitions.
13.cInitial Layer: 300 mm/s² — Gentle movement prevents lifting from the bed.
13.dOuter Wall: 1500 mm/s² — Improves outer surface clarity.
13.eInner Wall: 2000 mm/s² — Balanced for structural components.
13.fTop Surface: 1500 mm/s² — Ensures smooth detailing.14. Adhesion and Brims
14.aSkirt Loops: 2 — Helps prime nozzle and start cleanly.
14.bBrim Width: 6 mm — Helps hold soft materials down.
14.cBrim Gap: 0.15 mm — Allows for easy removal without tearing.15. Prime Tower and Flush Settings
15.aPrime Tower: ON — Purges moisture and early flow inconsistencies.
15.bTower Width: 40 mm — Prevents collapse due to heat.
15.cBrim Width (Tower): 4 mm — Adds stability to the purge base.
15.dFlush Into Support: ON — Discards unwanted early flow safely.16. G-Code Start Script
M900 K0.05 ; Pressure Advance M106 S0 ; Fan off G92 E0 G1 E15 F300 ; purge line G92 E0
17. Additional Notes
17.aDry filament at 100°C for 2 hours before use.
17.bStore with desiccant.
17.cKeep extruder door open to allow vapor to escape.
17.dAvoid long dwell times at high temperatures.If you need print settings for other nozzle sizes, feel free to reach out to us at timeplast@timeplast.com — we’ll be happy to help.
Free U.S. standard shipping on orders of 5+ spools!
Custom colors for 5+ same-type spools’ orders
Ball
-
What if 3D-printed objects could bounce, stretch, and absorb impact like real rubber—without the weaknesses of traditional elastomers? TimeMass - Ball is a next-generation ultra-flexible, high-molecular-weight polymer filament, engineered to replicate the mechanical properties of rubber with superior resilience, printability, and long-term durability.
Unlike conventional rubber-like 3D printing filaments, which often suffer from poor elasticity recovery and weak layer adhesion, TimeMass - Ball leverages a specialized polymer structure with long-chain entanglements and high molecular cohesion. This unique formulation ensures exceptional bounce, impact absorption, and mechanical endurance—delivering true rubber-like performance with the reliability of advanced polymers.
Designed for Maximum Elasticity & Energy Efficiency
- Unrivaled Strain Recovery – Maintains high elasticity and rebounds efficiently, ensuring minimal permanent deformation even after repeated compression.
- Energy-Efficient Bounce – Engineered for dynamic response, allowing objects to store and release energy efficiently, mimicking the behavior of real rubber.
- Superior Layer Adhesion & Tear Resistance – Unlike other flexible filaments that delaminate or tear easily, TimeMass - Ball retains strong interlayer bonding, making it perfect for high-impact applications.Where Performance Meets Practicality
- Sporting Goods & High-Impact Prototypes – Print high-rebound balls, protective padding, and shock-absorbing components with unparalleled flexibility.
- Automotive & Robotics Applications – Develop durable vibration dampeners, soft grippers, or suspension elements that can withstand repeated stress.
- Toys, Games & Interactive Designs – Create durable, bouncy objects such as stress balls, fidget toys, or play equipment that can endure constant use.
- Wearable & Medical Innovations – Design pressure-distributing insoles, orthopedic supports, or flexible exoskeletons that adapt to movement without breaking down.
- Soft Robotics & Experimental Engineering – Use TimeMass - Ball to build responsive actuators, inflatable chambers, or shock-resistant casings for cutting-edge research.Revolutionizing Rubber-Like 3D Printing
By eliminating the weaknesses of standard elastomers, TimeMass - Ball enables new possibilities in sports, engineering, robotics, and beyond. Its ability to stretch, compress, and rebound dynamically makes it a game-changer for high-performance, flexible applications.
For those who demand precision, durability, and true rubber-like performance, TimeMass - Ball is the next evolution in flexible 3D printing.
Need Ideas? Here You Go:
Fully functional, airless sports balls, like basketballs and soccer balls, without the need for inflation.
Impact-resistant pads and bumpers for robotics, industrial machinery, or automotive components.
Vibration-dampening parts for mechanical or soundproofing applications.
Stress-relief and therapeutic squeeze balls for medical and wellness use.
Flexible grips, handles, and soft-touch surfacesfor ergonomic tools.
Advanced robotic actuators that require soft material interactions.
-
Click here to access our specialized TimeMass GPT Assistant. Just tell it your printer model and the TimeMass filament you're using—it will instantly recommend the exact parameters you need to start printing successfully.
Using a Bambu Lab printer?
Click here to download our updated Bambu Lab profile. All printing parameters are fully optimized and tested—just load the file and start printing.1. Introduction
These parameters are designed to help avoid printing issues; however, temperatures and speed timings can be adjusted based on your specific goals. For example, if you prefer a less rigid result, we recommend using a lower temperature. This section outlines a complete slicing and printing profile for TimeMass Ball, tailored for printers with a 0.8 mm nozzle. If the print is not being successful, please lower the nozzle temperature by 10°C and start over until an optimal print is achieved. While these examples were printed with a 0.8 mm nozzle, TimeMass can be used with any nozzle size. Please check the manual for printing parameters with all the other nozzle sizes.2. Temperature Settings
2.aNozzle Temperature: 240°C — Optimal for flowability while avoiding decomposition (which begins around 250°C).
2.bBed Temperature: 95°C — Ensures strong first-layer adhesion and prevents moisture bubbling.
2.cNozzle Temperature Range: 230–245°C — Timeplast melts around 165°C but prints best at 240°C for precise viscosity control.3. Cooling Settings
3.aNo Cooling for First Layers: 3 layers — Prevents shrinkage due to rapid cooling of moisture-rich filament.
3.bFan Minimum Speed: 0% for the first 100 seconds — Allows heat retention during early layers.
3.cFan Maximum Speed: 15% starting at 8 seconds — Avoids overcooling that can lead to warping.
3.dKeep Fan Always On: OFF — Allows vapor to escape and avoids internal fogging.
3.eSlow Down for Cooling: ON — Improves surface finish with controlled cooling.
3.fForce Cooling for Overhangs: OFF — Overcooling can deform bridges in Timeplast.
3.gFan for Overhangs: 15% — Only for essential cooling in complex areas.
3.hPre-Start Fan Time: 2 seconds — Minimizes pressure differential during the first layer.4. Volumetric Flow
4.aMax Volumetric Speed: 12 mm³/s — Based on a melt flow index of ~15 g/10min, allows high-speed printing.
4.bRamming Speed: 3 mm³/s — Prevents bubbles or popping from pressure spikes.5. Retraction and Flow
5.aRetraction Distance: 0.4 mm — Minimal retraction required for soft filaments to avoid stringing.
5.bRetraction Speed: 15 mm/s — Slow enough to avoid pulling molten plastic.
5.cPressure Advance: 0.05 — Compensates for nozzle lag at high flow rates.
5.dFlow Ratio: 92% — Slight under-extrusion avoids swelling and surface artifacts.6. Precision Settings
6.aGap Closing Radius: 0.1 mm — Tolerant of gaps in thicker walls.
6.bArc Fitting: ON — Reduces G-code size and smooths curve transitions.
6.cElephant Foot Compensation: 0.1 mm — Offsets squishing in the first layer caused by large bead sizes.7. Walls and Shells
7.aWall Loops: 2 — Minimum for strength when using a 0.8 mm nozzle.
7.bDetect Thin Walls: ON — Ensures tight geometries aren’t skipped.
7.cTop/Bottom Shell Layers: 3 — Provides good coverage; increase if watertightness is needed.
7.dTop/Bottom Thickness: 1.2 mm — Equals 1.5x the nozzle size for solid strength.
7.eTop/Bottom Pattern: Monotonic — Distributes tension evenly and improves surface finish.8. Geometry and Movement
8.aWall Order: Inner before Outer — Creates cleaner outer surfaces.
8.bInfill First: OFF — Maintains precise outer dimensions.
8.cSmooth Speed Transition: ON — Prevents ringing caused by abrupt speed changes.
8.dSmooth Coefficient: 80 — Ideal damping for soft materials.
8.eAvoid Crossing Wall: ON — Minimizes stringing across part walls.
8.fMax Detour for Crossing: 10 mm or 5% — Balances time with print cleanliness.9. Layer and Width Settings
9.aLayer Height: 0.3 mm — Optimal for strength and resolution using a 0.8 mm nozzle.
9.bInitial Layer Height: 0.35 mm — Slightly higher to improve adhesion.
9.cLine Widths (all): 0.8 mm — Matches nozzle diameter for consistent extrusion.10. Seam Settings
10.aSeam Position: Aligned or Back — Use aligned for mechanical consistency, back for visual appeal.
10.bSmart Scarf Seam: ON — Automatically adjusts seam location to reduce visual impact.
10.cSeam Angle: 155° — Standard seam angle for clean transitions.
10.dSeam Steps: 10 — Smooths seam path and improves visual finish.11. Infill Settings
11.aWall/Infill Overlap: 10% — Prevents infill from deforming soft exterior walls.
11.bInfill Combination: ON — Consolidates paths for efficiency.
11.cDetect Floating Shells: ON — Ensures unsupported vertical structures are printed reliably.
11.dSparse Infill Density: 20–25% — Balanced rigidity vs. material use.
11.eSparse Pattern: Grid — Stable and efficient for flexible geometries.12. Speed Settings
12.aTravel: 160 mm/s — Fast but safe against backlash.
12.bInitial Layer: 15 mm/s — Prevents nozzle from skimming and ensures bed adhesion.
12.cOuter Wall: 60 mm/s — Controlled speed for surface quality.
12.dInner Wall: 90 mm/s — Slightly faster without compromising control.
12.eSmall Perimeter: 35 mm/s — Reduced speed for detailed geometry.
12.fTop Surface: 40 mm/s — Improves finish on topmost layers.
12.gInfill: 100–120 mm/s — Takes advantage of high flowability.13. Acceleration Settings
13.aNormal Print: 2000 mm/s² — Prevents ringing in soft filaments.
13.bTravel: 4000 mm/s² — Enables fast movement without harsh transitions.
13.cInitial Layer: 300 mm/s² — Gentle movement prevents lifting from the bed.
13.dOuter Wall: 1500 mm/s² — Improves outer surface clarity.
13.eInner Wall: 2000 mm/s² — Balanced for structural components.
13.fTop Surface: 1500 mm/s² — Ensures smooth detailing.14. Adhesion and Brims
14.aSkirt Loops: 2 — Helps prime nozzle and start cleanly.
14.bBrim Width: 6 mm — Helps hold soft materials down.
14.cBrim Gap: 0.15 mm — Allows for easy removal without tearing.15. Prime Tower and Flush Settings
15.aPrime Tower: ON — Purges moisture and early flow inconsistencies.
15.bTower Width: 40 mm — Prevents collapse due to heat.
15.cBrim Width (Tower): 4 mm — Adds stability to the purge base.
15.dFlush Into Support: ON — Discards unwanted early flow safely.16. G-Code Start Script
M900 K0.05 ; Pressure Advance M106 S0 ; Fan off G92 E0 G1 E15 F300 ; purge line G92 E0
17. Additional Notes
17.aDry filament at 100°C for 2 hours before use.
17.bStore with desiccant.
17.cKeep extruder door open to allow vapor to escape.
17.dAvoid long dwell times at high temperatures.If you need print settings for other nozzle sizes, feel free to reach out to us at timeplast@timeplast.com — we’ll be happy to help.
Free U.S. standard shipping on orders of 5+ spools!
Custom colors for 5+ same-type spools’ orders
Wear
-
What if clothing could be printed to fit perfectly, adapt dynamically, and enhance functionality beyond anything traditional fabrics allow? TimeMass - Wear is a next-generation 4D printing filament, engineered for customized, high-performance wearables that move, flex, and breathe—all while maintaining exceptional durability and comfort.
Unlike traditional flexible filaments, TimeMass - Wear is designed with highly ordered molecular alignments, ensuring it remains strong, stretchable, and breathable under repeated stress. Whether used for clothing, accessories, or specialized gear, this filament represents the future of 3D-printed fashion and function.
Revolutionizing Wearables: Fashion Beyond Limits
Unprecedented Dress Designs – When combined with TimeMass Fiber, TimeMass - Wear unlocks revolutionary soft fabric-like structures, making it possible to print dresses the likes of which no one has ever seen before. Intricate patterns, seamless organic curves, and one-piece garments can now be created without the limitations of traditional sewing and stitching. Imagine flowing gowns with interwoven lattices, geometric sculptural forms, or self-supporting textile structures that could never be achieved with conventional materials.
Next-Level Suits for Any Purpose – Fashion is no longer just about aesthetics—TimeMass - Wear enables fully functional suits tailored for specific jobs, survival, and extreme conditions:
- Survivalist Suits – Glow in the dark, provide thermal insulation, float on water, and even integrate insect-repellent properties. Industrial & Job-Specific Gear – Design heat-resistant, impact-absorbing, or weatherproof suits tailored for construction, firefighting, or space exploration.
- Adaptive Uniforms – Military, first responders, and outdoor enthusiasts can wear multi-layered, intelligent fabrics that react dynamically to temperature, moisture, and movement.A Fusion of Fashion, Science & Utility
Hybrid Fabric-Texture Printing – When paired with TimeMass Fiber, TimeMass - Wear can mimic woven textiles, layered fabrics, and organic fiber patterns—merging the best qualities of traditional materials and futuristic design.
Breathable, Soft, Yet Ultra-Durable – Unlike rigid 3D-printed plastics, this filament is designed for comfort in motion, ensuring clothing is lightweight, flexible, and skin-friendly.
Sustainable, Waste-Free Manufacturing – Print on-demand apparel, accessories, and functional gear, eliminating fabric waste and pioneering a more circular, eco-friendly fashion industry.
Combining 4D Printing for Maximum Impact – When paired with other TimeMass filaments, wearable designs become even more multifunctional:
- TimeMass Glow & Reflect – Create self-illuminating safety wear for nighttime visibility.
- TimeMass Sublimation – Print temporary dissolvable designs that disappear on command.
- TimeMass Plant Vitamin – Integrate biodegradable, self-sustaining materials into garments that support nature and growth.A New Era of Wearable Design Begins
With TimeMass - Wear, fashion becomes more than fabric—it becomes an extension of the body, a tool for survival, and a limitless canvas for innovation.
For designers, engineers, and visionaries shaping the future, this filament unlocks possibilities never before imagined—from gravity-defying dresses to intelligent, multifunctional suits that adapt to their environment.
The future of wearables isn’t just smart—it’s printed.
Need Ideas? Here You Go:
Watch bands, wristbands, and wearable smart device accessories.
Adjustable, ergonomic footwear components, such as insoles or custom-fit straps.
Breathable, flexible clothing elements for cosplay, sportswear, or fashion.
High-impact protective gear, such as soft armor layers or reinforced gloves.
Integrated textile-print hybrid designs, mixing with TimeMass Fiber for fabric-like finishes.
Smart textiles with embedded sensors, leveraging conductivity-enhancing post-processing techniques.
-
Click here to access our specialized TimeMass GPT Assistant. Just tell it your printer model and the TimeMass filament you're using—it will instantly recommend the exact parameters you need to start printing successfully.
Using a Bambu Lab printer?
Click here to download our updated Bambu Lab profile. All printing parameters are fully optimized and tested—just load the file and start printing.1. Introduction
These parameters are designed to help avoid printing issues; however, temperatures and speed timings can be adjusted based on your specific goals. For example, if you prefer a less rigid result, we recommend using a lower temperature. This section outlines a complete slicing and printing profile for TimeMass Wear, tailored for printers with a 0.8 mm nozzle. If the print is not being successful, please lower the nozzle temperature by 10°C and start over until an optimal print is achieved.While these examples were printed with a 0.8 mm nozzle, TimeMass can be used with any nozzle size. Please check the manual for printing parameters with all the other nozzle sizes.2. Temperature Settings
2.aNozzle Temperature: 240°C — Optimal for flowability while avoiding decomposition (which begins around 250°C).
2.bBed Temperature: 95°C — Ensures strong first-layer adhesion and prevents moisture bubbling.
2.cNozzle Temperature Range: 230–245°C — Timeplast melts around 165°C but prints best at 240°C for precise viscosity control.3. Cooling Settings
3.aNo Cooling for First Layers: 3 layers — Prevents shrinkage due to rapid cooling of moisture-rich filament.
3.bFan Minimum Speed: 0% for the first 100 seconds — Allows heat retention during early layers.
3.cFan Maximum Speed: 15% starting at 8 seconds — Avoids overcooling that can lead to warping.
3.dKeep Fan Always On: OFF — Allows vapor to escape and avoids internal fogging.
3.eSlow Down for Cooling: ON — Improves surface finish with controlled cooling.
3.fForce Cooling for Overhangs: OFF — Overcooling can deform bridges in Timeplast.
3.gFan for Overhangs: 15% — Only for essential cooling in complex areas.
3.hPre-Start Fan Time: 2 seconds — Minimizes pressure differential during the first layer.4. Volumetric Flow
4.aMax Volumetric Speed: 12 mm³/s — Based on a melt flow index of ~15 g/10min, allows high-speed printing.
4.bRamming Speed: 3 mm³/s — Prevents bubbles or popping from pressure spikes.5. Retraction and Flow
5.aRetraction Distance: 0.4 mm — Minimal retraction required for soft filaments to avoid stringing.
5.bRetraction Speed: 15 mm/s — Slow enough to avoid pulling molten plastic.
5.cPressure Advance: 0.05 — Compensates for nozzle lag at high flow rates.
5.dFlow Ratio: 92% — Slight under-extrusion avoids swelling and surface artifacts.6. Precision Settings
6.aGap Closing Radius: 0.1 mm — Tolerant of gaps in thicker walls.
6.bArc Fitting: ON — Reduces G-code size and smooths curve transitions.
6.cElephant Foot Compensation: 0.1 mm — Offsets squishing in the first layer caused by large bead sizes.7. Walls and Shells
7.aWall Loops: 2 — Minimum for strength when using a 0.8 mm nozzle.
7.bDetect Thin Walls: ON — Ensures tight geometries aren’t skipped.
7.cTop/Bottom Shell Layers: 3 — Provides good coverage; increase if watertightness is needed.
7.dTop/Bottom Thickness: 1.2 mm — Equals 1.5x the nozzle size for solid strength.
7.eTop/Bottom Pattern: Monotonic — Distributes tension evenly and improves surface finish.8. Geometry and Movement
8.aWall Order: Inner before Outer — Creates cleaner outer surfaces.
8.bInfill First: OFF — Maintains precise outer dimensions.
8.cSmooth Speed Transition: ON — Prevents ringing caused by abrupt speed changes.
8.dSmooth Coefficient: 80 — Ideal damping for soft materials.
8.eAvoid Crossing Wall: ON — Minimizes stringing across part walls.
8.fMax Detour for Crossing: 10 mm or 5% — Balances time with print cleanliness.9. Layer and Width Settings
9.aLayer Height: 0.3 mm — Optimal for strength and resolution using a 0.8 mm nozzle.
9.bInitial Layer Height: 0.35 mm — Slightly higher to improve adhesion.
9.cLine Widths (all): 0.8 mm — Matches nozzle diameter for consistent extrusion.10. Seam Settings
10.aSeam Position: Aligned or Back — Use aligned for mechanical consistency, back for visual appeal.
10.bSmart Scarf Seam: ON — Automatically adjusts seam location to reduce visual impact.
10.cSeam Angle: 155° — Standard seam angle for clean transitions.
10.dSeam Steps: 10 — Smooths seam path and improves visual finish.11. Infill Settings
11.aWall/Infill Overlap: 10% — Prevents infill from deforming soft exterior walls.
11.bInfill Combination: ON — Consolidates paths for efficiency.
11.cDetect Floating Shells: ON — Ensures unsupported vertical structures are printed reliably.
11.dSparse Infill Density: 20–25% — Balanced rigidity vs. material use.
11.eSparse Pattern: Grid — Stable and efficient for flexible geometries.12. Speed Settings
12.aTravel: 160 mm/s — Fast but safe against backlash.
12.bInitial Layer: 15 mm/s — Prevents nozzle from skimming and ensures bed adhesion.
12.cOuter Wall: 60 mm/s — Controlled speed for surface quality.
12.dInner Wall: 90 mm/s — Slightly faster without compromising control.
12.eSmall Perimeter: 35 mm/s — Reduced speed for detailed geometry.
12.fTop Surface: 40 mm/s — Improves finish on topmost layers.
12.gInfill: 100–120 mm/s — Takes advantage of high flowability.13. Acceleration Settings
13.aNormal Print: 2000 mm/s² — Prevents ringing in soft filaments.
13.bTravel: 4000 mm/s² — Enables fast movement without harsh transitions.
13.cInitial Layer: 300 mm/s² — Gentle movement prevents lifting from the bed.
13.dOuter Wall: 1500 mm/s² — Improves outer surface clarity.
13.eInner Wall: 2000 mm/s² — Balanced for structural components.
13.fTop Surface: 1500 mm/s² — Ensures smooth detailing.14. Adhesion and Brims
14.aSkirt Loops: 2 — Helps prime nozzle and start cleanly.
14.bBrim Width: 6 mm — Helps hold soft materials down.
14.cBrim Gap: 0.15 mm — Allows for easy removal without tearing.15. Prime Tower and Flush Settings
15.aPrime Tower: ON — Purges moisture and early flow inconsistencies.
15.bTower Width: 40 mm — Prevents collapse due to heat.
15.cBrim Width (Tower): 4 mm — Adds stability to the purge base.
15.dFlush Into Support: ON — Discards unwanted early flow safely.16. G-Code Start Script
M900 K0.05 ; Pressure Advance M106 S0 ; Fan off G92 E0 G1 E15 F300 ; purge line G92 E0
17. Additional Notes
17.aDry filament at 100°C for 2 hours before use.
17.bStore with desiccant.
17.cKeep extruder door open to allow vapor to escape.
17.dAvoid long dwell times at high temperatures.If you need print settings for other nozzle sizes, feel free to reach out to us at timeplast@timeplast.com — we’ll be happy to help.
Free U.S. standard shipping on orders of 5+ spools!
Custom colors for 5+ same-type spools’ orders
Reflect & Glow
-
When it’s dark, you’ve got two options: disappear or glow like a legend.
TimeMass Reflect & Glow does both—glows in total darkness and reflects light straight back to the source when hit with headlights, flashlights, or whatever else is bouncing around out there.No batteries. No wires. Just light in, visibility out.
How it works:
Phosphorescent glow – Charges in ambient light and glows when the lights go out.
Microprism retroreflection – Reflects light directly back, so you stay visible from every angle. Like a cat’s eye, but printable.
If the glow fades? No problem. The reflection kicks in. You’re still seen. You’re still safe.
Where to use it:
Wearables – Jackets, helmets, bags—anything you want to keep visible on a night ride or rave.
Vehicles & roads – Print your own reflectors, emergency tags, or bumper warnings.
Camping gear – Tag your tent, tools, or that one zipper you always lose.
Home safety – Mark stairs, doors, or exit paths so they light up when you need them.
Creative chaos – Glowing art, hidden messages, nighttime signage... whatever weird glowing object you need in your life.
No charging cables. No nonsense.
Just a print that remembers the light and knows how to throw it back when it counts.Whether you're staying safe or just showing off, Reflect & Glow makes sure you're never left in the dark.
Need Ideas? Here You Go:
Wearable safety gear, such as jogging armbands and biking accessories.
Reflective road signs and trail markers for enhanced nighttime navigation.
Emergency equipment labels visible in low light and under direct illumination.
Glow-reactive sculptures and interactive designs.
-
Click here to access our specialized TimeMass GPT Assistant. Just tell it your printer model and the TimeMass filament you're using—it will instantly recommend the exact parameters you need to start printing successfully.
Using a Bambu Lab printer?
Click here to download our updated Bambu Lab profile. All printing parameters are fully optimized and tested—just load the file and start printing.1. Introduction
These parameters are designed to help avoid printing issues; however, temperatures and speed timings can be adjusted based on your specific goals. For example, if you prefer a less rigid result, we recommend using a lower temperature. This section outlines a complete slicing and printing profile for TimeMass Reflect & Glow, tailored for printers with a 0.8 mm nozzle. If the print is not being successful, please lower the nozzle temperature by 10°C and start over until an optimal print is achieved.While these examples were printed with a 0.8 mm nozzle, TimeMass can be used with any nozzle size. Please check the manual for printing parameters with all the other nozzle sizes.2. Temperature Settings
2.aNozzle Temperature: 240°C — Optimal for flowability while avoiding decomposition (which begins around 250°C).
2.bBed Temperature: 95°C — Ensures strong first-layer adhesion and prevents moisture bubbling.
2.cNozzle Temperature Range: 230–245°C — Timeplast melts around 165°C but prints best at 240°C for precise viscosity control.3. Cooling Settings
3.aNo Cooling for First Layers: 3 layers — Prevents shrinkage due to rapid cooling of moisture-rich filament.
3.bFan Minimum Speed: 0% for the first 100 seconds — Allows heat retention during early layers.
3.cFan Maximum Speed: 15% starting at 8 seconds — Avoids overcooling that can lead to warping.
3.dKeep Fan Always On: OFF — Allows vapor to escape and avoids internal fogging.
3.eSlow Down for Cooling: ON — Improves surface finish with controlled cooling.
3.fForce Cooling for Overhangs: OFF — Overcooling can deform bridges in Timeplast.
3.gFan for Overhangs: 15% — Only for essential cooling in complex areas.
3.hPre-Start Fan Time: 2 seconds — Minimizes pressure differential during the first layer.4. Volumetric Flow
4.aMax Volumetric Speed: 12 mm³/s — Based on a melt flow index of ~15 g/10min, allows high-speed printing.
4.bRamming Speed: 3 mm³/s — Prevents bubbles or popping from pressure spikes.5. Retraction and Flow
5.aRetraction Distance: 0.4 mm — Minimal retraction required for soft filaments to avoid stringing.
5.bRetraction Speed: 15 mm/s — Slow enough to avoid pulling molten plastic.
5.cPressure Advance: 0.05 — Compensates for nozzle lag at high flow rates.
5.dFlow Ratio: 92% — Slight under-extrusion avoids swelling and surface artifacts.6. Precision Settings
6.aGap Closing Radius: 0.1 mm — Tolerant of gaps in thicker walls.
6.bArc Fitting: ON — Reduces G-code size and smooths curve transitions.
6.cElephant Foot Compensation: 0.1 mm — Offsets squishing in the first layer caused by large bead sizes.7. Walls and Shells
7.aWall Loops: 2 — Minimum for strength when using a 0.8 mm nozzle.
7.bDetect Thin Walls: ON — Ensures tight geometries aren’t skipped.
7.cTop/Bottom Shell Layers: 3 — Provides good coverage; increase if watertightness is needed.
7.dTop/Bottom Thickness: 1.2 mm — Equals 1.5x the nozzle size for solid strength.
7.eTop/Bottom Pattern: Monotonic — Distributes tension evenly and improves surface finish.8. Geometry and Movement
8.aWall Order: Inner before Outer — Creates cleaner outer surfaces.
8.bInfill First: OFF — Maintains precise outer dimensions.
8.cSmooth Speed Transition: ON — Prevents ringing caused by abrupt speed changes.
8.dSmooth Coefficient: 80 — Ideal damping for soft materials.
8.eAvoid Crossing Wall: ON — Minimizes stringing across part walls.
8.fMax Detour for Crossing: 10 mm or 5% — Balances time with print cleanliness.9. Layer and Width Settings
9.aLayer Height: 0.3 mm — Optimal for strength and resolution using a 0.8 mm nozzle.
9.bInitial Layer Height: 0.35 mm — Slightly higher to improve adhesion.
9.cLine Widths (all): 0.8 mm — Matches nozzle diameter for consistent extrusion.10. Seam Settings
10.aSeam Position: Aligned or Back — Use aligned for mechanical consistency, back for visual appeal.
10.bSmart Scarf Seam: ON — Automatically adjusts seam location to reduce visual impact.
10.cSeam Angle: 155° — Standard seam angle for clean transitions.
10.dSeam Steps: 10 — Smooths seam path and improves visual finish.11. Infill Settings
11.aWall/Infill Overlap: 10% — Prevents infill from deforming soft exterior walls.
11.bInfill Combination: ON — Consolidates paths for efficiency.
11.cDetect Floating Shells: ON — Ensures unsupported vertical structures are printed reliably.
11.dSparse Infill Density: 20–25% — Balanced rigidity vs. material use.
11.eSparse Pattern: Grid — Stable and efficient for flexible geometries.12. Speed Settings
12.aTravel: 160 mm/s — Fast but safe against backlash.
12.bInitial Layer: 15 mm/s — Prevents nozzle from skimming and ensures bed adhesion.
12.cOuter Wall: 60 mm/s — Controlled speed for surface quality.
12.dInner Wall: 90 mm/s — Slightly faster without compromising control.
12.eSmall Perimeter: 35 mm/s — Reduced speed for detailed geometry.
12.fTop Surface: 40 mm/s — Improves finish on topmost layers.
12.gInfill: 100–120 mm/s — Takes advantage of high flowability.13. Acceleration Settings
13.aNormal Print: 2000 mm/s² — Prevents ringing in soft filaments.
13.bTravel: 4000 mm/s² — Enables fast movement without harsh transitions.
13.cInitial Layer: 300 mm/s² — Gentle movement prevents lifting from the bed.
13.dOuter Wall: 1500 mm/s² — Improves outer surface clarity.
13.eInner Wall: 2000 mm/s² — Balanced for structural components.
13.fTop Surface: 1500 mm/s² — Ensures smooth detailing.14. Adhesion and Brims
14.aSkirt Loops: 2 — Helps prime nozzle and start cleanly.
14.bBrim Width: 6 mm — Helps hold soft materials down.
14.cBrim Gap: 0.15 mm — Allows for easy removal without tearing.15. Prime Tower and Flush Settings
15.aPrime Tower: ON — Purges moisture and early flow inconsistencies.
15.bTower Width: 40 mm — Prevents collapse due to heat.
15.cBrim Width (Tower): 4 mm — Adds stability to the purge base.
15.dFlush Into Support: ON — Discards unwanted early flow safely.16. G-Code Start Script
M900 K0.05 ; Pressure Advance M106 S0 ; Fan off G92 E0 G1 E15 F300 ; purge line G92 E0
17. Additional Notes
17.aDry filament at 100°C for 2 hours before use.
17.bStore with desiccant.
17.cKeep extruder door open to allow vapor to escape.
17.dAvoid long dwell times at high temperatures.If you need print settings for other nozzle sizes, feel free to reach out to us at timeplast@timeplast.com — we’ll be happy to help.
Free U.S. standard shipping on orders of 5+ spools!
Custom colors for 5+ same-type spools’ orders
Smart Nutrition
Plant Vitamin - Gen 2
-
TimeMass Plant Vitamin is a water-retaining, nutrient-loaded filament engineered for slow-release fertilization right from the print bed. Built with carbon, nitrogen, phosphorus, and sulfur—plus structured water and calcium carbonate—it lets you 3D print objects that nourish plants over time.
No runoff. No burst-release. Just sustained growth, powered by smart material design.
How it works:
Hydrophilic matrix absorbs moisture and dissolves slowly, releasing nutrients in sync with plant needs.
Water = trigger – Pods can be printed to behave like analog biological computers, using moisture to time and deliver nutrient output.
No batteries. No sensors. Just physics.
Full Nutrient Breakdown (per 350g spool):
Nitrogen (N): 10.8 g – Chlorophyll production & leaf growth
Phosphate (P₂O₅): 8.4 g – Root development & flowering
Potash (K₂O): 6.8 g – Disease resistance & overall health
Calcium (Ca): 2.4 g – Cell wall structure & nutrient absorption
Magnesium (Mg): 0.8 g – Photosynthesis & enzyme function
Core Material:
Structured Water: 70% – Boosts solubility and uptake
Calcium Carbonate: 20% – Strengthens the filament and feeds the soil
Sustained Release Design:
Nutrients are embedded within the Timeplast Plus matrix for gradual delivery
Structured water ensures efficient solubility
No leaching = no waste
Stability & Vitamin Integrity (Because Growers Actually Care):
Microencapsulation – Heat-resistant shells (sol-gel silica, melamine, urea-formaldehyde, etc.) prevent degradation during extrusion.
Vitamin Derivatives – Stable precursors like ascorbyl palmitate reactivate in soil through pH, enzymes, or hydration.
Multi-phase Composite – Core-shell architecture keeps active components cool during print.
Low-shear, thermally controlled extrusion – Custom nozzles and low-friction channels reduce heat spikes.
Water-based integration – Vitamins are solvent-bound into low-temp meltable additives, preserving potency.
Where to use it:
Urban gardening & hydroponics – Print self-feeding seed pods, planters, or nutrient spikes
Precision agriculture – Design root-zone diffusers to boost yield without runoff
Reforestation – Print biodegradable seed capsules with long-term nutrient support
Irrigation aids & smart pots – Combine watering and feeding in one functional print
The result?
Printed structures that actually feed the soil. No over-fertilizing. No chemical waste. Just controlled, water-powered nutrient delivery—designed by you.Need Ideas? Here You Go:
Self-fertilizing plant pots and holders, eliminating the need for chemical fertilizers.
Water-dispersible nutrient discs that can be buried in soil for controlled nutrient release.
Eco-friendly seedling trays that break down naturally, enriching the soil.
Hydroponic nutrient carriers, improving plant growth in water-based systems.
Custom garden markers, serving both as labels and soil enhancers.
-
Click here to access our specialized TimeMass GPT Assistant. Just tell it your printer model and the TimeMass filament you're using—it will instantly recommend the exact parameters you need to start printing successfully.
Using a Bambu Lab printer?
Click here to download our updated Bambu Lab profile. All printing parameters are fully optimized and tested—just load the file and start printing.1. Introduction
These parameters are designed to help avoid printing issues; however, temperatures and speed timings can be adjusted based on your specific goals. For example, if you prefer a less rigid result, we recommend using a lower temperature. This section outlines a complete slicing and printing profile for TimeMass Plant Vitamin, tailored for printers with a 0.8 mm nozzle. If the print is not being successful, please lower the nozzle temperature by 10°C and start over until an optimal print is achieved. While these examples were printed with a 0.8 mm nozzle, TimeMass can be used with any nozzle size. Please check the manual for printing parameters with all the other nozzle sizes.2. Temperature Settings
2.aNozzle Temperature: 240°C — Optimal for flowability while avoiding decomposition (which begins around 250°C).
2.bBed Temperature: 95°C — Ensures strong first-layer adhesion and prevents moisture bubbling.
2.cNozzle Temperature Range: 230–245°C — Timeplast melts around 165°C but prints best at 240°C for precise viscosity control.3. Cooling Settings
3.aNo Cooling for First Layers: 3 layers — Prevents shrinkage due to rapid cooling of moisture-rich filament.
3.bFan Minimum Speed: 0% for the first 100 seconds — Allows heat retention during early layers.
3.cFan Maximum Speed: 15% starting at 8 seconds — Avoids overcooling that can lead to warping.
3.dKeep Fan Always On: OFF — Allows vapor to escape and avoids internal fogging.
3.eSlow Down for Cooling: ON — Improves surface finish with controlled cooling.
3.fForce Cooling for Overhangs: OFF — Overcooling can deform bridges in Timeplast.
3.gFan for Overhangs: 15% — Only for essential cooling in complex areas.
3.hPre-Start Fan Time: 2 seconds — Minimizes pressure differential during the first layer.4. Volumetric Flow
4.aMax Volumetric Speed: 12 mm³/s — Based on a melt flow index of ~15 g/10min, allows high-speed printing.
4.bRamming Speed: 3 mm³/s — Prevents bubbles or popping from pressure spikes.5. Retraction and Flow
5.aRetraction Distance: 0.4 mm — Minimal retraction required for soft filaments to avoid stringing.
5.bRetraction Speed: 15 mm/s — Slow enough to avoid pulling molten plastic.
5.cPressure Advance: 0.05 — Compensates for nozzle lag at high flow rates.
5.dFlow Ratio: 92% — Slight under-extrusion avoids swelling and surface artifacts.6. Precision Settings
6.aGap Closing Radius: 0.1 mm — Tolerant of gaps in thicker walls.
6.bArc Fitting: ON — Reduces G-code size and smooths curve transitions.
6.cElephant Foot Compensation: 0.1 mm — Offsets squishing in the first layer caused by large bead sizes.7. Walls and Shells
7.aWall Loops: 2 — Minimum for strength when using a 0.8 mm nozzle.
7.bDetect Thin Walls: ON — Ensures tight geometries aren’t skipped.
7.cTop/Bottom Shell Layers: 3 — Provides good coverage; increase if watertightness is needed.
7.dTop/Bottom Thickness: 1.2 mm — Equals 1.5x the nozzle size for solid strength.
7.eTop/Bottom Pattern: Monotonic — Distributes tension evenly and improves surface finish.8. Geometry and Movement
8.aWall Order: Inner before Outer — Creates cleaner outer surfaces.
8.bInfill First: OFF — Maintains precise outer dimensions.
8.cSmooth Speed Transition: ON — Prevents ringing caused by abrupt speed changes.
8.dSmooth Coefficient: 80 — Ideal damping for soft materials.
8.eAvoid Crossing Wall: ON — Minimizes stringing across part walls.
8.fMax Detour for Crossing: 10 mm or 5% — Balances time with print cleanliness.9. Layer and Width Settings
9.aLayer Height: 0.3 mm — Optimal for strength and resolution using a 0.8 mm nozzle.
9.bInitial Layer Height: 0.35 mm — Slightly higher to improve adhesion.
9.cLine Widths (all): 0.8 mm — Matches nozzle diameter for consistent extrusion.10. Seam Settings
10.aSeam Position: Aligned or Back — Use aligned for mechanical consistency, back for visual appeal.
10.bSmart Scarf Seam: ON — Automatically adjusts seam location to reduce visual impact.
10.cSeam Angle: 155° — Standard seam angle for clean transitions.
10.dSeam Steps: 10 — Smooths seam path and improves visual finish.11. Infill Settings
11.aWall/Infill Overlap: 10% — Prevents infill from deforming soft exterior walls.
11.bInfill Combination: ON — Consolidates paths for efficiency.
11.cDetect Floating Shells: ON — Ensures unsupported vertical structures are printed reliably.
11.dSparse Infill Density: 20–25% — Balanced rigidity vs. material use.
11.eSparse Pattern: Grid — Stable and efficient for flexible geometries.12. Speed Settings
12.aTravel: 160 mm/s — Fast but safe against backlash.
12.bInitial Layer: 15 mm/s — Prevents nozzle from skimming and ensures bed adhesion.
12.cOuter Wall: 60 mm/s — Controlled speed for surface quality.
12.dInner Wall: 90 mm/s — Slightly faster without compromising control.
12.eSmall Perimeter: 35 mm/s — Reduced speed for detailed geometry.
12.fTop Surface: 40 mm/s — Improves finish on topmost layers.
12.gInfill: 100–120 mm/s — Takes advantage of high flowability.13. Acceleration Settings
13.aNormal Print: 2000 mm/s² — Prevents ringing in soft filaments.
13.bTravel: 4000 mm/s² — Enables fast movement without harsh transitions.
13.cInitial Layer: 300 mm/s² — Gentle movement prevents lifting from the bed.
13.dOuter Wall: 1500 mm/s² — Improves outer surface clarity.
13.eInner Wall: 2000 mm/s² — Balanced for structural components.
13.fTop Surface: 1500 mm/s² — Ensures smooth detailing.14. Adhesion and Brims
14.aSkirt Loops: 2 — Helps prime nozzle and start cleanly.
14.bBrim Width: 6 mm — Helps hold soft materials down.
14.cBrim Gap: 0.15 mm — Allows for easy removal without tearing.15. Prime Tower and Flush Settings
15.aPrime Tower: ON — Purges moisture and early flow inconsistencies.
15.bTower Width: 40 mm — Prevents collapse due to heat.
15.cBrim Width (Tower): 4 mm — Adds stability to the purge base.
15.dFlush Into Support: ON — Discards unwanted early flow safely.16. G-Code Start Script
M900 K0.05 ; Pressure Advance M106 S0 ; Fan off G92 E0 G1 E15 F300 ; purge line G92 E0
17. Additional Notes
17.aDry filament at 100°C for 2 hours before use.
17.bStore with desiccant.
17.cKeep extruder door open to allow vapor to escape.
17.dAvoid long dwell times at high temperatures.If you need print settings for other nozzle sizes, feel free to reach out to us at timeplast@timeplast.com — we’ll be happy to help.
Free U.S. standard shipping on orders of 5+ spools!
Custom colors for 5+ same-type spools’ orders
Sugar
-
A water-activated, sweet-loaded filament ideal for biochemical triggers, insect farming, or experimental food-based prints. Releases glucose and sucrose in trace amounts over time.
Sweet science.
Where to use it:
Insect traps and feeders
Microbial growth experiments
Edutainment or biochemical test kits
-
Click here to access our specialized TimeMass GPT Assistant. Just tell it your printer model and the TimeMass filament you're using—it will instantly recommend the exact parameters you need to start printing successfully.
Using a Bambu Lab printer?
Click here to download our updated Bambu Lab profile. All printing parameters are fully optimized and tested—just load the file and start printing.1. Introduction
These parameters are designed to help avoid printing issues; however, temperatures and speed timings can be adjusted based on your specific goals. For example, if you prefer a less rigid result, we recommend using a lower temperature. This section outlines a complete slicing and printing profile for TimeMass Sugar, tailored for printers with a 0.8 mm nozzle. If the print is not being successful, please lower the nozzle temperature by 10°C and start over until an optimal print is achieved. While these examples were printed with a 0.8 mm nozzle, TimeMass can be used with any nozzle size. Please check the manual for printing parameters with all the other nozzle sizes.2. Temperature Settings
2.aNozzle Temperature: 240°C — Optimal for flowability while avoiding decomposition (which begins around 250°C).
2.bBed Temperature: 95°C — Ensures strong first-layer adhesion and prevents moisture bubbling.
2.cNozzle Temperature Range: 230–245°C — Timeplast melts around 165°C but prints best at 240°C for precise viscosity control.3. Cooling Settings
3.aNo Cooling for First Layers: 3 layers — Prevents shrinkage due to rapid cooling of moisture-rich filament.
3.bFan Minimum Speed: 0% for the first 100 seconds — Allows heat retention during early layers.
3.cFan Maximum Speed: 15% starting at 8 seconds — Avoids overcooling that can lead to warping.
3.dKeep Fan Always On: OFF — Allows vapor to escape and avoids internal fogging.
3.eSlow Down for Cooling: ON — Improves surface finish with controlled cooling.
3.fForce Cooling for Overhangs: OFF — Overcooling can deform bridges in Timeplast.
3.gFan for Overhangs: 15% — Only for essential cooling in complex areas.
3.hPre-Start Fan Time: 2 seconds — Minimizes pressure differential during the first layer.4. Volumetric Flow
4.aMax Volumetric Speed: 12 mm³/s — Based on a melt flow index of ~15 g/10min, allows high-speed printing.
4.bRamming Speed: 3 mm³/s — Prevents bubbles or popping from pressure spikes.5. Retraction and Flow
5.aRetraction Distance: 0.4 mm — Minimal retraction required for soft filaments to avoid stringing.
5.bRetraction Speed: 15 mm/s — Slow enough to avoid pulling molten plastic.
5.cPressure Advance: 0.05 — Compensates for nozzle lag at high flow rates.
5.dFlow Ratio: 92% — Slight under-extrusion avoids swelling and surface artifacts.6. Precision Settings
6.aGap Closing Radius: 0.1 mm — Tolerant of gaps in thicker walls.
6.bArc Fitting: ON — Reduces G-code size and smooths curve transitions.
6.cElephant Foot Compensation: 0.1 mm — Offsets squishing in the first layer caused by large bead sizes.7. Walls and Shells
7.aWall Loops: 2 — Minimum for strength when using a 0.8 mm nozzle.
7.bDetect Thin Walls: ON — Ensures tight geometries aren’t skipped.
7.cTop/Bottom Shell Layers: 3 — Provides good coverage; increase if watertightness is needed.
7.dTop/Bottom Thickness: 1.2 mm — Equals 1.5x the nozzle size for solid strength.
7.eTop/Bottom Pattern: Monotonic — Distributes tension evenly and improves surface finish.8. Geometry and Movement
8.aWall Order: Inner before Outer — Creates cleaner outer surfaces.
8.bInfill First: OFF — Maintains precise outer dimensions.
8.cSmooth Speed Transition: ON — Prevents ringing caused by abrupt speed changes.
8.dSmooth Coefficient: 80 — Ideal damping for soft materials.
8.eAvoid Crossing Wall: ON — Minimizes stringing across part walls.
8.fMax Detour for Crossing: 10 mm or 5% — Balances time with print cleanliness.9. Layer and Width Settings
9.aLayer Height: 0.3 mm — Optimal for strength and resolution using a 0.8 mm nozzle.
9.bInitial Layer Height: 0.35 mm — Slightly higher to improve adhesion.
9.cLine Widths (all): 0.8 mm — Matches nozzle diameter for consistent extrusion.10. Seam Settings
10.aSeam Position: Aligned or Back — Use aligned for mechanical consistency, back for visual appeal.
10.bSmart Scarf Seam: ON — Automatically adjusts seam location to reduce visual impact.
10.cSeam Angle: 155° — Standard seam angle for clean transitions.
10.dSeam Steps: 10 — Smooths seam path and improves visual finish.11. Infill Settings
11.aWall/Infill Overlap: 10% — Prevents infill from deforming soft exterior walls.
11.bInfill Combination: ON — Consolidates paths for efficiency.
11.cDetect Floating Shells: ON — Ensures unsupported vertical structures are printed reliably.
11.dSparse Infill Density: 20–25% — Balanced rigidity vs. material use.
11.eSparse Pattern: Grid — Stable and efficient for flexible geometries.12. Speed Settings
12.aTravel: 160 mm/s — Fast but safe against backlash.
12.bInitial Layer: 15 mm/s — Prevents nozzle from skimming and ensures bed adhesion.
12.cOuter Wall: 60 mm/s — Controlled speed for surface quality.
12.dInner Wall: 90 mm/s — Slightly faster without compromising control.
12.eSmall Perimeter: 35 mm/s — Reduced speed for detailed geometry.
12.fTop Surface: 40 mm/s — Improves finish on topmost layers.
12.gInfill: 100–120 mm/s — Takes advantage of high flowability.13. Acceleration Settings
13.aNormal Print: 2000 mm/s² — Prevents ringing in soft filaments.
13.bTravel: 4000 mm/s² — Enables fast movement without harsh transitions.
13.cInitial Layer: 300 mm/s² — Gentle movement prevents lifting from the bed.
13.dOuter Wall: 1500 mm/s² — Improves outer surface clarity.
13.eInner Wall: 2000 mm/s² — Balanced for structural components.
13.fTop Surface: 1500 mm/s² — Ensures smooth detailing.14. Adhesion and Brims
14.aSkirt Loops: 2 — Helps prime nozzle and start cleanly.
14.bBrim Width: 6 mm — Helps hold soft materials down.
14.cBrim Gap: 0.15 mm — Allows for easy removal without tearing.15. Prime Tower and Flush Settings
15.aPrime Tower: ON — Purges moisture and early flow inconsistencies.
15.bTower Width: 40 mm — Prevents collapse due to heat.
15.cBrim Width (Tower): 4 mm — Adds stability to the purge base.
15.dFlush Into Support: ON — Discards unwanted early flow safely.16. G-Code Start Script
M900 K0.05 ; Pressure Advance M106 S0 ; Fan off G92 E0 G1 E15 F300 ; purge line G92 E0
17. Additional Notes
17.aDry filament at 100°C for 2 hours before use.
17.bStore with desiccant.
17.cKeep extruder door open to allow vapor to escape.
17.dAvoid long dwell times at high temperatures.If you need print settings for other nozzle sizes, feel free to reach out to us at timeplast@timeplast.com — we’ll be happy to help.
Free U.S. standard shipping on orders of 5+ spools!
Custom colors for 5+ same-type spools’ orders
Cinnamon
-
This aromatic filament slowly releases real cinnamon—thanks to our water-encapsulation technology that protects and diffuses versatile compounds. Create interactive, scent-forward designs with a warm, spiced identity.
Scent meets function. And it’s all natural.
How it works:
Microencapsulated cinnamon oil and powder are protected during extrusion and slowly released as ambient moisture activates the surface.
Always fresh.
Core Material:
Encapsulated Cinnamon: 18% – Ground and oil blend stabilized via silica-gel shells
Structured water polymer: 82% – Enables consistent print quality and scent diffusion
Scent Design:
Gradual release for up to 6 months depending on exposure
Can be triggered faster in high humidity or warm air flow
Where to use it:
Home fragrance objects – Scented wall tiles, drawer inserts, or ornaments
Edutainment – Teach kids about aromatic molecules with interactive models
Event décor – Custom cinnamon-scented printables for holidays
Bug repellents – Print cinnamon-scented outdoor items (mosquitoes hate it!)
-
Click here to access our specialized TimeMass GPT Assistant. Just tell it your printer model and the TimeMass filament you're using—it will instantly recommend the exact parameters you need to start printing successfully.
Using a Bambu Lab printer?
Click here to download our updated Bambu Lab profile. All printing parameters are fully optimized and tested—just load the file and start printing.1. Introduction
These parameters are designed to help avoid printing issues; however, temperatures and speed timings can be adjusted based on your specific goals. For example, if you prefer a less rigid result, we recommend using a lower temperature. This section outlines a complete slicing and printing profile for TimeMass Cinnamon, tailored for printers with a 0.8 mm nozzle. If the print is not being successful, please lower the nozzle temperature by 10°C and start over until an optimal print is achieved. While these examples were printed with a 0.8 mm nozzle, TimeMass can be used with any nozzle size. Please check the manual for printing parameters with all the other nozzle sizes.2. Temperature Settings
2.aNozzle Temperature: 240°C — Optimal for flowability while avoiding decomposition (which begins around 250°C).
2.bBed Temperature: 95°C — Ensures strong first-layer adhesion and prevents moisture bubbling.
2.cNozzle Temperature Range: 230–245°C — Timeplast melts around 165°C but prints best at 240°C for precise viscosity control.3. Cooling Settings
3.aNo Cooling for First Layers: 3 layers — Prevents shrinkage due to rapid cooling of moisture-rich filament.
3.bFan Minimum Speed: 0% for the first 100 seconds — Allows heat retention during early layers.
3.cFan Maximum Speed: 15% starting at 8 seconds — Avoids overcooling that can lead to warping.
3.dKeep Fan Always On: OFF — Allows vapor to escape and avoids internal fogging.
3.eSlow Down for Cooling: ON — Improves surface finish with controlled cooling.
3.fForce Cooling for Overhangs: OFF — Overcooling can deform bridges in Timeplast.
3.gFan for Overhangs: 15% — Only for essential cooling in complex areas.
3.hPre-Start Fan Time: 2 seconds — Minimizes pressure differential during the first layer.4. Volumetric Flow
4.aMax Volumetric Speed: 12 mm³/s — Based on a melt flow index of ~15 g/10min, allows high-speed printing.
4.bRamming Speed: 3 mm³/s — Prevents bubbles or popping from pressure spikes.5. Retraction and Flow
5.aRetraction Distance: 0.4 mm — Minimal retraction required for soft filaments to avoid stringing.
5.bRetraction Speed: 15 mm/s — Slow enough to avoid pulling molten plastic.
5.cPressure Advance: 0.05 — Compensates for nozzle lag at high flow rates.
5.dFlow Ratio: 92% — Slight under-extrusion avoids swelling and surface artifacts.6. Precision Settings
6.aGap Closing Radius: 0.1 mm — Tolerant of gaps in thicker walls.
6.bArc Fitting: ON — Reduces G-code size and smooths curve transitions.
6.cElephant Foot Compensation: 0.1 mm — Offsets squishing in the first layer caused by large bead sizes.7. Walls and Shells
7.aWall Loops: 2 — Minimum for strength when using a 0.8 mm nozzle.
7.bDetect Thin Walls: ON — Ensures tight geometries aren’t skipped.
7.cTop/Bottom Shell Layers: 3 — Provides good coverage; increase if watertightness is needed.
7.dTop/Bottom Thickness: 1.2 mm — Equals 1.5x the nozzle size for solid strength.
7.eTop/Bottom Pattern: Monotonic — Distributes tension evenly and improves surface finish.8. Geometry and Movement
8.aWall Order: Inner before Outer — Creates cleaner outer surfaces.
8.bInfill First: OFF — Maintains precise outer dimensions.
8.cSmooth Speed Transition: ON — Prevents ringing caused by abrupt speed changes.
8.dSmooth Coefficient: 80 — Ideal damping for soft materials.
8.eAvoid Crossing Wall: ON — Minimizes stringing across part walls.
8.fMax Detour for Crossing: 10 mm or 5% — Balances time with print cleanliness.9. Layer and Width Settings
9.aLayer Height: 0.3 mm — Optimal for strength and resolution using a 0.8 mm nozzle.
9.bInitial Layer Height: 0.35 mm — Slightly higher to improve adhesion.
9.cLine Widths (all): 0.8 mm — Matches nozzle diameter for consistent extrusion.10. Seam Settings
10.aSeam Position: Aligned or Back — Use aligned for mechanical consistency, back for visual appeal.
10.bSmart Scarf Seam: ON — Automatically adjusts seam location to reduce visual impact.
10.cSeam Angle: 155° — Standard seam angle for clean transitions.
10.dSeam Steps: 10 — Smooths seam path and improves visual finish.11. Infill Settings
11.aWall/Infill Overlap: 10% — Prevents infill from deforming soft exterior walls.
11.bInfill Combination: ON — Consolidates paths for efficiency.
11.cDetect Floating Shells: ON — Ensures unsupported vertical structures are printed reliably.
11.dSparse Infill Density: 20–25% — Balanced rigidity vs. material use.
11.eSparse Pattern: Grid — Stable and efficient for flexible geometries.12. Speed Settings
12.aTravel: 160 mm/s — Fast but safe against backlash.
12.bInitial Layer: 15 mm/s — Prevents nozzle from skimming and ensures bed adhesion.
12.cOuter Wall: 60 mm/s — Controlled speed for surface quality.
12.dInner Wall: 90 mm/s — Slightly faster without compromising control.
12.eSmall Perimeter: 35 mm/s — Reduced speed for detailed geometry.
12.fTop Surface: 40 mm/s — Improves finish on topmost layers.
12.gInfill: 100–120 mm/s — Takes advantage of high flowability.13. Acceleration Settings
13.aNormal Print: 2000 mm/s² — Prevents ringing in soft filaments.
13.bTravel: 4000 mm/s² — Enables fast movement without harsh transitions.
13.cInitial Layer: 300 mm/s² — Gentle movement prevents lifting from the bed.
13.dOuter Wall: 1500 mm/s² — Improves outer surface clarity.
13.eInner Wall: 2000 mm/s² — Balanced for structural components.
13.fTop Surface: 1500 mm/s² — Ensures smooth detailing.14. Adhesion and Brims
14.aSkirt Loops: 2 — Helps prime nozzle and start cleanly.
14.bBrim Width: 6 mm — Helps hold soft materials down.
14.cBrim Gap: 0.15 mm — Allows for easy removal without tearing.15. Prime Tower and Flush Settings
15.aPrime Tower: ON — Purges moisture and early flow inconsistencies.
15.bTower Width: 40 mm — Prevents collapse due to heat.
15.cBrim Width (Tower): 4 mm — Adds stability to the purge base.
15.dFlush Into Support: ON — Discards unwanted early flow safely.16. G-Code Start Script
M900 K0.05 ; Pressure Advance M106 S0 ; Fan off G92 E0 G1 E15 F300 ; purge line G92 E0
17. Additional Notes
17.aDry filament at 100°C for 2 hours before use.
17.bStore with desiccant.
17.cKeep extruder door open to allow vapor to escape.
17.dAvoid long dwell times at high temperatures.If you need print settings for other nozzle sizes, feel free to reach out to us at timeplast@timeplast.com — we’ll be happy to help.
Free U.S. standard shipping on orders of 5+ spools!
Custom colors for 5+ same-type spools’ orders
Fungi Food
-
Optimized for mushroom growing, this filament contains gypsum (calcium sulfate) to provide vital minerals while managing pH. Includes slow-release hydration tech for sustained mycelium support.
Grow your mycelial empire—one layer at a time.
Where to use it:
DIY mushroom blocks
Humidity-retaining plugs
Spore carriers for inoculation kits.
-
Click here to access our specialized TimeMass GPT Assistant. Just tell it your printer model and the TimeMass filament you're using—it will instantly recommend the exact parameters you need to start printing successfully.
Using a Bambu Lab printer?
Click here to download our updated Bambu Lab profile. All printing parameters are fully optimized and tested—just load the file and start printing.1. Introduction
These parameters are designed to help avoid printing issues; however, temperatures and speed timings can be adjusted based on your specific goals. For example, if you prefer a less rigid result, we recommend using a lower temperature. This section outlines a complete slicing and printing profile for TimeMass Fungi Food, tailored for printers with a 0.8 mm nozzle. If the print is not being successful, please lower the nozzle temperature by 10°C and start over until an optimal print is achieved. While these examples were printed with a 0.8 mm nozzle, TimeMass can be used with any nozzle size. Please check the manual for printing parameters with all the other nozzle sizes.2. Temperature Settings
2.aNozzle Temperature: 240°C — Optimal for flowability while avoiding decomposition (which begins around 250°C).
2.bBed Temperature: 95°C — Ensures strong first-layer adhesion and prevents moisture bubbling.
2.cNozzle Temperature Range: 230–245°C — Timeplast melts around 165°C but prints best at 240°C for precise viscosity control.3. Cooling Settings
3.aNo Cooling for First Layers: 3 layers — Prevents shrinkage due to rapid cooling of moisture-rich filament.
3.bFan Minimum Speed: 0% for the first 100 seconds — Allows heat retention during early layers.
3.cFan Maximum Speed: 15% starting at 8 seconds — Avoids overcooling that can lead to warping.
3.dKeep Fan Always On: OFF — Allows vapor to escape and avoids internal fogging.
3.eSlow Down for Cooling: ON — Improves surface finish with controlled cooling.
3.fForce Cooling for Overhangs: OFF — Overcooling can deform bridges in Timeplast.
3.gFan for Overhangs: 15% — Only for essential cooling in complex areas.
3.hPre-Start Fan Time: 2 seconds — Minimizes pressure differential during the first layer.4. Volumetric Flow
4.aMax Volumetric Speed: 12 mm³/s — Based on a melt flow index of ~15 g/10min, allows high-speed printing.
4.bRamming Speed: 3 mm³/s — Prevents bubbles or popping from pressure spikes.5. Retraction and Flow
5.aRetraction Distance: 0.4 mm — Minimal retraction required for soft filaments to avoid stringing.
5.bRetraction Speed: 15 mm/s — Slow enough to avoid pulling molten plastic.
5.cPressure Advance: 0.05 — Compensates for nozzle lag at high flow rates.
5.dFlow Ratio: 92% — Slight under-extrusion avoids swelling and surface artifacts.6. Precision Settings
6.aGap Closing Radius: 0.1 mm — Tolerant of gaps in thicker walls.
6.bArc Fitting: ON — Reduces G-code size and smooths curve transitions.
6.cElephant Foot Compensation: 0.1 mm — Offsets squishing in the first layer caused by large bead sizes.7. Walls and Shells
7.aWall Loops: 2 — Minimum for strength when using a 0.8 mm nozzle.
7.bDetect Thin Walls: ON — Ensures tight geometries aren’t skipped.
7.cTop/Bottom Shell Layers: 3 — Provides good coverage; increase if watertightness is needed.
7.dTop/Bottom Thickness: 1.2 mm — Equals 1.5x the nozzle size for solid strength.
7.eTop/Bottom Pattern: Monotonic — Distributes tension evenly and improves surface finish.8. Geometry and Movement
8.aWall Order: Inner before Outer — Creates cleaner outer surfaces.
8.bInfill First: OFF — Maintains precise outer dimensions.
8.cSmooth Speed Transition: ON — Prevents ringing caused by abrupt speed changes.
8.dSmooth Coefficient: 80 — Ideal damping for soft materials.
8.eAvoid Crossing Wall: ON — Minimizes stringing across part walls.
8.fMax Detour for Crossing: 10 mm or 5% — Balances time with print cleanliness.9. Layer and Width Settings
9.aLayer Height: 0.3 mm — Optimal for strength and resolution using a 0.8 mm nozzle.
9.bInitial Layer Height: 0.35 mm — Slightly higher to improve adhesion.
9.cLine Widths (all): 0.8 mm — Matches nozzle diameter for consistent extrusion.10. Seam Settings
10.aSeam Position: Aligned or Back — Use aligned for mechanical consistency, back for visual appeal.
10.bSmart Scarf Seam: ON — Automatically adjusts seam location to reduce visual impact.
10.cSeam Angle: 155° — Standard seam angle for clean transitions.
10.dSeam Steps: 10 — Smooths seam path and improves visual finish.11. Infill Settings
11.aWall/Infill Overlap: 10% — Prevents infill from deforming soft exterior walls.
11.bInfill Combination: ON — Consolidates paths for efficiency.
11.cDetect Floating Shells: ON — Ensures unsupported vertical structures are printed reliably.
11.dSparse Infill Density: 20–25% — Balanced rigidity vs. material use.
11.eSparse Pattern: Grid — Stable and efficient for flexible geometries.12. Speed Settings
12.aTravel: 160 mm/s — Fast but safe against backlash.
12.bInitial Layer: 15 mm/s — Prevents nozzle from skimming and ensures bed adhesion.
12.cOuter Wall: 60 mm/s — Controlled speed for surface quality.
12.dInner Wall: 90 mm/s — Slightly faster without compromising control.
12.eSmall Perimeter: 35 mm/s — Reduced speed for detailed geometry.
12.fTop Surface: 40 mm/s — Improves finish on topmost layers.
12.gInfill: 100–120 mm/s — Takes advantage of high flowability.13. Acceleration Settings
13.aNormal Print: 2000 mm/s² — Prevents ringing in soft filaments.
13.bTravel: 4000 mm/s² — Enables fast movement without harsh transitions.
13.cInitial Layer: 300 mm/s² — Gentle movement prevents lifting from the bed.
13.dOuter Wall: 1500 mm/s² — Improves outer surface clarity.
13.eInner Wall: 2000 mm/s² — Balanced for structural components.
13.fTop Surface: 1500 mm/s² — Ensures smooth detailing.14. Adhesion and Brims
14.aSkirt Loops: 2 — Helps prime nozzle and start cleanly.
14.bBrim Width: 6 mm — Helps hold soft materials down.
14.cBrim Gap: 0.15 mm — Allows for easy removal without tearing.15. Prime Tower and Flush Settings
15.aPrime Tower: ON — Purges moisture and early flow inconsistencies.
15.bTower Width: 40 mm — Prevents collapse due to heat.
15.cBrim Width (Tower): 4 mm — Adds stability to the purge base.
15.dFlush Into Support: ON — Discards unwanted early flow safely.16. G-Code Start Script
M900 K0.05 ; Pressure Advance M106 S0 ; Fan off G92 E0 G1 E15 F300 ; purge line G92 E0
17. Additional Notes
17.aDry filament at 100°C for 2 hours before use.
17.bStore with desiccant.
17.cKeep extruder door open to allow vapor to escape.
17.dAvoid long dwell times at high temperatures.If you need print settings for other nozzle sizes, feel free to reach out to us at timeplast@timeplast.com — we’ll be happy to help.
Free U.S. standard shipping on orders of 5+ spools!
Custom colors for 5+ same-type spools’ orders
Survival & Emergency
Fire - Gen 2
-
TimeMass Fire Gen 2 is a burnable 3D printing filament made of water, wood, calcium carbonate, vinegar, in-house made and patented polymerized alcohol.
It prints fast, melts smooth, burns clean, and yes—it’s designed to ignite on purpose. Unlike traditional filaments that either melt like sad spaghetti or combust like a campfire mistake, this one burns right.
Want to print candles? Fire sculptures? Ritual objects for your post-plastic utopia? Go wild. You can even design your prints to control how they burn—fast, slow, flashy, or dramatic.
Pro tip: treat your print like a wick. Too thick? It’ll choke. Too thin? It’ll vanish. Just right? Beautiful combustion.
-
Click here to access our specialized TimeMass GPT Assistant. Just tell it your printer model and the TimeMass filament you're using—it will instantly recommend the exact parameters you need to start printing successfully.
Using a Bambu Lab printer?
Click here to download our updated Bambu Lab profile. All printing parameters are fully optimized and tested—just load the file and start printing.1. Introduction
These parameters are designed to help avoid printing issues; however, temperatures and speed timings can be adjusted based on your specific goals. For example, if you prefer a less rigid result, we recommend using a lower temperature. This section outlines a complete slicing and printing profile for TimeMass Active, tailored for printers with a 0.8 mm nozzle. If the print is not being successful, please lower the nozzle temperature by 10°C and start over until an optimal print is achieved.While these examples were printed with a 0.8 mm nozzle, TimeMass can be used with any nozzle size. Please check the manual for printing parameters with all the other nozzle sizes.2. Temperature Settings
2.aNozzle Temperature: 240°C — Optimal for flowability while avoiding decomposition (which begins around 250°C).
2.bBed Temperature: 95°C — Ensures strong first-layer adhesion and prevents moisture bubbling.
2.cNozzle Temperature Range: 230–245°C — Timeplast melts around 165°C but prints best at 240°C for precise viscosity control.3. Cooling Settings
3.aNo Cooling for First Layers: 3 layers — Prevents shrinkage due to rapid cooling of moisture-rich filament.
3.bFan Minimum Speed: 0% for the first 100 seconds — Allows heat retention during early layers.
3.cFan Maximum Speed: 15% starting at 8 seconds — Avoids overcooling that can lead to warping.
3.dKeep Fan Always On: OFF — Allows vapor to escape and avoids internal fogging.
3.eSlow Down for Cooling: ON — Improves surface finish with controlled cooling.
3.fForce Cooling for Overhangs: OFF — Overcooling can deform bridges in Timeplast.
3.gFan for Overhangs: 15% — Only for essential cooling in complex areas.
3.hPre-Start Fan Time: 2 seconds — Minimizes pressure differential during the first layer.4. Volumetric Flow
4.aMax Volumetric Speed: 12 mm³/s — Based on a melt flow index of ~15 g/10min, allows high-speed printing.
4.bRamming Speed: 3 mm³/s — Prevents bubbles or popping from pressure spikes.5. Retraction and Flow
5.aRetraction Distance: 0.4 mm — Minimal retraction required for soft filaments to avoid stringing.
5.bRetraction Speed: 15 mm/s — Slow enough to avoid pulling molten plastic.
5.cPressure Advance: 0.05 — Compensates for nozzle lag at high flow rates.
5.dFlow Ratio: 92% — Slight under-extrusion avoids swelling and surface artifacts.6. Precision Settings
6.aGap Closing Radius: 0.1 mm — Tolerant of gaps in thicker walls.
6.bArc Fitting: ON — Reduces G-code size and smooths curve transitions.
6.cElephant Foot Compensation: 0.1 mm — Offsets squishing in the first layer caused by large bead sizes.7. Walls and Shells
7.aWall Loops: 2 — Minimum for strength when using a 0.8 mm nozzle.
7.bDetect Thin Walls: ON — Ensures tight geometries aren’t skipped.
7.cTop/Bottom Shell Layers: 3 — Provides good coverage; increase if watertightness is needed.
7.dTop/Bottom Thickness: 1.2 mm — Equals 1.5x the nozzle size for solid strength.
7.eTop/Bottom Pattern: Monotonic — Distributes tension evenly and improves surface finish.8. Geometry and Movement
8.aWall Order: Inner before Outer — Creates cleaner outer surfaces.
8.bInfill First: OFF — Maintains precise outer dimensions.
8.cSmooth Speed Transition: ON — Prevents ringing caused by abrupt speed changes.
8.dSmooth Coefficient: 80 — Ideal damping for soft materials.
8.eAvoid Crossing Wall: ON — Minimizes stringing across part walls.
8.fMax Detour for Crossing: 10 mm or 5% — Balances time with print cleanliness.9. Layer and Width Settings
9.aLayer Height: 0.3 mm — Optimal for strength and resolution using a 0.8 mm nozzle.
9.bInitial Layer Height: 0.35 mm — Slightly higher to improve adhesion.
9.cLine Widths (all): 0.8 mm — Matches nozzle diameter for consistent extrusion.10. Seam Settings
10.aSeam Position: Aligned or Back — Use aligned for mechanical consistency, back for visual appeal.
10.bSmart Scarf Seam: ON — Automatically adjusts seam location to reduce visual impact.
10.cSeam Angle: 155° — Standard seam angle for clean transitions.
10.dSeam Steps: 10 — Smooths seam path and improves visual finish.11. Infill Settings
11.aWall/Infill Overlap: 10% — Prevents infill from deforming soft exterior walls.
11.bInfill Combination: ON — Consolidates paths for efficiency.
11.cDetect Floating Shells: ON — Ensures unsupported vertical structures are printed reliably.
11.dSparse Infill Density: 20–25% — Balanced rigidity vs. material use.
11.eSparse Pattern: Grid — Stable and efficient for flexible geometries.12. Speed Settings
12.aTravel: 160 mm/s — Fast but safe against backlash.
12.bInitial Layer: 15 mm/s — Prevents nozzle from skimming and ensures bed adhesion.
12.cOuter Wall: 60 mm/s — Controlled speed for surface quality.
12.dInner Wall: 90 mm/s — Slightly faster without compromising control.
12.eSmall Perimeter: 35 mm/s — Reduced speed for detailed geometry.
12.fTop Surface: 40 mm/s — Improves finish on topmost layers.
12.gInfill: 100–120 mm/s — Takes advantage of high flowability.13. Acceleration Settings
13.aNormal Print: 2000 mm/s² — Prevents ringing in soft filaments.
13.bTravel: 4000 mm/s² — Enables fast movement without harsh transitions.
13.cInitial Layer: 300 mm/s² — Gentle movement prevents lifting from the bed.
13.dOuter Wall: 1500 mm/s² — Improves outer surface clarity.
13.eInner Wall: 2000 mm/s² — Balanced for structural components.
13.fTop Surface: 1500 mm/s² — Ensures smooth detailing.14. Adhesion and Brims
14.aSkirt Loops: 2 — Helps prime nozzle and start cleanly.
14.bBrim Width: 6 mm — Helps hold soft materials down.
14.cBrim Gap: 0.15 mm — Allows for easy removal without tearing.15. Prime Tower and Flush Settings
15.aPrime Tower: ON — Purges moisture and early flow inconsistencies.
15.bTower Width: 40 mm — Prevents collapse due to heat.
15.cBrim Width (Tower): 4 mm — Adds stability to the purge base.
15.dFlush Into Support: ON — Discards unwanted early flow safely.16. G-Code Start Script
M900 K0.05 ; Pressure Advance M106 S0 ; Fan off G92 E0 G1 E15 F300 ; purge line G92 E0
17. Additional Notes
17.aDry filament at 100°C for 2 hours before use.
17.bStore with desiccant.
17.cKeep extruder door open to allow vapor to escape.
17.dAvoid long dwell times at high temperatures.If you need print settings for other nozzle sizes, feel free to reach out to us at timeplast@timeplast.com — we’ll be happy to help.
Free U.S. standard shipping on orders of 5+ spools!
Custom colors for 5+ same-type spools’ orders
Soap - Gen 4
-
TimeMass Soap Gen 4 – Now With Bubbles. You're Welcome.
TimeMass Soap Gen 4 is the world’s first truly 3D-printable soap that not only cleans like a lab-engineered miracle—it actually foams. Yes. You read that right. We finally cracked the code.
Built from water, calcium carbonate, in-house polymerized alcohols, olive oil, essential oils, and a balanced mix of surfactants and emulsifiers (Coco-Glucoside and Glyceryl Stearate), this filament is part soap, part science experiment, part victory lap.
With Gen 4, we stabilized the chemistry to unleash full surfactant performance without compromising printability. The result: a bar of soap that prints like butter, foams like a show-off, and still lasts 10x longer than whatever you're buying in a box store.
What’s Inside:
Water + Alcohol – Gives it print flexibility, then hardens post-print like it means business.
Calcium Carbonate – For that gentle grit you didn’t know you loved (also in toothpaste).
Surfactants & Emulsifiers – Now optimized to actually lather, not just clean in silence.
Olive Oil – Moisturizing, luxurious, Mediterranean-approved.
Essential Oils – Fragrance, antimicrobial power, and optional spa vibes.
New in Gen 4: Bubbles. Real Ones.
After years of foam denial, we said, “Fine, let’s give the people what they want.”
And now? Lather. Suds. Foamy satisfaction.
It’s still smart. Still efficient. Still weird. Just now... it’s bubbly too.Use It Like a Mad Soap Alchemist:
Print your own soaps. Pause mid-print to inject oils, moisturizers, exfoliants—or secrets.
Embed capsules or time-release additives.
Sculpt messages into your soap. (Post-apocalyptic love notes, maybe?)
Why It Rules:
Cleans with actual foam (finally).
Printable on any basic 3D printer.
Reusable, regenerative, long-lasting.
Customizable with whatever wild scent profile you dream up.
Electrostatically attracts and removes dirt and grease like a polite molecular hitman.
TimeMass Soap Gen 4:
For people who love soap science, hate waste, and secretly always wanted a 3D printer that could make bath products. We did what the skeptics said was impossible.Now go print something that lathers.
Safety tip: Don’t go wild with undiluted essential oils. They’re called “concentrated” for a reason. Use responsibly.
-
Click here to access our specialized TimeMass GPT Assistant. Just tell it your printer model and the TimeMass filament you're using—it will instantly recommend the exact parameters you need to start printing successfully.
Using a Bambu Lab printer?
Click here to download our updated Bambu Lab profile. All printing parameters are fully optimized and tested—just load the file and start printing.1. Introduction
These parameters are designed to help avoid printing issues; however, temperatures and speed timings can be adjusted based on your specific goals. For example, if you prefer a less rigid result, we recommend using a lower temperature. This section outlines a complete slicing and printing profile for TimeMass Fire, tailored for printers with a 0.8 mm nozzle. If the print is not being successful, please lower the nozzle temperature by 10°C and start over until an optimal print is achieved. While these examples were printed with a 0.8 mm nozzle, TimeMass can be used with any nozzle size. Please check the manual for printing parameters with all the other nozzle sizes.2. Temperature Settings
2.aNozzle Temperature: 240°C — Optimal for flowability while avoiding decomposition (which begins around 250°C).
2.bBed Temperature: 95°C — Ensures strong first-layer adhesion and prevents moisture bubbling.
2.cNozzle Temperature Range: 230–245°C — Timeplast melts around 165°C but prints best at 240°C for precise viscosity control.3. Cooling Settings
3.aNo Cooling for First Layers: 3 layers — Prevents shrinkage due to rapid cooling of moisture-rich filament.
3.bFan Minimum Speed: 0% for the first 100 seconds — Allows heat retention during early layers.
3.cFan Maximum Speed: 15% starting at 8 seconds — Avoids overcooling that can lead to warping.
3.dKeep Fan Always On: OFF — Allows vapor to escape and avoids internal fogging.
3.eSlow Down for Cooling: ON — Improves surface finish with controlled cooling.
3.fForce Cooling for Overhangs: OFF — Overcooling can deform bridges in Timeplast.
3.gFan for Overhangs: 15% — Only for essential cooling in complex areas.
3.hPre-Start Fan Time: 2 seconds — Minimizes pressure differential during the first layer.4. Volumetric Flow
4.aMax Volumetric Speed: 12 mm³/s — Based on a melt flow index of ~15 g/10min, allows high-speed printing.
4.bRamming Speed: 3 mm³/s — Prevents bubbles or popping from pressure spikes.5. Retraction and Flow
5.aRetraction Distance: 0.4 mm — Minimal retraction required for soft filaments to avoid stringing.
5.bRetraction Speed: 15 mm/s — Slow enough to avoid pulling molten plastic.
5.cPressure Advance: 0.05 — Compensates for nozzle lag at high flow rates.
5.dFlow Ratio: 92% — Slight under-extrusion avoids swelling and surface artifacts.6. Precision Settings
6.aGap Closing Radius: 0.1 mm — Tolerant of gaps in thicker walls.
6.bArc Fitting: ON — Reduces G-code size and smooths curve transitions.
6.cElephant Foot Compensation: 0.1 mm — Offsets squishing in the first layer caused by large bead sizes.7. Walls and Shells
7.aWall Loops: 2 — Minimum for strength when using a 0.8 mm nozzle.
7.bDetect Thin Walls: ON — Ensures tight geometries aren’t skipped.
7.cTop/Bottom Shell Layers: 3 — Provides good coverage; increase if watertightness is needed.
7.dTop/Bottom Thickness: 1.2 mm — Equals 1.5x the nozzle size for solid strength.
7.eTop/Bottom Pattern: Monotonic — Distributes tension evenly and improves surface finish.8. Geometry and Movement
8.aWall Order: Inner before Outer — Creates cleaner outer surfaces.
8.bInfill First: OFF — Maintains precise outer dimensions.
8.cSmooth Speed Transition: ON — Prevents ringing caused by abrupt speed changes.
8.dSmooth Coefficient: 80 — Ideal damping for soft materials.
8.eAvoid Crossing Wall: ON — Minimizes stringing across part walls.
8.fMax Detour for Crossing: 10 mm or 5% — Balances time with print cleanliness.9. Layer and Width Settings
9.aLayer Height: 0.3 mm — Optimal for strength and resolution using a 0.8 mm nozzle.
9.bInitial Layer Height: 0.35 mm — Slightly higher to improve adhesion.
9.cLine Widths (all): 0.8 mm — Matches nozzle diameter for consistent extrusion.10. Seam Settings
10.aSeam Position: Aligned or Back — Use aligned for mechanical consistency, back for visual appeal.
10.bSmart Scarf Seam: ON — Automatically adjusts seam location to reduce visual impact.
10.cSeam Angle: 155° — Standard seam angle for clean transitions.
10.dSeam Steps: 10 — Smooths seam path and improves visual finish.11. Infill Settings
11.aWall/Infill Overlap: 10% — Prevents infill from deforming soft exterior walls.
11.bInfill Combination: ON — Consolidates paths for efficiency.
11.cDetect Floating Shells: ON — Ensures unsupported vertical structures are printed reliably.
11.dSparse Infill Density: 20–25% — Balanced rigidity vs. material use.
11.eSparse Pattern: Grid — Stable and efficient for flexible geometries.12. Speed Settings
12.aTravel: 160 mm/s — Fast but safe against backlash.
12.bInitial Layer: 15 mm/s — Prevents nozzle from skimming and ensures bed adhesion.
12.cOuter Wall: 60 mm/s — Controlled speed for surface quality.
12.dInner Wall: 90 mm/s — Slightly faster without compromising control.
12.eSmall Perimeter: 35 mm/s — Reduced speed for detailed geometry.
12.fTop Surface: 40 mm/s — Improves finish on topmost layers.
12.gInfill: 100–120 mm/s — Takes advantage of high flowability.13. Acceleration Settings
13.aNormal Print: 2000 mm/s² — Prevents ringing in soft filaments.
13.bTravel: 4000 mm/s² — Enables fast movement without harsh transitions.
13.cInitial Layer: 300 mm/s² — Gentle movement prevents lifting from the bed.
13.dOuter Wall: 1500 mm/s² — Improves outer surface clarity.
13.eInner Wall: 2000 mm/s² — Balanced for structural components.
13.fTop Surface: 1500 mm/s² — Ensures smooth detailing.14. Adhesion and Brims
14.aSkirt Loops: 2 — Helps prime nozzle and start cleanly.
14.bBrim Width: 6 mm — Helps hold soft materials down.
14.cBrim Gap: 0.15 mm — Allows for easy removal without tearing.15. Prime Tower and Flush Settings
15.aPrime Tower: ON — Purges moisture and early flow inconsistencies.
15.bTower Width: 40 mm — Prevents collapse due to heat.
15.cBrim Width (Tower): 4 mm — Adds stability to the purge base.
15.dFlush Into Support: ON — Discards unwanted early flow safely.16. G-Code Start Script
M900 K0.05 ; Pressure Advance M106 S0 ; Fan off G92 E0 G1 E15 F300 ; purge line G92 E0
17. Additional Notes
17.aDry filament at 100°C for 2 hours before use.
17.bStore with desiccant.
17.cKeep extruder door open to allow vapor to escape.
17.dAvoid long dwell times at high temperatures.If you need print settings for other nozzle sizes, feel free to reach out to us at timeplast@timeplast.com — we’ll be happy to help.
Free U.S. standard shipping on orders of 5+ spools!
Custom colors for 5+ same-type spools’ orders
Antibacterial Soap - Gen 4
-
A self-cleaning filament that combines natural antibacterial and antifungal power into one. Made with vinegar, borax, zinc oxide, and miconazole nitrate (2%), this filament is ready to fight microbial threats from every angle.
Clean hands. Clean surfaces. Clean tech.
How it works:
Moisture triggers the slow release of antimicrobial actives while preserving integrity for extended use.
No slime. No waste. Just embedded hygiene.
Active Components:
Vinegar – Natural disinfectant
Zinc Oxide – Skin-safe germ barrier
Miconazole Nitrate – Fungus-fighting hero
Where to use it:
Reusable soap bars – Long-lasting, antibacterial blocks
Public-use objects – Prevent bacteria build-up
Gym or school items – Stay protected with every touch
Anti-fungal trays or dispensers
-
Click here to access our specialized TimeMass GPT Assistant. Just tell it your printer model and the TimeMass filament you're using—it will instantly recommend the exact parameters you need to start printing successfully.
Using a Bambu Lab printer?
Click here to download our updated Bambu Lab profile. All printing parameters are fully optimized and tested—just load the file and start printing.1. Introduction
These parameters are designed to help avoid printing issues; however, temperatures and speed timings can be adjusted based on your specific goals. For example, if you prefer a less rigid result, we recommend using a lower temperature. This section outlines a complete slicing and printing profile for TimeMass Antibacterial Soap, tailored for printers with a 0.8 mm nozzle. If the print is not being successful, please lower the nozzle temperature by 10°C and start over until an optimal print is achieved. While these examples were printed with a 0.8 mm nozzle, TimeMass can be used with any nozzle size. Please check the manual for printing parameters with all the other nozzle sizes.2. Temperature Settings
2.aNozzle Temperature: 240°C — Optimal for flowability while avoiding decomposition (which begins around 250°C).
2.bBed Temperature: 95°C — Ensures strong first-layer adhesion and prevents moisture bubbling.
2.cNozzle Temperature Range: 230–245°C — Timeplast melts around 165°C but prints best at 240°C for precise viscosity control.3. Cooling Settings
3.aNo Cooling for First Layers: 3 layers — Prevents shrinkage due to rapid cooling of moisture-rich filament.
3.bFan Minimum Speed: 0% for the first 100 seconds — Allows heat retention during early layers.
3.cFan Maximum Speed: 15% starting at 8 seconds — Avoids overcooling that can lead to warping.
3.dKeep Fan Always On: OFF — Allows vapor to escape and avoids internal fogging.
3.eSlow Down for Cooling: ON — Improves surface finish with controlled cooling.
3.fForce Cooling for Overhangs: OFF — Overcooling can deform bridges in Timeplast.
3.gFan for Overhangs: 15% — Only for essential cooling in complex areas.
3.hPre-Start Fan Time: 2 seconds — Minimizes pressure differential during the first layer.4. Volumetric Flow
4.aMax Volumetric Speed: 12 mm³/s — Based on a melt flow index of ~15 g/10min, allows high-speed printing.
4.bRamming Speed: 3 mm³/s — Prevents bubbles or popping from pressure spikes.5. Retraction and Flow
5.aRetraction Distance: 0.4 mm — Minimal retraction required for soft filaments to avoid stringing.
5.bRetraction Speed: 15 mm/s — Slow enough to avoid pulling molten plastic.
5.cPressure Advance: 0.05 — Compensates for nozzle lag at high flow rates.
5.dFlow Ratio: 92% — Slight under-extrusion avoids swelling and surface artifacts.6. Precision Settings
6.aGap Closing Radius: 0.1 mm — Tolerant of gaps in thicker walls.
6.bArc Fitting: ON — Reduces G-code size and smooths curve transitions.
6.cElephant Foot Compensation: 0.1 mm — Offsets squishing in the first layer caused by large bead sizes.7. Walls and Shells
7.aWall Loops: 2 — Minimum for strength when using a 0.8 mm nozzle.
7.bDetect Thin Walls: ON — Ensures tight geometries aren’t skipped.
7.cTop/Bottom Shell Layers: 3 — Provides good coverage; increase if watertightness is needed.
7.dTop/Bottom Thickness: 1.2 mm — Equals 1.5x the nozzle size for solid strength.
7.eTop/Bottom Pattern: Monotonic — Distributes tension evenly and improves surface finish.8. Geometry and Movement
8.aWall Order: Inner before Outer — Creates cleaner outer surfaces.
8.bInfill First: OFF — Maintains precise outer dimensions.
8.cSmooth Speed Transition: ON — Prevents ringing caused by abrupt speed changes.
8.dSmooth Coefficient: 80 — Ideal damping for soft materials.
8.eAvoid Crossing Wall: ON — Minimizes stringing across part walls.
8.fMax Detour for Crossing: 10 mm or 5% — Balances time with print cleanliness.9. Layer and Width Settings
9.aLayer Height: 0.3 mm — Optimal for strength and resolution using a 0.8 mm nozzle.
9.bInitial Layer Height: 0.35 mm — Slightly higher to improve adhesion.
9.cLine Widths (all): 0.8 mm — Matches nozzle diameter for consistent extrusion.10. Seam Settings
10.aSeam Position: Aligned or Back — Use aligned for mechanical consistency, back for visual appeal.
10.bSmart Scarf Seam: ON — Automatically adjusts seam location to reduce visual impact.
10.cSeam Angle: 155° — Standard seam angle for clean transitions.
10.dSeam Steps: 10 — Smooths seam path and improves visual finish.11. Infill Settings
11.aWall/Infill Overlap: 10% — Prevents infill from deforming soft exterior walls.
11.bInfill Combination: ON — Consolidates paths for efficiency.
11.cDetect Floating Shells: ON — Ensures unsupported vertical structures are printed reliably.
11.dSparse Infill Density: 20–25% — Balanced rigidity vs. material use.
11.eSparse Pattern: Grid — Stable and efficient for flexible geometries.12. Speed Settings
12.aTravel: 160 mm/s — Fast but safe against backlash.
12.bInitial Layer: 15 mm/s — Prevents nozzle from skimming and ensures bed adhesion.
12.cOuter Wall: 60 mm/s — Controlled speed for surface quality.
12.dInner Wall: 90 mm/s — Slightly faster without compromising control.
12.eSmall Perimeter: 35 mm/s — Reduced speed for detailed geometry.
12.fTop Surface: 40 mm/s — Improves finish on topmost layers.
12.gInfill: 100–120 mm/s — Takes advantage of high flowability.13. Acceleration Settings
13.aNormal Print: 2000 mm/s² — Prevents ringing in soft filaments.
13.bTravel: 4000 mm/s² — Enables fast movement without harsh transitions.
13.cInitial Layer: 300 mm/s² — Gentle movement prevents lifting from the bed.
13.dOuter Wall: 1500 mm/s² — Improves outer surface clarity.
13.eInner Wall: 2000 mm/s² — Balanced for structural components.
13.fTop Surface: 1500 mm/s² — Ensures smooth detailing.14. Adhesion and Brims
14.aSkirt Loops: 2 — Helps prime nozzle and start cleanly.
14.bBrim Width: 6 mm — Helps hold soft materials down.
14.cBrim Gap: 0.15 mm — Allows for easy removal without tearing.15. Prime Tower and Flush Settings
15.aPrime Tower: ON — Purges moisture and early flow inconsistencies.
15.bTower Width: 40 mm — Prevents collapse due to heat.
15.cBrim Width (Tower): 4 mm — Adds stability to the purge base.
15.dFlush Into Support: ON — Discards unwanted early flow safely.16. G-Code Start Script
M900 K0.05 ; Pressure Advance M106 S0 ; Fan off G92 E0 G1 E15 F300 ; purge line G92 E0
17. Additional Notes
17.aDry filament at 100°C for 2 hours before use.
17.bStore with desiccant.
17.cKeep extruder door open to allow vapor to escape.
17.dAvoid long dwell times at high temperatures.If you need print settings for other nozzle sizes, feel free to reach out to us at timeplast@timeplast.com — we’ll be happy to help.
Free U.S. standard shipping on orders of 5+ spools!
Custom colors for 5+ same-type spools’ orders
Antibacterial
-
Engineered with embedded slow-release antibacterial agents like Vinegar, borax and chloride compounds, this filament forms a protective and immunity aura around your printed part. Designed to maintain hygiene and reduce microbial growth on high-contact surfaces.
Built-in immunity, powered by science.
How it works:
Encapsulated antimicrobials are slowly released upon contact with ambient moisture, delivering long-term protection without leaching or surface degradation.
No coatings. No sprays. Just baked-in sanitation.
Antibacterial Agents:
Vinegar and Borax: Inhibits bacterial metabolism
Calcium hypochlorite, powerful oxidant and cell killer.
Zinc Oxide (trace): Reinforces microbe resistance
Where to use it:
Public touchpoints – Door handles, elevator buttons, light switches
Healthcare prototypes – Lab tools, dispensers, trays
Pet products – Clean bowls, toys, or water-dispensing structures
Educational tools – Safe-to-touch classroom models
-
Click here to access our specialized TimeMass GPT Assistant. Just tell it your printer model and the TimeMass filament you're using—it will instantly recommend the exact parameters you need to start printing successfully.
Using a Bambu Lab printer?
Click here to download our updated Bambu Lab profile. All printing parameters are fully optimized and tested—just load the file and start printing.1. Introduction
These parameters are designed to help avoid printing issues; however, temperatures and speed timings can be adjusted based on your specific goals. For example, if you prefer a less rigid result, we recommend using a lower temperature. This section outlines a complete slicing and printing profile for TimeMass Antibacterial, tailored for printers with a 0.8 mm nozzle. If the print is not being successful, please lower the nozzle temperature by 10°C and start over until an optimal print is achieved. While these examples were printed with a 0.8 mm nozzle, TimeMass can be used with any nozzle size. Please check the manual for printing parameters with all the other nozzle sizes.2. Temperature Settings
2.aNozzle Temperature: 240°C — Optimal for flowability while avoiding decomposition (which begins around 250°C).
2.bBed Temperature: 95°C — Ensures strong first-layer adhesion and prevents moisture bubbling.
2.cNozzle Temperature Range: 230–245°C — Timeplast melts around 165°C but prints best at 240°C for precise viscosity control.3. Cooling Settings
3.aNo Cooling for First Layers: 3 layers — Prevents shrinkage due to rapid cooling of moisture-rich filament.
3.bFan Minimum Speed: 0% for the first 100 seconds — Allows heat retention during early layers.
3.cFan Maximum Speed: 15% starting at 8 seconds — Avoids overcooling that can lead to warping.
3.dKeep Fan Always On: OFF — Allows vapor to escape and avoids internal fogging.
3.eSlow Down for Cooling: ON — Improves surface finish with controlled cooling.
3.fForce Cooling for Overhangs: OFF — Overcooling can deform bridges in Timeplast.
3.gFan for Overhangs: 15% — Only for essential cooling in complex areas.
3.hPre-Start Fan Time: 2 seconds — Minimizes pressure differential during the first layer.4. Volumetric Flow
4.aMax Volumetric Speed: 12 mm³/s — Based on a melt flow index of ~15 g/10min, allows high-speed printing.
4.bRamming Speed: 3 mm³/s — Prevents bubbles or popping from pressure spikes.5. Retraction and Flow
5.aRetraction Distance: 0.4 mm — Minimal retraction required for soft filaments to avoid stringing.
5.bRetraction Speed: 15 mm/s — Slow enough to avoid pulling molten plastic.
5.cPressure Advance: 0.05 — Compensates for nozzle lag at high flow rates.
5.dFlow Ratio: 92% — Slight under-extrusion avoids swelling and surface artifacts.6. Precision Settings
6.aGap Closing Radius: 0.1 mm — Tolerant of gaps in thicker walls.
6.bArc Fitting: ON — Reduces G-code size and smooths curve transitions.
6.cElephant Foot Compensation: 0.1 mm — Offsets squishing in the first layer caused by large bead sizes.7. Walls and Shells
7.aWall Loops: 2 — Minimum for strength when using a 0.8 mm nozzle.
7.bDetect Thin Walls: ON — Ensures tight geometries aren’t skipped.
7.cTop/Bottom Shell Layers: 3 — Provides good coverage; increase if watertightness is needed.
7.dTop/Bottom Thickness: 1.2 mm — Equals 1.5x the nozzle size for solid strength.
7.eTop/Bottom Pattern: Monotonic — Distributes tension evenly and improves surface finish.8. Geometry and Movement
8.aWall Order: Inner before Outer — Creates cleaner outer surfaces.
8.bInfill First: OFF — Maintains precise outer dimensions.
8.cSmooth Speed Transition: ON — Prevents ringing caused by abrupt speed changes.
8.dSmooth Coefficient: 80 — Ideal damping for soft materials.
8.eAvoid Crossing Wall: ON — Minimizes stringing across part walls.
8.fMax Detour for Crossing: 10 mm or 5% — Balances time with print cleanliness.9. Layer and Width Settings
9.aLayer Height: 0.3 mm — Optimal for strength and resolution using a 0.8 mm nozzle.
9.bInitial Layer Height: 0.35 mm — Slightly higher to improve adhesion.
9.cLine Widths (all): 0.8 mm — Matches nozzle diameter for consistent extrusion.10. Seam Settings
10.aSeam Position: Aligned or Back — Use aligned for mechanical consistency, back for visual appeal.
10.bSmart Scarf Seam: ON — Automatically adjusts seam location to reduce visual impact.
10.cSeam Angle: 155° — Standard seam angle for clean transitions.
10.dSeam Steps: 10 — Smooths seam path and improves visual finish.11. Infill Settings
11.aWall/Infill Overlap: 10% — Prevents infill from deforming soft exterior walls.
11.bInfill Combination: ON — Consolidates paths for efficiency.
11.cDetect Floating Shells: ON — Ensures unsupported vertical structures are printed reliably.
11.dSparse Infill Density: 20–25% — Balanced rigidity vs. material use.
11.eSparse Pattern: Grid — Stable and efficient for flexible geometries.12. Speed Settings
12.aTravel: 160 mm/s — Fast but safe against backlash.
12.bInitial Layer: 15 mm/s — Prevents nozzle from skimming and ensures bed adhesion.
12.cOuter Wall: 60 mm/s — Controlled speed for surface quality.
12.dInner Wall: 90 mm/s — Slightly faster without compromising control.
12.eSmall Perimeter: 35 mm/s — Reduced speed for detailed geometry.
12.fTop Surface: 40 mm/s — Improves finish on topmost layers.
12.gInfill: 100–120 mm/s — Takes advantage of high flowability.13. Acceleration Settings
13.aNormal Print: 2000 mm/s² — Prevents ringing in soft filaments.
13.bTravel: 4000 mm/s² — Enables fast movement without harsh transitions.
13.cInitial Layer: 300 mm/s² — Gentle movement prevents lifting from the bed.
13.dOuter Wall: 1500 mm/s² — Improves outer surface clarity.
13.eInner Wall: 2000 mm/s² — Balanced for structural components.
13.fTop Surface: 1500 mm/s² — Ensures smooth detailing.14. Adhesion and Brims
14.aSkirt Loops: 2 — Helps prime nozzle and start cleanly.
14.bBrim Width: 6 mm — Helps hold soft materials down.
14.cBrim Gap: 0.15 mm — Allows for easy removal without tearing.15. Prime Tower and Flush Settings
15.aPrime Tower: ON — Purges moisture and early flow inconsistencies.
15.bTower Width: 40 mm — Prevents collapse due to heat.
15.cBrim Width (Tower): 4 mm — Adds stability to the purge base.
15.dFlush Into Support: ON — Discards unwanted early flow safely.16. G-Code Start Script
M900 K0.05 ; Pressure Advance M106 S0 ; Fan off G92 E0 G1 E15 F300 ; purge line G92 E0
17. Additional Notes
17.aDry filament at 100°C for 2 hours before use.
17.bStore with desiccant.
17.cKeep extruder door open to allow vapor to escape.
17.dAvoid long dwell times at high temperatures.If you need print settings for other nozzle sizes, feel free to reach out to us at timeplast@timeplast.com — we’ll be happy to help.
Free U.S. standard shipping on orders of 5+ spools!
Custom colors for 5+ same-type spools’ orders
Multifunctional
Stick & Glow
-
A triple-visibility filament that glows in the dark, reflects light, and sparkles in daylight. Made for visibility, safety, and unapologetic flair. If you want your prints to pop—day or night—this is your go-to.
Shine. Reflect. Dazzle.
How it works:
Multiple light-responsive additives are embedded within a durable polymer carrier, activated by natural or artificial light.
Day or night – it never goes unnoticed.
Core Components:
Photoluminescent Pigments: 30% – Recharge in light, glow for hours
Retroreflective Microbeads: 20% – Bounce light directly back to source
Iridescent Flakes: 10% – Add visual punch under sunlight
Base Material: 40% – Tough and printable for long-lasting use
Where to use it:
Night cycling accessories – Make yourself seen
Safety gear prototypes – Reflective tools for visibility testing
Party/event props – Light up the night with flair
Fashion or cosplay – Wearable elements that glow and shimmer.
-
Click here to access our specialized TimeMass GPT Assistant. Just tell it your printer model and the TimeMass filament you're using—it will instantly recommend the exact parameters you need to start printing successfully.
Using a Bambu Lab printer?
Click here to download our updated Bambu Lab profile. All printing parameters are fully optimized and tested—just load the file and start printing.1. Introduction
These parameters are designed to help avoid printing issues; however, temperatures and speed timings can be adjusted based on your specific goals. For example, if you prefer a less rigid result, we recommend using a lower temperature. This section outlines a complete slicing and printing profile for TimeMass Stick & Glow, tailored for printers with a 0.8 mm nozzle. If the print is not being successful, please lower the nozzle temperature by 10°C and start over until an optimal print is achieved.While these examples were printed with a 0.8 mm nozzle, TimeMass can be used with any nozzle size. Please check the manual for printing parameters with all the other nozzle sizes.2. Temperature Settings
2.aNozzle Temperature: 240°C — Optimal for flowability while avoiding decomposition (which begins around 250°C).
2.bBed Temperature: 95°C — Ensures strong first-layer adhesion and prevents moisture bubbling.
2.cNozzle Temperature Range: 230–245°C — Timeplast melts around 165°C but prints best at 240°C for precise viscosity control.3. Cooling Settings
3.aNo Cooling for First Layers: 3 layers — Prevents shrinkage due to rapid cooling of moisture-rich filament.
3.bFan Minimum Speed: 0% for the first 100 seconds — Allows heat retention during early layers.
3.cFan Maximum Speed: 15% starting at 8 seconds — Avoids overcooling that can lead to warping.
3.dKeep Fan Always On: OFF — Allows vapor to escape and avoids internal fogging.
3.eSlow Down for Cooling: ON — Improves surface finish with controlled cooling.
3.fForce Cooling for Overhangs: OFF — Overcooling can deform bridges in Timeplast.
3.gFan for Overhangs: 15% — Only for essential cooling in complex areas.
3.hPre-Start Fan Time: 2 seconds — Minimizes pressure differential during the first layer.4. Volumetric Flow
4.aMax Volumetric Speed: 12 mm³/s — Based on a melt flow index of ~15 g/10min, allows high-speed printing.
4.bRamming Speed: 3 mm³/s — Prevents bubbles or popping from pressure spikes.5. Retraction and Flow
5.aRetraction Distance: 0.4 mm — Minimal retraction required for soft filaments to avoid stringing.
5.bRetraction Speed: 15 mm/s — Slow enough to avoid pulling molten plastic.
5.cPressure Advance: 0.05 — Compensates for nozzle lag at high flow rates.
5.dFlow Ratio: 92% — Slight under-extrusion avoids swelling and surface artifacts.6. Precision Settings
6.aGap Closing Radius: 0.1 mm — Tolerant of gaps in thicker walls.
6.bArc Fitting: ON — Reduces G-code size and smooths curve transitions.
6.cElephant Foot Compensation: 0.1 mm — Offsets squishing in the first layer caused by large bead sizes.7. Walls and Shells
7.aWall Loops: 2 — Minimum for strength when using a 0.8 mm nozzle.
7.bDetect Thin Walls: ON — Ensures tight geometries aren’t skipped.
7.cTop/Bottom Shell Layers: 3 — Provides good coverage; increase if watertightness is needed.
7.dTop/Bottom Thickness: 1.2 mm — Equals 1.5x the nozzle size for solid strength.
7.eTop/Bottom Pattern: Monotonic — Distributes tension evenly and improves surface finish.8. Geometry and Movement
8.aWall Order: Inner before Outer — Creates cleaner outer surfaces.
8.bInfill First: OFF — Maintains precise outer dimensions.
8.cSmooth Speed Transition: ON — Prevents ringing caused by abrupt speed changes.
8.dSmooth Coefficient: 80 — Ideal damping for soft materials.
8.eAvoid Crossing Wall: ON — Minimizes stringing across part walls.
8.fMax Detour for Crossing: 10 mm or 5% — Balances time with print cleanliness.9. Layer and Width Settings
9.aLayer Height: 0.3 mm — Optimal for strength and resolution using a 0.8 mm nozzle.
9.bInitial Layer Height: 0.35 mm — Slightly higher to improve adhesion.
9.cLine Widths (all): 0.8 mm — Matches nozzle diameter for consistent extrusion.10. Seam Settings
10.aSeam Position: Aligned or Back — Use aligned for mechanical consistency, back for visual appeal.
10.bSmart Scarf Seam: ON — Automatically adjusts seam location to reduce visual impact.
10.cSeam Angle: 155° — Standard seam angle for clean transitions.
10.dSeam Steps: 10 — Smooths seam path and improves visual finish.11. Infill Settings
11.aWall/Infill Overlap: 10% — Prevents infill from deforming soft exterior walls.
11.bInfill Combination: ON — Consolidates paths for efficiency.
11.cDetect Floating Shells: ON — Ensures unsupported vertical structures are printed reliably.
11.dSparse Infill Density: 20–25% — Balanced rigidity vs. material use.
11.eSparse Pattern: Grid — Stable and efficient for flexible geometries.12. Speed Settings
12.aTravel: 160 mm/s — Fast but safe against backlash.
12.bInitial Layer: 15 mm/s — Prevents nozzle from skimming and ensures bed adhesion.
12.cOuter Wall: 60 mm/s — Controlled speed for surface quality.
12.dInner Wall: 90 mm/s — Slightly faster without compromising control.
12.eSmall Perimeter: 35 mm/s — Reduced speed for detailed geometry.
12.fTop Surface: 40 mm/s — Improves finish on topmost layers.
12.gInfill: 100–120 mm/s — Takes advantage of high flowability.13. Acceleration Settings
13.aNormal Print: 2000 mm/s² — Prevents ringing in soft filaments.
13.bTravel: 4000 mm/s² — Enables fast movement without harsh transitions.
13.cInitial Layer: 300 mm/s² — Gentle movement prevents lifting from the bed.
13.dOuter Wall: 1500 mm/s² — Improves outer surface clarity.
13.eInner Wall: 2000 mm/s² — Balanced for structural components.
13.fTop Surface: 1500 mm/s² — Ensures smooth detailing.14. Adhesion and Brims
14.aSkirt Loops: 2 — Helps prime nozzle and start cleanly.
14.bBrim Width: 6 mm — Helps hold soft materials down.
14.cBrim Gap: 0.15 mm — Allows for easy removal without tearing.15. Prime Tower and Flush Settings
15.aPrime Tower: ON — Purges moisture and early flow inconsistencies.
15.bTower Width: 40 mm — Prevents collapse due to heat.
15.cBrim Width (Tower): 4 mm — Adds stability to the purge base.
15.dFlush Into Support: ON — Discards unwanted early flow safely.16. G-Code Start Script
M900 K0.05 ; Pressure Advance M106 S0 ; Fan off G92 E0 G1 E15 F300 ; purge line G92 E0
17. Additional Notes
17.aDry filament at 100°C for 2 hours before use.
17.bStore with desiccant.
17.cKeep extruder door open to allow vapor to escape.
17.dAvoid long dwell times at high temperatures.If you need print settings for other nozzle sizes, feel free to reach out to us at timeplast@timeplast.com — we’ll be happy to help.
Free U.S. standard shipping on orders of 5+ spools!
Custom colors for 5+ same-type spools’ orders
Light - Gen 2
-
TimeMass Light - Make It Glow Without Wiring a Small City
TimeMass Light works like optical fiber… if optical fiber decided to chill out and light up everything, not just one boring line. Instead of shooting light straight through like a laser pointer at a PowerPoint, this filament scatters and diffuses it across its entire body. Translation? The whole thing glows like it knows it’s being admired.
Here’s how the magic works (without the wand):
• Microstructured diffusion:
We pack the filament with microscopic voids, sneaky shifts in refractive index, and nanoparticles that scatter light like it owes them money.
• Selective diffraction:
Unlike transparent materials that pretend to be cool and just let light pass through, TimeMass Light stays interesting—spreading the glow evenly instead of making one pixel overheat with existential pressure.
• Smart light entry:
Want it to glow properly? Cut or sand the base flat. The smoother it is, the easier it is for your LED, flashlight, or candle (yes, we make those too) to pump light inside and let it party.
Polishing the entry point isn’t extra credit—it’s how you avoid “tiny flashlight trapped in plastic cube” vibes. The flatter and cleaner the surface, the better the filament does its thing: glowing like it was born to.
⸻
Stuff You Can Do With It (That Looks Cooler in the Dark):
• Low-energy lighting: Glowing structures that don’t need 47 LEDs and a power grid.
• Wearables: Print accessories that light up your outfit and make you visible to cars and confused party guests.
• Art & signage: Want a glowing logo with no wires? Done. Just don’t spell your name wrong.
• Emergency lighting: Self-lit exit signs for power outages, low-key apocalypses, or overly dramatic basements.
• Sci-fi layering experiments: Create semi-transparent, light-diffusing structures that make it look like you’re up to something.
-
Click here to access our specialized TimeMass GPT Assistant. Just tell it your printer model and the TimeMass filament you're using—it will instantly recommend the exact parameters you need to start printing successfully.
Using a Bambu Lab printer?
Click here to download our updated Bambu Lab profile. All printing parameters are fully optimized and tested—just load the file and start printing.1. Introduction
These parameters are designed to help avoid printing issues; however, temperatures and speed timings can be adjusted based on your specific goals. For example, if you prefer a less rigid result, we recommend using a lower temperature. This section outlines a complete slicing and printing profile for TimeMass Light, tailored for printers with a 0.8 mm nozzle. If the print is not being successful, please lower the nozzle temperature by 10°C and start over until an optimal print is achieved.While these examples were printed with a 0.8 mm nozzle, TimeMass can be used with any nozzle size. Please check the manual for printing parameters with all the other nozzle sizes.2. Temperature Settings
2.aNozzle Temperature: 240°C — Optimal for flowability while avoiding decomposition (which begins around 250°C).
2.bBed Temperature: 95°C — Ensures strong first-layer adhesion and prevents moisture bubbling.
2.cNozzle Temperature Range: 230–245°C — Timeplast melts around 165°C but prints best at 240°C for precise viscosity control.3. Cooling Settings
3.aNo Cooling for First Layers: 3 layers — Prevents shrinkage due to rapid cooling of moisture-rich filament.
3.bFan Minimum Speed: 0% for the first 100 seconds — Allows heat retention during early layers.
3.cFan Maximum Speed: 15% starting at 8 seconds — Avoids overcooling that can lead to warping.
3.dKeep Fan Always On: OFF — Allows vapor to escape and avoids internal fogging.
3.eSlow Down for Cooling: ON — Improves surface finish with controlled cooling.
3.fForce Cooling for Overhangs: OFF — Overcooling can deform bridges in Timeplast.
3.gFan for Overhangs: 15% — Only for essential cooling in complex areas.
3.hPre-Start Fan Time: 2 seconds — Minimizes pressure differential during the first layer.4. Volumetric Flow
4.aMax Volumetric Speed: 12 mm³/s — Based on a melt flow index of ~15 g/10min, allows high-speed printing.
4.bRamming Speed: 3 mm³/s — Prevents bubbles or popping from pressure spikes.5. Retraction and Flow
5.aRetraction Distance: 0.4 mm — Minimal retraction required for soft filaments to avoid stringing.
5.bRetraction Speed: 15 mm/s — Slow enough to avoid pulling molten plastic.
5.cPressure Advance: 0.05 — Compensates for nozzle lag at high flow rates.
5.dFlow Ratio: 92% — Slight under-extrusion avoids swelling and surface artifacts.6. Precision Settings
6.aGap Closing Radius: 0.1 mm — Tolerant of gaps in thicker walls.
6.bArc Fitting: ON — Reduces G-code size and smooths curve transitions.
6.cElephant Foot Compensation: 0.1 mm — Offsets squishing in the first layer caused by large bead sizes.7. Walls and Shells
7.aWall Loops: 2 — Minimum for strength when using a 0.8 mm nozzle.
7.bDetect Thin Walls: ON — Ensures tight geometries aren’t skipped.
7.cTop/Bottom Shell Layers: 3 — Provides good coverage; increase if watertightness is needed.
7.dTop/Bottom Thickness: 1.2 mm — Equals 1.5x the nozzle size for solid strength.
7.eTop/Bottom Pattern: Monotonic — Distributes tension evenly and improves surface finish.8. Geometry and Movement
8.aWall Order: Inner before Outer — Creates cleaner outer surfaces.
8.bInfill First: OFF — Maintains precise outer dimensions.
8.cSmooth Speed Transition: ON — Prevents ringing caused by abrupt speed changes.
8.dSmooth Coefficient: 80 — Ideal damping for soft materials.
8.eAvoid Crossing Wall: ON — Minimizes stringing across part walls.
8.fMax Detour for Crossing: 10 mm or 5% — Balances time with print cleanliness.9. Layer and Width Settings
9.aLayer Height: 0.3 mm — Optimal for strength and resolution using a 0.8 mm nozzle.
9.bInitial Layer Height: 0.35 mm — Slightly higher to improve adhesion.
9.cLine Widths (all): 0.8 mm — Matches nozzle diameter for consistent extrusion.10. Seam Settings
10.aSeam Position: Aligned or Back — Use aligned for mechanical consistency, back for visual appeal.
10.bSmart Scarf Seam: ON — Automatically adjusts seam location to reduce visual impact.
10.cSeam Angle: 155° — Standard seam angle for clean transitions.
10.dSeam Steps: 10 — Smooths seam path and improves visual finish.11. Infill Settings
11.aWall/Infill Overlap: 10% — Prevents infill from deforming soft exterior walls.
11.bInfill Combination: ON — Consolidates paths for efficiency.
11.cDetect Floating Shells: ON — Ensures unsupported vertical structures are printed reliably.
11.dSparse Infill Density: 20–25% — Balanced rigidity vs. material use.
11.eSparse Pattern: Grid — Stable and efficient for flexible geometries.12. Speed Settings
12.aTravel: 160 mm/s — Fast but safe against backlash.
12.bInitial Layer: 15 mm/s — Prevents nozzle from skimming and ensures bed adhesion.
12.cOuter Wall: 60 mm/s — Controlled speed for surface quality.
12.dInner Wall: 90 mm/s — Slightly faster without compromising control.
12.eSmall Perimeter: 35 mm/s — Reduced speed for detailed geometry.
12.fTop Surface: 40 mm/s — Improves finish on topmost layers.
12.gInfill: 100–120 mm/s — Takes advantage of high flowability.13. Acceleration Settings
13.aNormal Print: 2000 mm/s² — Prevents ringing in soft filaments.
13.bTravel: 4000 mm/s² — Enables fast movement without harsh transitions.
13.cInitial Layer: 300 mm/s² — Gentle movement prevents lifting from the bed.
13.dOuter Wall: 1500 mm/s² — Improves outer surface clarity.
13.eInner Wall: 2000 mm/s² — Balanced for structural components.
13.fTop Surface: 1500 mm/s² — Ensures smooth detailing.14. Adhesion and Brims
14.aSkirt Loops: 2 — Helps prime nozzle and start cleanly.
14.bBrim Width: 6 mm — Helps hold soft materials down.
14.cBrim Gap: 0.15 mm — Allows for easy removal without tearing.15. Prime Tower and Flush Settings
15.aPrime Tower: ON — Purges moisture and early flow inconsistencies.
15.bTower Width: 40 mm — Prevents collapse due to heat.
15.cBrim Width (Tower): 4 mm — Adds stability to the purge base.
15.dFlush Into Support: ON — Discards unwanted early flow safely.16. G-Code Start Script
M900 K0.05 ; Pressure Advance M106 S0 ; Fan off G92 E0 G1 E15 F300 ; purge line G92 E0
17. Additional Notes
17.aDry filament at 100°C for 2 hours before use.
17.bStore with desiccant.
17.cKeep extruder door open to allow vapor to escape.
17.dAvoid long dwell times at high temperatures.If you need print settings for other nozzle sizes, feel free to reach out to us at timeplast@timeplast.com — we’ll be happy to help.
You can also get instant support through our dedicated ChatGPT assistant here:https://chatgpt.com/g/g-6823924241cc8191bbabcf0bc6523e3f-timemass-4d-printing🚀
Free U.S. standard shipping on orders of 5+ spools!
Custom colors for 5+ same-type spools’ orders
Stick, Spark & Glow
-
A triple-visibility filament that glows in the dark, reflects light, and sparkles in daylight. Made for visibility, safety, and unapologetic flair. If you want your prints to pop—day or night—this is your go-to.
Shine. Reflect. Dazzle.
How it works:
Multiple light-responsive additives are embedded within a durable polymer carrier, activated by natural or artificial light.
Day or night – it never goes unnoticed.
Core Components:
Photoluminescent Pigments: 30% – Recharge in light, glow for hours
Retroreflective Microbeads: 20% – Bounce light directly back to source
Iridescent Flakes: 10% – Add visual punch under sunlight
Base Material: 40% – Tough and printable for long-lasting use
Where to use it:
Night cycling accessories – Make yourself seen
Safety gear prototypes – Reflective tools for visibility testing
Party/event props – Light up the night with flair
Fashion or cosplay – Wearable elements that glow and shimmer
-
Click here to access our specialized TimeMass GPT Assistant. Just tell it your printer model and the TimeMass filament you're using—it will instantly recommend the exact parameters you need to start printing successfully.
Using a Bambu Lab printer?
Click here to download our updated Bambu Lab profile. All printing parameters are fully optimized and tested—just load the file and start printing.1. Introduction
These parameters are designed to help avoid printing issues; however, temperatures and speed timings can be adjusted based on your specific goals. For example, if you prefer a less rigid result, we recommend using a lower temperature. This section outlines a complete slicing and printing profile for TimeMass Active, tailored for printers with a 0.8 mm nozzle. If the print is not being successful, please lower the nozzle temperature by 10°C and start over until an optimal print is achieved.While these examples were printed with a 0.8 mm nozzle, TimeMass can be used with any nozzle size. Please check the manual for printing parameters with all the other nozzle sizes.2. Temperature Settings
2.aNozzle Temperature: 240°C — Optimal for flowability while avoiding decomposition (which begins around 250°C).
2.bBed Temperature: 95°C — Ensures strong first-layer adhesion and prevents moisture bubbling.
2.cNozzle Temperature Range: 230–245°C — Timeplast melts around 165°C but prints best at 240°C for precise viscosity control.3. Cooling Settings
3.aNo Cooling for First Layers: 3 layers — Prevents shrinkage due to rapid cooling of moisture-rich filament.
3.bFan Minimum Speed: 0% for the first 100 seconds — Allows heat retention during early layers.
3.cFan Maximum Speed: 15% starting at 8 seconds — Avoids overcooling that can lead to warping.
3.dKeep Fan Always On: OFF — Allows vapor to escape and avoids internal fogging.
3.eSlow Down for Cooling: ON — Improves surface finish with controlled cooling.
3.fForce Cooling for Overhangs: OFF — Overcooling can deform bridges in Timeplast.
3.gFan for Overhangs: 15% — Only for essential cooling in complex areas.
3.hPre-Start Fan Time: 2 seconds — Minimizes pressure differential during the first layer.4. Volumetric Flow
4.aMax Volumetric Speed: 12 mm³/s — Based on a melt flow index of ~15 g/10min, allows high-speed printing.
4.bRamming Speed: 3 mm³/s — Prevents bubbles or popping from pressure spikes.5. Retraction and Flow
5.aRetraction Distance: 0.4 mm — Minimal retraction required for soft filaments to avoid stringing.
5.bRetraction Speed: 15 mm/s — Slow enough to avoid pulling molten plastic.
5.cPressure Advance: 0.05 — Compensates for nozzle lag at high flow rates.
5.dFlow Ratio: 92% — Slight under-extrusion avoids swelling and surface artifacts.6. Precision Settings
6.aGap Closing Radius: 0.1 mm — Tolerant of gaps in thicker walls.
6.bArc Fitting: ON — Reduces G-code size and smooths curve transitions.
6.cElephant Foot Compensation: 0.1 mm — Offsets squishing in the first layer caused by large bead sizes.7. Walls and Shells
7.aWall Loops: 2 — Minimum for strength when using a 0.8 mm nozzle.
7.bDetect Thin Walls: ON — Ensures tight geometries aren’t skipped.
7.cTop/Bottom Shell Layers: 3 — Provides good coverage; increase if watertightness is needed.
7.dTop/Bottom Thickness: 1.2 mm — Equals 1.5x the nozzle size for solid strength.
7.eTop/Bottom Pattern: Monotonic — Distributes tension evenly and improves surface finish.8. Geometry and Movement
8.aWall Order: Inner before Outer — Creates cleaner outer surfaces.
8.bInfill First: OFF — Maintains precise outer dimensions.
8.cSmooth Speed Transition: ON — Prevents ringing caused by abrupt speed changes.
8.dSmooth Coefficient: 80 — Ideal damping for soft materials.
8.eAvoid Crossing Wall: ON — Minimizes stringing across part walls.
8.fMax Detour for Crossing: 10 mm or 5% — Balances time with print cleanliness.9. Layer and Width Settings
9.aLayer Height: 0.3 mm — Optimal for strength and resolution using a 0.8 mm nozzle.
9.bInitial Layer Height: 0.35 mm — Slightly higher to improve adhesion.
9.cLine Widths (all): 0.8 mm — Matches nozzle diameter for consistent extrusion.10. Seam Settings
10.aSeam Position: Aligned or Back — Use aligned for mechanical consistency, back for visual appeal.
10.bSmart Scarf Seam: ON — Automatically adjusts seam location to reduce visual impact.
10.cSeam Angle: 155° — Standard seam angle for clean transitions.
10.dSeam Steps: 10 — Smooths seam path and improves visual finish.11. Infill Settings
11.aWall/Infill Overlap: 10% — Prevents infill from deforming soft exterior walls.
11.bInfill Combination: ON — Consolidates paths for efficiency.
11.cDetect Floating Shells: ON — Ensures unsupported vertical structures are printed reliably.
11.dSparse Infill Density: 20–25% — Balanced rigidity vs. material use.
11.eSparse Pattern: Grid — Stable and efficient for flexible geometries.12. Speed Settings
12.aTravel: 160 mm/s — Fast but safe against backlash.
12.bInitial Layer: 15 mm/s — Prevents nozzle from skimming and ensures bed adhesion.
12.cOuter Wall: 60 mm/s — Controlled speed for surface quality.
12.dInner Wall: 90 mm/s — Slightly faster without compromising control.
12.eSmall Perimeter: 35 mm/s — Reduced speed for detailed geometry.
12.fTop Surface: 40 mm/s — Improves finish on topmost layers.
12.gInfill: 100–120 mm/s — Takes advantage of high flowability.13. Acceleration Settings
13.aNormal Print: 2000 mm/s² — Prevents ringing in soft filaments.
13.bTravel: 4000 mm/s² — Enables fast movement without harsh transitions.
13.cInitial Layer: 300 mm/s² — Gentle movement prevents lifting from the bed.
13.dOuter Wall: 1500 mm/s² — Improves outer surface clarity.
13.eInner Wall: 2000 mm/s² — Balanced for structural components.
13.fTop Surface: 1500 mm/s² — Ensures smooth detailing.14. Adhesion and Brims
14.aSkirt Loops: 2 — Helps prime nozzle and start cleanly.
14.bBrim Width: 6 mm — Helps hold soft materials down.
14.cBrim Gap: 0.15 mm — Allows for easy removal without tearing.15. Prime Tower and Flush Settings
15.aPrime Tower: ON — Purges moisture and early flow inconsistencies.
15.bTower Width: 40 mm — Prevents collapse due to heat.
15.cBrim Width (Tower): 4 mm — Adds stability to the purge base.
15.dFlush Into Support: ON — Discards unwanted early flow safely.16. G-Code Start Script
M900 K0.05 ; Pressure Advance M106 S0 ; Fan off G92 E0 G1 E15 F300 ; purge line G92 E0
17. Additional Notes
17.aDry filament at 100°C for 2 hours before use.
17.bStore with desiccant.
17.cKeep extruder door open to allow vapor to escape.
17.dAvoid long dwell times at high temperatures.If you need print settings for other nozzle sizes, feel free to reach out to us at timeplast@timeplast.com — we’ll be happy to help.
Free U.S. standard shipping on orders of 5+ spools!
Custom colors for 5+ same-type spools’ orders
UV Reveal
-
A stealthy, light-shifting filament that looks neutral in daylight—but under UV or blacklight? It glows a vivid, electric purple. Engineered with photo-reactive dyes, it's perfect for hidden messages, party prints, or security-related applications.
Plain by day. Purple by blacklight.
How it works:
UV-reactive compounds stay invisible in visible light, but emit bright fluorescence under ultraviolet light sources.
No batteries. No electronics. Just physics and photochemistry.
Core Composition:
UV-reactive Fluorophores: 18% – Designed for high-contrast glow
Neutral Carrier Polymer: 82% – Maintains daylight camouflage
Where to use it:
Secret messages & codes – Hide visual data in plain sight
Escape rooms & puzzles – Reveal clues only under UV
Event décor – Prints that transform under party lighting
Counterfeit deterrents – Secure packaging and labels
-
Click here to access our specialized TimeMass GPT Assistant. Just tell it your printer model and the TimeMass filament you're using—it will instantly recommend the exact parameters you need to start printing successfully.
Using a Bambu Lab printer?
Click here to download our updated Bambu Lab profile. All printing parameters are fully optimized and tested—just load the file and start printing.1. Introduction
These parameters are designed to help avoid printing issues; however, temperatures and speed timings can be adjusted based on your specific goals. For example, if you prefer a less rigid result, we recommend using a lower temperature. This section outlines a complete slicing and printing profile for TimeMass UV tailored for printers with a 0.8 mm nozzle. If the print is not being successful, please lower the nozzle temperature by 10°C and start over until an optimal print is achieved.While these examples were printed with a 0.8 mm nozzle, TimeMass can be used with any nozzle size. Please check the manual for printing parameters with all the other nozzle sizes.2. Temperature Settings
2.aNozzle Temperature: 240°C — Optimal for flowability while avoiding decomposition (which begins around 250°C).
2.bBed Temperature: 95°C — Ensures strong first-layer adhesion and prevents moisture bubbling.
2.cNozzle Temperature Range: 230–245°C — Timeplast melts around 165°C but prints best at 240°C for precise viscosity control.3. Cooling Settings
3.aNo Cooling for First Layers: 3 layers — Prevents shrinkage due to rapid cooling of moisture-rich filament.
3.bFan Minimum Speed: 0% for the first 100 seconds — Allows heat retention during early layers.
3.cFan Maximum Speed: 15% starting at 8 seconds — Avoids overcooling that can lead to warping.
3.dKeep Fan Always On: OFF — Allows vapor to escape and avoids internal fogging.
3.eSlow Down for Cooling: ON — Improves surface finish with controlled cooling.
3.fForce Cooling for Overhangs: OFF — Overcooling can deform bridges in Timeplast.
3.gFan for Overhangs: 15% — Only for essential cooling in complex areas.
3.hPre-Start Fan Time: 2 seconds — Minimizes pressure differential during the first layer.4. Volumetric Flow
4.aMax Volumetric Speed: 12 mm³/s — Based on a melt flow index of ~15 g/10min, allows high-speed printing.
4.bRamming Speed: 3 mm³/s — Prevents bubbles or popping from pressure spikes.5. Retraction and Flow
5.aRetraction Distance: 0.4 mm — Minimal retraction required for soft filaments to avoid stringing.
5.bRetraction Speed: 15 mm/s — Slow enough to avoid pulling molten plastic.
5.cPressure Advance: 0.05 — Compensates for nozzle lag at high flow rates.
5.dFlow Ratio: 92% — Slight under-extrusion avoids swelling and surface artifacts.6. Precision Settings
6.aGap Closing Radius: 0.1 mm — Tolerant of gaps in thicker walls.
6.bArc Fitting: ON — Reduces G-code size and smooths curve transitions.
6.cElephant Foot Compensation: 0.1 mm — Offsets squishing in the first layer caused by large bead sizes.7. Walls and Shells
7.aWall Loops: 2 — Minimum for strength when using a 0.8 mm nozzle.
7.bDetect Thin Walls: ON — Ensures tight geometries aren’t skipped.
7.cTop/Bottom Shell Layers: 3 — Provides good coverage; increase if watertightness is needed.
7.dTop/Bottom Thickness: 1.2 mm — Equals 1.5x the nozzle size for solid strength.
7.eTop/Bottom Pattern: Monotonic — Distributes tension evenly and improves surface finish.8. Geometry and Movement
8.aWall Order: Inner before Outer — Creates cleaner outer surfaces.
8.bInfill First: OFF — Maintains precise outer dimensions.
8.cSmooth Speed Transition: ON — Prevents ringing caused by abrupt speed changes.
8.dSmooth Coefficient: 80 — Ideal damping for soft materials.
8.eAvoid Crossing Wall: ON — Minimizes stringing across part walls.
8.fMax Detour for Crossing: 10 mm or 5% — Balances time with print cleanliness.9. Layer and Width Settings
9.aLayer Height: 0.3 mm — Optimal for strength and resolution using a 0.8 mm nozzle.
9.bInitial Layer Height: 0.35 mm — Slightly higher to improve adhesion.
9.cLine Widths (all): 0.8 mm — Matches nozzle diameter for consistent extrusion.10. Seam Settings
10.aSeam Position: Aligned or Back — Use aligned for mechanical consistency, back for visual appeal.
10.bSmart Scarf Seam: ON — Automatically adjusts seam location to reduce visual impact.
10.cSeam Angle: 155° — Standard seam angle for clean transitions.
10.dSeam Steps: 10 — Smooths seam path and improves visual finish.11. Infill Settings
11.aWall/Infill Overlap: 10% — Prevents infill from deforming soft exterior walls.
11.bInfill Combination: ON — Consolidates paths for efficiency.
11.cDetect Floating Shells: ON — Ensures unsupported vertical structures are printed reliably.
11.dSparse Infill Density: 20–25% — Balanced rigidity vs. material use.
11.eSparse Pattern: Grid — Stable and efficient for flexible geometries.12. Speed Settings
12.aTravel: 160 mm/s — Fast but safe against backlash.
12.bInitial Layer: 15 mm/s — Prevents nozzle from skimming and ensures bed adhesion.
12.cOuter Wall: 60 mm/s — Controlled speed for surface quality.
12.dInner Wall: 90 mm/s — Slightly faster without compromising control.
12.eSmall Perimeter: 35 mm/s — Reduced speed for detailed geometry.
12.fTop Surface: 40 mm/s — Improves finish on topmost layers.
12.gInfill: 100–120 mm/s — Takes advantage of high flowability.13. Acceleration Settings
13.aNormal Print: 2000 mm/s² — Prevents ringing in soft filaments.
13.bTravel: 4000 mm/s² — Enables fast movement without harsh transitions.
13.cInitial Layer: 300 mm/s² — Gentle movement prevents lifting from the bed.
13.dOuter Wall: 1500 mm/s² — Improves outer surface clarity.
13.eInner Wall: 2000 mm/s² — Balanced for structural components.
13.fTop Surface: 1500 mm/s² — Ensures smooth detailing.14. Adhesion and Brims
14.aSkirt Loops: 2 — Helps prime nozzle and start cleanly.
14.bBrim Width: 6 mm — Helps hold soft materials down.
14.cBrim Gap: 0.15 mm — Allows for easy removal without tearing.15. Prime Tower and Flush Settings
15.aPrime Tower: ON — Purges moisture and early flow inconsistencies.
15.bTower Width: 40 mm — Prevents collapse due to heat.
15.cBrim Width (Tower): 4 mm — Adds stability to the purge base.
15.dFlush Into Support: ON — Discards unwanted early flow safely.16. G-Code Start Script
M900 K0.05 ; Pressure Advance M106 S0 ; Fan off G92 E0 G1 E15 F300 ; purge line G92 E0
17. Additional Notes
17.aDry filament at 100°C for 2 hours before use.
17.bStore with desiccant.
17.cKeep extruder door open to allow vapor to escape.
17.dAvoid long dwell times at high temperatures.If you need print settings for other nozzle sizes, feel free to reach out to us at timeplast@timeplast.com — we’ll be happy to help.
Free U.S. standard shipping on orders of 5+ spools!
Custom colors for 5+ same-type spools’ orders
Biohackers
Bug Attractor
-
Designed for controlled bug attraction, this filament is infused with maltodextrin, sugars, milk proteins, and yeast extract. Ideal for DIY insect farms, traps, or study tools—it draws in scavengers, flyers, and larvae-feeders.
From ant trails to fly swarms, this filament brings the bugs to you.
How it works:
Water-activated compounds release food-scent molecules gradually, maintaining consistent attraction without spoilage.
Insects love it. You control the design.
Core Attractants:
Glucose + Fructose + Maltodextrin – Sweet lures for cockroaches, ants, and flies
Milk Proteins + Yeast Extract – Attract egg-laying insects and larval feeders
Where to use it:
Insect farming – Feed black soldier flies, ants, beetles
Bug behavior studies – Controlled environments for research
Custom traps – Build your own lure stations
Garden insect monitoring
-
Click here to access our specialized TimeMass GPT Assistant. Just tell it your printer model and the TimeMass filament you're using—it will instantly recommend the exact parameters you need to start printing successfully.
Using a Bambu Lab printer?
Click here to download our updated Bambu Lab profile. All printing parameters are fully optimized and tested—just load the file and start printing.1. Introduction
These parameters are designed to help avoid printing issues; however, temperatures and speed timings can be adjusted based on your specific goals. For example, if you prefer a less rigid result, we recommend using a lower temperature. This section outlines a complete slicing and printing profile for TimeMass Bug Attractor, tailored for printers with a 0.8 mm nozzle. If the print is not being successful, please lower the nozzle temperature by 10°C and start over until an optimal print is achieved. While these examples were printed with a 0.8 mm nozzle, TimeMass can be used with any nozzle size. Please check the manual for printing parameters with all the other nozzle sizes.2. Temperature Settings
2.aNozzle Temperature: 240°C — Optimal for flowability while avoiding decomposition (which begins around 250°C).
2.bBed Temperature: 95°C — Ensures strong first-layer adhesion and prevents moisture bubbling.
2.cNozzle Temperature Range: 230–245°C — Timeplast melts around 165°C but prints best at 240°C for precise viscosity control.3. Cooling Settings
3.aNo Cooling for First Layers: 3 layers — Prevents shrinkage due to rapid cooling of moisture-rich filament.
3.bFan Minimum Speed: 0% for the first 100 seconds — Allows heat retention during early layers.
3.cFan Maximum Speed: 15% starting at 8 seconds — Avoids overcooling that can lead to warping.
3.dKeep Fan Always On: OFF — Allows vapor to escape and avoids internal fogging.
3.eSlow Down for Cooling: ON — Improves surface finish with controlled cooling.
3.fForce Cooling for Overhangs: OFF — Overcooling can deform bridges in Timeplast.
3.gFan for Overhangs: 15% — Only for essential cooling in complex areas.
3.hPre-Start Fan Time: 2 seconds — Minimizes pressure differential during the first layer.4. Volumetric Flow
4.aMax Volumetric Speed: 12 mm³/s — Based on a melt flow index of ~15 g/10min, allows high-speed printing.
4.bRamming Speed: 3 mm³/s — Prevents bubbles or popping from pressure spikes.5. Retraction and Flow
5.aRetraction Distance: 0.4 mm — Minimal retraction required for soft filaments to avoid stringing.
5.bRetraction Speed: 15 mm/s — Slow enough to avoid pulling molten plastic.
5.cPressure Advance: 0.05 — Compensates for nozzle lag at high flow rates.
5.dFlow Ratio: 92% — Slight under-extrusion avoids swelling and surface artifacts.6. Precision Settings
6.aGap Closing Radius: 0.1 mm — Tolerant of gaps in thicker walls.
6.bArc Fitting: ON — Reduces G-code size and smooths curve transitions.
6.cElephant Foot Compensation: 0.1 mm — Offsets squishing in the first layer caused by large bead sizes.7. Walls and Shells
7.aWall Loops: 2 — Minimum for strength when using a 0.8 mm nozzle.
7.bDetect Thin Walls: ON — Ensures tight geometries aren’t skipped.
7.cTop/Bottom Shell Layers: 3 — Provides good coverage; increase if watertightness is needed.
7.dTop/Bottom Thickness: 1.2 mm — Equals 1.5x the nozzle size for solid strength.
7.eTop/Bottom Pattern: Monotonic — Distributes tension evenly and improves surface finish.8. Geometry and Movement
8.aWall Order: Inner before Outer — Creates cleaner outer surfaces.
8.bInfill First: OFF — Maintains precise outer dimensions.
8.cSmooth Speed Transition: ON — Prevents ringing caused by abrupt speed changes.
8.dSmooth Coefficient: 80 — Ideal damping for soft materials.
8.eAvoid Crossing Wall: ON — Minimizes stringing across part walls.
8.fMax Detour for Crossing: 10 mm or 5% — Balances time with print cleanliness.9. Layer and Width Settings
9.aLayer Height: 0.3 mm — Optimal for strength and resolution using a 0.8 mm nozzle.
9.bInitial Layer Height: 0.35 mm — Slightly higher to improve adhesion.
9.cLine Widths (all): 0.8 mm — Matches nozzle diameter for consistent extrusion.10. Seam Settings
10.aSeam Position: Aligned or Back — Use aligned for mechanical consistency, back for visual appeal.
10.bSmart Scarf Seam: ON — Automatically adjusts seam location to reduce visual impact.
10.cSeam Angle: 155° — Standard seam angle for clean transitions.
10.dSeam Steps: 10 — Smooths seam path and improves visual finish.11. Infill Settings
11.aWall/Infill Overlap: 10% — Prevents infill from deforming soft exterior walls.
11.bInfill Combination: ON — Consolidates paths for efficiency.
11.cDetect Floating Shells: ON — Ensures unsupported vertical structures are printed reliably.
11.dSparse Infill Density: 20–25% — Balanced rigidity vs. material use.
11.eSparse Pattern: Grid — Stable and efficient for flexible geometries.12. Speed Settings
12.aTravel: 160 mm/s — Fast but safe against backlash.
12.bInitial Layer: 15 mm/s — Prevents nozzle from skimming and ensures bed adhesion.
12.cOuter Wall: 60 mm/s — Controlled speed for surface quality.
12.dInner Wall: 90 mm/s — Slightly faster without compromising control.
12.eSmall Perimeter: 35 mm/s — Reduced speed for detailed geometry.
12.fTop Surface: 40 mm/s — Improves finish on topmost layers.
12.gInfill: 100–120 mm/s — Takes advantage of high flowability.13. Acceleration Settings
13.aNormal Print: 2000 mm/s² — Prevents ringing in soft filaments.
13.bTravel: 4000 mm/s² — Enables fast movement without harsh transitions.
13.cInitial Layer: 300 mm/s² — Gentle movement prevents lifting from the bed.
13.dOuter Wall: 1500 mm/s² — Improves outer surface clarity.
13.eInner Wall: 2000 mm/s² — Balanced for structural components.
13.fTop Surface: 1500 mm/s² — Ensures smooth detailing.14. Adhesion and Brims
14.aSkirt Loops: 2 — Helps prime nozzle and start cleanly.
14.bBrim Width: 6 mm — Helps hold soft materials down.
14.cBrim Gap: 0.15 mm — Allows for easy removal without tearing.15. Prime Tower and Flush Settings
15.aPrime Tower: ON — Purges moisture and early flow inconsistencies.
15.bTower Width: 40 mm — Prevents collapse due to heat.
15.cBrim Width (Tower): 4 mm — Adds stability to the purge base.
15.dFlush Into Support: ON — Discards unwanted early flow safely.16. G-Code Start Script
M900 K0.05 ; Pressure Advance M106 S0 ; Fan off G92 E0 G1 E15 F300 ; purge line G92 E0
17. Additional Notes
17.aDry filament at 100°C for 2 hours before use.
17.bStore with desiccant.
17.cKeep extruder door open to allow vapor to escape.
17.dAvoid long dwell times at high temperatures.If you need print settings for other nozzle sizes, feel free to reach out to us at timeplast@timeplast.com — we’ll be happy to help.
Free U.S. standard shipping on orders of 5+ spools!
Custom colors for 5+ same-type spools’ orders
Bug Killer
-
This bug-busting filament is loaded with slow-release diatomaceous earth (silicon dioxide) and built for safe, chemical-free pest control. When printed, it acts as a micro-abrasive that physically damages insect exoskeletons upon contact.
No poison. No smell. Just mechanical insect control.
How it works:
Humidity-activated release combined with rough surfaces deliver a continuous anti-insect effect.
Kills roaches, fleas, ants, bedbugs, silverfish—and keeps working for weeks.
Core Material:
Diatomaceous Earth: 35% – Sharp, fine particles destroy insect shells
Hydrophilic Matrix: 65% – Activates in moist environments for better coverage
Where to use it:
Indoor pest control – Line baseboards, under sinks, behind fridges
Garden bug shields – Safe for organic gardening (OMRI listed)
Pet-safe zones – Create custom traps or feeders
-
Click here to access our specialized TimeMass GPT Assistant. Just tell it your printer model and the TimeMass filament you're using—it will instantly recommend the exact parameters you need to start printing successfully.
Using a Bambu Lab printer?
Click here to download our updated Bambu Lab profile. All printing parameters are fully optimized and tested—just load the file and start printing.1. Introduction
These parameters are designed to help avoid printing issues; however, temperatures and speed timings can be adjusted based on your specific goals. For example, if you prefer a less rigid result, we recommend using a lower temperature. This section outlines a complete slicing and printing profile for TimeMass Bug Killer, tailored for printers with a 0.8 mm nozzle. If the print is not being successful, please lower the nozzle temperature by 10°C and start over until an optimal print is achieved. While these examples were printed with a 0.8 mm nozzle, TimeMass can be used with any nozzle size. Please check the manual for printing parameters with all the other nozzle sizes.2. Temperature Settings
2.aNozzle Temperature: 240°C — Optimal for flowability while avoiding decomposition (which begins around 250°C).
2.bBed Temperature: 95°C — Ensures strong first-layer adhesion and prevents moisture bubbling.
2.cNozzle Temperature Range: 230–245°C — Timeplast melts around 165°C but prints best at 240°C for precise viscosity control.3. Cooling Settings
3.aNo Cooling for First Layers: 3 layers — Prevents shrinkage due to rapid cooling of moisture-rich filament.
3.bFan Minimum Speed: 0% for the first 100 seconds — Allows heat retention during early layers.
3.cFan Maximum Speed: 15% starting at 8 seconds — Avoids overcooling that can lead to warping.
3.dKeep Fan Always On: OFF — Allows vapor to escape and avoids internal fogging.
3.eSlow Down for Cooling: ON — Improves surface finish with controlled cooling.
3.fForce Cooling for Overhangs: OFF — Overcooling can deform bridges in Timeplast.
3.gFan for Overhangs: 15% — Only for essential cooling in complex areas.
3.hPre-Start Fan Time: 2 seconds — Minimizes pressure differential during the first layer.4. Volumetric Flow
4.aMax Volumetric Speed: 12 mm³/s — Based on a melt flow index of ~15 g/10min, allows high-speed printing.
4.bRamming Speed: 3 mm³/s — Prevents bubbles or popping from pressure spikes.5. Retraction and Flow
5.aRetraction Distance: 0.4 mm — Minimal retraction required for soft filaments to avoid stringing.
5.bRetraction Speed: 15 mm/s — Slow enough to avoid pulling molten plastic.
5.cPressure Advance: 0.05 — Compensates for nozzle lag at high flow rates.
5.dFlow Ratio: 92% — Slight under-extrusion avoids swelling and surface artifacts.6. Precision Settings
6.aGap Closing Radius: 0.1 mm — Tolerant of gaps in thicker walls.
6.bArc Fitting: ON — Reduces G-code size and smooths curve transitions.
6.cElephant Foot Compensation: 0.1 mm — Offsets squishing in the first layer caused by large bead sizes.7. Walls and Shells
7.aWall Loops: 2 — Minimum for strength when using a 0.8 mm nozzle.
7.bDetect Thin Walls: ON — Ensures tight geometries aren’t skipped.
7.cTop/Bottom Shell Layers: 3 — Provides good coverage; increase if watertightness is needed.
7.dTop/Bottom Thickness: 1.2 mm — Equals 1.5x the nozzle size for solid strength.
7.eTop/Bottom Pattern: Monotonic — Distributes tension evenly and improves surface finish.8. Geometry and Movement
8.aWall Order: Inner before Outer — Creates cleaner outer surfaces.
8.bInfill First: OFF — Maintains precise outer dimensions.
8.cSmooth Speed Transition: ON — Prevents ringing caused by abrupt speed changes.
8.dSmooth Coefficient: 80 — Ideal damping for soft materials.
8.eAvoid Crossing Wall: ON — Minimizes stringing across part walls.
8.fMax Detour for Crossing: 10 mm or 5% — Balances time with print cleanliness.9. Layer and Width Settings
9.aLayer Height: 0.3 mm — Optimal for strength and resolution using a 0.8 mm nozzle.
9.bInitial Layer Height: 0.35 mm — Slightly higher to improve adhesion.
9.cLine Widths (all): 0.8 mm — Matches nozzle diameter for consistent extrusion.10. Seam Settings
10.aSeam Position: Aligned or Back — Use aligned for mechanical consistency, back for visual appeal.
10.bSmart Scarf Seam: ON — Automatically adjusts seam location to reduce visual impact.
10.cSeam Angle: 155° — Standard seam angle for clean transitions.
10.dSeam Steps: 10 — Smooths seam path and improves visual finish.11. Infill Settings
11.aWall/Infill Overlap: 10% — Prevents infill from deforming soft exterior walls.
11.bInfill Combination: ON — Consolidates paths for efficiency.
11.cDetect Floating Shells: ON — Ensures unsupported vertical structures are printed reliably.
11.dSparse Infill Density: 20–25% — Balanced rigidity vs. material use.
11.eSparse Pattern: Grid — Stable and efficient for flexible geometries.12. Speed Settings
12.aTravel: 160 mm/s — Fast but safe against backlash.
12.bInitial Layer: 15 mm/s — Prevents nozzle from skimming and ensures bed adhesion.
12.cOuter Wall: 60 mm/s — Controlled speed for surface quality.
12.dInner Wall: 90 mm/s — Slightly faster without compromising control.
12.eSmall Perimeter: 35 mm/s — Reduced speed for detailed geometry.
12.fTop Surface: 40 mm/s — Improves finish on topmost layers.
12.gInfill: 100–120 mm/s — Takes advantage of high flowability.13. Acceleration Settings
13.aNormal Print: 2000 mm/s² — Prevents ringing in soft filaments.
13.bTravel: 4000 mm/s² — Enables fast movement without harsh transitions.
13.cInitial Layer: 300 mm/s² — Gentle movement prevents lifting from the bed.
13.dOuter Wall: 1500 mm/s² — Improves outer surface clarity.
13.eInner Wall: 2000 mm/s² — Balanced for structural components.
13.fTop Surface: 1500 mm/s² — Ensures smooth detailing.14. Adhesion and Brims
14.aSkirt Loops: 2 — Helps prime nozzle and start cleanly.
14.bBrim Width: 6 mm — Helps hold soft materials down.
14.cBrim Gap: 0.15 mm — Allows for easy removal without tearing.15. Prime Tower and Flush Settings
15.aPrime Tower: ON — Purges moisture and early flow inconsistencies.
15.bTower Width: 40 mm — Prevents collapse due to heat.
15.cBrim Width (Tower): 4 mm — Adds stability to the purge base.
15.dFlush Into Support: ON — Discards unwanted early flow safely.16. G-Code Start Script
M900 K0.05 ; Pressure Advance M106 S0 ; Fan off G92 E0 G1 E15 F300 ; purge line G92 E0
17. Additional Notes
17.aDry filament at 100°C for 2 hours before use.
17.bStore with desiccant.
17.cKeep extruder door open to allow vapor to escape.
17.dAvoid long dwell times at high temperatures.If you need print settings for other nozzle sizes, feel free to reach out to us at timeplast@timeplast.com — we’ll be happy to help.
Free U.S. standard shipping on orders of 5+ spools!
Custom colors for 5+ same-type spools’ orders
Toilet Color
-
A disinfecting, water-tinting filament built to clean and color your toilet bowl from inside the tank. Formulated with borax and chlorine-based disinfectants, it releases slowly, turning water blue (or other colors) while actively sanitizing.
Looks clean. Is clean.
How it works:
Moisture triggers gradual leaching of color and cleaning agents over 2–4 weeks.
Core Composition:
Borax + Chloride Compounds – Kill bacteria and neutralize odors
Color Agents – Tints water for visual hygiene cue
Where to use it:
Toilet tank discs – Replace commercial drop-ins with your own design
Travel toilets or portables – Custom color + clean units
Bathroom branding – Hotels, restaurants, or creative use
-
Click here to access our specialized TimeMass GPT Assistant. Just tell it your printer model and the TimeMass filament you're using—it will instantly recommend the exact parameters you need to start printing successfully.
Using a Bambu Lab printer?
Click here to download our updated Bambu Lab profile. All printing parameters are fully optimized and tested—just load the file and start printing.1. Introduction
These parameters are designed to help avoid printing issues; however, temperatures and speed timings can be adjusted based on your specific goals. For example, if you prefer a less rigid result, we recommend using a lower temperature. This section outlines a complete slicing and printing profile for TimeMass Toilet Color, tailored for printers with a 0.8 mm nozzle. If the print is not being successful, please lower the nozzle temperature by 10°C and start over until an optimal print is achieved. While these examples were printed with a 0.8 mm nozzle, TimeMass can be used with any nozzle size. Please check the manual for printing parameters with all the other nozzle sizes.2. Temperature Settings
2.aNozzle Temperature: 240°C — Optimal for flowability while avoiding decomposition (which begins around 250°C).
2.bBed Temperature: 95°C — Ensures strong first-layer adhesion and prevents moisture bubbling.
2.cNozzle Temperature Range: 230–245°C — Timeplast melts around 165°C but prints best at 240°C for precise viscosity control.3. Cooling Settings
3.aNo Cooling for First Layers: 3 layers — Prevents shrinkage due to rapid cooling of moisture-rich filament.
3.bFan Minimum Speed: 0% for the first 100 seconds — Allows heat retention during early layers.
3.cFan Maximum Speed: 15% starting at 8 seconds — Avoids overcooling that can lead to warping.
3.dKeep Fan Always On: OFF — Allows vapor to escape and avoids internal fogging.
3.eSlow Down for Cooling: ON — Improves surface finish with controlled cooling.
3.fForce Cooling for Overhangs: OFF — Overcooling can deform bridges in Timeplast.
3.gFan for Overhangs: 15% — Only for essential cooling in complex areas.
3.hPre-Start Fan Time: 2 seconds — Minimizes pressure differential during the first layer.4. Volumetric Flow
4.aMax Volumetric Speed: 12 mm³/s — Based on a melt flow index of ~15 g/10min, allows high-speed printing.
4.bRamming Speed: 3 mm³/s — Prevents bubbles or popping from pressure spikes.5. Retraction and Flow
5.aRetraction Distance: 0.4 mm — Minimal retraction required for soft filaments to avoid stringing.
5.bRetraction Speed: 15 mm/s — Slow enough to avoid pulling molten plastic.
5.cPressure Advance: 0.05 — Compensates for nozzle lag at high flow rates.
5.dFlow Ratio: 92% — Slight under-extrusion avoids swelling and surface artifacts.6. Precision Settings
6.aGap Closing Radius: 0.1 mm — Tolerant of gaps in thicker walls.
6.bArc Fitting: ON — Reduces G-code size and smooths curve transitions.
6.cElephant Foot Compensation: 0.1 mm — Offsets squishing in the first layer caused by large bead sizes.7. Walls and Shells
7.aWall Loops: 2 — Minimum for strength when using a 0.8 mm nozzle.
7.bDetect Thin Walls: ON — Ensures tight geometries aren’t skipped.
7.cTop/Bottom Shell Layers: 3 — Provides good coverage; increase if watertightness is needed.
7.dTop/Bottom Thickness: 1.2 mm — Equals 1.5x the nozzle size for solid strength.
7.eTop/Bottom Pattern: Monotonic — Distributes tension evenly and improves surface finish.8. Geometry and Movement
8.aWall Order: Inner before Outer — Creates cleaner outer surfaces.
8.bInfill First: OFF — Maintains precise outer dimensions.
8.cSmooth Speed Transition: ON — Prevents ringing caused by abrupt speed changes.
8.dSmooth Coefficient: 80 — Ideal damping for soft materials.
8.eAvoid Crossing Wall: ON — Minimizes stringing across part walls.
8.fMax Detour for Crossing: 10 mm or 5% — Balances time with print cleanliness.9. Layer and Width Settings
9.aLayer Height: 0.3 mm — Optimal for strength and resolution using a 0.8 mm nozzle.
9.bInitial Layer Height: 0.35 mm — Slightly higher to improve adhesion.
9.cLine Widths (all): 0.8 mm — Matches nozzle diameter for consistent extrusion.10. Seam Settings
10.aSeam Position: Aligned or Back — Use aligned for mechanical consistency, back for visual appeal.
10.bSmart Scarf Seam: ON — Automatically adjusts seam location to reduce visual impact.
10.cSeam Angle: 155° — Standard seam angle for clean transitions.
10.dSeam Steps: 10 — Smooths seam path and improves visual finish.11. Infill Settings
11.aWall/Infill Overlap: 10% — Prevents infill from deforming soft exterior walls.
11.bInfill Combination: ON — Consolidates paths for efficiency.
11.cDetect Floating Shells: ON — Ensures unsupported vertical structures are printed reliably.
11.dSparse Infill Density: 20–25% — Balanced rigidity vs. material use.
11.eSparse Pattern: Grid — Stable and efficient for flexible geometries.12. Speed Settings
12.aTravel: 160 mm/s — Fast but safe against backlash.
12.bInitial Layer: 15 mm/s — Prevents nozzle from skimming and ensures bed adhesion.
12.cOuter Wall: 60 mm/s — Controlled speed for surface quality.
12.dInner Wall: 90 mm/s — Slightly faster without compromising control.
12.eSmall Perimeter: 35 mm/s — Reduced speed for detailed geometry.
12.fTop Surface: 40 mm/s — Improves finish on topmost layers.
12.gInfill: 100–120 mm/s — Takes advantage of high flowability.13. Acceleration Settings
13.aNormal Print: 2000 mm/s² — Prevents ringing in soft filaments.
13.bTravel: 4000 mm/s² — Enables fast movement without harsh transitions.
13.cInitial Layer: 300 mm/s² — Gentle movement prevents lifting from the bed.
13.dOuter Wall: 1500 mm/s² — Improves outer surface clarity.
13.eInner Wall: 2000 mm/s² — Balanced for structural components.
13.fTop Surface: 1500 mm/s² — Ensures smooth detailing.14. Adhesion and Brims
14.aSkirt Loops: 2 — Helps prime nozzle and start cleanly.
14.bBrim Width: 6 mm — Helps hold soft materials down.
14.cBrim Gap: 0.15 mm — Allows for easy removal without tearing.15. Prime Tower and Flush Settings
15.aPrime Tower: ON — Purges moisture and early flow inconsistencies.
15.bTower Width: 40 mm — Prevents collapse due to heat.
15.cBrim Width (Tower): 4 mm — Adds stability to the purge base.
15.dFlush Into Support: ON — Discards unwanted early flow safely.16. G-Code Start Script
M900 K0.05 ; Pressure Advance M106 S0 ; Fan off G92 E0 G1 E15 F300 ; purge line G92 E0
17. Additional Notes
17.aDry filament at 100°C for 2 hours before use.
17.bStore with desiccant.
17.cKeep extruder door open to allow vapor to escape.
17.dAvoid long dwell times at high temperatures.If you need print settings for other nozzle sizes, feel free to reach out to us at timeplast@timeplast.com — we’ll be happy to help.
Free U.S. standard shipping on orders of 5+ spools!
Custom colors for 5+ same-type spools’ orders
Vinegar
-
A humidity-activated filament loaded with vinegar for natural cleaning and disinfection. Releases over time to maintain localized acidity and remove odors or biofilm.
Clean with nature’s oldest solvent.
How it works:
Moisture triggers acid release in a controlled manner, useful for deodorizing or sanitizing small spaces.
Where to use it:
Deodorizing plugs – Trash cans, lockers, shoe cabinets
Natural cleaning pads – Kitchen and bath tools
Pet-safe disinfecting tools
-
Click here to access our specialized TimeMass GPT Assistant. Just tell it your printer model and the TimeMass filament you're using—it will instantly recommend the exact parameters you need to start printing successfully.
Using a Bambu Lab printer?
Click here to download our updated Bambu Lab profile. All printing parameters are fully optimized and tested—just load the file and start printing.1. Introduction
These parameters are designed to help avoid printing issues; however, temperatures and speed timings can be adjusted based on your specific goals. For example, if you prefer a less rigid result, we recommend using a lower temperature. This section outlines a complete slicing and printing profile for TimeMass Vinegar, tailored for printers with a 0.8 mm nozzle. If the print is not being successful, please lower the nozzle temperature by 10°C and start over until an optimal print is achieved. While these examples were printed with a 0.8 mm nozzle, TimeMass can be used with any nozzle size. Please check the manual for printing parameters with all the other nozzle sizes.2. Temperature Settings
2.aNozzle Temperature: 240°C — Optimal for flowability while avoiding decomposition (which begins around 250°C).
2.bBed Temperature: 95°C — Ensures strong first-layer adhesion and prevents moisture bubbling.
2.cNozzle Temperature Range: 230–245°C — Timeplast melts around 165°C but prints best at 240°C for precise viscosity control.3. Cooling Settings
3.aNo Cooling for First Layers: 3 layers — Prevents shrinkage due to rapid cooling of moisture-rich filament.
3.bFan Minimum Speed: 0% for the first 100 seconds — Allows heat retention during early layers.
3.cFan Maximum Speed: 15% starting at 8 seconds — Avoids overcooling that can lead to warping.
3.dKeep Fan Always On: OFF — Allows vapor to escape and avoids internal fogging.
3.eSlow Down for Cooling: ON — Improves surface finish with controlled cooling.
3.fForce Cooling for Overhangs: OFF — Overcooling can deform bridges in Timeplast.
3.gFan for Overhangs: 15% — Only for essential cooling in complex areas.
3.hPre-Start Fan Time: 2 seconds — Minimizes pressure differential during the first layer.4. Volumetric Flow
4.aMax Volumetric Speed: 12 mm³/s — Based on a melt flow index of ~15 g/10min, allows high-speed printing.
4.bRamming Speed: 3 mm³/s — Prevents bubbles or popping from pressure spikes.5. Retraction and Flow
5.aRetraction Distance: 0.4 mm — Minimal retraction required for soft filaments to avoid stringing.
5.bRetraction Speed: 15 mm/s — Slow enough to avoid pulling molten plastic.
5.cPressure Advance: 0.05 — Compensates for nozzle lag at high flow rates.
5.dFlow Ratio: 92% — Slight under-extrusion avoids swelling and surface artifacts.6. Precision Settings
6.aGap Closing Radius: 0.1 mm — Tolerant of gaps in thicker walls.
6.bArc Fitting: ON — Reduces G-code size and smooths curve transitions.
6.cElephant Foot Compensation: 0.1 mm — Offsets squishing in the first layer caused by large bead sizes.7. Walls and Shells
7.aWall Loops: 2 — Minimum for strength when using a 0.8 mm nozzle.
7.bDetect Thin Walls: ON — Ensures tight geometries aren’t skipped.
7.cTop/Bottom Shell Layers: 3 — Provides good coverage; increase if watertightness is needed.
7.dTop/Bottom Thickness: 1.2 mm — Equals 1.5x the nozzle size for solid strength.
7.eTop/Bottom Pattern: Monotonic — Distributes tension evenly and improves surface finish.8. Geometry and Movement
8.aWall Order: Inner before Outer — Creates cleaner outer surfaces.
8.bInfill First: OFF — Maintains precise outer dimensions.
8.cSmooth Speed Transition: ON — Prevents ringing caused by abrupt speed changes.
8.dSmooth Coefficient: 80 — Ideal damping for soft materials.
8.eAvoid Crossing Wall: ON — Minimizes stringing across part walls.
8.fMax Detour for Crossing: 10 mm or 5% — Balances time with print cleanliness.9. Layer and Width Settings
9.aLayer Height: 0.3 mm — Optimal for strength and resolution using a 0.8 mm nozzle.
9.bInitial Layer Height: 0.35 mm — Slightly higher to improve adhesion.
9.cLine Widths (all): 0.8 mm — Matches nozzle diameter for consistent extrusion.10. Seam Settings
10.aSeam Position: Aligned or Back — Use aligned for mechanical consistency, back for visual appeal.
10.bSmart Scarf Seam: ON — Automatically adjusts seam location to reduce visual impact.
10.cSeam Angle: 155° — Standard seam angle for clean transitions.
10.dSeam Steps: 10 — Smooths seam path and improves visual finish.11. Infill Settings
11.aWall/Infill Overlap: 10% — Prevents infill from deforming soft exterior walls.
11.bInfill Combination: ON — Consolidates paths for efficiency.
11.cDetect Floating Shells: ON — Ensures unsupported vertical structures are printed reliably.
11.dSparse Infill Density: 20–25% — Balanced rigidity vs. material use.
11.eSparse Pattern: Grid — Stable and efficient for flexible geometries.12. Speed Settings
12.aTravel: 160 mm/s — Fast but safe against backlash.
12.bInitial Layer: 15 mm/s — Prevents nozzle from skimming and ensures bed adhesion.
12.cOuter Wall: 60 mm/s — Controlled speed for surface quality.
12.dInner Wall: 90 mm/s — Slightly faster without compromising control.
12.eSmall Perimeter: 35 mm/s — Reduced speed for detailed geometry.
12.fTop Surface: 40 mm/s — Improves finish on topmost layers.
12.gInfill: 100–120 mm/s — Takes advantage of high flowability.13. Acceleration Settings
13.aNormal Print: 2000 mm/s² — Prevents ringing in soft filaments.
13.bTravel: 4000 mm/s² — Enables fast movement without harsh transitions.
13.cInitial Layer: 300 mm/s² — Gentle movement prevents lifting from the bed.
13.dOuter Wall: 1500 mm/s² — Improves outer surface clarity.
13.eInner Wall: 2000 mm/s² — Balanced for structural components.
13.fTop Surface: 1500 mm/s² — Ensures smooth detailing.14. Adhesion and Brims
14.aSkirt Loops: 2 — Helps prime nozzle and start cleanly.
14.bBrim Width: 6 mm — Helps hold soft materials down.
14.cBrim Gap: 0.15 mm — Allows for easy removal without tearing.15. Prime Tower and Flush Settings
15.aPrime Tower: ON — Purges moisture and early flow inconsistencies.
15.bTower Width: 40 mm — Prevents collapse due to heat.
15.cBrim Width (Tower): 4 mm — Adds stability to the purge base.
15.dFlush Into Support: ON — Discards unwanted early flow safely.16. G-Code Start Script
M900 K0.05 ; Pressure Advance M106 S0 ; Fan off G92 E0 G1 E15 F300 ; purge line G92 E0
17. Additional Notes
17.aDry filament at 100°C for 2 hours before use.
17.bStore with desiccant.
17.cKeep extruder door open to allow vapor to escape.
17.dAvoid long dwell times at high temperatures.If you need print settings for other nozzle sizes, feel free to reach out to us at timeplast@timeplast.com — we’ll be happy to help.
Free U.S. standard shipping on orders of 5+ spools!
Custom colors for 5+ same-type spools’ orders
Multi Material Printing
Support - Gen 2
-
TimeMass Support is a flexible, ultra high molecular weight support filament that peels off in one clean stroke. No scraping. No dissolving. No drama.
Unlike brittle support materials that shatter like dry pasta, this one bends, flexes, and then just... comes off. Perfect for big prints, weird angles, and geometry that usually sends slicers into therapy.
What makes it different:
Flexible but removable – Bends instead of snapping, then detaches without a fight.
No cleanup – Leaves your print smooth, not scarred. No water, no solvents, no wasted time.
Geometry-friendly – Built for overhangs, bridges, and all the complicated nonsense normal supports can't handle.
Eco-conscious – No chemical baths. Just pull, toss, done. It will fully dissolve in water.
TimeMass Support gives you one less thing to fight with. Design crazy. Print smarter.
Need Ideas? Here You Go:
High-End Prototyping – Enables rapid iteration of complex designs without post-processing delays.
Consumer Product Manufacturing – Ideal for mass production where fast and easy support removal is needed.
Medical & Dental Applications – Great for printing intricate prosthetics or dental models without risk of damaging fine details.
Architectural Models – Allows for printing delicate structures that require support but need clean final surfaces.
Soft Robotics & Wearables – Facilitates the creation of flexible, multi-material parts with temporary internal supports.
Jewelry & Artistic Prints – Provides an easy way to remove supports without damaging fine engravings or tiny details.
-
Click here to access our specialized TimeMass GPT Assistant. Just tell it your printer model and the TimeMass filament you're using—it will instantly recommend the exact parameters you need to start printing successfully.
Using a Bambu Lab printer?
Click here to download our updated Bambu Lab profile. All printing parameters are fully optimized and tested—just load the file and start printing.1. Introduction
These parameters are designed to help avoid printing issues; however, temperatures and speed timings can be adjusted based on your specific goals. For example, if you prefer a less rigid result, we recommend using a lower temperature. This section outlines a complete slicing and printing profile for TimeMass Support, tailored for printers with a 0.8 mm nozzle. If the print is not being successful, please lower the nozzle temperature by 10°C and start over until an optimal print is achieved. While these examples were printed with a 0.8 mm nozzle, TimeMass can be used with any nozzle size. Please check the manual for printing parameters with all the other nozzle sizes.2. Temperature Settings
2.aNozzle Temperature: 240°C — Optimal for flowability while avoiding decomposition (which begins around 250°C).
2.bBed Temperature: 95°C — Ensures strong first-layer adhesion and prevents moisture bubbling.
2.cNozzle Temperature Range: 230–245°C — Timeplast melts around 165°C but prints best at 240°C for precise viscosity control.3. Cooling Settings
3.aNo Cooling for First Layers: 3 layers — Prevents shrinkage due to rapid cooling of moisture-rich filament.
3.bFan Minimum Speed: 0% for the first 100 seconds — Allows heat retention during early layers.
3.cFan Maximum Speed: 15% starting at 8 seconds — Avoids overcooling that can lead to warping.
3.dKeep Fan Always On: OFF — Allows vapor to escape and avoids internal fogging.
3.eSlow Down for Cooling: ON — Improves surface finish with controlled cooling.
3.fForce Cooling for Overhangs: OFF — Overcooling can deform bridges in Timeplast.
3.gFan for Overhangs: 15% — Only for essential cooling in complex areas.
3.hPre-Start Fan Time: 2 seconds — Minimizes pressure differential during the first layer.4. Volumetric Flow
4.aMax Volumetric Speed: 12 mm³/s — Based on a melt flow index of ~15 g/10min, allows high-speed printing.
4.bRamming Speed: 3 mm³/s — Prevents bubbles or popping from pressure spikes.5. Retraction and Flow
5.aRetraction Distance: 0.4 mm — Minimal retraction required for soft filaments to avoid stringing.
5.bRetraction Speed: 15 mm/s — Slow enough to avoid pulling molten plastic.
5.cPressure Advance: 0.05 — Compensates for nozzle lag at high flow rates.
5.dFlow Ratio: 92% — Slight under-extrusion avoids swelling and surface artifacts.6. Precision Settings
6.aGap Closing Radius: 0.1 mm — Tolerant of gaps in thicker walls.
6.bArc Fitting: ON — Reduces G-code size and smooths curve transitions.
6.cElephant Foot Compensation: 0.1 mm — Offsets squishing in the first layer caused by large bead sizes.7. Walls and Shells
7.aWall Loops: 2 — Minimum for strength when using a 0.8 mm nozzle.
7.bDetect Thin Walls: ON — Ensures tight geometries aren’t skipped.
7.cTop/Bottom Shell Layers: 3 — Provides good coverage; increase if watertightness is needed.
7.dTop/Bottom Thickness: 1.2 mm — Equals 1.5x the nozzle size for solid strength.
7.eTop/Bottom Pattern: Monotonic — Distributes tension evenly and improves surface finish.8. Geometry and Movement
8.aWall Order: Inner before Outer — Creates cleaner outer surfaces.
8.bInfill First: OFF — Maintains precise outer dimensions.
8.cSmooth Speed Transition: ON — Prevents ringing caused by abrupt speed changes.
8.dSmooth Coefficient: 80 — Ideal damping for soft materials.
8.eAvoid Crossing Wall: ON — Minimizes stringing across part walls.
8.fMax Detour for Crossing: 10 mm or 5% — Balances time with print cleanliness.9. Layer and Width Settings
9.aLayer Height: 0.3 mm — Optimal for strength and resolution using a 0.8 mm nozzle.
9.bInitial Layer Height: 0.35 mm — Slightly higher to improve adhesion.
9.cLine Widths (all): 0.8 mm — Matches nozzle diameter for consistent extrusion.10. Seam Settings
10.aSeam Position: Aligned or Back — Use aligned for mechanical consistency, back for visual appeal.
10.bSmart Scarf Seam: ON — Automatically adjusts seam location to reduce visual impact.
10.cSeam Angle: 155° — Standard seam angle for clean transitions.
10.dSeam Steps: 10 — Smooths seam path and improves visual finish.11. Infill Settings
11.aWall/Infill Overlap: 10% — Prevents infill from deforming soft exterior walls.
11.bInfill Combination: ON — Consolidates paths for efficiency.
11.cDetect Floating Shells: ON — Ensures unsupported vertical structures are printed reliably.
11.dSparse Infill Density: 20–25% — Balanced rigidity vs. material use.
11.eSparse Pattern: Grid — Stable and efficient for flexible geometries.12. Speed Settings
12.aTravel: 160 mm/s — Fast but safe against backlash.
12.bInitial Layer: 15 mm/s — Prevents nozzle from skimming and ensures bed adhesion.
12.cOuter Wall: 60 mm/s — Controlled speed for surface quality.
12.dInner Wall: 90 mm/s — Slightly faster without compromising control.
12.eSmall Perimeter: 35 mm/s — Reduced speed for detailed geometry.
12.fTop Surface: 40 mm/s — Improves finish on topmost layers.
12.gInfill: 100–120 mm/s — Takes advantage of high flowability.13. Acceleration Settings
13.aNormal Print: 2000 mm/s² — Prevents ringing in soft filaments.
13.bTravel: 4000 mm/s² — Enables fast movement without harsh transitions.
13.cInitial Layer: 300 mm/s² — Gentle movement prevents lifting from the bed.
13.dOuter Wall: 1500 mm/s² — Improves outer surface clarity.
13.eInner Wall: 2000 mm/s² — Balanced for structural components.
13.fTop Surface: 1500 mm/s² — Ensures smooth detailing.14. Adhesion and Brims
14.aSkirt Loops: 2 — Helps prime nozzle and start cleanly.
14.bBrim Width: 6 mm — Helps hold soft materials down.
14.cBrim Gap: 0.15 mm — Allows for easy removal without tearing.15. Prime Tower and Flush Settings
15.aPrime Tower: ON — Purges moisture and early flow inconsistencies.
15.bTower Width: 40 mm — Prevents collapse due to heat.
15.cBrim Width (Tower): 4 mm — Adds stability to the purge base.
15.dFlush Into Support: ON — Discards unwanted early flow safely.16. G-Code Start Script
M900 K0.05 ; Pressure Advance M106 S0 ; Fan off G92 E0 G1 E15 F300 ; purge line G92 E0
17. Additional Notes
17.aDry filament at 100°C for 2 hours before use.
17.bStore with desiccant.
17.cKeep extruder door open to allow vapor to escape.
17.dAvoid long dwell times at high temperatures.If you need print settings for other nozzle sizes, feel free to reach out to us at timeplast@timeplast.com — we’ll be happy to help.
Free U.S. standard shipping on orders of 5+ spools!
Custom colors for 5+ same-type spools’ orders
Metal Surface - Gen 2
-
What if 3D-printed objects could look, feel, and behave like real metal—without ever needing a metal printer? TimeMass - Metal Surface is an advanced 4D printing filament that transforms polymer-based prints into metallic masterpieces with just a quick dip in water and fine metal powders.
Unlike conventional metal-infused filaments, which contain embedded metallic particles that dilute their true metal effect, TimeMass - Metal Surface actively bonds with external metals post-print. Engineered with a high-affinity polymer matrix, this filament temporarily becomes hydrophilic upon contact with water, allowing iron filings, copper, brass, or other metallic powders to interlock with its surface. As the print dries, these metallic elements lock into place, creating a high-density, conductive, and slightly ferromagnetic finish.
How It Works: A Revolutionary Surface Chemistry
⚡ Hydrophilic Activation – Once printed, the object briefly absorbs water, creating an ultra-fine microcapillary structure that pulls in metallic powders.
🧲 Metallic Interlocking – The material’s surface chemistry actively bonds with iron, copper, brass, or other metals, ensuring a strong, permanent adhesion without embedded metal particles.
🔄 Real Metal Behavior – Unlike plastic-based metallic finishes, TimeMass - Metal Surface creates a true-to-life metal appearance that interacts with light, magnetism, and oxidation just like an actual metal object.Where Aesthetics Meet Functionality
🏛️ Luxury Finishes & Industrial Design – Print stunning metallic sculptures, architectural models, or machine-like prototypes that look and feel like cast metal.
⚙️ Functional Magnetic & Conductive Surfaces – Use iron-infused finishes to create ferromagnetic parts, magnetic tool holders, or smart electrical components.
🎭 Hyper-Realistic Props & Replicas – Make high-end movie props, jewelry, or antique recreations that pass for real metal at a fraction of the weight.
🚀 Wearable & Fashion Tech – Design jewelry, watches, or metallic-textured accessories that look and behave like polished, brushed, or oxidized metals.
🎨 Custom Art & Home Decor – Develop bespoke metal-finished objects, from bronze-like sculptures to steampunk-inspired creations.
♻️ Sustainable Metal Effects – Achieve real metal looks without the need for costly, heavy, or energy-intensive metal 3D printing processes.Beyond Metal-Inspired—This Is Metal Transformed
With TimeMass - Metal Surface, 3D-printed plastic no longer looks like plastic. By combining advanced 4D material engineering with real metal bonding, this filament makes it possible to replicate the weight, conductivity, and texture of metal—all with the ease of polymer-based printing.
For artists, engineers, and visionaries seeking the power of metal without the constraints of metal printing, TimeMass - Metal Surface is the ultimate breakthrough.
Print it. Dip it. Transform it.
Iron filings is one of the best powders for this filament and you can find them on Amazon.
Need Ideas? Here You Go:
Functional mechanical components with improved weight, density, and partial magnetism.
Artistic and industrial-grade sculptures that require authentic metallic aesthetics.
Custom jewelry and accessories that mimic silver, brass, or iron without requiring metal casting.
Prop and cosplay armor pieces with real metallic reflections and textures.
Magnetic-reactive designs, such as hidden latches, sensors, and magnetic puzzles.
Customized speaker grilles or conductive surfaces for artistic and functional electrical projects.
-
Click here to access our specialized TimeMass GPT Assistant. Just tell it your printer model and the TimeMass filament you're using—it will instantly recommend the exact parameters you need to start printing successfully.
Using a Bambu Lab printer?
Click here to download our updated Bambu Lab profile. All printing parameters are fully optimized and tested—just load the file and start printing.1. Introduction
These parameters are designed to help avoid printing issues; however, temperatures and speed timings can be adjusted based on your specific goals. For example, if you prefer a less rigid result, we recommend using a lower temperature. This section outlines a complete slicing and printing profile for TimeMass Metal Surface, tailored for printers with a 0.8 mm nozzle. If the print is not being successful, please lower the nozzle temperature by 10°C and start over until an optimal print is achieved. While these examples were printed with a 0.8 mm nozzle, TimeMass can be used with any nozzle size. Please check the manual for printing parameters with all the other nozzle sizes.2. Temperature Settings
2.aNozzle Temperature: 240°C — Optimal for flowability while avoiding decomposition (which begins around 250°C).
2.bBed Temperature: 95°C — Ensures strong first-layer adhesion and prevents moisture bubbling.
2.cNozzle Temperature Range: 230–245°C — Timeplast melts around 165°C but prints best at 240°C for precise viscosity control.3. Cooling Settings
3.aNo Cooling for First Layers: 3 layers — Prevents shrinkage due to rapid cooling of moisture-rich filament.
3.bFan Minimum Speed: 0% for the first 100 seconds — Allows heat retention during early layers.
3.cFan Maximum Speed: 15% starting at 8 seconds — Avoids overcooling that can lead to warping.
3.dKeep Fan Always On: OFF — Allows vapor to escape and avoids internal fogging.
3.eSlow Down for Cooling: ON — Improves surface finish with controlled cooling.
3.fForce Cooling for Overhangs: OFF — Overcooling can deform bridges in Timeplast.
3.gFan for Overhangs: 15% — Only for essential cooling in complex areas.
3.hPre-Start Fan Time: 2 seconds — Minimizes pressure differential during the first layer.4. Volumetric Flow
4.aMax Volumetric Speed: 12 mm³/s — Based on a melt flow index of ~15 g/10min, allows high-speed printing.
4.bRamming Speed: 3 mm³/s — Prevents bubbles or popping from pressure spikes.5. Retraction and Flow
5.aRetraction Distance: 0.4 mm — Minimal retraction required for soft filaments to avoid stringing.
5.bRetraction Speed: 15 mm/s — Slow enough to avoid pulling molten plastic.
5.cPressure Advance: 0.05 — Compensates for nozzle lag at high flow rates.
5.dFlow Ratio: 92% — Slight under-extrusion avoids swelling and surface artifacts.6. Precision Settings
6.aGap Closing Radius: 0.1 mm — Tolerant of gaps in thicker walls.
6.bArc Fitting: ON — Reduces G-code size and smooths curve transitions.
6.cElephant Foot Compensation: 0.1 mm — Offsets squishing in the first layer caused by large bead sizes.7. Walls and Shells
7.aWall Loops: 2 — Minimum for strength when using a 0.8 mm nozzle.
7.bDetect Thin Walls: ON — Ensures tight geometries aren’t skipped.
7.cTop/Bottom Shell Layers: 3 — Provides good coverage; increase if watertightness is needed.
7.dTop/Bottom Thickness: 1.2 mm — Equals 1.5x the nozzle size for solid strength.
7.eTop/Bottom Pattern: Monotonic — Distributes tension evenly and improves surface finish.8. Geometry and Movement
8.aWall Order: Inner before Outer — Creates cleaner outer surfaces.
8.bInfill First: OFF — Maintains precise outer dimensions.
8.cSmooth Speed Transition: ON — Prevents ringing caused by abrupt speed changes.
8.dSmooth Coefficient: 80 — Ideal damping for soft materials.
8.eAvoid Crossing Wall: ON — Minimizes stringing across part walls.
8.fMax Detour for Crossing: 10 mm or 5% — Balances time with print cleanliness.9. Layer and Width Settings
9.aLayer Height: 0.3 mm — Optimal for strength and resolution using a 0.8 mm nozzle.
9.bInitial Layer Height: 0.35 mm — Slightly higher to improve adhesion.
9.cLine Widths (all): 0.8 mm — Matches nozzle diameter for consistent extrusion.10. Seam Settings
10.aSeam Position: Aligned or Back — Use aligned for mechanical consistency, back for visual appeal.
10.bSmart Scarf Seam: ON — Automatically adjusts seam location to reduce visual impact.
10.cSeam Angle: 155° — Standard seam angle for clean transitions.
10.dSeam Steps: 10 — Smooths seam path and improves visual finish.11. Infill Settings
11.aWall/Infill Overlap: 10% — Prevents infill from deforming soft exterior walls.
11.bInfill Combination: ON — Consolidates paths for efficiency.
11.cDetect Floating Shells: ON — Ensures unsupported vertical structures are printed reliably.
11.dSparse Infill Density: 20–25% — Balanced rigidity vs. material use.
11.eSparse Pattern: Grid — Stable and efficient for flexible geometries.12. Speed Settings
12.aTravel: 160 mm/s — Fast but safe against backlash.
12.bInitial Layer: 15 mm/s — Prevents nozzle from skimming and ensures bed adhesion.
12.cOuter Wall: 60 mm/s — Controlled speed for surface quality.
12.dInner Wall: 90 mm/s — Slightly faster without compromising control.
12.eSmall Perimeter: 35 mm/s — Reduced speed for detailed geometry.
12.fTop Surface: 40 mm/s — Improves finish on topmost layers.
12.gInfill: 100–120 mm/s — Takes advantage of high flowability.13. Acceleration Settings
13.aNormal Print: 2000 mm/s² — Prevents ringing in soft filaments.
13.bTravel: 4000 mm/s² — Enables fast movement without harsh transitions.
13.cInitial Layer: 300 mm/s² — Gentle movement prevents lifting from the bed.
13.dOuter Wall: 1500 mm/s² — Improves outer surface clarity.
13.eInner Wall: 2000 mm/s² — Balanced for structural components.
13.fTop Surface: 1500 mm/s² — Ensures smooth detailing.14. Adhesion and Brims
14.aSkirt Loops: 2 — Helps prime nozzle and start cleanly.
14.bBrim Width: 6 mm — Helps hold soft materials down.
14.cBrim Gap: 0.15 mm — Allows for easy removal without tearing.15. Prime Tower and Flush Settings
15.aPrime Tower: ON — Purges moisture and early flow inconsistencies.
15.bTower Width: 40 mm — Prevents collapse due to heat.
15.cBrim Width (Tower): 4 mm — Adds stability to the purge base.
15.dFlush Into Support: ON — Discards unwanted early flow safely.16. G-Code Start Script
M900 K0.05 ; Pressure Advance M106 S0 ; Fan off G92 E0 G1 E15 F300 ; purge line G92 E0
17. Additional Notes
17.aDry filament at 100°C for 2 hours before use.
17.bStore with desiccant.
17.cKeep extruder door open to allow vapor to escape.
17.dAvoid long dwell times at high temperatures.If you need print settings for other nozzle sizes, feel free to reach out to us at timeplast@timeplast.com — we’ll be happy to help.
You can also get instant support through our dedicated ChatGPT assistant here:https://chatgpt.com/g/g-6823924241cc8191bbabcf0bc6523e3f-timemass-4d-printing🚀
Free U.S. standard shipping on orders of 5+ spools!
Custom colors for 5+ same-type spools’ orders
Paper Surface
-
What if your 3D print felt like aged parchment but held up like plastic?
TimeMass Paper Surface makes that happen. It’s a post-processing filament that lets you print tough, durable parts with the soft, organic texture of real paper.How it works:
After printing, dunk the object in water—just enough to activate the surface. Then dust it with a cellulose-based powder. As it dries, the fibers bond, giving the piece a matte, fibrous finish that looks handmade but holds up like tech.
Why it’s different:
Paper feel, polymer strength – It won’t tear, crumple, or dissolve like the real thing.
Reactive surface treatment – A water dip + powder coat = authentic texture.
No fake “grain” gimmicks – This isn’t molded plastic pretending to be paper. It is paper—on the surface.
Where to use it:
Fine art & sculpture – Print textured canvases, delicate details, or weird little relics.
Custom packaging & branding – Business cards that don’t suck, packaging that feels like it belongs in an art gallery.
Historical props & replicas – Make museum-worthy “manuscripts” that don’t fall apart.
Interior design & signage – Print lightweight panels that look hand-finished, not injection molded.
Bookbinding & paper prototypes – Covers that feel real, pages that don’t quit.
No gimmicks. No lamination.
Just that clean, warm, paper feel—built right into the print.If you want every layer to say “craft” instead of “plastic,” Paper Surface makes it happen.
Need Ideas? Here You Go:
Books, scrolls, and artistic paper-like sculptures, preserving a unique handmade aesthetic.
Paper-textured prototypes for product design and packaging concepts.
Custom greeting cards, business cards, and invitations with intricate 3D textures.
Tactile signage and educational tools, combining print durability with a paper feel.
Handwritten notebooks or calligraphy-ready sheets, offering 3D-printed permanence with a paper finish.
⚠️ Please note: the cellulose-based finishing powder is sold separately.
-
Click here to access our specialized TimeMass GPT Assistant. Just tell it your printer model and the TimeMass filament you're using—it will instantly recommend the exact parameters you need to start printing successfully.
Using a Bambu Lab printer?
Click here to download our updated Bambu Lab profile. All printing parameters are fully optimized and tested—just load the file and start printing.1. Introduction
These parameters are designed to help avoid printing issues; however, temperatures and speed timings can be adjusted based on your specific goals. For example, if you prefer a less rigid result, we recommend using a lower temperature. This section outlines a complete slicing and printing profile for TimeMass Paper Surface, tailored for printers with a 0.8 mm nozzle. If the print is not being successful, please lower the nozzle temperature by 10°C and start over until an optimal print is achieved. While these examples were printed with a 0.8 mm nozzle, TimeMass can be used with any nozzle size. Please check the manual for printing parameters with all the other nozzle sizes.2. Temperature Settings
2.aNozzle Temperature: 240°C — Optimal for flowability while avoiding decomposition (which begins around 250°C).
2.bBed Temperature: 95°C — Ensures strong first-layer adhesion and prevents moisture bubbling.
2.cNozzle Temperature Range: 230–245°C — Timeplast melts around 165°C but prints best at 240°C for precise viscosity control.3. Cooling Settings
3.aNo Cooling for First Layers: 3 layers — Prevents shrinkage due to rapid cooling of moisture-rich filament.
3.bFan Minimum Speed: 0% for the first 100 seconds — Allows heat retention during early layers.
3.cFan Maximum Speed: 15% starting at 8 seconds — Avoids overcooling that can lead to warping.
3.dKeep Fan Always On: OFF — Allows vapor to escape and avoids internal fogging.
3.eSlow Down for Cooling: ON — Improves surface finish with controlled cooling.
3.fForce Cooling for Overhangs: OFF — Overcooling can deform bridges in Timeplast.
3.gFan for Overhangs: 15% — Only for essential cooling in complex areas.
3.hPre-Start Fan Time: 2 seconds — Minimizes pressure differential during the first layer.4. Volumetric Flow
4.aMax Volumetric Speed: 12 mm³/s — Based on a melt flow index of ~15 g/10min, allows high-speed printing.
4.bRamming Speed: 3 mm³/s — Prevents bubbles or popping from pressure spikes.5. Retraction and Flow
5.aRetraction Distance: 0.4 mm — Minimal retraction required for soft filaments to avoid stringing.
5.bRetraction Speed: 15 mm/s — Slow enough to avoid pulling molten plastic.
5.cPressure Advance: 0.05 — Compensates for nozzle lag at high flow rates.
5.dFlow Ratio: 92% — Slight under-extrusion avoids swelling and surface artifacts.6. Precision Settings
6.aGap Closing Radius: 0.1 mm — Tolerant of gaps in thicker walls.
6.bArc Fitting: ON — Reduces G-code size and smooths curve transitions.
6.cElephant Foot Compensation: 0.1 mm — Offsets squishing in the first layer caused by large bead sizes.7. Walls and Shells
7.aWall Loops: 2 — Minimum for strength when using a 0.8 mm nozzle.
7.bDetect Thin Walls: ON — Ensures tight geometries aren’t skipped.
7.cTop/Bottom Shell Layers: 3 — Provides good coverage; increase if watertightness is needed.
7.dTop/Bottom Thickness: 1.2 mm — Equals 1.5x the nozzle size for solid strength.
7.eTop/Bottom Pattern: Monotonic — Distributes tension evenly and improves surface finish.8. Geometry and Movement
8.aWall Order: Inner before Outer — Creates cleaner outer surfaces.
8.bInfill First: OFF — Maintains precise outer dimensions.
8.cSmooth Speed Transition: ON — Prevents ringing caused by abrupt speed changes.
8.dSmooth Coefficient: 80 — Ideal damping for soft materials.
8.eAvoid Crossing Wall: ON — Minimizes stringing across part walls.
8.fMax Detour for Crossing: 10 mm or 5% — Balances time with print cleanliness.9. Layer and Width Settings
9.aLayer Height: 0.3 mm — Optimal for strength and resolution using a 0.8 mm nozzle.
9.bInitial Layer Height: 0.35 mm — Slightly higher to improve adhesion.
9.cLine Widths (all): 0.8 mm — Matches nozzle diameter for consistent extrusion.10. Seam Settings
10.aSeam Position: Aligned or Back — Use aligned for mechanical consistency, back for visual appeal.
10.bSmart Scarf Seam: ON — Automatically adjusts seam location to reduce visual impact.
10.cSeam Angle: 155° — Standard seam angle for clean transitions.
10.dSeam Steps: 10 — Smooths seam path and improves visual finish.11. Infill Settings
11.aWall/Infill Overlap: 10% — Prevents infill from deforming soft exterior walls.
11.bInfill Combination: ON — Consolidates paths for efficiency.
11.cDetect Floating Shells: ON — Ensures unsupported vertical structures are printed reliably.
11.dSparse Infill Density: 20–25% — Balanced rigidity vs. material use.
11.eSparse Pattern: Grid — Stable and efficient for flexible geometries.12. Speed Settings
12.aTravel: 160 mm/s — Fast but safe against backlash.
12.bInitial Layer: 15 mm/s — Prevents nozzle from skimming and ensures bed adhesion.
12.cOuter Wall: 60 mm/s — Controlled speed for surface quality.
12.dInner Wall: 90 mm/s — Slightly faster without compromising control.
12.eSmall Perimeter: 35 mm/s — Reduced speed for detailed geometry.
12.fTop Surface: 40 mm/s — Improves finish on topmost layers.
12.gInfill: 100–120 mm/s — Takes advantage of high flowability.13. Acceleration Settings
13.aNormal Print: 2000 mm/s² — Prevents ringing in soft filaments.
13.bTravel: 4000 mm/s² — Enables fast movement without harsh transitions.
13.cInitial Layer: 300 mm/s² — Gentle movement prevents lifting from the bed.
13.dOuter Wall: 1500 mm/s² — Improves outer surface clarity.
13.eInner Wall: 2000 mm/s² — Balanced for structural components.
13.fTop Surface: 1500 mm/s² — Ensures smooth detailing.14. Adhesion and Brims
14.aSkirt Loops: 2 — Helps prime nozzle and start cleanly.
14.bBrim Width: 6 mm — Helps hold soft materials down.
14.cBrim Gap: 0.15 mm — Allows for easy removal without tearing.15. Prime Tower and Flush Settings
15.aPrime Tower: ON — Purges moisture and early flow inconsistencies.
15.bTower Width: 40 mm — Prevents collapse due to heat.
15.cBrim Width (Tower): 4 mm — Adds stability to the purge base.
15.dFlush Into Support: ON — Discards unwanted early flow safely.16. G-Code Start Script
M900 K0.05 ; Pressure Advance M106 S0 ; Fan off G92 E0 G1 E15 F300 ; purge line G92 E0
17. Additional Notes
17.aDry filament at 100°C for 2 hours before use.
17.bStore with desiccant.
17.cKeep extruder door open to allow vapor to escape.
17.dAvoid long dwell times at high temperatures.If you need print settings for other nozzle sizes, feel free to reach out to us at timeplast@timeplast.com — we’ll be happy to help.
You can also get instant support through our dedicated ChatGPT assistant here:https://chatgpt.com/g/g-6823924241cc8191bbabcf0bc6523e3f-timemass-4d-printing🚀
Free U.S. standard shipping on orders of 5+ spools!
Custom colors for 5+ same-type spools’ orders
Texture
-
TimeMass Texture is a flexible, semi-water-soluble filament that temporarily becomes sticky upon a quick dip in water so that it can then be covered in any powder material, altering 100% of its texture, and making it a non-plastic feel print.
After successfully printing your object, submerge it in water for 2 to 5 seconds, then briefly dry it. Next, coat it with your chosen powder to create the desired texture—for example, stone powder for a stone-like appearance.
If you want a thicker texture layer, leave the object in water for a longer period and dry it less, allowing the material to absorb and retain more of the powder.
Once coated, use a paper towel to remove any excess powder. After 48 hours, you can refine the texture further with light sandpaper to achieve the final desired finish.
Surface treatment compatibility: The sticky surface can bond with fine powders, creating a textured, non-plastic finish.
Need Ideas? Here You Go:
Hyper-realistic models: Print objects, then coat them with fine materials (sand, dirt, stone powder) to create ultra-realistic terrain, fossils, or artifacts.
Naturally degradable textures: Print and coat objects with benign materials for natural-looking prototypes.
Anti-plastic aesthetic: Produce objects that feel organic by layering them with non-plastic textures like wood dust, chalk, or minerals.
Special effects & cosplay: Create lightweight, flexible armor or props that look like solid stone or metal.
Medical & ergonomic surfaces: Create handles or grips that become naturally textured when exposed to moisture, improving grip without synthetic rubber.
-
Click here to access our specialized TimeMass GPT Assistant. Just tell it your printer model and the TimeMass filament you're using—it will instantly recommend the exact parameters you need to start printing successfully.
Using a Bambu Lab printer?
Click here to download our updated Bambu Lab profile. All printing parameters are fully optimized and tested—just load the file and start printing.1. Introduction
These parameters are designed to help avoid printing issues; however, temperatures and speed timings can be adjusted based on your specific goals. For example, if you prefer a less rigid result, we recommend using a lower temperature. This section outlines a complete slicing and printing profile for TimeMass Texture, tailored for printers with a 0.8 mm nozzle. If the print is not being successful, please lower the nozzle temperature by 10°C and start over until an optimal print is achieved. While these examples were printed with a 0.8 mm nozzle, TimeMass can be used with any nozzle size. Please check the manual for printing parameters with all the other nozzle sizes.2. Temperature Settings
2.aNozzle Temperature: 240°C — Optimal for flowability while avoiding decomposition (which begins around 250°C).
2.bBed Temperature: 95°C — Ensures strong first-layer adhesion and prevents moisture bubbling.
2.cNozzle Temperature Range: 230–245°C — Timeplast melts around 165°C but prints best at 240°C for precise viscosity control.3. Cooling Settings
3.aNo Cooling for First Layers: 3 layers — Prevents shrinkage due to rapid cooling of moisture-rich filament.
3.bFan Minimum Speed: 0% for the first 100 seconds — Allows heat retention during early layers.
3.cFan Maximum Speed: 15% starting at 8 seconds — Avoids overcooling that can lead to warping.
3.dKeep Fan Always On: OFF — Allows vapor to escape and avoids internal fogging.
3.eSlow Down for Cooling: ON — Improves surface finish with controlled cooling.
3.fForce Cooling for Overhangs: OFF — Overcooling can deform bridges in Timeplast.
3.gFan for Overhangs: 15% — Only for essential cooling in complex areas.
3.hPre-Start Fan Time: 2 seconds — Minimizes pressure differential during the first layer.4. Volumetric Flow
4.aMax Volumetric Speed: 12 mm³/s — Based on a melt flow index of ~15 g/10min, allows high-speed printing.
4.bRamming Speed: 3 mm³/s — Prevents bubbles or popping from pressure spikes.5. Retraction and Flow
5.aRetraction Distance: 0.4 mm — Minimal retraction required for soft filaments to avoid stringing.
5.bRetraction Speed: 15 mm/s — Slow enough to avoid pulling molten plastic.
5.cPressure Advance: 0.05 — Compensates for nozzle lag at high flow rates.
5.dFlow Ratio: 92% — Slight under-extrusion avoids swelling and surface artifacts.6. Precision Settings
6.aGap Closing Radius: 0.1 mm — Tolerant of gaps in thicker walls.
6.bArc Fitting: ON — Reduces G-code size and smooths curve transitions.
6.cElephant Foot Compensation: 0.1 mm — Offsets squishing in the first layer caused by large bead sizes.7. Walls and Shells
7.aWall Loops: 2 — Minimum for strength when using a 0.8 mm nozzle.
7.bDetect Thin Walls: ON — Ensures tight geometries aren’t skipped.
7.cTop/Bottom Shell Layers: 3 — Provides good coverage; increase if watertightness is needed.
7.dTop/Bottom Thickness: 1.2 mm — Equals 1.5x the nozzle size for solid strength.
7.eTop/Bottom Pattern: Monotonic — Distributes tension evenly and improves surface finish.8. Geometry and Movement
8.aWall Order: Inner before Outer — Creates cleaner outer surfaces.
8.bInfill First: OFF — Maintains precise outer dimensions.
8.cSmooth Speed Transition: ON — Prevents ringing caused by abrupt speed changes.
8.dSmooth Coefficient: 80 — Ideal damping for soft materials.
8.eAvoid Crossing Wall: ON — Minimizes stringing across part walls.
8.fMax Detour for Crossing: 10 mm or 5% — Balances time with print cleanliness.9. Layer and Width Settings
9.aLayer Height: 0.3 mm — Optimal for strength and resolution using a 0.8 mm nozzle.
9.bInitial Layer Height: 0.35 mm — Slightly higher to improve adhesion.
9.cLine Widths (all): 0.8 mm — Matches nozzle diameter for consistent extrusion.10. Seam Settings
10.aSeam Position: Aligned or Back — Use aligned for mechanical consistency, back for visual appeal.
10.bSmart Scarf Seam: ON — Automatically adjusts seam location to reduce visual impact.
10.cSeam Angle: 155° — Standard seam angle for clean transitions.
10.dSeam Steps: 10 — Smooths seam path and improves visual finish.11. Infill Settings
11.aWall/Infill Overlap: 10% — Prevents infill from deforming soft exterior walls.
11.bInfill Combination: ON — Consolidates paths for efficiency.
11.cDetect Floating Shells: ON — Ensures unsupported vertical structures are printed reliably.
11.dSparse Infill Density: 20–25% — Balanced rigidity vs. material use.
11.eSparse Pattern: Grid — Stable and efficient for flexible geometries.12. Speed Settings
12.aTravel: 160 mm/s — Fast but safe against backlash.
12.bInitial Layer: 15 mm/s — Prevents nozzle from skimming and ensures bed adhesion.
12.cOuter Wall: 60 mm/s — Controlled speed for surface quality.
12.dInner Wall: 90 mm/s — Slightly faster without compromising control.
12.eSmall Perimeter: 35 mm/s — Reduced speed for detailed geometry.
12.fTop Surface: 40 mm/s — Improves finish on topmost layers.
12.gInfill: 100–120 mm/s — Takes advantage of high flowability.13. Acceleration Settings
13.aNormal Print: 2000 mm/s² — Prevents ringing in soft filaments.
13.bTravel: 4000 mm/s² — Enables fast movement without harsh transitions.
13.cInitial Layer: 300 mm/s² — Gentle movement prevents lifting from the bed.
13.dOuter Wall: 1500 mm/s² — Improves outer surface clarity.
13.eInner Wall: 2000 mm/s² — Balanced for structural components.
13.fTop Surface: 1500 mm/s² — Ensures smooth detailing.14. Adhesion and Brims
14.aSkirt Loops: 2 — Helps prime nozzle and start cleanly.
14.bBrim Width: 6 mm — Helps hold soft materials down.
14.cBrim Gap: 0.15 mm — Allows for easy removal without tearing.15. Prime Tower and Flush Settings
15.aPrime Tower: ON — Purges moisture and early flow inconsistencies.
15.bTower Width: 40 mm — Prevents collapse due to heat.
15.cBrim Width (Tower): 4 mm — Adds stability to the purge base.
15.dFlush Into Support: ON — Discards unwanted early flow safely.16. G-Code Start Script
M900 K0.05 ; Pressure Advance M106 S0 ; Fan off G92 E0 G1 E15 F300 ; purge line G92 E0
17. Additional Notes
17.aDry filament at 100°C for 2 hours before use.
17.bStore with desiccant.
17.cKeep extruder door open to allow vapor to escape.
17.dAvoid long dwell times at high temperatures.If you need print settings for other nozzle sizes, feel free to reach out to us at timeplast@timeplast.com — we’ll be happy to help.
You can also get instant support through our dedicated ChatGPT assistant here:https://chatgpt.com/g/g-6823924241cc8191bbabcf0bc6523e3f-timemass-4d-printing🚀
Free U.S. standard shipping on orders of 5+ spools!
Custom colors for 5+ same-type spools’ orders
Scientific Exploration
Fiber
-
TimeMass Fiber incorporates sacrificial polymer technology, which enables specific portions of the material to dissolve in a controlled manner. This feature is especially valuable in 3D printed soft fabrics, due to the small diameter of the remaining fibers. It is also used for advanced manufacturing and prototyping, as it allows for internal embedded supports, temporary reinforcements, or multi-material prints that transition over time.
After successfully printing an intricate fabric-like object using our TimeMass Fiber filament, you’ll need to submerge it in water for a period directly proportional to the softness you want to achieve.
For very soft fabrics, soak the object for 24 to 48 hours, depending on its thickness. The longer it remains submerged, the more of the sacrificial polymer will dissolve, leaving behind finer and more delicate fibers.
After the water treatment, it’s crucial to properly dry the material to finalize its structure. You can air-dry it in the sun or use a food dehydrator for a controlled process. The level of drying will directly impact the final texture—the more it dries, the firmer it becomes.
Mastering this filament involves experimentation, as balancing water exposure and drying time allows you to tailor the fabric’s softness to your specific needs and creative ideas.
How Sacrificial Polymer Technology Works in Time-Mass Fiber
Dual-Phase Composition – The filament consists of a durable, fiber-reinforced phase and a strategically embedded sacrificial polymer that weakens under water.
Post-Processing Activation – After printing, the sacrificial polymer can be removed through dissolution, thermal degradation, or mechanical peeling, leaving behind the intended final structure.
Self-Optimizing Material – The controlled removal of the sacrificial polymer can reduce weight, create internal channels, or improve flexibility in certain regions of the printed object.
Enhanced Printability – This technology ensures complex geometries print more reliably by integrating internal support structures that disappear when no longer needed.
Need Ideas? Here You Go:
Structural Components – Ideal for lightweight but strong or very soft parts in aerospace, automotive, and robotics. Depending on the sacrificial treatment.
Load-Bearing Prototypes – Useful for creating prototypes that need mechanical stress testing.
Sports Equipment & Protective Gear – Can be used in helmets, padding, and high-impact sports gear.
Medical Devices & Braces – Suitable for orthopedic supports and custom medical applications.
High-Performance Tooling – Can be used in jigs, fixtures, and manufacturing tools that require resilience.
Sustainable Consumer Products – Could be applied in eco-friendly furniture, accessories, or industrial design projects.
-
Click here to access our specialized TimeMass GPT Assistant.Just tell it your printer model and the TimeMass filament you're using—it will instantly recommend the exact parameters you need to start printing successfully.
Using a Bambu Lab printer?
Click here to download our updated Bambu Lab profile. All printing parameters are fully optimized and tested—just load the file and start printing.These parameters are designed to help avoid printing issues; however, temperatures and speed timings can be adjusted based on your specific goals. For example, if you prefer a less rigid result, we recommend using a lower temperature. This is the printing reference for TimeMass Fiber filament, tested on the Bambu Labs A1 printer, and optimized for 0.2 mm, 0.4 mm, 0.6 mm, and 0.8 mm nozzles. TimeMass Fiber is more thermally sensitive and features a dual-phase structure, which emits more vapor during printing. It benefits from careful temperature ramping and reduced internal pressure. All settings are specifically optimized to reduce bubbling, fogging, and material instability. If the print fails, it is recommended to lower the nozzle temperature by 10°C and restart until optimal results are achieved. While these examples were printed with a 0.8 mm nozzle, TimeMass can be used with any nozzle size. Please check the manual for printing parameters with all the other nozzle sizes.
Temperature Settings vary by nozzle. For a 0.2 mm nozzle, set the nozzle temperature to 215°C and the bed to 60°C, optimizing for lower flow, finer bead, and less thermal stress. For 0.4 mm, use 225°C nozzle temperature and 60°C bed temperature to maintain melt uniformity for the encapsulated blend. The 0.6 mm nozzle works best at 230°C to ensure stable output for larger extrusion volumes, while the 0.8 mm nozzle should be set to 235°C, helping vapor escape from the larger filament volume without causing clogs. A textured PEI plate is required for adhesion—avoid smooth platesunless properly primed.
Cooling Settings should disable cooling for the first 3 layers to prevent fog formation under sensors. Set the fan minimum speed to 0% for the first 100 seconds to allow vapor to escape without becoming trapped. The maximum fan speed should be limited to 10–15%, preventing filament oval deformation. Keep the fan always off to avoid thermal shock and material stiffening mid-print. Do not force cooling on overhangs, and use only minimal airflow (10–15%)for structural overhangs.
Maximum Volumetric Flow varies per nozzle. For 0.2 mm, keep the flow at 1.5 mm³/s, which is sensitive to clogging due to low melt strength. For 0.4 mm, set it at 4 mm³/s, balancing for higher viscosity variance. The 0.6 mm should run at 6 mm³/s, avoiding pressure spikes and bubbles, and the 0.8 mm at 9 mm³/s, preventing vapor entrapment and melt lag. Ramming speed should be adjusted between 1–3 mm³/s depending on your purge tower strategy.
Retraction and Pressure Advance should be configured as follows: for a 0.2 mm nozzle, use a retraction distance of 0.7 mm at 20 mm/s speed, with a pressure advance of 0.04. For 0.4 mm, use 0.6 mm retraction, 18 mm/s speed, and 0.045 pressure advance. The 0.6 mm nozzle requires 0.5 mm retraction, 15 mm/s, and 0.05 advance, and the 0.8 mm nozzle performs best with 0.4 mm retraction, 15 mm/s, and 0.055 pressure advance. These values help manage off-gassing during slowdowns.
For Layer Height and Line Width, use 0.12 mm layer height, 0.18 mm initial layer, and 0.25 mm line width for the 0.2 mm nozzle. For 0.4 mm: 0.2 mm height, 0.22 mm initial, and 0.42 mm width. For 0.6 mm: 0.3 mm height, 0.32 mm initial, and 0.6 mm width. And for 0.8 mm: 0.3 mm height, 0.35 mm initial, and 0.8 mm width.
In terms of Wall, Shell, and Infill Settings, use 3 wall loops and 4 top/bottom shells for 0.2 mm and 0.4 mm nozzles, and 2 wall loops and 3 shells for 0.6 mm and 0.8 mm. Set top/bottom thickness to 1 mm for smaller nozzles and 1.2 mm for larger ones. Sparse infill density should be 30% for 0.2 mm, 25% for 0.4 mm, and 20–25% for 0.6 mm and 0.8 mm. These configurations support vapor containment inside internal zones.
Speed and Acceleration settings are as follows: For travel speed, use 100 mm/s (0.2 mm), 130 mm/s (0.4 mm), 140 mm/s (0.6 mm), and 150 mm/s (0.8 mm). Set outer wall speed to 30 mm/s, 35 mm/s, 45 mm/s, and 55 mm/s, respectively. Infill speed should be 50 mm/s to 100 mm/s, depending on nozzle size. For acceleration, print acceleration should range from 1000 mm/s² (0.2 mm) to 1800 mm/s² (0.8 mm), and travel acceleration from 2500 mm/s² to 4000 mm/s². These values are calibrated to reduce vibration and pressure surges.
For Adhesion and Brims, use 2 skirt loops to purge water vapor early. Set the brim width between 4 and 6 mm to stabilize softened edges during print start. A brim gap of 0.15 mm ensures easy release after printing.
Under Flush, Prime, and G-code, the use of a prime tower is recommended due to the heavy vapor released at the start of the print. Suggested start G-code is:
M900 K[PA] ; Pressure Advance M106 S0 ; Fan off G92 E0 G1 E15 F300 ; purge line G92 E0
Replace [PA] with the pressure advance value corresponding to your nozzle.
Lastly, parameters consistent across all nozzles include: Bed temperature of 60°C with a textured PEI bed, "Avoid crossing walls" set to ON, "Smart seam" ON, a cooling delay of 3 layers, and brim/skirt defaults remain functional. Always dry the filament before use, and it is recommended to print with the door open for optimal ventilation.
If you need print settings for other nozzle sizes or any other assistance, feel free to reach out to us anytime at timeplast@timeplast.com — we’ll be happy to help.
Free U.S. standard shipping on orders of 5+ spools!
Custom colors for 5+ same-type spools’ orders
Sublimation
-
What if a material could transform, disappear, or reshape itself—on demand? TimeMass - Sublimation is a revolutionary microwave-sensitive filament that bypasses the liquid phase, shifting directly from solid to gas. Engineered with sublimation-prone compounds and a high water content, this material responds aggressively to microwave frequencies, enabling controlled vaporization, collapsible structures, and reactive mechanical components.
A New Dimension of Design & Experimentation
- Microwave-Triggered Disappearance – Watch as structures vanish in seconds when exposed to specific heat conditions, leaving behind no messy residue.
- Precision-Controlled Void Creation – Design temporary supports, chambers, or scaffolds that remove themselves at the perfect moment.
- Reactive, Self-Collapsing Mechanisms – Develop pistons, pressure-release valves, or dissolving seals that respond to thermal input.
- Accelerated Future Simulation – Simulate how objects will deform over centuries under exposure to sunlight, geological radiation, or heat by rapidly accelerating their decay process. Researchers, material scientists, and engineers can now study long-term environmental effects in real time—compressing 1,000 years of exposure into minutes.With TimeMass - Sublimation, traditional design limits evaporate—literally.
Where Science Meets Innovation
- Self-Disassembling Prototypes – Create temporary support structures that remove themselves without manual post-processing.
- Smart Manufacturing & Tooling – Use vaporization to clear out internal cavities in 3D-printed molds, forming complex hollow geometries.
- Special Effects & Theatrical Props – Design disappearing objects for immersive experiences, magic tricks, or experimental art installations.
- Transient Mechanical Components – Build heat-activated pistons or self-erasing message systems, perfect for experimental engineering.
- Environmental Aging Simulation – Speed up centuries of degradation to predict how materials, structures, or artifacts will react to extreme environments over time.
- Zero-Waste Printing – No need for dissolving chemicals or breakaway supports—just heat and gone.Engineered for the Future of Fabrication
By harnessing microwave frequencies as an activation trigger, TimeMass - Sublimation unlocks a new class of transient, responsive, and self-removing designs. Whether you're an innovator, engineer, or artist, this filament disrupts conventional 3D printing, replacing permanence with precision-controlled impermanence.
For those who dream of materials that change, disappear, and evolve—TimeMass - Sublimation brings the future into focus, then lets it fade away.
Evolving sculptures, where sections vanish upon activation.
Microwave-driven actuators for experimental soft robotics.
Disappearing piston chambers that create vacuum-driven motion.
Vaporization-based energy release designs.
-
Click here to access our specialized TimeMass GPT Assistant. Just tell it your printer model and the TimeMass filament you're using—it will instantly recommend the exact parameters you need to start printing successfully.
Using a Bambu Lab printer?
Click here to download our updated Bambu Lab profile. All printing parameters are fully optimized and tested—just load the file and start printing.1. Introduction
These parameters are designed to help avoid printing issues; however, temperatures and speed timings can be adjusted based on your specific goals. For example, if you prefer a less rigid result, we recommend using a lower temperature. This section outlines a complete slicing and printing profile for TimeMass Sublimation, tailored for printers with a 0.8 mm nozzle. If the print is not being successful, please lower the nozzle temperature by 10°C and start over until an optimal print is achieved. While these examples were printed with a 0.8 mm nozzle, TimeMass can be used with any nozzle size. Please check the manual for printing parameters with all the other nozzle sizes.2. Temperature Settings
2.aNozzle Temperature: 240°C — Optimal for flowability while avoiding decomposition (which begins around 250°C).
2.bBed Temperature: 95°C — Ensures strong first-layer adhesion and prevents moisture bubbling.
2.cNozzle Temperature Range: 230–245°C — Timeplast melts around 165°C but prints best at 240°C for precise viscosity control.3. Cooling Settings
3.aNo Cooling for First Layers: 3 layers — Prevents shrinkage due to rapid cooling of moisture-rich filament.
3.bFan Minimum Speed: 0% for the first 100 seconds — Allows heat retention during early layers.
3.cFan Maximum Speed: 15% starting at 8 seconds — Avoids overcooling that can lead to warping.
3.dKeep Fan Always On: OFF — Allows vapor to escape and avoids internal fogging.
3.eSlow Down for Cooling: ON — Improves surface finish with controlled cooling.
3.fForce Cooling for Overhangs: OFF — Overcooling can deform bridges in Timeplast.
3.gFan for Overhangs: 15% — Only for essential cooling in complex areas.
3.hPre-Start Fan Time: 2 seconds — Minimizes pressure differential during the first layer.4. Volumetric Flow
4.aMax Volumetric Speed: 12 mm³/s — Based on a melt flow index of ~15 g/10min, allows high-speed printing.
4.bRamming Speed: 3 mm³/s — Prevents bubbles or popping from pressure spikes.5. Retraction and Flow
5.aRetraction Distance: 0.4 mm — Minimal retraction required for soft filaments to avoid stringing.
5.bRetraction Speed: 15 mm/s — Slow enough to avoid pulling molten plastic.
5.cPressure Advance: 0.05 — Compensates for nozzle lag at high flow rates.
5.dFlow Ratio: 92% — Slight under-extrusion avoids swelling and surface artifacts.6. Precision Settings
6.aGap Closing Radius: 0.1 mm — Tolerant of gaps in thicker walls.
6.bArc Fitting: ON — Reduces G-code size and smooths curve transitions.
6.cElephant Foot Compensation: 0.1 mm — Offsets squishing in the first layer caused by large bead sizes.7. Walls and Shells
7.aWall Loops: 2 — Minimum for strength when using a 0.8 mm nozzle.
7.bDetect Thin Walls: ON — Ensures tight geometries aren’t skipped.
7.cTop/Bottom Shell Layers: 3 — Provides good coverage; increase if watertightness is needed.
7.dTop/Bottom Thickness: 1.2 mm — Equals 1.5x the nozzle size for solid strength.
7.eTop/Bottom Pattern: Monotonic — Distributes tension evenly and improves surface finish.8. Geometry and Movement
8.aWall Order: Inner before Outer — Creates cleaner outer surfaces.
8.bInfill First: OFF — Maintains precise outer dimensions.
8.cSmooth Speed Transition: ON — Prevents ringing caused by abrupt speed changes.
8.dSmooth Coefficient: 80 — Ideal damping for soft materials.
8.eAvoid Crossing Wall: ON — Minimizes stringing across part walls.
8.fMax Detour for Crossing: 10 mm or 5% — Balances time with print cleanliness.9. Layer and Width Settings
9.aLayer Height: 0.3 mm — Optimal for strength and resolution using a 0.8 mm nozzle.
9.bInitial Layer Height: 0.35 mm — Slightly higher to improve adhesion.
9.cLine Widths (all): 0.8 mm — Matches nozzle diameter for consistent extrusion.10. Seam Settings
10.aSeam Position: Aligned or Back — Use aligned for mechanical consistency, back for visual appeal.
10.bSmart Scarf Seam: ON — Automatically adjusts seam location to reduce visual impact.
10.cSeam Angle: 155° — Standard seam angle for clean transitions.
10.dSeam Steps: 10 — Smooths seam path and improves visual finish.11. Infill Settings
11.aWall/Infill Overlap: 10% — Prevents infill from deforming soft exterior walls.
11.bInfill Combination: ON — Consolidates paths for efficiency.
11.cDetect Floating Shells: ON — Ensures unsupported vertical structures are printed reliably.
11.dSparse Infill Density: 20–25% — Balanced rigidity vs. material use.
11.eSparse Pattern: Grid — Stable and efficient for flexible geometries.12. Speed Settings
12.aTravel: 160 mm/s — Fast but safe against backlash.
12.bInitial Layer: 15 mm/s — Prevents nozzle from skimming and ensures bed adhesion.
12.cOuter Wall: 60 mm/s — Controlled speed for surface quality.
12.dInner Wall: 90 mm/s — Slightly faster without compromising control.
12.eSmall Perimeter: 35 mm/s — Reduced speed for detailed geometry.
12.fTop Surface: 40 mm/s — Improves finish on topmost layers.
12.gInfill: 100–120 mm/s — Takes advantage of high flowability.13. Acceleration Settings
13.aNormal Print: 2000 mm/s² — Prevents ringing in soft filaments.
13.bTravel: 4000 mm/s² — Enables fast movement without harsh transitions.
13.cInitial Layer: 300 mm/s² — Gentle movement prevents lifting from the bed.
13.dOuter Wall: 1500 mm/s² — Improves outer surface clarity.
13.eInner Wall: 2000 mm/s² — Balanced for structural components.
13.fTop Surface: 1500 mm/s² — Ensures smooth detailing.14. Adhesion and Brims
14.aSkirt Loops: 2 — Helps prime nozzle and start cleanly.
14.bBrim Width: 6 mm — Helps hold soft materials down.
14.cBrim Gap: 0.15 mm — Allows for easy removal without tearing.15. Prime Tower and Flush Settings
15.aPrime Tower: ON — Purges moisture and early flow inconsistencies.
15.bTower Width: 40 mm — Prevents collapse due to heat.
15.cBrim Width (Tower): 4 mm — Adds stability to the purge base.
15.dFlush Into Support: ON — Discards unwanted early flow safely.16. G-Code Start Script
M900 K0.05 ; Pressure Advance M106 S0 ; Fan off G92 E0 G1 E15 F300 ; purge line G92 E0
17. Additional Notes
17.aDry filament at 100°C for 2 hours before use.
17.bStore with desiccant.
17.cKeep extruder door open to allow vapor to escape.
17.dAvoid long dwell times at high temperatures.If you need print settings for other nozzle sizes, feel free to reach out to us at timeplast@timeplast.com — we’ll be happy to help.
Free U.S. standard shipping on orders of 5+ spools!
Custom colors for 5+ same-type spools’ orders
Hydro Gel
-
A moisture-activated, shape-retaining filament that turns into a soft gel after printing. Engineered with Timeplast’s proprietary hydrogel matrix, it absorbs water post-print to become pliable, squishy, and tactile—perfect for soft robotics, aquatic enrichment tools, or sensory tech.
Print. Soak. Transform.
How it works:
Hydrophilic polymer blends absorb and lock in water, expanding the printed structure up to 3x its original volume.
Soak time = behavior – Customize squishiness and size by controlling the submersion duration (1–4 hours).
No solvents. No post-processing. Just water-activated performance.
Core Material Composition:
Hydrogel Matrix: 75% – Creates gel-like consistency through water entrapment
Alcohol-based Polymers: 25% – Maintain structural form pre- and post-swelling
Tunable Softness:
1 hr soak = Slight flex
2–3 hr soak = Full gel feel
4 hr soak = Maximum expansion
Where to use it:
Soft robotics prototypes – Create compliant, adaptive components
Sensory toys – Print stress balls or squishy elements for therapy or fun
Aquarium enrichment – Submersible, gentle-texture objects for aquatic pets
Hydrophilic gaskets – Expands to form watertight seals
-
Click here to access our specialized TimeMass GPT Assistant. Just tell it your printer model and the TimeMass filament you're using—it will instantly recommend the exact parameters you need to start printing successfully.
Using a Bambu Lab printer?
Click here to download our updated Bambu Lab profile. All printing parameters are fully optimized and tested—just load the file and start printing.1. Introduction
These parameters are designed to help avoid printing issues; however, temperatures and speed timings can be adjusted based on your specific goals. For example, if you prefer a less rigid result, we recommend using a lower temperature. This section outlines a complete slicing and printing profile for TimeMass Hydro Gel, tailored for printers with a 0.8 mm nozzle. If the print is not being successful, please lower the nozzle temperature by 10°C and start over until an optimal print is achieved. While these examples were printed with a 0.8 mm nozzle, TimeMass can be used with any nozzle size. Please check the manual for printing parameters with all the other nozzle sizes.2. Temperature Settings
2.aNozzle Temperature: 240°C — Optimal for flowability while avoiding decomposition (which begins around 250°C).
2.bBed Temperature: 95°C — Ensures strong first-layer adhesion and prevents moisture bubbling.
2.cNozzle Temperature Range: 230–245°C — Timeplast melts around 165°C but prints best at 240°C for precise viscosity control.3. Cooling Settings
3.aNo Cooling for First Layers: 3 layers — Prevents shrinkage due to rapid cooling of moisture-rich filament.
3.bFan Minimum Speed: 0% for the first 100 seconds — Allows heat retention during early layers.
3.cFan Maximum Speed: 15% starting at 8 seconds — Avoids overcooling that can lead to warping.
3.dKeep Fan Always On: OFF — Allows vapor to escape and avoids internal fogging.
3.eSlow Down for Cooling: ON — Improves surface finish with controlled cooling.
3.fForce Cooling for Overhangs: OFF — Overcooling can deform bridges in Timeplast.
3.gFan for Overhangs: 15% — Only for essential cooling in complex areas.
3.hPre-Start Fan Time: 2 seconds — Minimizes pressure differential during the first layer.4. Volumetric Flow
4.aMax Volumetric Speed: 12 mm³/s — Based on a melt flow index of ~15 g/10min, allows high-speed printing.
4.bRamming Speed: 3 mm³/s — Prevents bubbles or popping from pressure spikes.5. Retraction and Flow
5.aRetraction Distance: 0.4 mm — Minimal retraction required for soft filaments to avoid stringing.
5.bRetraction Speed: 15 mm/s — Slow enough to avoid pulling molten plastic.
5.cPressure Advance: 0.05 — Compensates for nozzle lag at high flow rates.
5.dFlow Ratio: 92% — Slight under-extrusion avoids swelling and surface artifacts.6. Precision Settings
6.aGap Closing Radius: 0.1 mm — Tolerant of gaps in thicker walls.
6.bArc Fitting: ON — Reduces G-code size and smooths curve transitions.
6.cElephant Foot Compensation: 0.1 mm — Offsets squishing in the first layer caused by large bead sizes.7. Walls and Shells
7.aWall Loops: 2 — Minimum for strength when using a 0.8 mm nozzle.
7.bDetect Thin Walls: ON — Ensures tight geometries aren’t skipped.
7.cTop/Bottom Shell Layers: 3 — Provides good coverage; increase if watertightness is needed.
7.dTop/Bottom Thickness: 1.2 mm — Equals 1.5x the nozzle size for solid strength.
7.eTop/Bottom Pattern: Monotonic — Distributes tension evenly and improves surface finish.8. Geometry and Movement
8.aWall Order: Inner before Outer — Creates cleaner outer surfaces.
8.bInfill First: OFF — Maintains precise outer dimensions.
8.cSmooth Speed Transition: ON — Prevents ringing caused by abrupt speed changes.
8.dSmooth Coefficient: 80 — Ideal damping for soft materials.
8.eAvoid Crossing Wall: ON — Minimizes stringing across part walls.
8.fMax Detour for Crossing: 10 mm or 5% — Balances time with print cleanliness.9. Layer and Width Settings
9.aLayer Height: 0.3 mm — Optimal for strength and resolution using a 0.8 mm nozzle.
9.bInitial Layer Height: 0.35 mm — Slightly higher to improve adhesion.
9.cLine Widths (all): 0.8 mm — Matches nozzle diameter for consistent extrusion.10. Seam Settings
10.aSeam Position: Aligned or Back — Use aligned for mechanical consistency, back for visual appeal.
10.bSmart Scarf Seam: ON — Automatically adjusts seam location to reduce visual impact.
10.cSeam Angle: 155° — Standard seam angle for clean transitions.
10.dSeam Steps: 10 — Smooths seam path and improves visual finish.11. Infill Settings
11.aWall/Infill Overlap: 10% — Prevents infill from deforming soft exterior walls.
11.bInfill Combination: ON — Consolidates paths for efficiency.
11.cDetect Floating Shells: ON — Ensures unsupported vertical structures are printed reliably.
11.dSparse Infill Density: 20–25% — Balanced rigidity vs. material use.
11.eSparse Pattern: Grid — Stable and efficient for flexible geometries.12. Speed Settings
12.aTravel: 160 mm/s — Fast but safe against backlash.
12.bInitial Layer: 15 mm/s — Prevents nozzle from skimming and ensures bed adhesion.
12.cOuter Wall: 60 mm/s — Controlled speed for surface quality.
12.dInner Wall: 90 mm/s — Slightly faster without compromising control.
12.eSmall Perimeter: 35 mm/s — Reduced speed for detailed geometry.
12.fTop Surface: 40 mm/s — Improves finish on topmost layers.
12.gInfill: 100–120 mm/s — Takes advantage of high flowability.13. Acceleration Settings
13.aNormal Print: 2000 mm/s² — Prevents ringing in soft filaments.
13.bTravel: 4000 mm/s² — Enables fast movement without harsh transitions.
13.cInitial Layer: 300 mm/s² — Gentle movement prevents lifting from the bed.
13.dOuter Wall: 1500 mm/s² — Improves outer surface clarity.
13.eInner Wall: 2000 mm/s² — Balanced for structural components.
13.fTop Surface: 1500 mm/s² — Ensures smooth detailing.14. Adhesion and Brims
14.aSkirt Loops: 2 — Helps prime nozzle and start cleanly.
14.bBrim Width: 6 mm — Helps hold soft materials down.
14.cBrim Gap: 0.15 mm — Allows for easy removal without tearing.15. Prime Tower and Flush Settings
15.aPrime Tower: ON — Purges moisture and early flow inconsistencies.
15.bTower Width: 40 mm — Prevents collapse due to heat.
15.cBrim Width (Tower): 4 mm — Adds stability to the purge base.
15.dFlush Into Support: ON — Discards unwanted early flow safely.16. G-Code Start Script
M900 K0.05 ; Pressure Advance M106 S0 ; Fan off G92 E0 G1 E15 F300 ; purge line G92 E0
17. Additional Notes
17.aDry filament at 100°C for 2 hours before use.
17.bStore with desiccant.
17.cKeep extruder door open to allow vapor to escape.
17.dAvoid long dwell times at high temperatures.If you need print settings for other nozzle sizes, feel free to reach out to us at timeplast@timeplast.com — we’ll be happy to help.
Free U.S. standard shipping on orders of 5+ spools!
Custom colors for 5+ same-type spools’ orders
Microwave
-
What if your 3D print could change shape—expand, twist, collapse—without motors, wires, or gears? Just pure microwave energy?
TimeMass Microwave is the first-ever filament that transforms under electromagnetic radiation. No mechanics. Just heat, vapor, and smart geometry doing all the work.
Most thermoplastics ignore microwaves. Ours eats them for breakfast.
It’s made with polar molecular groups that absorb microwave frequencies (yeah, like your food does). Once activated, it heats up from the inside, triggering built-in shape changes—from slow bends to sudden inflations.
How it works:
Microwave activation – UHF radiation excites the polar molecules. Boom: internal heat.
Microfluidic expansion – embedded water vaporizes, causing controlled pressure changes.
Programmable geometry – smart design means you can decide how it transforms.
What can you actually do with this?
Morphing sculptures – kinetic art that moves with invisible waves.
Self-expanding structures – think packaging, architecture, deployable tech.
Soft robotics & smart actuators – no motors needed, just energy.
Interactive displays – things that open, bend, or animate on command.
Space tech – lightweight, compact prints that “deploy” mid-orbit.
Need Ideas? Here You Go:
Transforming sculptures and kinetic art piecesthat change under microwave exposure.
Self-expanding objects, such as soft robotic actuators or deployable structures.
Educational experiments in thermodynamics and microwave interaction physics.
Custom food-safe molds that expand slightly when heated to create precise shaping.
Biomimetic designs, inspired by nature’s shape-shifting structures.
-
Click here to access our specialized TimeMass GPT Assistant. Just tell it your printer model and the TimeMass filament you're using—it will instantly recommend the exact parameters you need to start printing successfully.
Using a Bambu Lab printer?
Click here to download our updated Bambu Lab profile. All printing parameters are fully optimized and tested—just load the file and start printing.1. Introduction
These parameters are designed to help avoid printing issues; however, temperatures and speed timings can be adjusted based on your specific goals. For example, if you prefer a less rigid result, we recommend using a lower temperature. This section outlines a complete slicing and printing profile for TimeMass Microwave, tailored for printers with a 0.8 mm nozzle. If the print is not being successful, please lower the nozzle temperature by 10°C and start over until an optimal print is achieved.While these examples were printed with a 0.8 mm nozzle, TimeMass can be used with any nozzle size. Please check the manual for printing parameters with all the other nozzle sizes.2. Temperature Settings
2.aNozzle Temperature: 240°C — Optimal for flowability while avoiding decomposition (which begins around 250°C).
2.bBed Temperature: 95°C — Ensures strong first-layer adhesion and prevents moisture bubbling.
2.cNozzle Temperature Range: 230–245°C — Timeplast melts around 165°C but prints best at 240°C for precise viscosity control.3. Cooling Settings
3.aNo Cooling for First Layers: 3 layers — Prevents shrinkage due to rapid cooling of moisture-rich filament.
3.bFan Minimum Speed: 0% for the first 100 seconds — Allows heat retention during early layers.
3.cFan Maximum Speed: 15% starting at 8 seconds — Avoids overcooling that can lead to warping.
3.dKeep Fan Always On: OFF — Allows vapor to escape and avoids internal fogging.
3.eSlow Down for Cooling: ON — Improves surface finish with controlled cooling.
3.fForce Cooling for Overhangs: OFF — Overcooling can deform bridges in Timeplast.
3.gFan for Overhangs: 15% — Only for essential cooling in complex areas.
3.hPre-Start Fan Time: 2 seconds — Minimizes pressure differential during the first layer.4. Volumetric Flow
4.aMax Volumetric Speed: 12 mm³/s — Based on a melt flow index of ~15 g/10min, allows high-speed printing.
4.bRamming Speed: 3 mm³/s — Prevents bubbles or popping from pressure spikes.5. Retraction and Flow
5.aRetraction Distance: 0.4 mm — Minimal retraction required for soft filaments to avoid stringing.
5.bRetraction Speed: 15 mm/s — Slow enough to avoid pulling molten plastic.
5.cPressure Advance: 0.05 — Compensates for nozzle lag at high flow rates.
5.dFlow Ratio: 92% — Slight under-extrusion avoids swelling and surface artifacts.6. Precision Settings
6.aGap Closing Radius: 0.1 mm — Tolerant of gaps in thicker walls.
6.bArc Fitting: ON — Reduces G-code size and smooths curve transitions.
6.cElephant Foot Compensation: 0.1 mm — Offsets squishing in the first layer caused by large bead sizes.7. Walls and Shells
7.aWall Loops: 2 — Minimum for strength when using a 0.8 mm nozzle.
7.bDetect Thin Walls: ON — Ensures tight geometries aren’t skipped.
7.cTop/Bottom Shell Layers: 3 — Provides good coverage; increase if watertightness is needed.
7.dTop/Bottom Thickness: 1.2 mm — Equals 1.5x the nozzle size for solid strength.
7.eTop/Bottom Pattern: Monotonic — Distributes tension evenly and improves surface finish.8. Geometry and Movement
8.aWall Order: Inner before Outer — Creates cleaner outer surfaces.
8.bInfill First: OFF — Maintains precise outer dimensions.
8.cSmooth Speed Transition: ON — Prevents ringing caused by abrupt speed changes.
8.dSmooth Coefficient: 80 — Ideal damping for soft materials.
8.eAvoid Crossing Wall: ON — Minimizes stringing across part walls.
8.fMax Detour for Crossing: 10 mm or 5% — Balances time with print cleanliness.9. Layer and Width Settings
9.aLayer Height: 0.3 mm — Optimal for strength and resolution using a 0.8 mm nozzle.
9.bInitial Layer Height: 0.35 mm — Slightly higher to improve adhesion.
9.cLine Widths (all): 0.8 mm — Matches nozzle diameter for consistent extrusion.10. Seam Settings
10.aSeam Position: Aligned or Back — Use aligned for mechanical consistency, back for visual appeal.
10.bSmart Scarf Seam: ON — Automatically adjusts seam location to reduce visual impact.
10.cSeam Angle: 155° — Standard seam angle for clean transitions.
10.dSeam Steps: 10 — Smooths seam path and improves visual finish.11. Infill Settings
11.aWall/Infill Overlap: 10% — Prevents infill from deforming soft exterior walls.
11.bInfill Combination: ON — Consolidates paths for efficiency.
11.cDetect Floating Shells: ON — Ensures unsupported vertical structures are printed reliably.
11.dSparse Infill Density: 20–25% — Balanced rigidity vs. material use.
11.eSparse Pattern: Grid — Stable and efficient for flexible geometries.12. Speed Settings
12.aTravel: 160 mm/s — Fast but safe against backlash.
12.bInitial Layer: 15 mm/s — Prevents nozzle from skimming and ensures bed adhesion.
12.cOuter Wall: 60 mm/s — Controlled speed for surface quality.
12.dInner Wall: 90 mm/s — Slightly faster without compromising control.
12.eSmall Perimeter: 35 mm/s — Reduced speed for detailed geometry.
12.fTop Surface: 40 mm/s — Improves finish on topmost layers.
12.gInfill: 100–120 mm/s — Takes advantage of high flowability.13. Acceleration Settings
13.aNormal Print: 2000 mm/s² — Prevents ringing in soft filaments.
13.bTravel: 4000 mm/s² — Enables fast movement without harsh transitions.
13.cInitial Layer: 300 mm/s² — Gentle movement prevents lifting from the bed.
13.dOuter Wall: 1500 mm/s² — Improves outer surface clarity.
13.eInner Wall: 2000 mm/s² — Balanced for structural components.
13.fTop Surface: 1500 mm/s² — Ensures smooth detailing.14. Adhesion and Brims
14.aSkirt Loops: 2 — Helps prime nozzle and start cleanly.
14.bBrim Width: 6 mm — Helps hold soft materials down.
14.cBrim Gap: 0.15 mm — Allows for easy removal without tearing.15. Prime Tower and Flush Settings
15.aPrime Tower: ON — Purges moisture and early flow inconsistencies.
15.bTower Width: 40 mm — Prevents collapse due to heat.
15.cBrim Width (Tower): 4 mm — Adds stability to the purge base.
15.dFlush Into Support: ON — Discards unwanted early flow safely.16. G-Code Start Script
M900 K0.05 ; Pressure Advance M106 S0 ; Fan off G92 E0 G1 E15 F300 ; purge line G92 E0
17. Additional Notes
17.aDry filament at 100°C for 2 hours before use.
17.bStore with desiccant.
17.cKeep extruder door open to allow vapor to escape.
17.dAvoid long dwell times at high temperatures.If you need print settings for other nozzle sizes, feel free to reach out to us at timeplast@timeplast.com — we’ll be happy to help.
Free U.S. standard shipping on orders of 5+ spools!
Custom colors for 5+ same-type spools’ orders
Water Security
Water Desalination
-
Drink Fresh, Forget Salt
Introducing the groundbreaking Water Desalination filament. Formulated with advanced ionic exchange resins and activated carbon composites, this filament effectively removes marine salts and contaminants from seawater. Print portable desalination filters, survival kits, coastal emergency water systems, and maritime hydration devices, instantly turning seawater into fresh, drinkable water.
Experience unparalleled preparedness and security with TimeMass filaments—designed with cutting-edge materials and technology to ensure your survival, sustainability, and peace of mind.
-
Click here to access our specialized TimeMass GPT Assistant. Just tell it your printer model and the TimeMass filament you're using—it will instantly recommend the exact parameters you need to start printing successfully.
Using a Bambu Lab printer?
Click here to download our updated Bambu Lab profile. All printing parameters are fully optimized and tested—just load the file and start printing.1. Introduction
These parameters are designed to help avoid printing issues; however, temperatures and speed timings can be adjusted based on your specific goals. For example, if you prefer a less rigid result, we recommend using a lower temperature. This section outlines a complete slicing and printing profile for TimeMass Water Desalinization, tailored for printers with a 0.8 mm nozzle. If the print is not being successful, please lower the nozzle temperature by 10°C and start over until an optimal print is achieved. While these examples were printed with a 0.8 mm nozzle, TimeMass can be used with any nozzle size. Please check the manual for printing parameters with all the other nozzle sizes.2. Temperature Settings
2.aNozzle Temperature: 240°C — Optimal for flowability while avoiding decomposition (which begins around 250°C).
2.bBed Temperature: 95°C — Ensures strong first-layer adhesion and prevents moisture bubbling.
2.cNozzle Temperature Range: 230–245°C — Timeplast melts around 165°C but prints best at 240°C for precise viscosity control.3. Cooling Settings
3.aNo Cooling for First Layers: 3 layers — Prevents shrinkage due to rapid cooling of moisture-rich filament.
3.bFan Minimum Speed: 0% for the first 100 seconds — Allows heat retention during early layers.
3.cFan Maximum Speed: 15% starting at 8 seconds — Avoids overcooling that can lead to warping.
3.dKeep Fan Always On: OFF — Allows vapor to escape and avoids internal fogging.
3.eSlow Down for Cooling: ON — Improves surface finish with controlled cooling.
3.fForce Cooling for Overhangs: OFF — Overcooling can deform bridges in Timeplast.
3.gFan for Overhangs: 15% — Only for essential cooling in complex areas.
3.hPre-Start Fan Time: 2 seconds — Minimizes pressure differential during the first layer.4. Volumetric Flow
4.aMax Volumetric Speed: 12 mm³/s — Based on a melt flow index of ~15 g/10min, allows high-speed printing.
4.bRamming Speed: 3 mm³/s — Prevents bubbles or popping from pressure spikes.5. Retraction and Flow
5.aRetraction Distance: 0.4 mm — Minimal retraction required for soft filaments to avoid stringing.
5.bRetraction Speed: 15 mm/s — Slow enough to avoid pulling molten plastic.
5.cPressure Advance: 0.05 — Compensates for nozzle lag at high flow rates.
5.dFlow Ratio: 92% — Slight under-extrusion avoids swelling and surface artifacts.6. Precision Settings
6.aGap Closing Radius: 0.1 mm — Tolerant of gaps in thicker walls.
6.bArc Fitting: ON — Reduces G-code size and smooths curve transitions.
6.cElephant Foot Compensation: 0.1 mm — Offsets squishing in the first layer caused by large bead sizes.7. Walls and Shells
7.aWall Loops: 2 — Minimum for strength when using a 0.8 mm nozzle.
7.bDetect Thin Walls: ON — Ensures tight geometries aren’t skipped.
7.cTop/Bottom Shell Layers: 3 — Provides good coverage; increase if watertightness is needed.
7.dTop/Bottom Thickness: 1.2 mm — Equals 1.5x the nozzle size for solid strength.
7.eTop/Bottom Pattern: Monotonic — Distributes tension evenly and improves surface finish.8. Geometry and Movement
8.aWall Order: Inner before Outer — Creates cleaner outer surfaces.
8.bInfill First: OFF — Maintains precise outer dimensions.
8.cSmooth Speed Transition: ON — Prevents ringing caused by abrupt speed changes.
8.dSmooth Coefficient: 80 — Ideal damping for soft materials.
8.eAvoid Crossing Wall: ON — Minimizes stringing across part walls.
8.fMax Detour for Crossing: 10 mm or 5% — Balances time with print cleanliness.9. Layer and Width Settings
9.aLayer Height: 0.3 mm — Optimal for strength and resolution using a 0.8 mm nozzle.
9.bInitial Layer Height: 0.35 mm — Slightly higher to improve adhesion.
9.cLine Widths (all): 0.8 mm — Matches nozzle diameter for consistent extrusion.10. Seam Settings
10.aSeam Position: Aligned or Back — Use aligned for mechanical consistency, back for visual appeal.
10.bSmart Scarf Seam: ON — Automatically adjusts seam location to reduce visual impact.
10.cSeam Angle: 155° — Standard seam angle for clean transitions.
10.dSeam Steps: 10 — Smooths seam path and improves visual finish.11. Infill Settings
11.aWall/Infill Overlap: 10% — Prevents infill from deforming soft exterior walls.
11.bInfill Combination: ON — Consolidates paths for efficiency.
11.cDetect Floating Shells: ON — Ensures unsupported vertical structures are printed reliably.
11.dSparse Infill Density: 20–25% — Balanced rigidity vs. material use.
11.eSparse Pattern: Grid — Stable and efficient for flexible geometries.12. Speed Settings
12.aTravel: 160 mm/s — Fast but safe against backlash.
12.bInitial Layer: 15 mm/s — Prevents nozzle from skimming and ensures bed adhesion.
12.cOuter Wall: 60 mm/s — Controlled speed for surface quality.
12.dInner Wall: 90 mm/s — Slightly faster without compromising control.
12.eSmall Perimeter: 35 mm/s — Reduced speed for detailed geometry.
12.fTop Surface: 40 mm/s — Improves finish on topmost layers.
12.gInfill: 100–120 mm/s — Takes advantage of high flowability.13. Acceleration Settings
13.aNormal Print: 2000 mm/s² — Prevents ringing in soft filaments.
13.bTravel: 4000 mm/s² — Enables fast movement without harsh transitions.
13.cInitial Layer: 300 mm/s² — Gentle movement prevents lifting from the bed.
13.dOuter Wall: 1500 mm/s² — Improves outer surface clarity.
13.eInner Wall: 2000 mm/s² — Balanced for structural components.
13.fTop Surface: 1500 mm/s² — Ensures smooth detailing.14. Adhesion and Brims
14.aSkirt Loops: 2 — Helps prime nozzle and start cleanly.
14.bBrim Width: 6 mm — Helps hold soft materials down.
14.cBrim Gap: 0.15 mm — Allows for easy removal without tearing.15. Prime Tower and Flush Settings
15.aPrime Tower: ON — Purges moisture and early flow inconsistencies.
15.bTower Width: 40 mm — Prevents collapse due to heat.
15.cBrim Width (Tower): 4 mm — Adds stability to the purge base.
15.dFlush Into Support: ON — Discards unwanted early flow safely.16. G-Code Start Script
M900 K0.05 ; Pressure Advance M106 S0 ; Fan off G92 E0 G1 E15 F300 ; purge line G92 E0
17. Additional Notes
17.aDry filament at 100°C for 2 hours before use.
17.bStore with desiccant.
17.cKeep extruder door open to allow vapor to escape.
17.dAvoid long dwell times at high temperatures.If you need print settings for other nozzle sizes, feel free to reach out to us at timeplast@timeplast.com — we’ll be happy to help.
Free U.S. standard shipping on orders of 5+ spools!
Custom colors for 5+ same-type spools’ orders
Water Retainer
-
Water-Holding Innovation
Harness water retention like never before with Water Retainer filament. Engineered with hydrogel-forming polymer composites, this filament absorbs, retains, and gradually releases water when needed. Prints swell upon water exposure, providing passive cooling, soil hydration, and prolonged moisture release. Applications include smart irrigation systems, plant hydration capsules, cooling garments, moisture-responsive insulation, and eco-friendly agriculture and landscaping aids.
-
Click here to access our specialized TimeMass GPT Assistant. Just tell it your printer model and the TimeMass filament you're using—it will instantly recommend the exact parameters you need to start printing successfully.
Using a Bambu Lab printer?
Click here to download our updated Bambu Lab profile. All printing parameters are fully optimized and tested—just load the file and start printing.1. Introduction
These parameters are designed to help avoid printing issues; however, temperatures and speed timings can be adjusted based on your specific goals. For example, if you prefer a less rigid result, we recommend using a lower temperature. This section outlines a complete slicing and printing profile for TimeMass Water Retainer, tailored for printers with a 0.8 mm nozzle. If the print is not being successful, please lower the nozzle temperature by 10°C and start over until an optimal print is achieved. While these examples were printed with a 0.8 mm nozzle, TimeMass can be used with any nozzle size. Please check the manual for printing parameters with all the other nozzle sizes.2. Temperature Settings
2.aNozzle Temperature: 240°C — Optimal for flowability while avoiding decomposition (which begins around 250°C).
2.bBed Temperature: 95°C — Ensures strong first-layer adhesion and prevents moisture bubbling.
2.cNozzle Temperature Range: 230–245°C — Timeplast melts around 165°C but prints best at 240°C for precise viscosity control.3. Cooling Settings
3.aNo Cooling for First Layers: 3 layers — Prevents shrinkage due to rapid cooling of moisture-rich filament.
3.bFan Minimum Speed: 0% for the first 100 seconds — Allows heat retention during early layers.
3.cFan Maximum Speed: 15% starting at 8 seconds — Avoids overcooling that can lead to warping.
3.dKeep Fan Always On: OFF — Allows vapor to escape and avoids internal fogging.
3.eSlow Down for Cooling: ON — Improves surface finish with controlled cooling.
3.fForce Cooling for Overhangs: OFF — Overcooling can deform bridges in Timeplast.
3.gFan for Overhangs: 15% — Only for essential cooling in complex areas.
3.hPre-Start Fan Time: 2 seconds — Minimizes pressure differential during the first layer.4. Volumetric Flow
4.aMax Volumetric Speed: 12 mm³/s — Based on a melt flow index of ~15 g/10min, allows high-speed printing.
4.bRamming Speed: 3 mm³/s — Prevents bubbles or popping from pressure spikes.5. Retraction and Flow
5.aRetraction Distance: 0.4 mm — Minimal retraction required for soft filaments to avoid stringing.
5.bRetraction Speed: 15 mm/s — Slow enough to avoid pulling molten plastic.
5.cPressure Advance: 0.05 — Compensates for nozzle lag at high flow rates.
5.dFlow Ratio: 92% — Slight under-extrusion avoids swelling and surface artifacts.6. Precision Settings
6.aGap Closing Radius: 0.1 mm — Tolerant of gaps in thicker walls.
6.bArc Fitting: ON — Reduces G-code size and smooths curve transitions.
6.cElephant Foot Compensation: 0.1 mm — Offsets squishing in the first layer caused by large bead sizes.7. Walls and Shells
7.aWall Loops: 2 — Minimum for strength when using a 0.8 mm nozzle.
7.bDetect Thin Walls: ON — Ensures tight geometries aren’t skipped.
7.cTop/Bottom Shell Layers: 3 — Provides good coverage; increase if watertightness is needed.
7.dTop/Bottom Thickness: 1.2 mm — Equals 1.5x the nozzle size for solid strength.
7.eTop/Bottom Pattern: Monotonic — Distributes tension evenly and improves surface finish.8. Geometry and Movement
8.aWall Order: Inner before Outer — Creates cleaner outer surfaces.
8.bInfill First: OFF — Maintains precise outer dimensions.
8.cSmooth Speed Transition: ON — Prevents ringing caused by abrupt speed changes.
8.dSmooth Coefficient: 80 — Ideal damping for soft materials.
8.eAvoid Crossing Wall: ON — Minimizes stringing across part walls.
8.fMax Detour for Crossing: 10 mm or 5% — Balances time with print cleanliness.9. Layer and Width Settings
9.aLayer Height: 0.3 mm — Optimal for strength and resolution using a 0.8 mm nozzle.
9.bInitial Layer Height: 0.35 mm — Slightly higher to improve adhesion.
9.cLine Widths (all): 0.8 mm — Matches nozzle diameter for consistent extrusion.10. Seam Settings
10.aSeam Position: Aligned or Back — Use aligned for mechanical consistency, back for visual appeal.
10.bSmart Scarf Seam: ON — Automatically adjusts seam location to reduce visual impact.
10.cSeam Angle: 155° — Standard seam angle for clean transitions.
10.dSeam Steps: 10 — Smooths seam path and improves visual finish.11. Infill Settings
11.aWall/Infill Overlap: 10% — Prevents infill from deforming soft exterior walls.
11.bInfill Combination: ON — Consolidates paths for efficiency.
11.cDetect Floating Shells: ON — Ensures unsupported vertical structures are printed reliably.
11.dSparse Infill Density: 20–25% — Balanced rigidity vs. material use.
11.eSparse Pattern: Grid — Stable and efficient for flexible geometries.12. Speed Settings
12.aTravel: 160 mm/s — Fast but safe against backlash.
12.bInitial Layer: 15 mm/s — Prevents nozzle from skimming and ensures bed adhesion.
12.cOuter Wall: 60 mm/s — Controlled speed for surface quality.
12.dInner Wall: 90 mm/s — Slightly faster without compromising control.
12.eSmall Perimeter: 35 mm/s — Reduced speed for detailed geometry.
12.fTop Surface: 40 mm/s — Improves finish on topmost layers.
12.gInfill: 100–120 mm/s — Takes advantage of high flowability.13. Acceleration Settings
13.aNormal Print: 2000 mm/s² — Prevents ringing in soft filaments.
13.bTravel: 4000 mm/s² — Enables fast movement without harsh transitions.
13.cInitial Layer: 300 mm/s² — Gentle movement prevents lifting from the bed.
13.dOuter Wall: 1500 mm/s² — Improves outer surface clarity.
13.eInner Wall: 2000 mm/s² — Balanced for structural components.
13.fTop Surface: 1500 mm/s² — Ensures smooth detailing.14. Adhesion and Brims
14.aSkirt Loops: 2 — Helps prime nozzle and start cleanly.
14.bBrim Width: 6 mm — Helps hold soft materials down.
14.cBrim Gap: 0.15 mm — Allows for easy removal without tearing.15. Prime Tower and Flush Settings
15.aPrime Tower: ON — Purges moisture and early flow inconsistencies.
15.bTower Width: 40 mm — Prevents collapse due to heat.
15.cBrim Width (Tower): 4 mm — Adds stability to the purge base.
15.dFlush Into Support: ON — Discards unwanted early flow safely.16. G-Code Start Script
M900 K0.05 ; Pressure Advance M106 S0 ; Fan off G92 E0 G1 E15 F300 ; purge line G92 E0
17. Additional Notes
17.aDry filament at 100°C for 2 hours before use.
17.bStore with desiccant.
17.cKeep extruder door open to allow vapor to escape.
17.dAvoid long dwell times at high temperatures.If you need print settings for other nozzle sizes, feel free to reach out to us at timeplast@timeplast.com — we’ll be happy to help.
You can also get instant support through our dedicated ChatGPT assistant here:https://chatgpt.com/g/g-6823924241cc8191bbabcf0bc6523e3f-timemass-4d-printing🚀
Free U.S. standard shipping on orders of 5+ spools!
Custom colors for 5+ same-type spools’ orders
Air Water Well
-
Infinite Air-to-Water Solution
Transform humidity into endless fresh drinking water with our Air Water Well filament. Utilizing embedded hygroscopic salts (such as calcium chloride and lithium chloride), this filament captures atmospheric moisture overnight. As temperatures rise at dawn, solar-activated additives release the stored water, which condenses into pure, potable water. Applications include printing atmospheric water collectors, portable hydration systems, and emergency water generation devices perfect for air water wells with infinite potential to collect water or for survival in arid climates.
-
Click here to access our specialized TimeMass GPT Assistant. Just tell it your printer model and the TimeMass filament you're using—it will instantly recommend the exact parameters you need to start printing successfully.
Using a Bambu Lab printer?
Click here to download our updated Bambu Lab profile. All printing parameters are fully optimized and tested—just load the file and start printing.1. Introduction
These parameters are designed to help avoid printing issues; however, temperatures and speed timings can be adjusted based on your specific goals. For example, if you prefer a less rigid result, we recommend using a lower temperature. This section outlines a complete slicing and printing profile for TimeMass Air Water Well, tailored for printers with a 0.8 mm nozzle. If the print is not being successful, please lower the nozzle temperature by 10°C and start over until an optimal print is achieved. While these examples were printed with a 0.8 mm nozzle, TimeMass can be used with any nozzle size. Please check the manual for printing parameters with all the other nozzle sizes.2. Temperature Settings
2.aNozzle Temperature: 240°C — Optimal for flowability while avoiding decomposition (which begins around 250°C).
2.bBed Temperature: 95°C — Ensures strong first-layer adhesion and prevents moisture bubbling.
2.cNozzle Temperature Range: 230–245°C — Timeplast melts around 165°C but prints best at 240°C for precise viscosity control.3. Cooling Settings
3.aNo Cooling for First Layers: 3 layers — Prevents shrinkage due to rapid cooling of moisture-rich filament.
3.bFan Minimum Speed: 0% for the first 100 seconds — Allows heat retention during early layers.
3.cFan Maximum Speed: 15% starting at 8 seconds — Avoids overcooling that can lead to warping.
3.dKeep Fan Always On: OFF — Allows vapor to escape and avoids internal fogging.
3.eSlow Down for Cooling: ON — Improves surface finish with controlled cooling.
3.fForce Cooling for Overhangs: OFF — Overcooling can deform bridges in Timeplast.
3.gFan for Overhangs: 15% — Only for essential cooling in complex areas.
3.hPre-Start Fan Time: 2 seconds — Minimizes pressure differential during the first layer.4. Volumetric Flow
4.aMax Volumetric Speed: 12 mm³/s — Based on a melt flow index of ~15 g/10min, allows high-speed printing.
4.bRamming Speed: 3 mm³/s — Prevents bubbles or popping from pressure spikes.5. Retraction and Flow
5.aRetraction Distance: 0.4 mm — Minimal retraction required for soft filaments to avoid stringing.
5.bRetraction Speed: 15 mm/s — Slow enough to avoid pulling molten plastic.
5.cPressure Advance: 0.05 — Compensates for nozzle lag at high flow rates.
5.dFlow Ratio: 92% — Slight under-extrusion avoids swelling and surface artifacts.6. Precision Settings
6.aGap Closing Radius: 0.1 mm — Tolerant of gaps in thicker walls.
6.bArc Fitting: ON — Reduces G-code size and smooths curve transitions.
6.cElephant Foot Compensation: 0.1 mm — Offsets squishing in the first layer caused by large bead sizes.7. Walls and Shells
7.aWall Loops: 2 — Minimum for strength when using a 0.8 mm nozzle.
7.bDetect Thin Walls: ON — Ensures tight geometries aren’t skipped.
7.cTop/Bottom Shell Layers: 3 — Provides good coverage; increase if watertightness is needed.
7.dTop/Bottom Thickness: 1.2 mm — Equals 1.5x the nozzle size for solid strength.
7.eTop/Bottom Pattern: Monotonic — Distributes tension evenly and improves surface finish.8. Geometry and Movement
8.aWall Order: Inner before Outer — Creates cleaner outer surfaces.
8.bInfill First: OFF — Maintains precise outer dimensions.
8.cSmooth Speed Transition: ON — Prevents ringing caused by abrupt speed changes.
8.dSmooth Coefficient: 80 — Ideal damping for soft materials.
8.eAvoid Crossing Wall: ON — Minimizes stringing across part walls.
8.fMax Detour for Crossing: 10 mm or 5% — Balances time with print cleanliness.9. Layer and Width Settings
9.aLayer Height: 0.3 mm — Optimal for strength and resolution using a 0.8 mm nozzle.
9.bInitial Layer Height: 0.35 mm — Slightly higher to improve adhesion.
9.cLine Widths (all): 0.8 mm — Matches nozzle diameter for consistent extrusion.10. Seam Settings
10.aSeam Position: Aligned or Back — Use aligned for mechanical consistency, back for visual appeal.
10.bSmart Scarf Seam: ON — Automatically adjusts seam location to reduce visual impact.
10.cSeam Angle: 155° — Standard seam angle for clean transitions.
10.dSeam Steps: 10 — Smooths seam path and improves visual finish.11. Infill Settings
11.aWall/Infill Overlap: 10% — Prevents infill from deforming soft exterior walls.
11.bInfill Combination: ON — Consolidates paths for efficiency.
11.cDetect Floating Shells: ON — Ensures unsupported vertical structures are printed reliably.
11.dSparse Infill Density: 20–25% — Balanced rigidity vs. material use.
11.eSparse Pattern: Grid — Stable and efficient for flexible geometries.12. Speed Settings
12.aTravel: 160 mm/s — Fast but safe against backlash.
12.bInitial Layer: 15 mm/s — Prevents nozzle from skimming and ensures bed adhesion.
12.cOuter Wall: 60 mm/s — Controlled speed for surface quality.
12.dInner Wall: 90 mm/s — Slightly faster without compromising control.
12.eSmall Perimeter: 35 mm/s — Reduced speed for detailed geometry.
12.fTop Surface: 40 mm/s — Improves finish on topmost layers.
12.gInfill: 100–120 mm/s — Takes advantage of high flowability.13. Acceleration Settings
13.aNormal Print: 2000 mm/s² — Prevents ringing in soft filaments.
13.bTravel: 4000 mm/s² — Enables fast movement without harsh transitions.
13.cInitial Layer: 300 mm/s² — Gentle movement prevents lifting from the bed.
13.dOuter Wall: 1500 mm/s² — Improves outer surface clarity.
13.eInner Wall: 2000 mm/s² — Balanced for structural components.
13.fTop Surface: 1500 mm/s² — Ensures smooth detailing.14. Adhesion and Brims
14.aSkirt Loops: 2 — Helps prime nozzle and start cleanly.
14.bBrim Width: 6 mm — Helps hold soft materials down.
14.cBrim Gap: 0.15 mm — Allows for easy removal without tearing.15. Prime Tower and Flush Settings
15.aPrime Tower: ON — Purges moisture and early flow inconsistencies.
15.bTower Width: 40 mm — Prevents collapse due to heat.
15.cBrim Width (Tower): 4 mm — Adds stability to the purge base.
15.dFlush Into Support: ON — Discards unwanted early flow safely.16. G-Code Start Script
M900 K0.05 ; Pressure Advance M106 S0 ; Fan off G92 E0 G1 E15 F300 ; purge line G92 E0
17. Additional Notes
17.aDry filament at 100°C for 2 hours before use.
17.bStore with desiccant.
17.cKeep extruder door open to allow vapor to escape.
17.dAvoid long dwell times at high temperatures.If you need print settings for other nozzle sizes, feel free to reach out to us at timeplast@timeplast.com — we’ll be happy to help.
Free U.S. standard shipping on orders of 5+ spools!
Custom colors for 5+ same-type spools’ orders
Water Purifier
-
Safe, Drinkable Water Anywhere
Purify water effortlessly with Water Purifier filament. Infused with antimicrobial silver ions, activated carbon, and iodine microcapsules, this filament creates prints that neutralize harmful bacteria, viruses, and pathogens in water. Applications include portable purification straws, inline filters, gravity-fed purification systems, and emergency water treatment devices, ensuring safe drinking water in minutes.
-
Click here to access our specialized TimeMass GPT Assistant. Just tell it your printer model and the TimeMass filament you're using—it will instantly recommend the exact parameters you need to start printing successfully.
Using a Bambu Lab printer?
Click here to download our updated Bambu Lab profile. All printing parameters are fully optimized and tested—just load the file and start printing.1. Introduction
These parameters are designed to help avoid printing issues; however, temperatures and speed timings can be adjusted based on your specific goals. For example, if you prefer a less rigid result, we recommend using a lower temperature. This section outlines a complete slicing and printing profile for TimeMass Water Purifier, tailored for printers with a 0.8 mm nozzle. If the print is not being successful, please lower the nozzle temperature by 10°C and start over until an optimal print is achieved. While these examples were printed with a 0.8 mm nozzle, TimeMass can be used with any nozzle size. Please check the manual for printing parameters with all the other nozzle sizes.2. Temperature Settings
2.aNozzle Temperature: 240°C — Optimal for flowability while avoiding decomposition (which begins around 250°C).
2.bBed Temperature: 95°C — Ensures strong first-layer adhesion and prevents moisture bubbling.
2.cNozzle Temperature Range: 230–245°C — Timeplast melts around 165°C but prints best at 240°C for precise viscosity control.3. Cooling Settings
3.aNo Cooling for First Layers: 3 layers — Prevents shrinkage due to rapid cooling of moisture-rich filament.
3.bFan Minimum Speed: 0% for the first 100 seconds — Allows heat retention during early layers.
3.cFan Maximum Speed: 15% starting at 8 seconds — Avoids overcooling that can lead to warping.
3.dKeep Fan Always On: OFF — Allows vapor to escape and avoids internal fogging.
3.eSlow Down for Cooling: ON — Improves surface finish with controlled cooling.
3.fForce Cooling for Overhangs: OFF — Overcooling can deform bridges in Timeplast.
3.gFan for Overhangs: 15% — Only for essential cooling in complex areas.
3.hPre-Start Fan Time: 2 seconds — Minimizes pressure differential during the first layer.4. Volumetric Flow
4.aMax Volumetric Speed: 12 mm³/s — Based on a melt flow index of ~15 g/10min, allows high-speed printing.
4.bRamming Speed: 3 mm³/s — Prevents bubbles or popping from pressure spikes.5. Retraction and Flow
5.aRetraction Distance: 0.4 mm — Minimal retraction required for soft filaments to avoid stringing.
5.bRetraction Speed: 15 mm/s — Slow enough to avoid pulling molten plastic.
5.cPressure Advance: 0.05 — Compensates for nozzle lag at high flow rates.
5.dFlow Ratio: 92% — Slight under-extrusion avoids swelling and surface artifacts.6. Precision Settings
6.aGap Closing Radius: 0.1 mm — Tolerant of gaps in thicker walls.
6.bArc Fitting: ON — Reduces G-code size and smooths curve transitions.
6.cElephant Foot Compensation: 0.1 mm — Offsets squishing in the first layer caused by large bead sizes.7. Walls and Shells
7.aWall Loops: 2 — Minimum for strength when using a 0.8 mm nozzle.
7.bDetect Thin Walls: ON — Ensures tight geometries aren’t skipped.
7.cTop/Bottom Shell Layers: 3 — Provides good coverage; increase if watertightness is needed.
7.dTop/Bottom Thickness: 1.2 mm — Equals 1.5x the nozzle size for solid strength.
7.eTop/Bottom Pattern: Monotonic — Distributes tension evenly and improves surface finish.8. Geometry and Movement
8.aWall Order: Inner before Outer — Creates cleaner outer surfaces.
8.bInfill First: OFF — Maintains precise outer dimensions.
8.cSmooth Speed Transition: ON — Prevents ringing caused by abrupt speed changes.
8.dSmooth Coefficient: 80 — Ideal damping for soft materials.
8.eAvoid Crossing Wall: ON — Minimizes stringing across part walls.
8.fMax Detour for Crossing: 10 mm or 5% — Balances time with print cleanliness.9. Layer and Width Settings
9.aLayer Height: 0.3 mm — Optimal for strength and resolution using a 0.8 mm nozzle.
9.bInitial Layer Height: 0.35 mm — Slightly higher to improve adhesion.
9.cLine Widths (all): 0.8 mm — Matches nozzle diameter for consistent extrusion.10. Seam Settings
10.aSeam Position: Aligned or Back — Use aligned for mechanical consistency, back for visual appeal.
10.bSmart Scarf Seam: ON — Automatically adjusts seam location to reduce visual impact.
10.cSeam Angle: 155° — Standard seam angle for clean transitions.
10.dSeam Steps: 10 — Smooths seam path and improves visual finish.11. Infill Settings
11.aWall/Infill Overlap: 10% — Prevents infill from deforming soft exterior walls.
11.bInfill Combination: ON — Consolidates paths for efficiency.
11.cDetect Floating Shells: ON — Ensures unsupported vertical structures are printed reliably.
11.dSparse Infill Density: 20–25% — Balanced rigidity vs. material use.
11.eSparse Pattern: Grid — Stable and efficient for flexible geometries.12. Speed Settings
12.aTravel: 160 mm/s — Fast but safe against backlash.
12.bInitial Layer: 15 mm/s — Prevents nozzle from skimming and ensures bed adhesion.
12.cOuter Wall: 60 mm/s — Controlled speed for surface quality.
12.dInner Wall: 90 mm/s — Slightly faster without compromising control.
12.eSmall Perimeter: 35 mm/s — Reduced speed for detailed geometry.
12.fTop Surface: 40 mm/s — Improves finish on topmost layers.
12.gInfill: 100–120 mm/s — Takes advantage of high flowability.13. Acceleration Settings
13.aNormal Print: 2000 mm/s² — Prevents ringing in soft filaments.
13.bTravel: 4000 mm/s² — Enables fast movement without harsh transitions.
13.cInitial Layer: 300 mm/s² — Gentle movement prevents lifting from the bed.
13.dOuter Wall: 1500 mm/s² — Improves outer surface clarity.
13.eInner Wall: 2000 mm/s² — Balanced for structural components.
13.fTop Surface: 1500 mm/s² — Ensures smooth detailing.14. Adhesion and Brims
14.aSkirt Loops: 2 — Helps prime nozzle and start cleanly.
14.bBrim Width: 6 mm — Helps hold soft materials down.
14.cBrim Gap: 0.15 mm — Allows for easy removal without tearing.15. Prime Tower and Flush Settings
15.aPrime Tower: ON — Purges moisture and early flow inconsistencies.
15.bTower Width: 40 mm — Prevents collapse due to heat.
15.cBrim Width (Tower): 4 mm — Adds stability to the purge base.
15.dFlush Into Support: ON — Discards unwanted early flow safely.16. G-Code Start Script
M900 K0.05 ; Pressure Advance M106 S0 ; Fan off G92 E0 G1 E15 F300 ; purge line G92 E0
17. Additional Notes
17.aDry filament at 100°C for 2 hours before use.
17.bStore with desiccant.
17.cKeep extruder door open to allow vapor to escape.
17.dAvoid long dwell times at high temperatures.If you need print settings for other nozzle sizes, feel free to reach out to us at timeplast@timeplast.com — we’ll be happy to help.
Free U.S. standard shipping on orders of 5+ spools!
Custom colors for 5+ same-type spools’ orders
Meaningful Prints
Urn
-
The passing of a loved one is a moment of profound loss, but also an opportunity to honor their life in a way that is as unique as they were.
TimeMass - Urn is a thoughtfully crafted 4D-filament, designed to provide a respectful, beautiful, and meaningful way to create a custom urn for someone dear.
Imagine a farewell that merges remembrance with renewal—an urn that floats gently upon the water, carrying the ashes of a loved one under the night sky. As it dissolves, it leaves behind something greater: Lotus seeds, symbolizing rebirth and enlightenment across many cultures, and Kelp spores, fostering new marine life in the waters that embrace them.
Crafted from planet-neutral, water-soluble materials, TimeMass - Urn is infused with:
Lotus Seeds (Nelumbo nucifera) – representing purity, spiritual awakening, and the cycle of life.
Kelp Spores (Macrocystis pyrifera) – nourishing marine environments, sustaining underwater ecosystems.
Crushed Coral (Calcium Carbonate) – aiding reef regeneration and symbolizing eternal connection to the ocean.If combined with TimeMass Fire, Light, or Glow, you can create a one-of-a-kind urn that glows softly in the twilight, offering a final radiant tribute before gracefully dissolving into the water.
As TimeMass - Urn gently breaks down, it disperses its embedded elements to support aquatic ecosystems—a final act of giving, turning loss into renewal, and remembrance into life.
For those seeking a farewell as beautiful as the life it honors, TimeMass - Urn offers a serene, unforgettable goodbye—one that echoes in the waters and hearts forever.
Need Ideas? Here You Go:
Floating urns for ceremonies, allowing ashes to be released into natural waters.
Commemorative sculptures that gradually dissolve over time, leaving no waste.
Aquatic life-support structures, such as artificial reef foundations or eco-art projects.
Eco-conscious time capsules that release elements into the water when needed.
-
Click here to access our specialized TimeMass GPT Assistant. Just tell it your printer model and the TimeMass filament you're using—it will instantly recommend the exact parameters you need to start printing successfully.
Using a Bambu Lab printer?
Click here to download our updated Bambu Lab profile. All printing parameters are fully optimized and tested—just load the file and start printing.1. Introduction
These parameters are designed to help avoid printing issues; however, temperatures and speed timings can be adjusted based on your specific goals. For example, if you prefer a less rigid result, we recommend using a lower temperature. This section outlines a complete slicing and printing profile for TimeMass Urn, tailored for printers with a 0.8 mm nozzle. If the print is not being successful, please lower the nozzle temperature by 10°C and start over until an optimal print is achieved. While these examples were printed with a 0.8 mm nozzle, TimeMass can be used with any nozzle size. Please check the manual for printing parameters with all the other nozzle sizes.2. Temperature Settings
2.aNozzle Temperature: 240°C — Optimal for flowability while avoiding decomposition (which begins around 250°C).
2.bBed Temperature: 95°C — Ensures strong first-layer adhesion and prevents moisture bubbling.
2.cNozzle Temperature Range: 230–245°C — Timeplast melts around 165°C but prints best at 240°C for precise viscosity control.3. Cooling Settings
3.aNo Cooling for First Layers: 3 layers — Prevents shrinkage due to rapid cooling of moisture-rich filament.
3.bFan Minimum Speed: 0% for the first 100 seconds — Allows heat retention during early layers.
3.cFan Maximum Speed: 15% starting at 8 seconds — Avoids overcooling that can lead to warping.
3.dKeep Fan Always On: OFF — Allows vapor to escape and avoids internal fogging.
3.eSlow Down for Cooling: ON — Improves surface finish with controlled cooling.
3.fForce Cooling for Overhangs: OFF — Overcooling can deform bridges in Timeplast.
3.gFan for Overhangs: 15% — Only for essential cooling in complex areas.
3.hPre-Start Fan Time: 2 seconds — Minimizes pressure differential during the first layer.4. Volumetric Flow
4.aMax Volumetric Speed: 12 mm³/s — Based on a melt flow index of ~15 g/10min, allows high-speed printing.
4.bRamming Speed: 3 mm³/s — Prevents bubbles or popping from pressure spikes.5. Retraction and Flow
5.aRetraction Distance: 0.4 mm — Minimal retraction required for soft filaments to avoid stringing.
5.bRetraction Speed: 15 mm/s — Slow enough to avoid pulling molten plastic.
5.cPressure Advance: 0.05 — Compensates for nozzle lag at high flow rates.
5.dFlow Ratio: 92% — Slight under-extrusion avoids swelling and surface artifacts.6. Precision Settings
6.aGap Closing Radius: 0.1 mm — Tolerant of gaps in thicker walls.
6.bArc Fitting: ON — Reduces G-code size and smooths curve transitions.
6.cElephant Foot Compensation: 0.1 mm — Offsets squishing in the first layer caused by large bead sizes.7. Walls and Shells
7.aWall Loops: 2 — Minimum for strength when using a 0.8 mm nozzle.
7.bDetect Thin Walls: ON — Ensures tight geometries aren’t skipped.
7.cTop/Bottom Shell Layers: 3 — Provides good coverage; increase if watertightness is needed.
7.dTop/Bottom Thickness: 1.2 mm — Equals 1.5x the nozzle size for solid strength.
7.eTop/Bottom Pattern: Monotonic — Distributes tension evenly and improves surface finish.8. Geometry and Movement
8.aWall Order: Inner before Outer — Creates cleaner outer surfaces.
8.bInfill First: OFF — Maintains precise outer dimensions.
8.cSmooth Speed Transition: ON — Prevents ringing caused by abrupt speed changes.
8.dSmooth Coefficient: 80 — Ideal damping for soft materials.
8.eAvoid Crossing Wall: ON — Minimizes stringing across part walls.
8.fMax Detour for Crossing: 10 mm or 5% — Balances time with print cleanliness.9. Layer and Width Settings
9.aLayer Height: 0.3 mm — Optimal for strength and resolution using a 0.8 mm nozzle.
9.bInitial Layer Height: 0.35 mm — Slightly higher to improve adhesion.
9.cLine Widths (all): 0.8 mm — Matches nozzle diameter for consistent extrusion.10. Seam Settings
10.aSeam Position: Aligned or Back — Use aligned for mechanical consistency, back for visual appeal.
10.bSmart Scarf Seam: ON — Automatically adjusts seam location to reduce visual impact.
10.cSeam Angle: 155° — Standard seam angle for clean transitions.
10.dSeam Steps: 10 — Smooths seam path and improves visual finish.11. Infill Settings
11.aWall/Infill Overlap: 10% — Prevents infill from deforming soft exterior walls.
11.bInfill Combination: ON — Consolidates paths for efficiency.
11.cDetect Floating Shells: ON — Ensures unsupported vertical structures are printed reliably.
11.dSparse Infill Density: 20–25% — Balanced rigidity vs. material use.
11.eSparse Pattern: Grid — Stable and efficient for flexible geometries.12. Speed Settings
12.aTravel: 160 mm/s — Fast but safe against backlash.
12.bInitial Layer: 15 mm/s — Prevents nozzle from skimming and ensures bed adhesion.
12.cOuter Wall: 60 mm/s — Controlled speed for surface quality.
12.dInner Wall: 90 mm/s — Slightly faster without compromising control.
12.eSmall Perimeter: 35 mm/s — Reduced speed for detailed geometry.
12.fTop Surface: 40 mm/s — Improves finish on topmost layers.
12.gInfill: 100–120 mm/s — Takes advantage of high flowability.13. Acceleration Settings
13.aNormal Print: 2000 mm/s² — Prevents ringing in soft filaments.
13.bTravel: 4000 mm/s² — Enables fast movement without harsh transitions.
13.cInitial Layer: 300 mm/s² — Gentle movement prevents lifting from the bed.
13.dOuter Wall: 1500 mm/s² — Improves outer surface clarity.
13.eInner Wall: 2000 mm/s² — Balanced for structural components.
13.fTop Surface: 1500 mm/s² — Ensures smooth detailing.14. Adhesion and Brims
14.aSkirt Loops: 2 — Helps prime nozzle and start cleanly.
14.bBrim Width: 6 mm — Helps hold soft materials down.
14.cBrim Gap: 0.15 mm — Allows for easy removal without tearing.15. Prime Tower and Flush Settings
15.aPrime Tower: ON — Purges moisture and early flow inconsistencies.
15.bTower Width: 40 mm — Prevents collapse due to heat.
15.cBrim Width (Tower): 4 mm — Adds stability to the purge base.
15.dFlush Into Support: ON — Discards unwanted early flow safely.16. G-Code Start Script
M900 K0.05 ; Pressure Advance M106 S0 ; Fan off G92 E0 G1 E15 F300 ; purge line G92 E0
17. Additional Notes
17.aDry filament at 100°C for 2 hours before use.
17.bStore with desiccant.
17.cKeep extruder door open to allow vapor to escape.
17.dAvoid long dwell times at high temperatures.If you need print settings for other nozzle sizes, feel free to reach out to us at timeplast@timeplast.com — we’ll be happy to help.
Free U.S. standard shipping on orders of 5+ spools!
Custom colors for 5+ same-type spools’ orders
Baby Gender Reveal
-
Delightful Surprises Revealed
Make your gender reveal memorable with Baby Gender Reveal filament. This innovative two-filament kit features one quick-dissolving filament and another durable, vividly colored filament underneath (blue or pink). When immersed in water, the outer filament dissolves swiftly, unveiling the hidden gender-specific color. Applications include personalized gender-reveal objects like figurines, decorative items, keepsake ornaments, customized reveal boxes, or playful gender-reveal party accessories, ensuring an unforgettable reveal experience.
-
Click here to access our specialized TimeMass GPT Assistant. Just tell it your printer model and the TimeMass filament you're using—it will instantly recommend the exact parameters you need to start printing successfully.
Using a Bambu Lab printer?
Click here to download our updated Bambu Lab profile. All printing parameters are fully optimized and tested—just load the file and start printing.1. Introduction
These parameters are designed to help avoid printing issues; however, temperatures and speed timings can be adjusted based on your specific goals. For example, if you prefer a less rigid result, we recommend using a lower temperature. This section outlines a complete slicing and printing profile for TimeMass Baby Gender Reveal, tailored for printers with a 0.8 mm nozzle. If the print is not being successful, please lower the nozzle temperature by 10°C and start over until an optimal print is achieved. While these examples were printed with a 0.8 mm nozzle, TimeMass can be used with any nozzle size. Please check the manual for printing parameters with all the other nozzle sizes.2. Temperature Settings
2.aNozzle Temperature: 240°C — Optimal for flowability while avoiding decomposition (which begins around 250°C).
2.bBed Temperature: 95°C — Ensures strong first-layer adhesion and prevents moisture bubbling.
2.cNozzle Temperature Range: 230–245°C — Timeplast melts around 165°C but prints best at 240°C for precise viscosity control.3. Cooling Settings
3.aNo Cooling for First Layers: 3 layers — Prevents shrinkage due to rapid cooling of moisture-rich filament.
3.bFan Minimum Speed: 0% for the first 100 seconds — Allows heat retention during early layers.
3.cFan Maximum Speed: 15% starting at 8 seconds — Avoids overcooling that can lead to warping.
3.dKeep Fan Always On: OFF — Allows vapor to escape and avoids internal fogging.
3.eSlow Down for Cooling: ON — Improves surface finish with controlled cooling.
3.fForce Cooling for Overhangs: OFF — Overcooling can deform bridges in Timeplast.
3.gFan for Overhangs: 15% — Only for essential cooling in complex areas.
3.hPre-Start Fan Time: 2 seconds — Minimizes pressure differential during the first layer.4. Volumetric Flow
4.aMax Volumetric Speed: 12 mm³/s — Based on a melt flow index of ~15 g/10min, allows high-speed printing.
4.bRamming Speed: 3 mm³/s — Prevents bubbles or popping from pressure spikes.5. Retraction and Flow
5.aRetraction Distance: 0.4 mm — Minimal retraction required for soft filaments to avoid stringing.
5.bRetraction Speed: 15 mm/s — Slow enough to avoid pulling molten plastic.
5.cPressure Advance: 0.05 — Compensates for nozzle lag at high flow rates.
5.dFlow Ratio: 92% — Slight under-extrusion avoids swelling and surface artifacts.6. Precision Settings
6.aGap Closing Radius: 0.1 mm — Tolerant of gaps in thicker walls.
6.bArc Fitting: ON — Reduces G-code size and smooths curve transitions.
6.cElephant Foot Compensation: 0.1 mm — Offsets squishing in the first layer caused by large bead sizes.7. Walls and Shells
7.aWall Loops: 2 — Minimum for strength when using a 0.8 mm nozzle.
7.bDetect Thin Walls: ON — Ensures tight geometries aren’t skipped.
7.cTop/Bottom Shell Layers: 3 — Provides good coverage; increase if watertightness is needed.
7.dTop/Bottom Thickness: 1.2 mm — Equals 1.5x the nozzle size for solid strength.
7.eTop/Bottom Pattern: Monotonic — Distributes tension evenly and improves surface finish.8. Geometry and Movement
8.aWall Order: Inner before Outer — Creates cleaner outer surfaces.
8.bInfill First: OFF — Maintains precise outer dimensions.
8.cSmooth Speed Transition: ON — Prevents ringing caused by abrupt speed changes.
8.dSmooth Coefficient: 80 — Ideal damping for soft materials.
8.eAvoid Crossing Wall: ON — Minimizes stringing across part walls.
8.fMax Detour for Crossing: 10 mm or 5% — Balances time with print cleanliness.9. Layer and Width Settings
9.aLayer Height: 0.3 mm — Optimal for strength and resolution using a 0.8 mm nozzle.
9.bInitial Layer Height: 0.35 mm — Slightly higher to improve adhesion.
9.cLine Widths (all): 0.8 mm — Matches nozzle diameter for consistent extrusion.10. Seam Settings
10.aSeam Position: Aligned or Back — Use aligned for mechanical consistency, back for visual appeal.
10.bSmart Scarf Seam: ON — Automatically adjusts seam location to reduce visual impact.
10.cSeam Angle: 155° — Standard seam angle for clean transitions.
10.dSeam Steps: 10 — Smooths seam path and improves visual finish.11. Infill Settings
11.aWall/Infill Overlap: 10% — Prevents infill from deforming soft exterior walls.
11.bInfill Combination: ON — Consolidates paths for efficiency.
11.cDetect Floating Shells: ON — Ensures unsupported vertical structures are printed reliably.
11.dSparse Infill Density: 20–25% — Balanced rigidity vs. material use.
11.eSparse Pattern: Grid — Stable and efficient for flexible geometries.12. Speed Settings
12.aTravel: 160 mm/s — Fast but safe against backlash.
12.bInitial Layer: 15 mm/s — Prevents nozzle from skimming and ensures bed adhesion.
12.cOuter Wall: 60 mm/s — Controlled speed for surface quality.
12.dInner Wall: 90 mm/s — Slightly faster without compromising control.
12.eSmall Perimeter: 35 mm/s — Reduced speed for detailed geometry.
12.fTop Surface: 40 mm/s — Improves finish on topmost layers.
12.gInfill: 100–120 mm/s — Takes advantage of high flowability.13. Acceleration Settings
13.aNormal Print: 2000 mm/s² — Prevents ringing in soft filaments.
13.bTravel: 4000 mm/s² — Enables fast movement without harsh transitions.
13.cInitial Layer: 300 mm/s² — Gentle movement prevents lifting from the bed.
13.dOuter Wall: 1500 mm/s² — Improves outer surface clarity.
13.eInner Wall: 2000 mm/s² — Balanced for structural components.
13.fTop Surface: 1500 mm/s² — Ensures smooth detailing.14. Adhesion and Brims
14.aSkirt Loops: 2 — Helps prime nozzle and start cleanly.
14.bBrim Width: 6 mm — Helps hold soft materials down.
14.cBrim Gap: 0.15 mm — Allows for easy removal without tearing.15. Prime Tower and Flush Settings
15.aPrime Tower: ON — Purges moisture and early flow inconsistencies.
15.bTower Width: 40 mm — Prevents collapse due to heat.
15.cBrim Width (Tower): 4 mm — Adds stability to the purge base.
15.dFlush Into Support: ON — Discards unwanted early flow safely.16. G-Code Start Script
M900 K0.05 ; Pressure Advance M106 S0 ; Fan off G92 E0 G1 E15 F300 ; purge line G92 E0
17. Additional Notes
17.aDry filament at 100°C for 2 hours before use.
17.bStore with desiccant.
17.cKeep extruder door open to allow vapor to escape.
17.dAvoid long dwell times at high temperatures.If you need print settings for other nozzle sizes, feel free to reach out to us at timeplast@timeplast.com — we’ll be happy to help.
Free U.S. standard shipping on orders of 5+ spools!
Custom colors for 5+ same-type spools’ orders
Repair & Maintenance
Duck Tape
-
Universal Repair Filament
Meet your ultimate repair companion: Duck Tape filament. This water-activated filament incorporates a strong, flexible polymer blend designed for immediate adhesion after being submerged in water and high durability after dried. Print resistant patches, seals, and quick-fix solutions. Ideal applications include emergency repairs on tents, boats, pipes, backpacks, and outdoor gear—stick it, fix it, and forget it.
-
Click here to access our specialized TimeMass GPT Assistant. Just tell it your printer model and the TimeMass filament you're using—it will instantly recommend the exact parameters you need to start printing successfully.
Using a Bambu Lab printer?
Click here to download our updated Bambu Lab profile. All printing parameters are fully optimized and tested—just load the file and start printing.1. Introduction
These parameters are designed to help avoid printing issues; however, temperatures and speed timings can be adjusted based on your specific goals. For example, if you prefer a less rigid result, we recommend using a lower temperature. This section outlines a complete slicing and printing profile for TimeMass Duck Tape, tailored for printers with a 0.8 mm nozzle. If the print is not being successful, please lower the nozzle temperature by 10°C and start over until an optimal print is achieved. While these examples were printed with a 0.8 mm nozzle, TimeMass can be used with any nozzle size. Please check the manual for printing parameters with all the other nozzle sizes.2. Temperature Settings
2.aNozzle Temperature: 240°C — Optimal for flowability while avoiding decomposition (which begins around 250°C).
2.bBed Temperature: 95°C — Ensures strong first-layer adhesion and prevents moisture bubbling.
2.cNozzle Temperature Range: 230–245°C — Timeplast melts around 165°C but prints best at 240°C for precise viscosity control.3. Cooling Settings
3.aNo Cooling for First Layers: 3 layers — Prevents shrinkage due to rapid cooling of moisture-rich filament.
3.bFan Minimum Speed: 0% for the first 100 seconds — Allows heat retention during early layers.
3.cFan Maximum Speed: 15% starting at 8 seconds — Avoids overcooling that can lead to warping.
3.dKeep Fan Always On: OFF — Allows vapor to escape and avoids internal fogging.
3.eSlow Down for Cooling: ON — Improves surface finish with controlled cooling.
3.fForce Cooling for Overhangs: OFF — Overcooling can deform bridges in Timeplast.
3.gFan for Overhangs: 15% — Only for essential cooling in complex areas.
3.hPre-Start Fan Time: 2 seconds — Minimizes pressure differential during the first layer.4. Volumetric Flow
4.aMax Volumetric Speed: 12 mm³/s — Based on a melt flow index of ~15 g/10min, allows high-speed printing.
4.bRamming Speed: 3 mm³/s — Prevents bubbles or popping from pressure spikes.5. Retraction and Flow
5.aRetraction Distance: 0.4 mm — Minimal retraction required for soft filaments to avoid stringing.
5.bRetraction Speed: 15 mm/s — Slow enough to avoid pulling molten plastic.
5.cPressure Advance: 0.05 — Compensates for nozzle lag at high flow rates.
5.dFlow Ratio: 92% — Slight under-extrusion avoids swelling and surface artifacts.6. Precision Settings
6.aGap Closing Radius: 0.1 mm — Tolerant of gaps in thicker walls.
6.bArc Fitting: ON — Reduces G-code size and smooths curve transitions.
6.cElephant Foot Compensation: 0.1 mm — Offsets squishing in the first layer caused by large bead sizes.7. Walls and Shells
7.aWall Loops: 2 — Minimum for strength when using a 0.8 mm nozzle.
7.bDetect Thin Walls: ON — Ensures tight geometries aren’t skipped.
7.cTop/Bottom Shell Layers: 3 — Provides good coverage; increase if watertightness is needed.
7.dTop/Bottom Thickness: 1.2 mm — Equals 1.5x the nozzle size for solid strength.
7.eTop/Bottom Pattern: Monotonic — Distributes tension evenly and improves surface finish.8. Geometry and Movement
8.aWall Order: Inner before Outer — Creates cleaner outer surfaces.
8.bInfill First: OFF — Maintains precise outer dimensions.
8.cSmooth Speed Transition: ON — Prevents ringing caused by abrupt speed changes.
8.dSmooth Coefficient: 80 — Ideal damping for soft materials.
8.eAvoid Crossing Wall: ON — Minimizes stringing across part walls.
8.fMax Detour for Crossing: 10 mm or 5% — Balances time with print cleanliness.9. Layer and Width Settings
9.aLayer Height: 0.3 mm — Optimal for strength and resolution using a 0.8 mm nozzle.
9.bInitial Layer Height: 0.35 mm — Slightly higher to improve adhesion.
9.cLine Widths (all): 0.8 mm — Matches nozzle diameter for consistent extrusion.10. Seam Settings
10.aSeam Position: Aligned or Back — Use aligned for mechanical consistency, back for visual appeal.
10.bSmart Scarf Seam: ON — Automatically adjusts seam location to reduce visual impact.
10.cSeam Angle: 155° — Standard seam angle for clean transitions.
10.dSeam Steps: 10 — Smooths seam path and improves visual finish.11. Infill Settings
11.aWall/Infill Overlap: 10% — Prevents infill from deforming soft exterior walls.
11.bInfill Combination: ON — Consolidates paths for efficiency.
11.cDetect Floating Shells: ON — Ensures unsupported vertical structures are printed reliably.
11.dSparse Infill Density: 20–25% — Balanced rigidity vs. material use.
11.eSparse Pattern: Grid — Stable and efficient for flexible geometries.12. Speed Settings
12.aTravel: 160 mm/s — Fast but safe against backlash.
12.bInitial Layer: 15 mm/s — Prevents nozzle from skimming and ensures bed adhesion.
12.cOuter Wall: 60 mm/s — Controlled speed for surface quality.
12.dInner Wall: 90 mm/s — Slightly faster without compromising control.
12.eSmall Perimeter: 35 mm/s — Reduced speed for detailed geometry.
12.fTop Surface: 40 mm/s — Improves finish on topmost layers.
12.gInfill: 100–120 mm/s — Takes advantage of high flowability.13. Acceleration Settings
13.aNormal Print: 2000 mm/s² — Prevents ringing in soft filaments.
13.bTravel: 4000 mm/s² — Enables fast movement without harsh transitions.
13.cInitial Layer: 300 mm/s² — Gentle movement prevents lifting from the bed.
13.dOuter Wall: 1500 mm/s² — Improves outer surface clarity.
13.eInner Wall: 2000 mm/s² — Balanced for structural components.
13.fTop Surface: 1500 mm/s² — Ensures smooth detailing.14. Adhesion and Brims
14.aSkirt Loops: 2 — Helps prime nozzle and start cleanly.
14.bBrim Width: 6 mm — Helps hold soft materials down.
14.cBrim Gap: 0.15 mm — Allows for easy removal without tearing.15. Prime Tower and Flush Settings
15.aPrime Tower: ON — Purges moisture and early flow inconsistencies.
15.bTower Width: 40 mm — Prevents collapse due to heat.
15.cBrim Width (Tower): 4 mm — Adds stability to the purge base.
15.dFlush Into Support: ON — Discards unwanted early flow safely.16. G-Code Start Script
M900 K0.05 ; Pressure Advance M106 S0 ; Fan off G92 E0 G1 E15 F300 ; purge line G92 E0
17. Additional Notes
17.aDry filament at 100°C for 2 hours before use.
17.bStore with desiccant.
17.cKeep extruder door open to allow vapor to escape.
17.dAvoid long dwell times at high temperatures.If you need print settings for other nozzle sizes, feel free to reach out to us at timeplast@timeplast.com — we’ll be happy to help.
Free U.S. standard shipping on orders of 5+ spools!
Custom colors for 5+ same-type spools’ orders
Seal & Repair
-
When emergencies happen, rely on Seal & Repair filament. Formulated with water-activated adhesive technology and elastic polymer composites, our filament adheres powerfully after dried. Applications include sealing of leaks in containers, surfaces and rapid-response patching in emergencies.
-
Click here to access our specialized TimeMass GPT Assistant. Just tell it your printer model and the TimeMass filament you're using—it will instantly recommend the exact parameters you need to start printing successfully.
Using a Bambu Lab printer?
Click here to download our updated Bambu Lab profile. All printing parameters are fully optimized and tested—just load the file and start printing.1. Introduction
These parameters are designed to help avoid printing issues; however, temperatures and speed timings can be adjusted based on your specific goals. For example, if you prefer a less rigid result, we recommend using a lower temperature. This section outlines a complete slicing and printing profile for TimeMass Seal & Repair, tailored for printers with a 0.8 mm nozzle. If the print is not being successful, please lower the nozzle temperature by 10°C and start over until an optimal print is achieved. While these examples were printed with a 0.8 mm nozzle, TimeMass can be used with any nozzle size. Please check the manual for printing parameters with all the other nozzle sizes.2. Temperature Settings
2.aNozzle Temperature: 240°C — Optimal for flowability while avoiding decomposition (which begins around 250°C).
2.bBed Temperature: 95°C — Ensures strong first-layer adhesion and prevents moisture bubbling.
2.cNozzle Temperature Range: 230–245°C — Timeplast melts around 165°C but prints best at 240°C for precise viscosity control.3. Cooling Settings
3.aNo Cooling for First Layers: 3 layers — Prevents shrinkage due to rapid cooling of moisture-rich filament.
3.bFan Minimum Speed: 0% for the first 100 seconds — Allows heat retention during early layers.
3.cFan Maximum Speed: 15% starting at 8 seconds — Avoids overcooling that can lead to warping.
3.dKeep Fan Always On: OFF — Allows vapor to escape and avoids internal fogging.
3.eSlow Down for Cooling: ON — Improves surface finish with controlled cooling.
3.fForce Cooling for Overhangs: OFF — Overcooling can deform bridges in Timeplast.
3.gFan for Overhangs: 15% — Only for essential cooling in complex areas.
3.hPre-Start Fan Time: 2 seconds — Minimizes pressure differential during the first layer.4. Volumetric Flow
4.aMax Volumetric Speed: 12 mm³/s — Based on a melt flow index of ~15 g/10min, allows high-speed printing.
4.bRamming Speed: 3 mm³/s — Prevents bubbles or popping from pressure spikes.5. Retraction and Flow
5.aRetraction Distance: 0.4 mm — Minimal retraction required for soft filaments to avoid stringing.
5.bRetraction Speed: 15 mm/s — Slow enough to avoid pulling molten plastic.
5.cPressure Advance: 0.05 — Compensates for nozzle lag at high flow rates.
5.dFlow Ratio: 92% — Slight under-extrusion avoids swelling and surface artifacts.6. Precision Settings
6.aGap Closing Radius: 0.1 mm — Tolerant of gaps in thicker walls.
6.bArc Fitting: ON — Reduces G-code size and smooths curve transitions.
6.cElephant Foot Compensation: 0.1 mm — Offsets squishing in the first layer caused by large bead sizes.7. Walls and Shells
7.aWall Loops: 2 — Minimum for strength when using a 0.8 mm nozzle.
7.bDetect Thin Walls: ON — Ensures tight geometries aren’t skipped.
7.cTop/Bottom Shell Layers: 3 — Provides good coverage; increase if watertightness is needed.
7.dTop/Bottom Thickness: 1.2 mm — Equals 1.5x the nozzle size for solid strength.
7.eTop/Bottom Pattern: Monotonic — Distributes tension evenly and improves surface finish.8. Geometry and Movement
8.aWall Order: Inner before Outer — Creates cleaner outer surfaces.
8.bInfill First: OFF — Maintains precise outer dimensions.
8.cSmooth Speed Transition: ON — Prevents ringing caused by abrupt speed changes.
8.dSmooth Coefficient: 80 — Ideal damping for soft materials.
8.eAvoid Crossing Wall: ON — Minimizes stringing across part walls.
8.fMax Detour for Crossing: 10 mm or 5% — Balances time with print cleanliness.9. Layer and Width Settings
9.aLayer Height: 0.3 mm — Optimal for strength and resolution using a 0.8 mm nozzle.
9.bInitial Layer Height: 0.35 mm — Slightly higher to improve adhesion.
9.cLine Widths (all): 0.8 mm — Matches nozzle diameter for consistent extrusion.10. Seam Settings
10.aSeam Position: Aligned or Back — Use aligned for mechanical consistency, back for visual appeal.
10.bSmart Scarf Seam: ON — Automatically adjusts seam location to reduce visual impact.
10.cSeam Angle: 155° — Standard seam angle for clean transitions.
10.dSeam Steps: 10 — Smooths seam path and improves visual finish.11. Infill Settings
11.aWall/Infill Overlap: 10% — Prevents infill from deforming soft exterior walls.
11.bInfill Combination: ON — Consolidates paths for efficiency.
11.cDetect Floating Shells: ON — Ensures unsupported vertical structures are printed reliably.
11.dSparse Infill Density: 20–25% — Balanced rigidity vs. material use.
11.eSparse Pattern: Grid — Stable and efficient for flexible geometries.12. Speed Settings
12.aTravel: 160 mm/s — Fast but safe against backlash.
12.bInitial Layer: 15 mm/s — Prevents nozzle from skimming and ensures bed adhesion.
12.cOuter Wall: 60 mm/s — Controlled speed for surface quality.
12.dInner Wall: 90 mm/s — Slightly faster without compromising control.
12.eSmall Perimeter: 35 mm/s — Reduced speed for detailed geometry.
12.fTop Surface: 40 mm/s — Improves finish on topmost layers.
12.gInfill: 100–120 mm/s — Takes advantage of high flowability.13. Acceleration Settings
13.aNormal Print: 2000 mm/s² — Prevents ringing in soft filaments.
13.bTravel: 4000 mm/s² — Enables fast movement without harsh transitions.
13.cInitial Layer: 300 mm/s² — Gentle movement prevents lifting from the bed.
13.dOuter Wall: 1500 mm/s² — Improves outer surface clarity.
13.eInner Wall: 2000 mm/s² — Balanced for structural components.
13.fTop Surface: 1500 mm/s² — Ensures smooth detailing.14. Adhesion and Brims
14.aSkirt Loops: 2 — Helps prime nozzle and start cleanly.
14.bBrim Width: 6 mm — Helps hold soft materials down.
14.cBrim Gap: 0.15 mm — Allows for easy removal without tearing.15. Prime Tower and Flush Settings
15.aPrime Tower: ON — Purges moisture and early flow inconsistencies.
15.bTower Width: 40 mm — Prevents collapse due to heat.
15.cBrim Width (Tower): 4 mm — Adds stability to the purge base.
15.dFlush Into Support: ON — Discards unwanted early flow safely.16. G-Code Start Script
M900 K0.05 ; Pressure Advance M106 S0 ; Fan off G92 E0 G1 E15 F300 ; purge line G92 E0
17. Additional Notes
17.aDry filament at 100°C for 2 hours before use.
17.bStore with desiccant.
17.cKeep extruder door open to allow vapor to escape.
17.dAvoid long dwell times at high temperatures.If you need print settings for other nozzle sizes, feel free to reach out to us at timeplast@timeplast.com — we’ll be happy to help.
Free U.S. standard shipping on orders of 5+ spools!
Custom colors for 5+ same-type spools’ orders
Iridescent Prints
Iridescent White
-
A rainbow-catching, eye-dazzling filament that changes color depending on the viewing angle or light source. With multi-layer thin-film pigments, this filament gives a prismatic sheen to your prints, ideal for high-fashion, toys, or artistic pieces.
Color-shifting magic, engineered to shine.
How it works:
Interference pigments bend light at different wavelengths, producing a spectrum of reflected hues as you move around the object.
Light angle = color angle.
Core Material:
Iridescent Flake Complex: 28% – Ultra-thin layered pigments
Flexible Transparent Matrix: 72% – Maintains light mobility across surface
Where to use it:
Fashion accessories – Jewelry, hair clips, bags
Futuristic art – Make your prints alive with color
Display models – Eye-catching effects for collectors
Event props – Shine under LEDs or camera lights
-
Click here to access our specialized TimeMass GPT Assistant.Just tell it your printer model and the TimeMass filament you're using—it will instantly recommend the exact parameters you need to start printing successfully.
Using a Bambu Lab printer?
Click here to download our updated Bambu Lab profile. All printing parameters are fully optimized and tested—just load the file and start printing.1. Introduction
These parameters are designed to help avoid printing issues; however, temperatures and speed timings can be adjusted based on your specific goals. For example, if you prefer a less rigid result, we recommend using a lower temperature. This section outlines a complete slicing and printing profile for TimeMass Iridescent White, tailored for printers with a 0.8 mm nozzle. If the print is not being successful, please lower the nozzle temperature by 10°C and start over until an optimal print is achieved.While these examples were printed with a 0.8 mm nozzle, TimeMass can be used with any nozzle size. Please check the manual for printing parameters with all the other nozzle sizes.2. Temperature Settings
2.aNozzle Temperature: 240°C — Optimal for flowability while avoiding decomposition (which begins around 250°C).
2.bBed Temperature: 95°C — Ensures strong first-layer adhesion and prevents moisture bubbling.
2.cNozzle Temperature Range: 230–245°C — Timeplast melts around 165°C but prints best at 240°C for precise viscosity control.3. Cooling Settings
3.aNo Cooling for First Layers: 3 layers — Prevents shrinkage due to rapid cooling of moisture-rich filament.
3.bFan Minimum Speed: 0% for the first 100 seconds — Allows heat retention during early layers.
3.cFan Maximum Speed: 15% starting at 8 seconds — Avoids overcooling that can lead to warping.
3.dKeep Fan Always On: OFF — Allows vapor to escape and avoids internal fogging.
3.eSlow Down for Cooling: ON — Improves surface finish with controlled cooling.
3.fForce Cooling for Overhangs: OFF — Overcooling can deform bridges in Timeplast.
3.gFan for Overhangs: 15% — Only for essential cooling in complex areas.
3.hPre-Start Fan Time: 2 seconds — Minimizes pressure differential during the first layer.4. Volumetric Flow
4.aMax Volumetric Speed: 12 mm³/s — Based on a melt flow index of ~15 g/10min, allows high-speed printing.
4.bRamming Speed: 3 mm³/s — Prevents bubbles or popping from pressure spikes.5. Retraction and Flow
5.aRetraction Distance: 0.4 mm — Minimal retraction required for soft filaments to avoid stringing.
5.bRetraction Speed: 15 mm/s — Slow enough to avoid pulling molten plastic.
5.cPressure Advance: 0.05 — Compensates for nozzle lag at high flow rates.
5.dFlow Ratio: 92% — Slight under-extrusion avoids swelling and surface artifacts.6. Precision Settings
6.aGap Closing Radius: 0.1 mm — Tolerant of gaps in thicker walls.
6.bArc Fitting: ON — Reduces G-code size and smooths curve transitions.
6.cElephant Foot Compensation: 0.1 mm — Offsets squishing in the first layer caused by large bead sizes.7. Walls and Shells
7.aWall Loops: 2 — Minimum for strength when using a 0.8 mm nozzle.
7.bDetect Thin Walls: ON — Ensures tight geometries aren’t skipped.
7.cTop/Bottom Shell Layers: 3 — Provides good coverage; increase if watertightness is needed.
7.dTop/Bottom Thickness: 1.2 mm — Equals 1.5x the nozzle size for solid strength.
7.eTop/Bottom Pattern: Monotonic — Distributes tension evenly and improves surface finish.8. Geometry and Movement
8.aWall Order: Inner before Outer — Creates cleaner outer surfaces.
8.bInfill First: OFF — Maintains precise outer dimensions.
8.cSmooth Speed Transition: ON — Prevents ringing caused by abrupt speed changes.
8.dSmooth Coefficient: 80 — Ideal damping for soft materials.
8.eAvoid Crossing Wall: ON — Minimizes stringing across part walls.
8.fMax Detour for Crossing: 10 mm or 5% — Balances time with print cleanliness.9. Layer and Width Settings
9.aLayer Height: 0.3 mm — Optimal for strength and resolution using a 0.8 mm nozzle.
9.bInitial Layer Height: 0.35 mm — Slightly higher to improve adhesion.
9.cLine Widths (all): 0.8 mm — Matches nozzle diameter for consistent extrusion.10. Seam Settings
10.aSeam Position: Aligned or Back — Use aligned for mechanical consistency, back for visual appeal.
10.bSmart Scarf Seam: ON — Automatically adjusts seam location to reduce visual impact.
10.cSeam Angle: 155° — Standard seam angle for clean transitions.
10.dSeam Steps: 10 — Smooths seam path and improves visual finish.11. Infill Settings
11.aWall/Infill Overlap: 10% — Prevents infill from deforming soft exterior walls.
11.bInfill Combination: ON — Consolidates paths for efficiency.
11.cDetect Floating Shells: ON — Ensures unsupported vertical structures are printed reliably.
11.dSparse Infill Density: 20–25% — Balanced rigidity vs. material use.
11.eSparse Pattern: Grid — Stable and efficient for flexible geometries.12. Speed Settings
12.aTravel: 160 mm/s — Fast but safe against backlash.
12.bInitial Layer: 15 mm/s — Prevents nozzle from skimming and ensures bed adhesion.
12.cOuter Wall: 60 mm/s — Controlled speed for surface quality.
12.dInner Wall: 90 mm/s — Slightly faster without compromising control.
12.eSmall Perimeter: 35 mm/s — Reduced speed for detailed geometry.
12.fTop Surface: 40 mm/s — Improves finish on topmost layers.
12.gInfill: 100–120 mm/s — Takes advantage of high flowability.13. Acceleration Settings
13.aNormal Print: 2000 mm/s² — Prevents ringing in soft filaments.
13.bTravel: 4000 mm/s² — Enables fast movement without harsh transitions.
13.cInitial Layer: 300 mm/s² — Gentle movement prevents lifting from the bed.
13.dOuter Wall: 1500 mm/s² — Improves outer surface clarity.
13.eInner Wall: 2000 mm/s² — Balanced for structural components.
13.fTop Surface: 1500 mm/s² — Ensures smooth detailing.14. Adhesion and Brims
14.aSkirt Loops: 2 — Helps prime nozzle and start cleanly.
14.bBrim Width: 6 mm — Helps hold soft materials down.
14.cBrim Gap: 0.15 mm — Allows for easy removal without tearing.15. Prime Tower and Flush Settings
15.aPrime Tower: ON — Purges moisture and early flow inconsistencies.
15.bTower Width: 40 mm — Prevents collapse due to heat.
15.cBrim Width (Tower): 4 mm — Adds stability to the purge base.
15.dFlush Into Support: ON — Discards unwanted early flow safely.16. G-Code Start Script
M900 K0.05 ; Pressure Advance M106 S0 ; Fan off G92 E0 G1 E15 F300 ; purge line G92 E0
17. Additional Notes
17.aDry filament at 100°C for 2 hours before use.
17.bStore with desiccant.
17.cKeep extruder door open to allow vapor to escape.
17.dAvoid long dwell times at high temperatures.If you need print settings for other nozzle sizes, feel free to reach out to us at timeplast@timeplast.com — we’ll be happy to help.
Free U.S. standard shipping on orders of 5+ spools!
Custom colors for 5+ same-type spools’ orders
Iridescent Pink
-
A rainbow-catching, eye-dazzling filament that changes color depending on the viewing angle or light source. With multi-layer thin-film pigments, this filament gives a prismatic sheen to your prints, ideal for high-fashion, toys, or artistic pieces.
Color-shifting magic, engineered to shine.
How it works:
Interference pigments bend light at different wavelengths, producing a spectrum of reflected hues as you move around the object.
Light angle = color angle.
Core Material:
Iridescent Flake Complex: 28% – Ultra-thin layered pigments
Flexible Transparent Matrix: 72% – Maintains light mobility across surface
Where to use it:
Fashion accessories – Jewelry, hair clips, bags
Futuristic art – Make your prints alive with color
Display models – Eye-catching effects for collectors
Event props – Shine under LEDs or camera lights
-
Click here to access our specialized TimeMass GPT Assistant.Just tell it your printer model and the TimeMass filament you're using—it will instantly recommend the exact parameters you need to start printing successfully.
Using a Bambu Lab printer?
Click here to download our updated Bambu Lab profile. All printing parameters are fully optimized and tested—just load the file and start printing.1. Introduction
These parameters are designed to help avoid printing issues; however, temperatures and speed timings can be adjusted based on your specific goals. For example, if you prefer a less rigid result, we recommend using a lower temperature. This section outlines a complete slicing and printing profile for TimeMass Iridescent Pink, tailored for printers with a 0.8 mm nozzle. If the print is not being successful, please lower the nozzle temperature by 10°C and start over until an optimal print is achieved.While these examples were printed with a 0.8 mm nozzle, TimeMass can be used with any nozzle size. Please check the manual for printing parameters with all the other nozzle sizes.2. Temperature Settings
2.aNozzle Temperature: 240°C — Optimal for flowability while avoiding decomposition (which begins around 250°C).
2.bBed Temperature: 95°C — Ensures strong first-layer adhesion and prevents moisture bubbling.
2.cNozzle Temperature Range: 230–245°C — Timeplast melts around 165°C but prints best at 240°C for precise viscosity control.3. Cooling Settings
3.aNo Cooling for First Layers: 3 layers — Prevents shrinkage due to rapid cooling of moisture-rich filament.
3.bFan Minimum Speed: 0% for the first 100 seconds — Allows heat retention during early layers.
3.cFan Maximum Speed: 15% starting at 8 seconds — Avoids overcooling that can lead to warping.
3.dKeep Fan Always On: OFF — Allows vapor to escape and avoids internal fogging.
3.eSlow Down for Cooling: ON — Improves surface finish with controlled cooling.
3.fForce Cooling for Overhangs: OFF — Overcooling can deform bridges in Timeplast.
3.gFan for Overhangs: 15% — Only for essential cooling in complex areas.
3.hPre-Start Fan Time: 2 seconds — Minimizes pressure differential during the first layer.4. Volumetric Flow
4.aMax Volumetric Speed: 12 mm³/s — Based on a melt flow index of ~15 g/10min, allows high-speed printing.
4.bRamming Speed: 3 mm³/s — Prevents bubbles or popping from pressure spikes.5. Retraction and Flow
5.aRetraction Distance: 0.4 mm — Minimal retraction required for soft filaments to avoid stringing.
5.bRetraction Speed: 15 mm/s — Slow enough to avoid pulling molten plastic.
5.cPressure Advance: 0.05 — Compensates for nozzle lag at high flow rates.
5.dFlow Ratio: 92% — Slight under-extrusion avoids swelling and surface artifacts.6. Precision Settings
6.aGap Closing Radius: 0.1 mm — Tolerant of gaps in thicker walls.
6.bArc Fitting: ON — Reduces G-code size and smooths curve transitions.
6.cElephant Foot Compensation: 0.1 mm — Offsets squishing in the first layer caused by large bead sizes.7. Walls and Shells
7.aWall Loops: 2 — Minimum for strength when using a 0.8 mm nozzle.
7.bDetect Thin Walls: ON — Ensures tight geometries aren’t skipped.
7.cTop/Bottom Shell Layers: 3 — Provides good coverage; increase if watertightness is needed.
7.dTop/Bottom Thickness: 1.2 mm — Equals 1.5x the nozzle size for solid strength.
7.eTop/Bottom Pattern: Monotonic — Distributes tension evenly and improves surface finish.8. Geometry and Movement
8.aWall Order: Inner before Outer — Creates cleaner outer surfaces.
8.bInfill First: OFF — Maintains precise outer dimensions.
8.cSmooth Speed Transition: ON — Prevents ringing caused by abrupt speed changes.
8.dSmooth Coefficient: 80 — Ideal damping for soft materials.
8.eAvoid Crossing Wall: ON — Minimizes stringing across part walls.
8.fMax Detour for Crossing: 10 mm or 5% — Balances time with print cleanliness.9. Layer and Width Settings
9.aLayer Height: 0.3 mm — Optimal for strength and resolution using a 0.8 mm nozzle.
9.bInitial Layer Height: 0.35 mm — Slightly higher to improve adhesion.
9.cLine Widths (all): 0.8 mm — Matches nozzle diameter for consistent extrusion.10. Seam Settings
10.aSeam Position: Aligned or Back — Use aligned for mechanical consistency, back for visual appeal.
10.bSmart Scarf Seam: ON — Automatically adjusts seam location to reduce visual impact.
10.cSeam Angle: 155° — Standard seam angle for clean transitions.
10.dSeam Steps: 10 — Smooths seam path and improves visual finish.11. Infill Settings
11.aWall/Infill Overlap: 10% — Prevents infill from deforming soft exterior walls.
11.bInfill Combination: ON — Consolidates paths for efficiency.
11.cDetect Floating Shells: ON — Ensures unsupported vertical structures are printed reliably.
11.dSparse Infill Density: 20–25% — Balanced rigidity vs. material use.
11.eSparse Pattern: Grid — Stable and efficient for flexible geometries.12. Speed Settings
12.aTravel: 160 mm/s — Fast but safe against backlash.
12.bInitial Layer: 15 mm/s — Prevents nozzle from skimming and ensures bed adhesion.
12.cOuter Wall: 60 mm/s — Controlled speed for surface quality.
12.dInner Wall: 90 mm/s — Slightly faster without compromising control.
12.eSmall Perimeter: 35 mm/s — Reduced speed for detailed geometry.
12.fTop Surface: 40 mm/s — Improves finish on topmost layers.
12.gInfill: 100–120 mm/s — Takes advantage of high flowability.13. Acceleration Settings
13.aNormal Print: 2000 mm/s² — Prevents ringing in soft filaments.
13.bTravel: 4000 mm/s² — Enables fast movement without harsh transitions.
13.cInitial Layer: 300 mm/s² — Gentle movement prevents lifting from the bed.
13.dOuter Wall: 1500 mm/s² — Improves outer surface clarity.
13.eInner Wall: 2000 mm/s² — Balanced for structural components.
13.fTop Surface: 1500 mm/s² — Ensures smooth detailing.14. Adhesion and Brims
14.aSkirt Loops: 2 — Helps prime nozzle and start cleanly.
14.bBrim Width: 6 mm — Helps hold soft materials down.
14.cBrim Gap: 0.15 mm — Allows for easy removal without tearing.15. Prime Tower and Flush Settings
15.aPrime Tower: ON — Purges moisture and early flow inconsistencies.
15.bTower Width: 40 mm — Prevents collapse due to heat.
15.cBrim Width (Tower): 4 mm — Adds stability to the purge base.
15.dFlush Into Support: ON — Discards unwanted early flow safely.16. G-Code Start Script
M900 K0.05 ; Pressure Advance M106 S0 ; Fan off G92 E0 G1 E15 F300 ; purge line G92 E0
17. Additional Notes
17.aDry filament at 100°C for 2 hours before use.
17.bStore with desiccant.
17.cKeep extruder door open to allow vapor to escape.
17.dAvoid long dwell times at high temperatures.If you need print settings for other nozzle sizes, feel free to reach out to us at timeplast@timeplast.com — we’ll be happy to help.
Free U.S. standard shipping on orders of 5+ spools!
Custom colors for 5+ same-type spools’ orders
Iridescent Gold
-
A rainbow-catching, eye-dazzling filament that changes color depending on the viewing angle or light source. With multi-layer thin-film pigments, this filament gives a prismatic sheen to your prints, ideal for high-fashion, toys, or artistic pieces.
Color-shifting magic, engineered to shine.
How it works:
Interference pigments bend light at different wavelengths, producing a spectrum of reflected hues as you move around the object.
Light angle = color angle.
Core Material:
Iridescent Flake Complex: 28% – Ultra-thin layered pigments
Flexible Transparent Matrix: 72% – Maintains light mobility across surface
Where to use it:
Fashion accessories – Jewelry, hair clips, bags
Futuristic art – Make your prints alive with color
Display models – Eye-catching effects for collectors
Event props – Shine under LEDs or camera lights
-
Click here to access our specialized TimeMass GPT Assistant.Just tell it your printer model and the TimeMass filament you're using—it will instantly recommend the exact parameters you need to start printing successfully.
Using a Bambu Lab printer?
Click here to download our updated Bambu Lab profile. All printing parameters are fully optimized and tested—just load the file and start printing.1. Introduction
These parameters are designed to help avoid printing issues; however, temperatures and speed timings can be adjusted based on your specific goals. For example, if you prefer a less rigid result, we recommend using a lower temperature. This section outlines a complete slicing and printing profile for TimeMass Iridescent Gold, tailored for printers with a 0.8 mm nozzle. If the print is not being successful, please lower the nozzle temperature by 10°C and start over until an optimal print is achieved.While these examples were printed with a 0.8 mm nozzle, TimeMass can be used with any nozzle size. Please check the manual for printing parameters with all the other nozzle sizes.2. Temperature Settings
2.aNozzle Temperature: 240°C — Optimal for flowability while avoiding decomposition (which begins around 250°C).
2.bBed Temperature: 95°C — Ensures strong first-layer adhesion and prevents moisture bubbling.
2.cNozzle Temperature Range: 230–245°C — Timeplast melts around 165°C but prints best at 240°C for precise viscosity control.3. Cooling Settings
3.aNo Cooling for First Layers: 3 layers — Prevents shrinkage due to rapid cooling of moisture-rich filament.
3.bFan Minimum Speed: 0% for the first 100 seconds — Allows heat retention during early layers.
3.cFan Maximum Speed: 15% starting at 8 seconds — Avoids overcooling that can lead to warping.
3.dKeep Fan Always On: OFF — Allows vapor to escape and avoids internal fogging.
3.eSlow Down for Cooling: ON — Improves surface finish with controlled cooling.
3.fForce Cooling for Overhangs: OFF — Overcooling can deform bridges in Timeplast.
3.gFan for Overhangs: 15% — Only for essential cooling in complex areas.
3.hPre-Start Fan Time: 2 seconds — Minimizes pressure differential during the first layer.4. Volumetric Flow
4.aMax Volumetric Speed: 12 mm³/s — Based on a melt flow index of ~15 g/10min, allows high-speed printing.
4.bRamming Speed: 3 mm³/s — Prevents bubbles or popping from pressure spikes.5. Retraction and Flow
5.aRetraction Distance: 0.4 mm — Minimal retraction required for soft filaments to avoid stringing.
5.bRetraction Speed: 15 mm/s — Slow enough to avoid pulling molten plastic.
5.cPressure Advance: 0.05 — Compensates for nozzle lag at high flow rates.
5.dFlow Ratio: 92% — Slight under-extrusion avoids swelling and surface artifacts.6. Precision Settings
6.aGap Closing Radius: 0.1 mm — Tolerant of gaps in thicker walls.
6.bArc Fitting: ON — Reduces G-code size and smooths curve transitions.
6.cElephant Foot Compensation: 0.1 mm — Offsets squishing in the first layer caused by large bead sizes.7. Walls and Shells
7.aWall Loops: 2 — Minimum for strength when using a 0.8 mm nozzle.
7.bDetect Thin Walls: ON — Ensures tight geometries aren’t skipped.
7.cTop/Bottom Shell Layers: 3 — Provides good coverage; increase if watertightness is needed.
7.dTop/Bottom Thickness: 1.2 mm — Equals 1.5x the nozzle size for solid strength.
7.eTop/Bottom Pattern: Monotonic — Distributes tension evenly and improves surface finish.8. Geometry and Movement
8.aWall Order: Inner before Outer — Creates cleaner outer surfaces.
8.bInfill First: OFF — Maintains precise outer dimensions.
8.cSmooth Speed Transition: ON — Prevents ringing caused by abrupt speed changes.
8.dSmooth Coefficient: 80 — Ideal damping for soft materials.
8.eAvoid Crossing Wall: ON — Minimizes stringing across part walls.
8.fMax Detour for Crossing: 10 mm or 5% — Balances time with print cleanliness.9. Layer and Width Settings
9.aLayer Height: 0.3 mm — Optimal for strength and resolution using a 0.8 mm nozzle.
9.bInitial Layer Height: 0.35 mm — Slightly higher to improve adhesion.
9.cLine Widths (all): 0.8 mm — Matches nozzle diameter for consistent extrusion.10. Seam Settings
10.aSeam Position: Aligned or Back — Use aligned for mechanical consistency, back for visual appeal.
10.bSmart Scarf Seam: ON — Automatically adjusts seam location to reduce visual impact.
10.cSeam Angle: 155° — Standard seam angle for clean transitions.
10.dSeam Steps: 10 — Smooths seam path and improves visual finish.11. Infill Settings
11.aWall/Infill Overlap: 10% — Prevents infill from deforming soft exterior walls.
11.bInfill Combination: ON — Consolidates paths for efficiency.
11.cDetect Floating Shells: ON — Ensures unsupported vertical structures are printed reliably.
11.dSparse Infill Density: 20–25% — Balanced rigidity vs. material use.
11.eSparse Pattern: Grid — Stable and efficient for flexible geometries.12. Speed Settings
12.aTravel: 160 mm/s — Fast but safe against backlash.
12.bInitial Layer: 15 mm/s — Prevents nozzle from skimming and ensures bed adhesion.
12.cOuter Wall: 60 mm/s — Controlled speed for surface quality.
12.dInner Wall: 90 mm/s — Slightly faster without compromising control.
12.eSmall Perimeter: 35 mm/s — Reduced speed for detailed geometry.
12.fTop Surface: 40 mm/s — Improves finish on topmost layers.
12.gInfill: 100–120 mm/s — Takes advantage of high flowability.13. Acceleration Settings
13.aNormal Print: 2000 mm/s² — Prevents ringing in soft filaments.
13.bTravel: 4000 mm/s² — Enables fast movement without harsh transitions.
13.cInitial Layer: 300 mm/s² — Gentle movement prevents lifting from the bed.
13.dOuter Wall: 1500 mm/s² — Improves outer surface clarity.
13.eInner Wall: 2000 mm/s² — Balanced for structural components.
13.fTop Surface: 1500 mm/s² — Ensures smooth detailing.14. Adhesion and Brims
14.aSkirt Loops: 2 — Helps prime nozzle and start cleanly.
14.bBrim Width: 6 mm — Helps hold soft materials down.
14.cBrim Gap: 0.15 mm — Allows for easy removal without tearing.15. Prime Tower and Flush Settings
15.aPrime Tower: ON — Purges moisture and early flow inconsistencies.
15.bTower Width: 40 mm — Prevents collapse due to heat.
15.cBrim Width (Tower): 4 mm — Adds stability to the purge base.
15.dFlush Into Support: ON — Discards unwanted early flow safely.16. G-Code Start Script
M900 K0.05 ; Pressure Advance M106 S0 ; Fan off G92 E0 G1 E15 F300 ; purge line G92 E0
17. Additional Notes
17.aDry filament at 100°C for 2 hours before use.
17.bStore with desiccant.
17.cKeep extruder door open to allow vapor to escape.
17.dAvoid long dwell times at high temperatures.If you need print settings for other nozzle sizes, feel free to reach out to us at timeplast@timeplast.com — we’ll be happy to help.
You can also get instant support through our dedicated ChatGPT assistant here:https://chatgpt.com/g/g-6823924241cc8191bbabcf0bc6523e3f-timemass-4d-printing🚀
Free U.S. standard shipping on orders of 5+ spools!
Custom colors for 5+ same-type spools’ orders
Iridescent Purple
-
A rainbow-catching, eye-dazzling filament that changes color depending on the viewing angle or light source. With multi-layer thin-film pigments, this filament gives a prismatic sheen to your prints, ideal for high-fashion, toys, or artistic pieces.
Color-shifting magic, engineered to shine.
How it works:
Interference pigments bend light at different wavelengths, producing a spectrum of reflected hues as you move around the object.
Light angle = color angle.
Core Material:
Iridescent Flake Complex: 28% – Ultra-thin layered pigments
Flexible Transparent Matrix: 72% – Maintains light mobility across surface
Where to use it:
Fashion accessories – Jewelry, hair clips, bags
Futuristic art – Make your prints alive with color
Display models – Eye-catching effects for collectors
Event props – Shine under LEDs or camera lights
-
Click here to access our specialized TimeMass GPT Assistant.Just tell it your printer model and the TimeMass filament you're using—it will instantly recommend the exact parameters you need to start printing successfully.
Using a Bambu Lab printer?
Click here to download our updated Bambu Lab profile. All printing parameters are fully optimized and tested—just load the file and start printing.1. Introduction
These parameters are designed to help avoid printing issues; however, temperatures and speed timings can be adjusted based on your specific goals. For example, if you prefer a less rigid result, we recommend using a lower temperature. This section outlines a complete slicing and printing profile for TimeMass Iridescent Purple, tailored for printers with a 0.8 mm nozzle. If the print is not being successful, please lower the nozzle temperature by 10°C and start over until an optimal print is achieved.While these examples were printed with a 0.8 mm nozzle, TimeMass can be used with any nozzle size. Please check the manual for printing parameters with all the other nozzle sizes.2. Temperature Settings
2.aNozzle Temperature: 240°C — Optimal for flowability while avoiding decomposition (which begins around 250°C).
2.bBed Temperature: 95°C — Ensures strong first-layer adhesion and prevents moisture bubbling.
2.cNozzle Temperature Range: 230–245°C — Timeplast melts around 165°C but prints best at 240°C for precise viscosity control.3. Cooling Settings
3.aNo Cooling for First Layers: 3 layers — Prevents shrinkage due to rapid cooling of moisture-rich filament.
3.bFan Minimum Speed: 0% for the first 100 seconds — Allows heat retention during early layers.
3.cFan Maximum Speed: 15% starting at 8 seconds — Avoids overcooling that can lead to warping.
3.dKeep Fan Always On: OFF — Allows vapor to escape and avoids internal fogging.
3.eSlow Down for Cooling: ON — Improves surface finish with controlled cooling.
3.fForce Cooling for Overhangs: OFF — Overcooling can deform bridges in Timeplast.
3.gFan for Overhangs: 15% — Only for essential cooling in complex areas.
3.hPre-Start Fan Time: 2 seconds — Minimizes pressure differential during the first layer.4. Volumetric Flow
4.aMax Volumetric Speed: 12 mm³/s — Based on a melt flow index of ~15 g/10min, allows high-speed printing.
4.bRamming Speed: 3 mm³/s — Prevents bubbles or popping from pressure spikes.5. Retraction and Flow
5.aRetraction Distance: 0.4 mm — Minimal retraction required for soft filaments to avoid stringing.
5.bRetraction Speed: 15 mm/s — Slow enough to avoid pulling molten plastic.
5.cPressure Advance: 0.05 — Compensates for nozzle lag at high flow rates.
5.dFlow Ratio: 92% — Slight under-extrusion avoids swelling and surface artifacts.6. Precision Settings
6.aGap Closing Radius: 0.1 mm — Tolerant of gaps in thicker walls.
6.bArc Fitting: ON — Reduces G-code size and smooths curve transitions.
6.cElephant Foot Compensation: 0.1 mm — Offsets squishing in the first layer caused by large bead sizes.7. Walls and Shells
7.aWall Loops: 2 — Minimum for strength when using a 0.8 mm nozzle.
7.bDetect Thin Walls: ON — Ensures tight geometries aren’t skipped.
7.cTop/Bottom Shell Layers: 3 — Provides good coverage; increase if watertightness is needed.
7.dTop/Bottom Thickness: 1.2 mm — Equals 1.5x the nozzle size for solid strength.
7.eTop/Bottom Pattern: Monotonic — Distributes tension evenly and improves surface finish.8. Geometry and Movement
8.aWall Order: Inner before Outer — Creates cleaner outer surfaces.
8.bInfill First: OFF — Maintains precise outer dimensions.
8.cSmooth Speed Transition: ON — Prevents ringing caused by abrupt speed changes.
8.dSmooth Coefficient: 80 — Ideal damping for soft materials.
8.eAvoid Crossing Wall: ON — Minimizes stringing across part walls.
8.fMax Detour for Crossing: 10 mm or 5% — Balances time with print cleanliness.9. Layer and Width Settings
9.aLayer Height: 0.3 mm — Optimal for strength and resolution using a 0.8 mm nozzle.
9.bInitial Layer Height: 0.35 mm — Slightly higher to improve adhesion.
9.cLine Widths (all): 0.8 mm — Matches nozzle diameter for consistent extrusion.10. Seam Settings
10.aSeam Position: Aligned or Back — Use aligned for mechanical consistency, back for visual appeal.
10.bSmart Scarf Seam: ON — Automatically adjusts seam location to reduce visual impact.
10.cSeam Angle: 155° — Standard seam angle for clean transitions.
10.dSeam Steps: 10 — Smooths seam path and improves visual finish.11. Infill Settings
11.aWall/Infill Overlap: 10% — Prevents infill from deforming soft exterior walls.
11.bInfill Combination: ON — Consolidates paths for efficiency.
11.cDetect Floating Shells: ON — Ensures unsupported vertical structures are printed reliably.
11.dSparse Infill Density: 20–25% — Balanced rigidity vs. material use.
11.eSparse Pattern: Grid — Stable and efficient for flexible geometries.12. Speed Settings
12.aTravel: 160 mm/s — Fast but safe against backlash.
12.bInitial Layer: 15 mm/s — Prevents nozzle from skimming and ensures bed adhesion.
12.cOuter Wall: 60 mm/s — Controlled speed for surface quality.
12.dInner Wall: 90 mm/s — Slightly faster without compromising control.
12.eSmall Perimeter: 35 mm/s — Reduced speed for detailed geometry.
12.fTop Surface: 40 mm/s — Improves finish on topmost layers.
12.gInfill: 100–120 mm/s — Takes advantage of high flowability.13. Acceleration Settings
13.aNormal Print: 2000 mm/s² — Prevents ringing in soft filaments.
13.bTravel: 4000 mm/s² — Enables fast movement without harsh transitions.
13.cInitial Layer: 300 mm/s² — Gentle movement prevents lifting from the bed.
13.dOuter Wall: 1500 mm/s² — Improves outer surface clarity.
13.eInner Wall: 2000 mm/s² — Balanced for structural components.
13.fTop Surface: 1500 mm/s² — Ensures smooth detailing.14. Adhesion and Brims
14.aSkirt Loops: 2 — Helps prime nozzle and start cleanly.
14.bBrim Width: 6 mm — Helps hold soft materials down.
14.cBrim Gap: 0.15 mm — Allows for easy removal without tearing.15. Prime Tower and Flush Settings
15.aPrime Tower: ON — Purges moisture and early flow inconsistencies.
15.bTower Width: 40 mm — Prevents collapse due to heat.
15.cBrim Width (Tower): 4 mm — Adds stability to the purge base.
15.dFlush Into Support: ON — Discards unwanted early flow safely.16. G-Code Start Script
M900 K0.05 ; Pressure Advance M106 S0 ; Fan off G92 E0 G1 E15 F300 ; purge line G92 E0
17. Additional Notes
17.aDry filament at 100°C for 2 hours before use.
17.bStore with desiccant.
17.cKeep extruder door open to allow vapor to escape.
17.dAvoid long dwell times at high temperatures.If you need print settings for other nozzle sizes, feel free to reach out to us at timeplast@timeplast.com — we’ll be happy to help.
You can also get instant support through our dedicated ChatGPT assistant here:https://chatgpt.com/g/g-6823924241cc8191bbabcf0bc6523e3f-timemass-4d-printing🚀
Free U.S. standard shipping on orders of 5+ spools!
Custom colors for 5+ same-type spools’ orders
Iridescent Green
-
A rainbow-catching, eye-dazzling filament that changes color depending on the viewing angle or light source. With multi-layer thin-film pigments, this filament gives a prismatic sheen to your prints, ideal for high-fashion, toys, or artistic pieces.
Color-shifting magic, engineered to shine.
How it works:
Interference pigments bend light at different wavelengths, producing a spectrum of reflected hues as you move around the object.
Light angle = color angle.
Core Material:
Iridescent Flake Complex: 28% – Ultra-thin layered pigments
Flexible Transparent Matrix: 72% – Maintains light mobility across surface
Where to use it:
Fashion accessories – Jewelry, hair clips, bags
Futuristic art – Make your prints alive with color
Display models – Eye-catching effects for collectors
Event props – Shine under LEDs or camera lights
-
Click here to access our specialized TimeMass GPT Assistant.Just tell it your printer model and the TimeMass filament you're using—it will instantly recommend the exact parameters you need to start printing successfully.
Using a Bambu Lab printer?
Click here to download our updated Bambu Lab profile. All printing parameters are fully optimized and tested—just load the file and start printing.1. Introduction
These parameters are designed to help avoid printing issues; however, temperatures and speed timings can be adjusted based on your specific goals. For example, if you prefer a less rigid result, we recommend using a lower temperature. This section outlines a complete slicing and printing profile for TimeMass Iridescent Green, tailored for printers with a 0.8 mm nozzle. If the print is not being successful, please lower the nozzle temperature by 10°C and start over until an optimal print is achieved.While these examples were printed with a 0.8 mm nozzle, TimeMass can be used with any nozzle size. Please check the manual for printing parameters with all the other nozzle sizes.2. Temperature Settings
2.aNozzle Temperature: 240°C — Optimal for flowability while avoiding decomposition (which begins around 250°C).
2.bBed Temperature: 95°C — Ensures strong first-layer adhesion and prevents moisture bubbling.
2.cNozzle Temperature Range: 230–245°C — Timeplast melts around 165°C but prints best at 240°C for precise viscosity control.3. Cooling Settings
3.aNo Cooling for First Layers: 3 layers — Prevents shrinkage due to rapid cooling of moisture-rich filament.
3.bFan Minimum Speed: 0% for the first 100 seconds — Allows heat retention during early layers.
3.cFan Maximum Speed: 15% starting at 8 seconds — Avoids overcooling that can lead to warping.
3.dKeep Fan Always On: OFF — Allows vapor to escape and avoids internal fogging.
3.eSlow Down for Cooling: ON — Improves surface finish with controlled cooling.
3.fForce Cooling for Overhangs: OFF — Overcooling can deform bridges in Timeplast.
3.gFan for Overhangs: 15% — Only for essential cooling in complex areas.
3.hPre-Start Fan Time: 2 seconds — Minimizes pressure differential during the first layer.4. Volumetric Flow
4.aMax Volumetric Speed: 12 mm³/s — Based on a melt flow index of ~15 g/10min, allows high-speed printing.
4.bRamming Speed: 3 mm³/s — Prevents bubbles or popping from pressure spikes.5. Retraction and Flow
5.aRetraction Distance: 0.4 mm — Minimal retraction required for soft filaments to avoid stringing.
5.bRetraction Speed: 15 mm/s — Slow enough to avoid pulling molten plastic.
5.cPressure Advance: 0.05 — Compensates for nozzle lag at high flow rates.
5.dFlow Ratio: 92% — Slight under-extrusion avoids swelling and surface artifacts.6. Precision Settings
6.aGap Closing Radius: 0.1 mm — Tolerant of gaps in thicker walls.
6.bArc Fitting: ON — Reduces G-code size and smooths curve transitions.
6.cElephant Foot Compensation: 0.1 mm — Offsets squishing in the first layer caused by large bead sizes.7. Walls and Shells
7.aWall Loops: 2 — Minimum for strength when using a 0.8 mm nozzle.
7.bDetect Thin Walls: ON — Ensures tight geometries aren’t skipped.
7.cTop/Bottom Shell Layers: 3 — Provides good coverage; increase if watertightness is needed.
7.dTop/Bottom Thickness: 1.2 mm — Equals 1.5x the nozzle size for solid strength.
7.eTop/Bottom Pattern: Monotonic — Distributes tension evenly and improves surface finish.8. Geometry and Movement
8.aWall Order: Inner before Outer — Creates cleaner outer surfaces.
8.bInfill First: OFF — Maintains precise outer dimensions.
8.cSmooth Speed Transition: ON — Prevents ringing caused by abrupt speed changes.
8.dSmooth Coefficient: 80 — Ideal damping for soft materials.
8.eAvoid Crossing Wall: ON — Minimizes stringing across part walls.
8.fMax Detour for Crossing: 10 mm or 5% — Balances time with print cleanliness.9. Layer and Width Settings
9.aLayer Height: 0.3 mm — Optimal for strength and resolution using a 0.8 mm nozzle.
9.bInitial Layer Height: 0.35 mm — Slightly higher to improve adhesion.
9.cLine Widths (all): 0.8 mm — Matches nozzle diameter for consistent extrusion.10. Seam Settings
10.aSeam Position: Aligned or Back — Use aligned for mechanical consistency, back for visual appeal.
10.bSmart Scarf Seam: ON — Automatically adjusts seam location to reduce visual impact.
10.cSeam Angle: 155° — Standard seam angle for clean transitions.
10.dSeam Steps: 10 — Smooths seam path and improves visual finish.11. Infill Settings
11.aWall/Infill Overlap: 10% — Prevents infill from deforming soft exterior walls.
11.bInfill Combination: ON — Consolidates paths for efficiency.
11.cDetect Floating Shells: ON — Ensures unsupported vertical structures are printed reliably.
11.dSparse Infill Density: 20–25% — Balanced rigidity vs. material use.
11.eSparse Pattern: Grid — Stable and efficient for flexible geometries.12. Speed Settings
12.aTravel: 160 mm/s — Fast but safe against backlash.
12.bInitial Layer: 15 mm/s — Prevents nozzle from skimming and ensures bed adhesion.
12.cOuter Wall: 60 mm/s — Controlled speed for surface quality.
12.dInner Wall: 90 mm/s — Slightly faster without compromising control.
12.eSmall Perimeter: 35 mm/s — Reduced speed for detailed geometry.
12.fTop Surface: 40 mm/s — Improves finish on topmost layers.
12.gInfill: 100–120 mm/s — Takes advantage of high flowability.13. Acceleration Settings
13.aNormal Print: 2000 mm/s² — Prevents ringing in soft filaments.
13.bTravel: 4000 mm/s² — Enables fast movement without harsh transitions.
13.cInitial Layer: 300 mm/s² — Gentle movement prevents lifting from the bed.
13.dOuter Wall: 1500 mm/s² — Improves outer surface clarity.
13.eInner Wall: 2000 mm/s² — Balanced for structural components.
13.fTop Surface: 1500 mm/s² — Ensures smooth detailing.14. Adhesion and Brims
14.aSkirt Loops: 2 — Helps prime nozzle and start cleanly.
14.bBrim Width: 6 mm — Helps hold soft materials down.
14.cBrim Gap: 0.15 mm — Allows for easy removal without tearing.15. Prime Tower and Flush Settings
15.aPrime Tower: ON — Purges moisture and early flow inconsistencies.
15.bTower Width: 40 mm — Prevents collapse due to heat.
15.cBrim Width (Tower): 4 mm — Adds stability to the purge base.
15.dFlush Into Support: ON — Discards unwanted early flow safely.16. G-Code Start Script
M900 K0.05 ; Pressure Advance M106 S0 ; Fan off G92 E0 G1 E15 F300 ; purge line G92 E0
17. Additional Notes
17.aDry filament at 100°C for 2 hours before use.
17.bStore with desiccant.
17.cKeep extruder door open to allow vapor to escape.
17.dAvoid long dwell times at high temperatures.If you need print settings for other nozzle sizes, feel free to reach out to us at timeplast@timeplast.com — we’ll be happy to help.
Free U.S. standard shipping on orders of 5+ spools!
Custom colors for 5+ same-type spools’ orders
Iridescent Blue
-
A rainbow-catching, eye-dazzling filament that changes color depending on the viewing angle or light source. With multi-layer thin-film pigments, this filament gives a prismatic sheen to your prints, ideal for high-fashion, toys, or artistic pieces.
Color-shifting magic, engineered to shine.
How it works:
Interference pigments bend light at different wavelengths, producing a spectrum of reflected hues as you move around the object.
Light angle = color angle.
Core Material:
Iridescent Flake Complex: 28% – Ultra-thin layered pigments
Flexible Transparent Matrix: 72% – Maintains light mobility across surface
Where to use it:
Fashion accessories – Jewelry, hair clips, bags
Futuristic art – Make your prints alive with color
Display models – Eye-catching effects for collectors
Event props – Shine under LEDs or camera lights
-
Click here to access our specialized TimeMass GPT Assistant.Just tell it your printer model and the TimeMass filament you're using—it will instantly recommend the exact parameters you need to start printing successfully.
Using a Bambu Lab printer?
Click here to download our updated Bambu Lab profile. All printing parameters are fully optimized and tested—just load the file and start printing.1. Introduction
These parameters are designed to help avoid printing issues; however, temperatures and speed timings can be adjusted based on your specific goals. For example, if you prefer a less rigid result, we recommend using a lower temperature. This section outlines a complete slicing and printing profile for TimeMass Iridescent Blue tailored for printers with a 0.8 mm nozzle. If the print is not being successful, please lower the nozzle temperature by 10°C and start over until an optimal print is achieved.While these examples were printed with a 0.8 mm nozzle, TimeMass can be used with any nozzle size. Please check the manual for printing parameters with all the other nozzle sizes.2. Temperature Settings
2.aNozzle Temperature: 240°C — Optimal for flowability while avoiding decomposition (which begins around 250°C).
2.bBed Temperature: 95°C — Ensures strong first-layer adhesion and prevents moisture bubbling.
2.cNozzle Temperature Range: 230–245°C — Timeplast melts around 165°C but prints best at 240°C for precise viscosity control.3. Cooling Settings
3.aNo Cooling for First Layers: 3 layers — Prevents shrinkage due to rapid cooling of moisture-rich filament.
3.bFan Minimum Speed: 0% for the first 100 seconds — Allows heat retention during early layers.
3.cFan Maximum Speed: 15% starting at 8 seconds — Avoids overcooling that can lead to warping.
3.dKeep Fan Always On: OFF — Allows vapor to escape and avoids internal fogging.
3.eSlow Down for Cooling: ON — Improves surface finish with controlled cooling.
3.fForce Cooling for Overhangs: OFF — Overcooling can deform bridges in Timeplast.
3.gFan for Overhangs: 15% — Only for essential cooling in complex areas.
3.hPre-Start Fan Time: 2 seconds — Minimizes pressure differential during the first layer.4. Volumetric Flow
4.aMax Volumetric Speed: 12 mm³/s — Based on a melt flow index of ~15 g/10min, allows high-speed printing.
4.bRamming Speed: 3 mm³/s — Prevents bubbles or popping from pressure spikes.5. Retraction and Flow
5.aRetraction Distance: 0.4 mm — Minimal retraction required for soft filaments to avoid stringing.
5.bRetraction Speed: 15 mm/s — Slow enough to avoid pulling molten plastic.
5.cPressure Advance: 0.05 — Compensates for nozzle lag at high flow rates.
5.dFlow Ratio: 92% — Slight under-extrusion avoids swelling and surface artifacts.6. Precision Settings
6.aGap Closing Radius: 0.1 mm — Tolerant of gaps in thicker walls.
6.bArc Fitting: ON — Reduces G-code size and smooths curve transitions.
6.cElephant Foot Compensation: 0.1 mm — Offsets squishing in the first layer caused by large bead sizes.7. Walls and Shells
7.aWall Loops: 2 — Minimum for strength when using a 0.8 mm nozzle.
7.bDetect Thin Walls: ON — Ensures tight geometries aren’t skipped.
7.cTop/Bottom Shell Layers: 3 — Provides good coverage; increase if watertightness is needed.
7.dTop/Bottom Thickness: 1.2 mm — Equals 1.5x the nozzle size for solid strength.
7.eTop/Bottom Pattern: Monotonic — Distributes tension evenly and improves surface finish.8. Geometry and Movement
8.aWall Order: Inner before Outer — Creates cleaner outer surfaces.
8.bInfill First: OFF — Maintains precise outer dimensions.
8.cSmooth Speed Transition: ON — Prevents ringing caused by abrupt speed changes.
8.dSmooth Coefficient: 80 — Ideal damping for soft materials.
8.eAvoid Crossing Wall: ON — Minimizes stringing across part walls.
8.fMax Detour for Crossing: 10 mm or 5% — Balances time with print cleanliness.9. Layer and Width Settings
9.aLayer Height: 0.3 mm — Optimal for strength and resolution using a 0.8 mm nozzle.
9.bInitial Layer Height: 0.35 mm — Slightly higher to improve adhesion.
9.cLine Widths (all): 0.8 mm — Matches nozzle diameter for consistent extrusion.10. Seam Settings
10.aSeam Position: Aligned or Back — Use aligned for mechanical consistency, back for visual appeal.
10.bSmart Scarf Seam: ON — Automatically adjusts seam location to reduce visual impact.
10.cSeam Angle: 155° — Standard seam angle for clean transitions.
10.dSeam Steps: 10 — Smooths seam path and improves visual finish.11. Infill Settings
11.aWall/Infill Overlap: 10% — Prevents infill from deforming soft exterior walls.
11.bInfill Combination: ON — Consolidates paths for efficiency.
11.cDetect Floating Shells: ON — Ensures unsupported vertical structures are printed reliably.
11.dSparse Infill Density: 20–25% — Balanced rigidity vs. material use.
11.eSparse Pattern: Grid — Stable and efficient for flexible geometries.12. Speed Settings
12.aTravel: 160 mm/s — Fast but safe against backlash.
12.bInitial Layer: 15 mm/s — Prevents nozzle from skimming and ensures bed adhesion.
12.cOuter Wall: 60 mm/s — Controlled speed for surface quality.
12.dInner Wall: 90 mm/s — Slightly faster without compromising control.
12.eSmall Perimeter: 35 mm/s — Reduced speed for detailed geometry.
12.fTop Surface: 40 mm/s — Improves finish on topmost layers.
12.gInfill: 100–120 mm/s — Takes advantage of high flowability.13. Acceleration Settings
13.aNormal Print: 2000 mm/s² — Prevents ringing in soft filaments.
13.bTravel: 4000 mm/s² — Enables fast movement without harsh transitions.
13.cInitial Layer: 300 mm/s² — Gentle movement prevents lifting from the bed.
13.dOuter Wall: 1500 mm/s² — Improves outer surface clarity.
13.eInner Wall: 2000 mm/s² — Balanced for structural components.
13.fTop Surface: 1500 mm/s² — Ensures smooth detailing.14. Adhesion and Brims
14.aSkirt Loops: 2 — Helps prime nozzle and start cleanly.
14.bBrim Width: 6 mm — Helps hold soft materials down.
14.cBrim Gap: 0.15 mm — Allows for easy removal without tearing.15. Prime Tower and Flush Settings
15.aPrime Tower: ON — Purges moisture and early flow inconsistencies.
15.bTower Width: 40 mm — Prevents collapse due to heat.
15.cBrim Width (Tower): 4 mm — Adds stability to the purge base.
15.dFlush Into Support: ON — Discards unwanted early flow safely.16. G-Code Start Script
M900 K0.05 ; Pressure Advance M106 S0 ; Fan off G92 E0 G1 E15 F300 ; purge line G92 E0
17. Additional Notes
17.aDry filament at 100°C for 2 hours before use.
17.bStore with desiccant.
17.cKeep extruder door open to allow vapor to escape.
17.dAvoid long dwell times at high temperatures.If you need print settings for other nozzle sizes, feel free to reach out to us at timeplast@timeplast.com — we’ll be happy to help.
Free U.S. standard shipping on orders of 5+ spools!
Custom colors for 5+ same-type spools’ orders
Holographic
-
A rainbow-catching, eye-dazzling filament that changes color depending on the viewing angle or light source. With multi-layer thin-film pigments, this filament gives a prismatic sheen to your prints, ideal for high-fashion, toys, or artistic pieces.
Color-shifting magic, engineered to shine.
How it works:
Interference pigments bend light at different wavelengths, producing a spectrum of reflected hues as you move around the object.
Light angle = color angle.
Core Material:
Iridescent Flake Complex: 28% – Ultra-thin layered pigments
Flexible Transparent Matrix: 72% – Maintains light mobility across surface
Where to use it:
Fashion accessories – Jewelry, hair clips, bags
Futuristic art – Make your prints alive with color
Display models – Eye-catching effects for collectors
Event props – Shine under LEDs or camera lights
-
Click here to access our specialized TimeMass GPT Assistant. Just tell it your printer model and the TimeMass filament you're using—it will instantly recommend the exact parameters you need to start printing successfully.
Using a Bambu Lab printer?
Click here to download our updated Bambu Lab profile. All printing parameters are fully optimized and tested—just load the file and start printing.1. Introduction
These parameters are designed to help avoid printing issues; however, temperatures and speed timings can be adjusted based on your specific goals. For example, if you prefer a less rigid result, we recommend using a lower temperature. This section outlines a complete slicing and printing profile for TimeMass UV tailored for printers with a 0.8 mm nozzle. If the print is not being successful, please lower the nozzle temperature by 10°C and start over until an optimal print is achieved.While these examples were printed with a 0.8 mm nozzle, TimeMass can be used with any nozzle size. Please check the manual for printing parameters with all the other nozzle sizes.2. Temperature Settings
2.aNozzle Temperature: 240°C — Optimal for flowability while avoiding decomposition (which begins around 250°C).
2.bBed Temperature: 95°C — Ensures strong first-layer adhesion and prevents moisture bubbling.
2.cNozzle Temperature Range: 230–245°C — Timeplast melts around 165°C but prints best at 240°C for precise viscosity control.3. Cooling Settings
3.aNo Cooling for First Layers: 3 layers — Prevents shrinkage due to rapid cooling of moisture-rich filament.
3.bFan Minimum Speed: 0% for the first 100 seconds — Allows heat retention during early layers.
3.cFan Maximum Speed: 15% starting at 8 seconds — Avoids overcooling that can lead to warping.
3.dKeep Fan Always On: OFF — Allows vapor to escape and avoids internal fogging.
3.eSlow Down for Cooling: ON — Improves surface finish with controlled cooling.
3.fForce Cooling for Overhangs: OFF — Overcooling can deform bridges in Timeplast.
3.gFan for Overhangs: 15% — Only for essential cooling in complex areas.
3.hPre-Start Fan Time: 2 seconds — Minimizes pressure differential during the first layer.4. Volumetric Flow
4.aMax Volumetric Speed: 12 mm³/s — Based on a melt flow index of ~15 g/10min, allows high-speed printing.
4.bRamming Speed: 3 mm³/s — Prevents bubbles or popping from pressure spikes.5. Retraction and Flow
5.aRetraction Distance: 0.4 mm — Minimal retraction required for soft filaments to avoid stringing.
5.bRetraction Speed: 15 mm/s — Slow enough to avoid pulling molten plastic.
5.cPressure Advance: 0.05 — Compensates for nozzle lag at high flow rates.
5.dFlow Ratio: 92% — Slight under-extrusion avoids swelling and surface artifacts.6. Precision Settings
6.aGap Closing Radius: 0.1 mm — Tolerant of gaps in thicker walls.
6.bArc Fitting: ON — Reduces G-code size and smooths curve transitions.
6.cElephant Foot Compensation: 0.1 mm — Offsets squishing in the first layer caused by large bead sizes.7. Walls and Shells
7.aWall Loops: 2 — Minimum for strength when using a 0.8 mm nozzle.
7.bDetect Thin Walls: ON — Ensures tight geometries aren’t skipped.
7.cTop/Bottom Shell Layers: 3 — Provides good coverage; increase if watertightness is needed.
7.dTop/Bottom Thickness: 1.2 mm — Equals 1.5x the nozzle size for solid strength.
7.eTop/Bottom Pattern: Monotonic — Distributes tension evenly and improves surface finish.8. Geometry and Movement
8.aWall Order: Inner before Outer — Creates cleaner outer surfaces.
8.bInfill First: OFF — Maintains precise outer dimensions.
8.cSmooth Speed Transition: ON — Prevents ringing caused by abrupt speed changes.
8.dSmooth Coefficient: 80 — Ideal damping for soft materials.
8.eAvoid Crossing Wall: ON — Minimizes stringing across part walls.
8.fMax Detour for Crossing: 10 mm or 5% — Balances time with print cleanliness.9. Layer and Width Settings
9.aLayer Height: 0.3 mm — Optimal for strength and resolution using a 0.8 mm nozzle.
9.bInitial Layer Height: 0.35 mm — Slightly higher to improve adhesion.
9.cLine Widths (all): 0.8 mm — Matches nozzle diameter for consistent extrusion.10. Seam Settings
10.aSeam Position: Aligned or Back — Use aligned for mechanical consistency, back for visual appeal.
10.bSmart Scarf Seam: ON — Automatically adjusts seam location to reduce visual impact.
10.cSeam Angle: 155° — Standard seam angle for clean transitions.
10.dSeam Steps: 10 — Smooths seam path and improves visual finish.11. Infill Settings
11.aWall/Infill Overlap: 10% — Prevents infill from deforming soft exterior walls.
11.bInfill Combination: ON — Consolidates paths for efficiency.
11.cDetect Floating Shells: ON — Ensures unsupported vertical structures are printed reliably.
11.dSparse Infill Density: 20–25% — Balanced rigidity vs. material use.
11.eSparse Pattern: Grid — Stable and efficient for flexible geometries.12. Speed Settings
12.aTravel: 160 mm/s — Fast but safe against backlash.
12.bInitial Layer: 15 mm/s — Prevents nozzle from skimming and ensures bed adhesion.
12.cOuter Wall: 60 mm/s — Controlled speed for surface quality.
12.dInner Wall: 90 mm/s — Slightly faster without compromising control.
12.eSmall Perimeter: 35 mm/s — Reduced speed for detailed geometry.
12.fTop Surface: 40 mm/s — Improves finish on topmost layers.
12.gInfill: 100–120 mm/s — Takes advantage of high flowability.13. Acceleration Settings
13.aNormal Print: 2000 mm/s² — Prevents ringing in soft filaments.
13.bTravel: 4000 mm/s² — Enables fast movement without harsh transitions.
13.cInitial Layer: 300 mm/s² — Gentle movement prevents lifting from the bed.
13.dOuter Wall: 1500 mm/s² — Improves outer surface clarity.
13.eInner Wall: 2000 mm/s² — Balanced for structural components.
13.fTop Surface: 1500 mm/s² — Ensures smooth detailing.14. Adhesion and Brims
14.aSkirt Loops: 2 — Helps prime nozzle and start cleanly.
14.bBrim Width: 6 mm — Helps hold soft materials down.
14.cBrim Gap: 0.15 mm — Allows for easy removal without tearing.15. Prime Tower and Flush Settings
15.aPrime Tower: ON — Purges moisture and early flow inconsistencies.
15.bTower Width: 40 mm — Prevents collapse due to heat.
15.cBrim Width (Tower): 4 mm — Adds stability to the purge base.
15.dFlush Into Support: ON — Discards unwanted early flow safely.16. G-Code Start Script
M900 K0.05 ; Pressure Advance M106 S0 ; Fan off G92 E0 G1 E15 F300 ; purge line G92 E0
17. Additional Notes
17.aDry filament at 100°C for 2 hours before use.
17.bStore with desiccant.
17.cKeep extruder door open to allow vapor to escape.
17.dAvoid long dwell times at high temperatures.If you need print settings for other nozzle sizes, feel free to reach out to us at timeplast@timeplast.com — we’ll be happy to help.
Free U.S. standard shipping on orders of 5+ spools!
Custom colors for 5+ same-type spools’ orders
Iridescent Bronze
-
A triple-visibility filament that glows in the dark, reflects light, and sparkles in daylight. Made for visibility, safety, and unapologetic flair. If you want your prints to pop—day or night—this is your go-to.
Shine. Reflect. Dazzle.
How it works:
Multiple light-responsive additives are embedded within a durable polymer carrier, activated by natural or artificial light.
Day or night – it never goes unnoticed.
Core Components:
Photoluminescent Pigments: 30% – Recharge in light, glow for hours
Retroreflective Microbeads: 20% – Bounce light directly back to source
Iridescent Flakes: 10% – Add visual punch under sunlight
Base Material: 40% – Tough and printable for long-lasting use
Where to use it:
Night cycling accessories – Make yourself seen
Safety gear prototypes – Reflective tools for visibility testing
Party/event props – Light up the night with flair
Fashion or cosplay – Wearable elements that glow and shimmer
-
Click here to access our specialized TimeMass GPT Assistant. Just tell it your printer model and the TimeMass filament you're using—it will instantly recommend the exact parameters you need to start printing successfully.
Using a Bambu Lab printer?
Click here to download our updated Bambu Lab profile. All printing parameters are fully optimized and tested—just load the file and start printing.1. Introduction
These parameters are designed to help avoid printing issues; however, temperatures and speed timings can be adjusted based on your specific goals. For example, if you prefer a less rigid result, we recommend using a lower temperature. This section outlines a complete slicing and printing profile for TimeMass Active, tailored for printers with a 0.8 mm nozzle. If the print is not being successful, please lower the nozzle temperature by 10°C and start over until an optimal print is achieved.While these examples were printed with a 0.8 mm nozzle, TimeMass can be used with any nozzle size. Please check the manual for printing parameters with all the other nozzle sizes.2. Temperature Settings
2.aNozzle Temperature: 240°C — Optimal for flowability while avoiding decomposition (which begins around 250°C).
2.bBed Temperature: 95°C — Ensures strong first-layer adhesion and prevents moisture bubbling.
2.cNozzle Temperature Range: 230–245°C — Timeplast melts around 165°C but prints best at 240°C for precise viscosity control.3. Cooling Settings
3.aNo Cooling for First Layers: 3 layers — Prevents shrinkage due to rapid cooling of moisture-rich filament.
3.bFan Minimum Speed: 0% for the first 100 seconds — Allows heat retention during early layers.
3.cFan Maximum Speed: 15% starting at 8 seconds — Avoids overcooling that can lead to warping.
3.dKeep Fan Always On: OFF — Allows vapor to escape and avoids internal fogging.
3.eSlow Down for Cooling: ON — Improves surface finish with controlled cooling.
3.fForce Cooling for Overhangs: OFF — Overcooling can deform bridges in Timeplast.
3.gFan for Overhangs: 15% — Only for essential cooling in complex areas.
3.hPre-Start Fan Time: 2 seconds — Minimizes pressure differential during the first layer.4. Volumetric Flow
4.aMax Volumetric Speed: 12 mm³/s — Based on a melt flow index of ~15 g/10min, allows high-speed printing.
4.bRamming Speed: 3 mm³/s — Prevents bubbles or popping from pressure spikes.5. Retraction and Flow
5.aRetraction Distance: 0.4 mm — Minimal retraction required for soft filaments to avoid stringing.
5.bRetraction Speed: 15 mm/s — Slow enough to avoid pulling molten plastic.
5.cPressure Advance: 0.05 — Compensates for nozzle lag at high flow rates.
5.dFlow Ratio: 92% — Slight under-extrusion avoids swelling and surface artifacts.6. Precision Settings
6.aGap Closing Radius: 0.1 mm — Tolerant of gaps in thicker walls.
6.bArc Fitting: ON — Reduces G-code size and smooths curve transitions.
6.cElephant Foot Compensation: 0.1 mm — Offsets squishing in the first layer caused by large bead sizes.7. Walls and Shells
7.aWall Loops: 2 — Minimum for strength when using a 0.8 mm nozzle.
7.bDetect Thin Walls: ON — Ensures tight geometries aren’t skipped.
7.cTop/Bottom Shell Layers: 3 — Provides good coverage; increase if watertightness is needed.
7.dTop/Bottom Thickness: 1.2 mm — Equals 1.5x the nozzle size for solid strength.
7.eTop/Bottom Pattern: Monotonic — Distributes tension evenly and improves surface finish.8. Geometry and Movement
8.aWall Order: Inner before Outer — Creates cleaner outer surfaces.
8.bInfill First: OFF — Maintains precise outer dimensions.
8.cSmooth Speed Transition: ON — Prevents ringing caused by abrupt speed changes.
8.dSmooth Coefficient: 80 — Ideal damping for soft materials.
8.eAvoid Crossing Wall: ON — Minimizes stringing across part walls.
8.fMax Detour for Crossing: 10 mm or 5% — Balances time with print cleanliness.9. Layer and Width Settings
9.aLayer Height: 0.3 mm — Optimal for strength and resolution using a 0.8 mm nozzle.
9.bInitial Layer Height: 0.35 mm — Slightly higher to improve adhesion.
9.cLine Widths (all): 0.8 mm — Matches nozzle diameter for consistent extrusion.10. Seam Settings
10.aSeam Position: Aligned or Back — Use aligned for mechanical consistency, back for visual appeal.
10.bSmart Scarf Seam: ON — Automatically adjusts seam location to reduce visual impact.
10.cSeam Angle: 155° — Standard seam angle for clean transitions.
10.dSeam Steps: 10 — Smooths seam path and improves visual finish.11. Infill Settings
11.aWall/Infill Overlap: 10% — Prevents infill from deforming soft exterior walls.
11.bInfill Combination: ON — Consolidates paths for efficiency.
11.cDetect Floating Shells: ON — Ensures unsupported vertical structures are printed reliably.
11.dSparse Infill Density: 20–25% — Balanced rigidity vs. material use.
11.eSparse Pattern: Grid — Stable and efficient for flexible geometries.12. Speed Settings
12.aTravel: 160 mm/s — Fast but safe against backlash.
12.bInitial Layer: 15 mm/s — Prevents nozzle from skimming and ensures bed adhesion.
12.cOuter Wall: 60 mm/s — Controlled speed for surface quality.
12.dInner Wall: 90 mm/s — Slightly faster without compromising control.
12.eSmall Perimeter: 35 mm/s — Reduced speed for detailed geometry.
12.fTop Surface: 40 mm/s — Improves finish on topmost layers.
12.gInfill: 100–120 mm/s — Takes advantage of high flowability.13. Acceleration Settings
13.aNormal Print: 2000 mm/s² — Prevents ringing in soft filaments.
13.bTravel: 4000 mm/s² — Enables fast movement without harsh transitions.
13.cInitial Layer: 300 mm/s² — Gentle movement prevents lifting from the bed.
13.dOuter Wall: 1500 mm/s² — Improves outer surface clarity.
13.eInner Wall: 2000 mm/s² — Balanced for structural components.
13.fTop Surface: 1500 mm/s² — Ensures smooth detailing.14. Adhesion and Brims
14.aSkirt Loops: 2 — Helps prime nozzle and start cleanly.
14.bBrim Width: 6 mm — Helps hold soft materials down.
14.cBrim Gap: 0.15 mm — Allows for easy removal without tearing.15. Prime Tower and Flush Settings
15.aPrime Tower: ON — Purges moisture and early flow inconsistencies.
15.bTower Width: 40 mm — Prevents collapse due to heat.
15.cBrim Width (Tower): 4 mm — Adds stability to the purge base.
15.dFlush Into Support: ON — Discards unwanted early flow safely.16. G-Code Start Script
M900 K0.05 ; Pressure Advance M106 S0 ; Fan off G92 E0 G1 E15 F300 ; purge line G92 E0
17. Additional Notes
17.aDry filament at 100°C for 2 hours before use.
17.bStore with desiccant.
17.cKeep extruder door open to allow vapor to escape.
17.dAvoid long dwell times at high temperatures.If you need print settings for other nozzle sizes, feel free to reach out to us at timeplast@timeplast.com — we’ll be happy to help.
Free U.S. standard shipping on orders of 5+ spools!
Custom colors for 5+ same-type spools’ orders
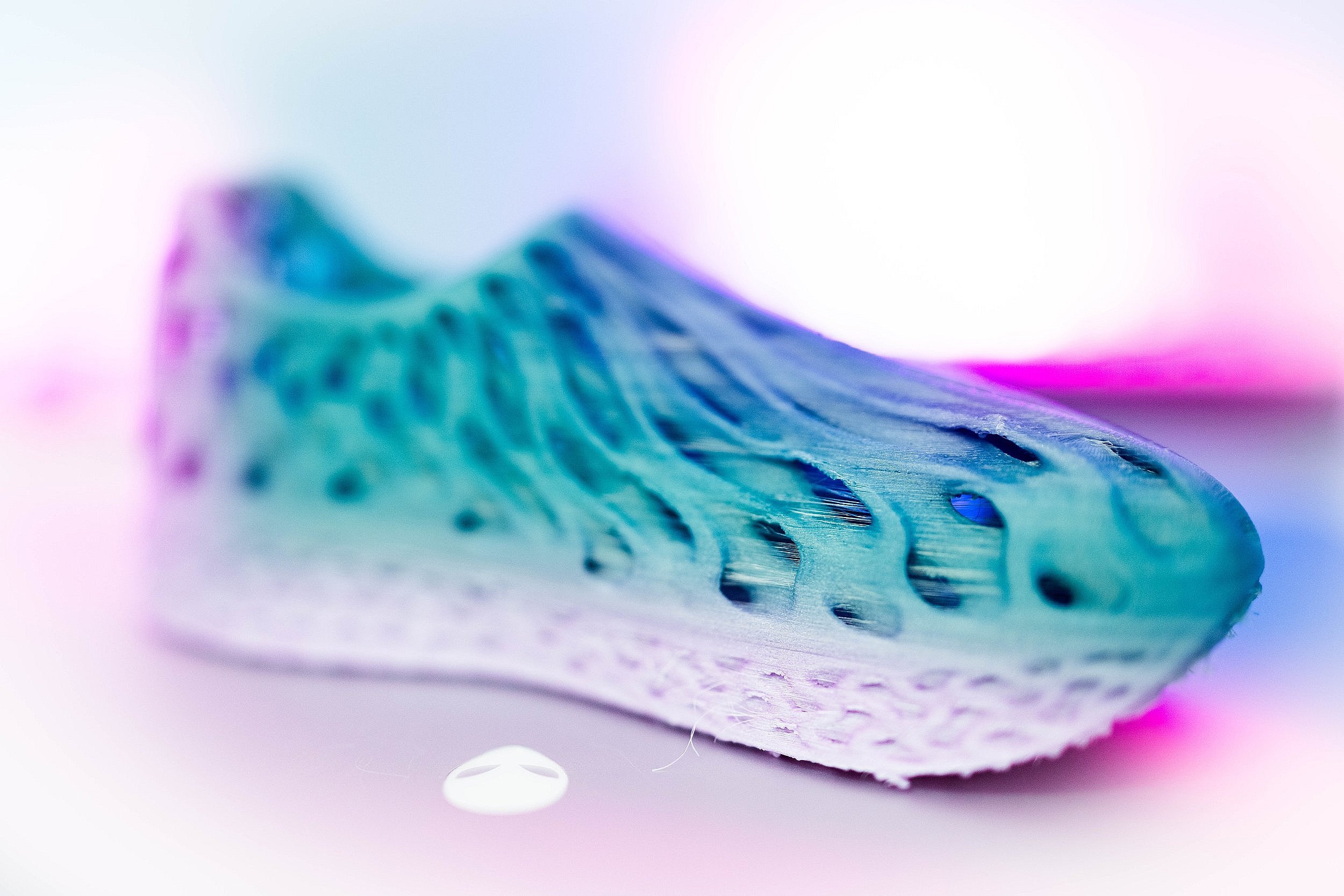
What is
TimeMass?
A must watch video made by our team.
Meet the Solution
-
Certified 100% Water Soluble
ASTM E 1148
-
Certified 100% PFAs-free
ASTM D7979-19
-
70% water, 30% sugar, vinegar, proprietary in-house Polyethenol and Calcium components
-
Patented Pabyss - The Plastic Abyss
A “Molecular Disintegrator” bottomless trashcan.
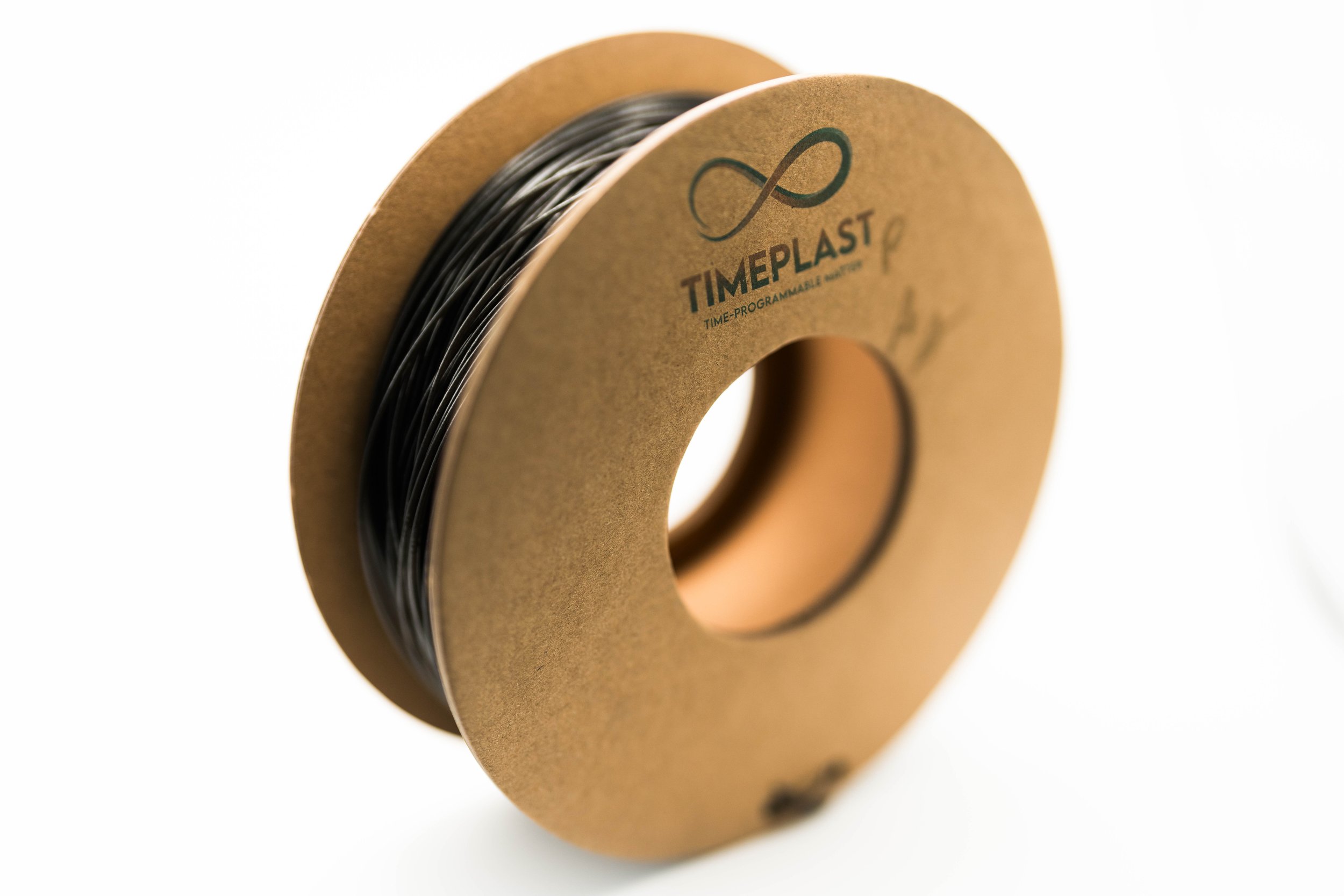
The possibilities are endless
Time-programmed wearables: Like artistic shoes, with incredible designs and at a very low cost of production.
Self-Eroding Marine Structures: Ocean-based supports that provide habitats for marine life and dissolve over time to release beneficial minerals, enriching marine ecosystems naturally.
Automated Farming Components: Timed-dissolving planters that release nutrients and water at key stages of plant growth, optimizing crop health and reducing artificial fertilizers.
Self-destructive Construction Scaffolding: Temporary, self-dissolving scaffolding for construction projects, removing the need for disassembly and minimizing post-construction waste.
Temporary Floating Platforms for Aquatic Events: Modular, dissolvable platforms for water-based events that disappear afterward, leaving the environment undisturbed.
Self-Deconstructing Medical Implants: Medical implants that dissolve once healing is complete, reducing the need for follow-up surgeries and minimizing infection risks.
Slow-Releasing Pesticide Capsules: Agricultural capsules that dissolve over time to release nutrients and pesticides sequentially, optimizing crop protection and reducing chemical waste.
Programmable Packaging Solutions: Water-soluble packaging for single-use items or perishables that disappears after disposal, reducing plastic waste effectively.
Zero-waste Temporary Art Installations: Timed art pieces designed to dissolve over time, creating ephemeral installations that leave no environmental impact, with increased art appreciation due to its ephemeral nature.
Ocean Buoys for Wildlife Monitoring: Timed-dissolving buoys that monitor marine life and disappear after their mission, preventing marine debris.
Personalized Fitness and Wellness Devices: Disposable fitness trackers that dissolve after use, releasing beneficial compounds, offering convenience with no waste.
Smart Infrastructure with Automated Deconstruction: Self-dissolving infrastructure for temporary construction needs, saving on cleanup costs and reducing waste when no longer needed.
Free U.S. standard shipping on orders of 5+ spools!
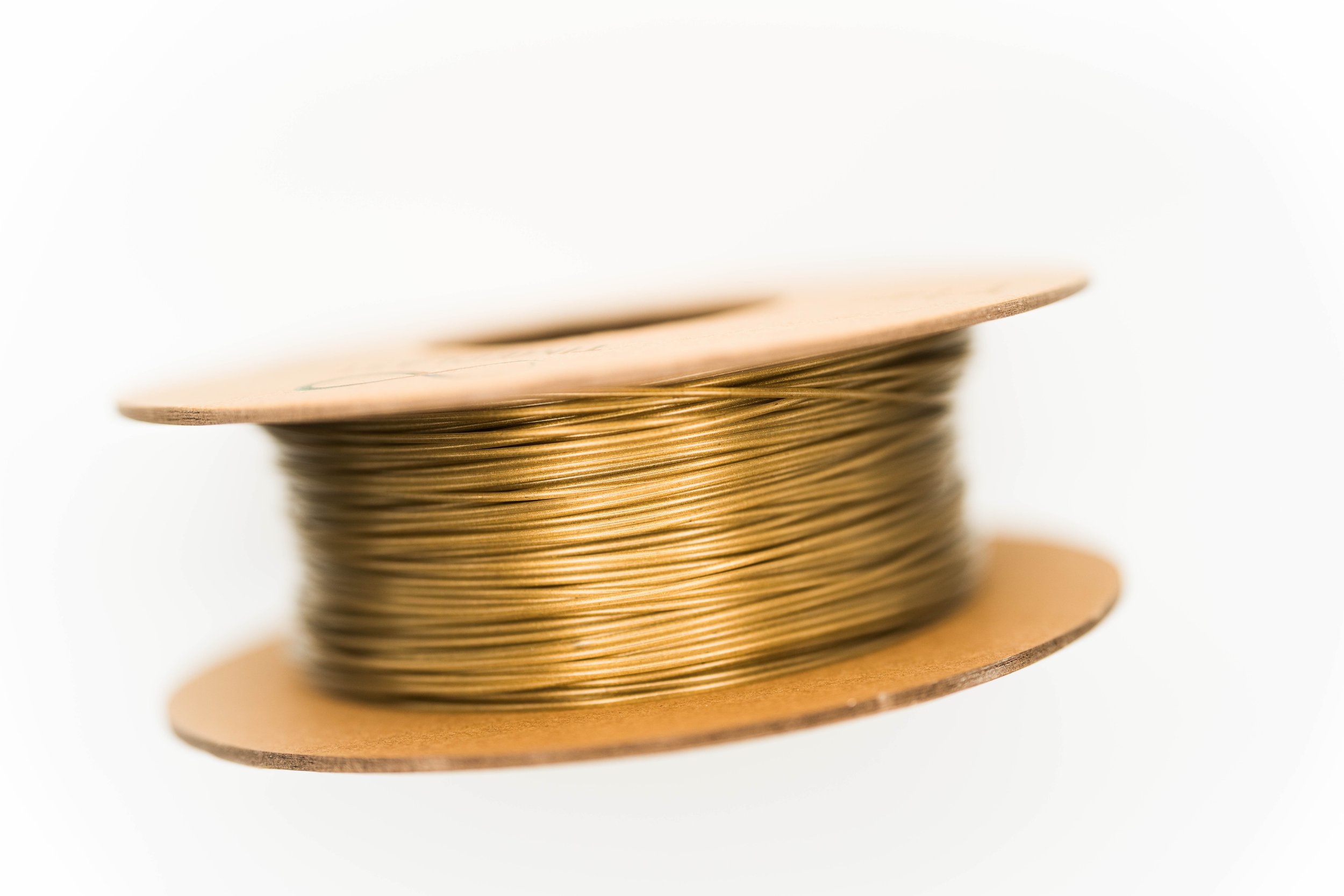
Manufactured
In-house
Your 24/7 TimeMass Printing Assistant
Need quick answers on slicer settings, troubleshooting, or filament tips? We’ve built a dedicated TimeMass ChatGPT assistant to support you anytime — just click below and ask your question:
Learn about our latest pieces.
-
Yes — we recommend drying for 2 hours at 100°C before use for best performance.
-
You can access our full User Manual with settings here:
👉 TimeMass User Manual (PDF) -
No. Microplastics are non-water-soluble at any size. TimeMass dissolves molecularly, leaving no microplastic residues.
-
Yes! For every 5 spools of the same filament type, you can request a custom color.
For example, 10 spools = 2 custom color options.Please note: custom color selections are final and not eligible for return.